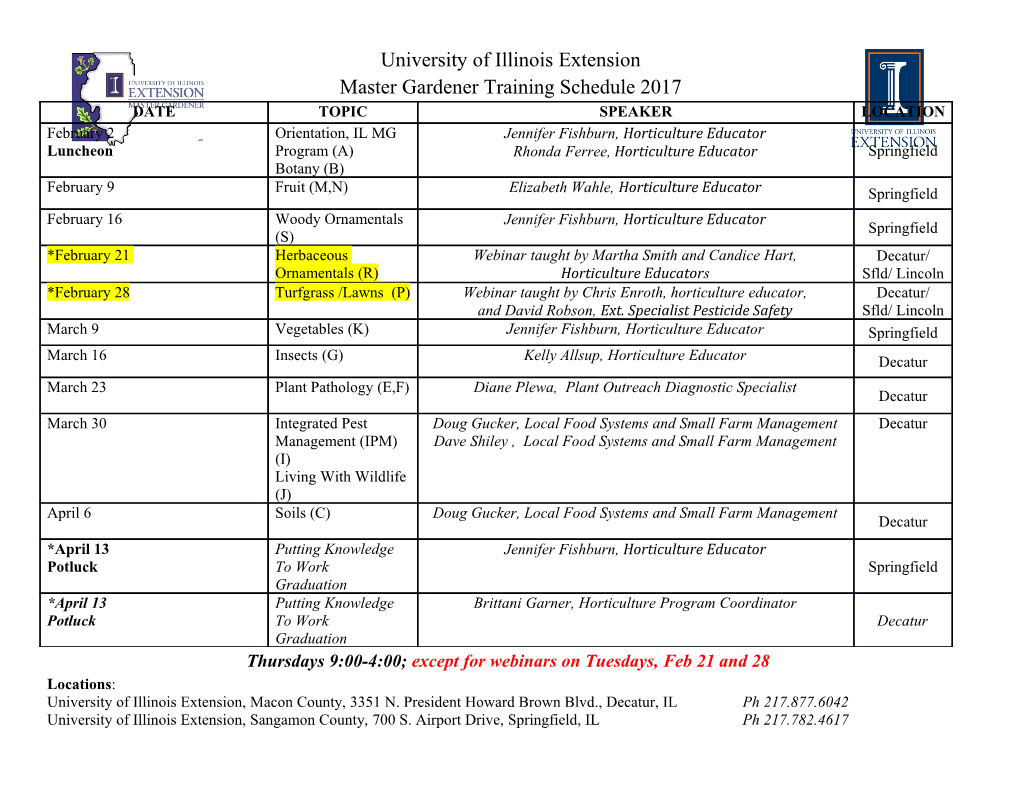
Extraction Efficiency, Quality and Characterization of Typha latifolia L. Fibres for Textile Applications by Koushik Chakma A thesis submitted to the Faculty of Graduate Studies of The University of Manitoba in partial fulfilment of the requirements of the degree of MASTER OF SCIENCE Department of Biosystems Engineering University of Manitoba Winnipeg, Manitoba, Canada Copyright © 2018 by Koushik Chakma Abstract The textile uses of the aquatic plant ‘Typha latifolia L.’ (genus Typha) have not been previously explored. The current research is the first of its kind to examine the extraction, quality and properties of this waste biomass fibre and compare them with the two most widely used fibres: cotton and polyester, wool. It was found that Typha leaves and the core spongy tissue could be transformed into fibres under controlled experimental conditions in aqueous alkaline solution giving a yield range of 15% to 60%. The diameter of the Typha fibre is much higher than the Cotton and wool while the moisture regain (%) and thermal resistance are comparable to these two fibres. SEM revealed a unique submicroscopic ‘crenelated’ structure and FTIR spectrum showed the cellulose rich content in the Typha fibre. The cellulose content helped Typha fibre absorb the reactive dyes and the dye exhaustion is similar or better than the cotton. However, the stiffness of the Typha fibre is higher than the cotton and polyester, which would make Typha fibre difficult to process in the Cotton spinning systems. i Acknowledgements Writing a scientific thesis is definitely a difficult task, and it was only possible because of great support from some moral people. First of all, I want to express my sincere gratitude towards my supervisor, Professor Dr. Mashiur Rahman, and my co-supervisor, Dr. Nazim Cicek. This thesis would not have been completed successful without their intellectual guidance and valuable advice. Most of all I am fully indebted to Dr. Rahman for his understanding, enthusiasm, wisdom, patience and continuous supervision, which helped me to reach my dream. I am thankful to Dr. Kevin McEleney from the Manitoba Institute for Materials (MIM), who gave me proper guidance on how to use FTIR and KBr pellet preparation. My special appreciation goes to the Manitoba Institute for Materials and Dr. Ravinder Sidhu, since she helped me to complete my research work by providing opportunities to use the SEM machine and the Typha fibre morphological analysis study. I am indebted to Mary Pelton, who supported me and provided me helpful guidance for editing my thesis. Needless to say, another two important people, Nicholson and Joe Ackerman, gave me tremendous support by providing Typha plant samples. I would like to thank the Natural Sciences and Engineering Research Council of Canada (NSERC). It would have been impossible without their assistance by helping me with their financial grant support. Last but not least, my deepest appreciation to God, my parents, my wife, and my classmates, esspecially Ikra Iftekhar Shuvo, Abdullah-Al-Mamun, Mahmudul Hasan, Yasin Sabik and my roommates; they gave me great support. Undoubtedly, I would like to add them for being a part of my success. They always supported me by helping me to survive all stresses and by not letting me give up. ii Table of contents Abstract……………………………………………………………………………………... i Acknowledgements ………………………………………………………………………… ii Table of contents………………………………………………………………………….... iii Abbribation…………………………………………………………………………………. viii List of Tables……………………………………………………………………………….. xi List of Figures…………………………………………………………………………….... xiii List of permitted copyrighted material from different sources……………………………... xxiv 1. Introduction………………………………………………………………………... 1 2. Literature review…………………………………………………………………... 9 2.1 History of textile fibres……………………………………………………………. 9 2.1.1 Natural cellulosic fibres……………………………………………………... 9 2.1.2 Common textile fibres ………………………………………………………. 15 2.2 Extraction of bast fibre……………………………………………………………. 18 2.2.1 Biological retting…………………………………………………………….. 19 2.2.2 Mechanical retting…………………………………………………………… 20 2.2.3 Chemical retting…………………………………………………………….... 20 2.2.4 Enzymatic retting…………………………………………………………….. 21 2.3 Characterization of bast fibre………………………………………………………. 22 2.3.1 Physical properties…………………………………………………………... 22 2.3.2 Spinning properties of fibres………………………………………………… 26 2.3.3 Blending properties………………………………………………………….. 28 2.3.4 Thermal properties…………………………………………………………... 28 2.4 Modification of bast fibre…………………………………………………………. 30 iii 2.4.1 Alkalization/mercerization…………………………………………………. 30 2.4.2 Dyeing of bast fibres………………………………………………………... 32 3. Materials and method…………………………………………………………….. 33 3.1 Retting and fibre extraction………………………………………………………. 34 3.2 Fibre extraction……………………………………………………………………. 35 3.3 Fibre characterization…………………………………………………………….. 37 3.3.1 Yield measurement…………………………………………………………. 38 3.3.2 Statistical analysis of Typha fibre length…………………………………… 39 3.3.3 Diameter measurement……………………………………………………... 39 3.3.4 Softness measurement…………………………………………………….... 40 3.3.5 Moisture regain (%) measurements……………………………………….... 40 3.3.6 Infrared (IR) spectrum study………………………………………………. 41 3.3.7 Thermal analysis…………………………………………………………… 41 3.3.8 Scanning electron microscopy (SEM)……………………………………… 42 3.3.9 Typha fibre dyeing with reactive dyes……………………………………… 43 3.3.10 Colour differences of dyed fibres………………………………………….. 44 3.3.11 Evaluation of dyeing performance (colorfastness to hot pressing) ………... 45 3.3.12 Statistical analysis……….............................................................................. 46 4. Extraction of Typha fibre…………………………………………………………. 47 4.1 General overview ………………………………………………………................ 47 4.1.1 Water retting………………………………………………………………. 47 4.1.2 Chemical retting……………………………………………………………. 50 4.2 Effect of various alkalis on fibre yield…………………………………………... 54 iv 4.2.1 Fibre yield (%) from mixed plants…………………………………………. 54 4.2.2 Fibre yield (%) on hard stem (HS), soft stem (SS) and no stem (NS) plants.. 59 4.2.3 Data analysis………………………………………………………………… 60 4.3 Sources of flakes and barks in the fibre…………………………………………... 62 4.3.1 Extraction of fibre from various plant components………………………... 65 4.3.2 Summary………………………………………………………………….... 74 5. Textile characteristics of Typha fibre…………………………….......................... 75 5.1 Fibre morphology……………………………………………………………......... 75 5.1.1 Macrostructure of Typha fibre……………………………………………... 75 5.1.1.1. Fibre length…………………………………………………………... 75 5.1.1.1.1 Relationship between Typha plant length (cut length) and fibre length ………………………………………………………. 77 5.1.1.2 Statistical results…………………...................................................... 77 5.1.1.3 Statistical analysis of Typha fibre length: Effect of treatment on fibre length………………………………………………………… 80 5.1.1.4 Implications…………………………………………………………… 81 5.1.1.5 Fibre diameter………………………………………………………… 81 5.1.1.6 Statistical analysis…………………………………………………….. 84 5.1.1.7 Summary……………………………………………………………... 85 5.1.2 Microstructure of Typha fibre……………………………………………… 86 5.1.2.1 Cross-sectional features………………………………………………… 86 5.1.2.2 Longitudinal view of fibre……………………………………………… 87 5.1.2.3 Submicroscopic structure………………………………………………. 8 8 v 5.2. Typha fibre chemical composition by FTIR…………………………………. 91 5.3 Moisture regain of textile materials…………………………………………. 95 5.3.1 Summary…………………………………………………………………. 99 5.4 Thermal properties………………………………………………………….... 98 5.4.1 Burning behaviour of Typha fibre………………………………………… 99 5.4.2 Evaluation of Typha fibre thermal properties…………………………….. 101 5.4.3 Summary………………………………………………………………….. 104 5.5 Dyeing of Typha fibres with reactive dye………………………………………… 106 5.5.1 Evaluation of colour fastness of dyed Typha fibres……………..................... 110 5.5.1.1 Summary…………………………………………………………………. 118 5.5.2 Color differences of dyed Typha fibre…………………………..................... 119 5.6 Typha fibre hand properties………………………………………………………. 121 5.6.1 Summary………………………………………………………………………. 125 6. Conclusions and future work…………………………………………………….. 127 References………………………………………………………………………………….. 132 Appendix I…………………………………………………………………………………. 146 Appendix II………………………………………………………………………………… 152 Appendix III……………………………………………………………………………….. 155 Appendix IV……………………………………………………………………………….. 159 Appendix V………………………………………………………………………………… 160 Appendix VI………………………………………………………………………………. 163 Appendix VII………………………………………………………………………………. 164 Appendix VIII……………………………………………………………………………... 168 vi Appendix IX………………………………………………………………………………. 170 Appendix X………………………………………………………………………………. 171 vii Abbribation American Association of Textile Chemists and Colorists (AATCC) American Society for Testing and Materials (ASTM) Analysis of Variance (ANOVA) Ethylenediaminetetraacetic acid (EDTA) Food and Agricultural Organization (FAO) Food and Agricultural Organization Statistical Databases (FAOSTAT) Fourier-transform infrared spectroscopy (FTIR) Mixed Stem (MS) Least Significant Difference (LSD) Hard Stem (HS) Scanning Electron Microscopy (SEM) Soft Stem (SS) No Stem (NS) World Wide Fund (WWF) Advanced Fibre Information System (AFIS) Image analysis microscopy (IAM) Polyethylene terephthalate (PET) Polycyclic aromatic hydrocarbons (PAH) Acrylic polyacrylontrile (PAN) Polypropylene (PP) Green House Gas (GHG) High Volume Instrument (HVI) International Organization for Standardization (ISO) viii List of Tables Table 1.1: Country-based natural fibres production……………………………………….. 6 Table 2.1: Chemical composition (%) of different
Details
-
File Typepdf
-
Upload Time-
-
Content LanguagesEnglish
-
Upload UserAnonymous/Not logged-in
-
File Pages195 Page
-
File Size-