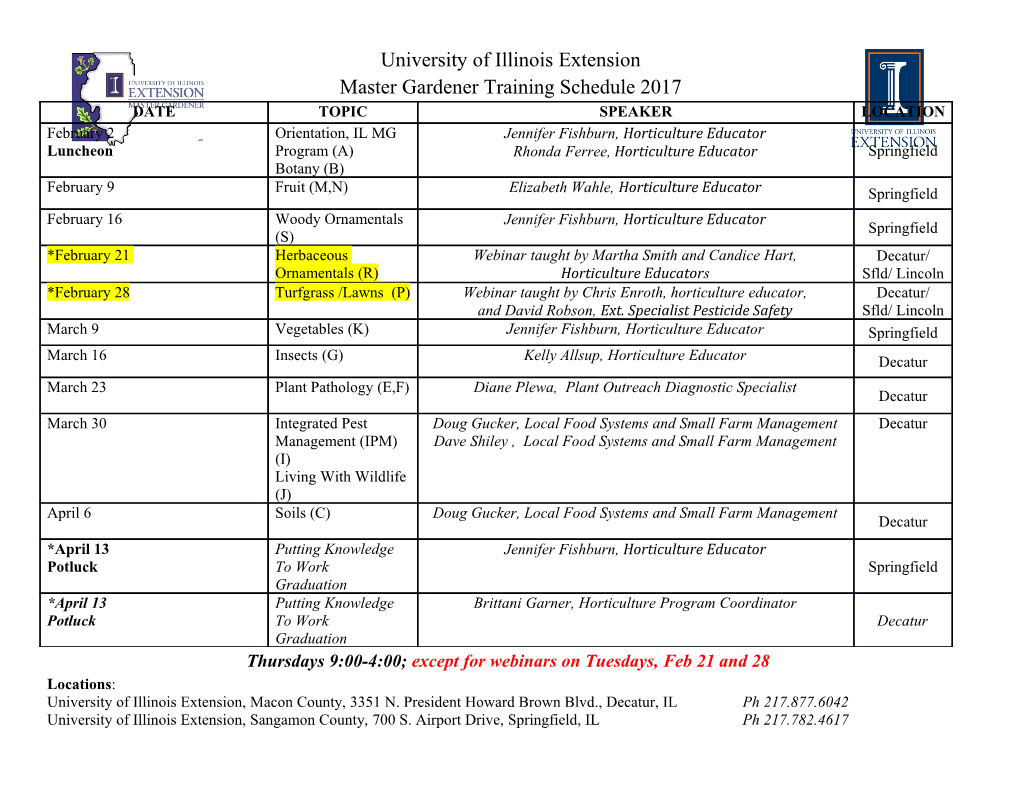
lubricants Article Tribological Properties of the Lubricant Containing Titanium Dioxide Nanoparticles as an Additive Filip Ilie 1,*,† and Cristina Covaliu 2,† 1 Department of Machine Elements and Tribology, Polytechnic University of Bucharest, 313 Spl. Independentei, 060042 Bucharest, Romania 2 Department of Biotechnical Systems, Polytechnic University of Bucharest, 313 Spl. Independentei, 060042 Bucharest, Romania; [email protected] * Correspondence: ilie.fi[email protected] or fi[email protected]; Tel.: +4-021-402-9411 † These authors contributed equally to this work. Academic Editors: Antolin Hernández Battez and Rubén González Rodríguez Received: 4 January 2016; Accepted: 12 April 2016; Published: 21 April 2016 Abstract: To improve the oil-solubility of nanoparticles, a new technology was used to prepare a kind of lubricant containing titanium dioxide (TiO2) nanoparticles. The microstructures of the prepared nanoparticles were characterized via transmission electron microscope (TEM) and infrared spectroscopy (IR). Tribological properties of TiO2 nanoparticles used as an additive in base oil were evaluated using four-ball tribometer and ball-on-disk tribometer. In addition, the worn surface of the steel ball was investigated via polarized microscopy (PM) and X-ray photoelectron spectroscopy (XPS). The TiO2 nanoparticles can be completely well-dispersed in the base oil under a new process (NP), which has no significantly negative effect on the anti-oxidation property. The results of the tribological tests show that TiO2 nanoparticles under the NP show a better anti-wear property and friction-reducing property in base oil compared to TiO2 nanoparticles under the tradition process (TP). The main aim of this paper lies in solving with the oil-solubility problem through the combination effect of surface modification and special blend process of lubricating oil. This method was first used to prepare lubricant containing TiO2 nanoparticles and then used as additives in engine oil, gear oil, and other industrial lubricants. At the same time, tribological properties of TiO2 nanoparticles in base oil as a lubricating additive were also studied. Keywords: blended oil; lubricants; titanium dioxide (TiO2) nanoparticles; oil-solubility; tribological properties 1. Introduction Conventional lubricant additives are generally thosecompounds containing sulfur, phosphor, or chlorine, among others [1–3] that play an important role in gear lubrication and cutting lubrication. However, the commercial applications of these kinds of additives are unsatisfactory because of the pungent odor, extreme corrosion, and the poor thermal stability [4–7]. Therefore, it is necessary to develop new kinds of additives that can be used as a substitute for traditional lubricant additives. The use of nanoparticles as oil additives and lubricants is a recent idea. Numerous nanoparticles have been investigated in recent years [8–22]. These oil additives contain small particles of solid material, and their use is not straightforward and only recently has been recognized as feasible. The utilization of oil additives as nanolubricants presents many advantages, as they are relatively insensitive to temperature, and tribochemical reactions are limited, compared to traditional additives. Different anti-friction and anti-wear mechanisms using the nanoparticulate additives have been explained in previous papers [10,12–14,23,24]. Lubricants 2016, 4, 12; doi:10.3390/lubricants4020012 www.mdpi.com/journal/lubricants Lubricants 2016, 4, 12 2 of 13 Experimental results with nanoparticles used as additives in oil lubricants show that they deposit on the friction surfaces and improve the tribological properties of the base oil, displaying good friction and wear reduction features, even at low concentrations. Inter alia, titanium dioxide (TiO2) nanoparticles as lubricant additive were studied with much more attention, because of their good performance on anti-oxidant features, relatively low toxicity, pleasant odor, and non-volatility [25–27]. Unfortunately, nanoparticles are not well dispersed in nonpolar organic solvents due to their oleo-philic property, which limits the nanoparticles applications in lubricants. Now, two approaches to solve this frequently problem are taken. The first method is the addition of dispersant into base oil. The main drawback of this method is that the sedimentation is unavoidable after a long-time storage and the negative effect of same dispersants on tribological properties [28–31]. The second method is the usage of surfactant [31–33]. Based on what we know metal nanoparticles, oxide nanoparticles and hydrate nanoparticles can change their oil solubility utterly under the effect of surface modification—even transfer from water to oil phase [34,35]. However, titanium (Ti) atoms of TiO2 coordinate with either two or three oxygen atoms (O) to form TiO2 or Ti2O3 groups, so they are hybridized to a planar or three-dimensional structure. Such structure units can comprise several different typical groups through various combinations, which lead to a structure more complex and cause the difficulty of surface modification of TiO2. However, the transfer and adhesion of the nanoparticles accelerates surface modification, self-reduction, and the formation of a fine TiO2 tribofilm that reduced the coefficient friction, pressure, and temperature in contact area and hence wear. Thus, it can be concluded that both methods (listed above) are classical and have their own defects (the addition of dispersant or usage of surfactant into base oil) for solving the oil solubility of TiO2 nanoparticles. This claim is strengthened by the works of several researchers [3,8–11,23,24,36–38]. Therefore, the application process of the two classical methods was named the traditional process (TP). The TiO2 nanoparticles cannot be well dispersed in the base oil after the TP, for the sedimentation is unavoidable in time, with negative effect on tribological properties. In this paper, a new preparation method—referred to here as the new process (NP)—is suggested for solving the poor oil solubility of TiO2. The new technology is no longer restricted to the surface modification process, but solves the difficult problem through the combination effect of surface modification and an oil-blending process. The new method was first used to prepare a lubricant containing TiO2 nanoparticles, and it should be helpful for the TiO2 nanoparticles used as additives in engine oil, gear oil, and other industrial lubricants [39–41]. At the same time, tribological properties of TiO2 nanoparticles in base oil as a lubricating additive were also studied. Thus, the paper discusses the anti-friction and anti-wear behavior of TiO2 nanoparticle suspensions in base oil (nanolubricant or nanofluid) under mixed lubrication using a four-ball tribometer and ball-on-disk tribometer, and presents PM and XPS analysis of the worn surfaces. 2. Experimental Details 2.1. Materials, Blend Oil Process, and Characterization Oleic acid for chemical industry (Sigma-Aldrich Co. LLC., Wilmington, NC, USA, from office in Germany), absolute ethanol (Sigma-Aldrich Chemie GmbH, Munich, Germany), TiO2 nanoparticles, and petroleum ether (60 ˝C–90 ˝C, Xilong Chemical Co. Ltd., Guangzhou, Guangdong, China) were of analytical grade. All the reagents were used without further purification. Distilled water was applied for all synthesis and processes. API-1509 base oil came from Petro-Brazi Lubricating Oil R&D Institute. Its typical properties are given in Table1. Lubricants 2016, 4, 12 3 of 13 Table 1. Properties of the API-1509 base oil. Kinematic Viscosity [mm2/s]to: 42.85 ´40˝C 6.037 ´100˝C Viscosity index 80 Pour point [˝C] ´9 Flash point [˝C] 199 Acid value [mgKOH/g] 0.05 Sulfur content [%} 0.03 Degree of saturation [%] 90 Color Yellowish The typical experimental procedure for preparing surfaces modified particles is as follows: Analytical-grade titanium tetrachloride (TiCl4) was adopted as the source material and sodium hydroxide (NaOH) as mineralizer, which by reaction is obtained TiO2. A certain amount of TiO2 (obtained from the reaction TiCl4 and NaOH) was first diluted in the mixture solution of absolute ethanol and distilled water. An aqueous solution of TiO2 was obtained by mixing one molar stoichiometric ratio of TiO2 in 50 mL of distilled water. The aqueous solution with 2–3 mol of NaOH was stirred for several minutes (5 min), resulting in a white colloidal solution. The final volume was adjusted to 90 mL using distilled water. Therefore, the 90-mL solution was transferred to a 100-mL Teflon lined auto clave vessel. The sealed vessel was heated to 240 ˝C for 12 h, and the resultant ˝ precipitate was dried at 450 C for 2 h to obtain TiO2 nanoparticles. Then, TiO2 nanoparticles were mixed with the petroleum ether containing oleic acid and stirred for 2 h at room temperature. The white liquid suspended matter was dried by the rotary evaporation method, followed by filtering, washing repeatedly with water and absolute ethanol to remove unreacted reactants and oleic acid, followed by drying at 80 ˝C for 4 h with a conventional oven, in an ambient air environment. A certain amount of prepared TiO2 nanoparticles was added to the base oil. The mixture (TiO2 nanoparticles added in base oil) was exposed to direct insert ultrasound irradiation in ambient air for 10 min. Ultrasound irradiation was accomplished with a high-intensity ultrasonic probe (Ti-horn, 25 kHz, 1200 W/cm2) immersed directly in the reaction solution. Then, the solution was
Details
-
File Typepdf
-
Upload Time-
-
Content LanguagesEnglish
-
Upload UserAnonymous/Not logged-in
-
File Pages13 Page
-
File Size-