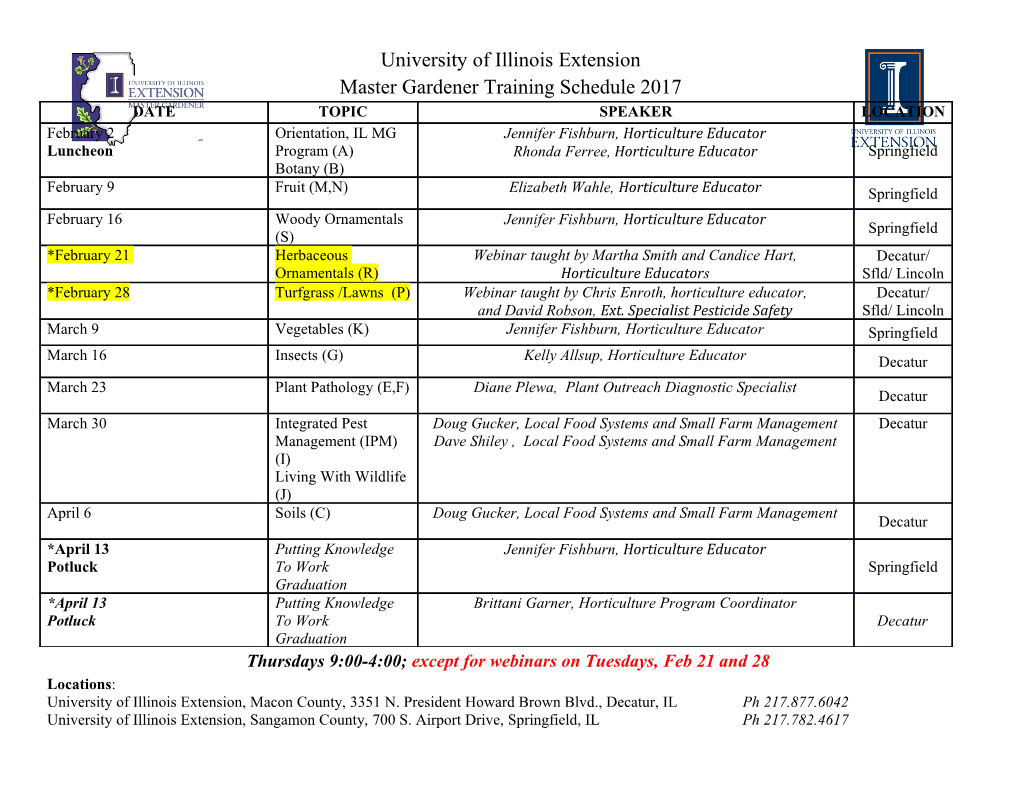
Bulletin of the Transilvania University of Braşov • Vol. 9 (58) No. 2 - 2016 Series I: Engineering Sciences DIESEL FUEL HEATER USING ENGINE COOLANT FOR COLD WEATHER OPERATION Veneția SANDU1 Abstract: The paper studies diesel fuel heating in vehicle operation at below-zero temperatures by means of engine coolant and a helical coil heat exchanger placed in the fuel tank. A preliminary prototype of the helical coil heat exchanger was manufactured and investigated on a diesel engine truck operating in real winter condition being measured the diesel fuel and coolant temperatures. The experimental data on coolant temperature variation and heating time were used to improve the final thermostatically controlled design. Key words: diesel fuel preheating, helical coil heat exchanger. 1. Introduction the heat released by engine hot sources such as coolant [6], lubricant or exhaust The behavior of fuel in diesel engines gas. A patent survey in this field was running at low temperatures is strongly presented in [9] showing that the most influenced by its paraffin content which spread solutions opt for electric and may crystallize and clog the fuel filter and coolant heating. block the fuel supply. The phenomenon Especially for heavy duty diesel vehicles, known as waxing may occur under 0 °C, the high demand of electricity on board so in order to avoid paraffin precipitation and the opportunity of energy harvesting the diesel cold flow performance must be led to the implementation of special managed either depressing the cold fuel purpose designed heat exchangers mounted temperatures (Cloud Point, Pour Point, either on the fuel tank or on the low Cold Filter Plugging Point) with diesel pressure fuel ducts. flow improvers or by using fuel heating. The present study reveals the design, The gradual replacement of the testing and improvement of a fuel heater petroleum diesel with renewable fuels such used in a 100 liter tank of the 7 tonne as biodiesel accentuates that difficulty due diesel truck using the heat of the engine to higher temperatures at which coolant. crystallization occurs in biodiesel blends. The need of fuel heating led to the 2. Design Demands and Phases implementation of several techniques described in literature either as electric For diesel engines fitted with mechanical heating of fuel filter, fuel pump or fuel injection systems the optimum viscosity of duct [4], [5] or heat exchangers based on the fuel in fuel filter is reached in the 1 Mechanical Engineering Dept., Transilvania University of Braşov. 2 Bulletin of the Transilvania University of Braşov • Series I • Vol. 9 (58) No. 2 - 2016 interval 20-40 °C [9]. The fuel heater was [11] of a similar truck and are indicated in intended to be placed in the fuel tank being Table 1. heated with engine coolant taken from the cabin heating system, upstream thermostat. Heat exchanger parameters Table 1 The coolant circuit passes through a hose Pure Diesel to fuel tank heater and returns in the water fuel cooling system upstream coolant pump. Inlet temperature, ti [°C] 72 5 In summer time the system is not used Outlet temperature, t [°C] 70 20 and the circuit is closed manually with a tap e Heat capacity, cp [J/kg·K] 4190 1800 or electrically with a thermostat. The system has no influence on the engine cold starting The fuel flow rate passing through the thus being performed by a glow plug. heater was around three times higher than The design was performed in three the engine fuel consumption [12] due to phases: the pumping technique which delivers 1. Preliminary design of a experimental more fuel to cool the injectors, implying prototype (heat exchanger and fuel heating some warmed excess fuel which is system); returned in the tank. 2. Prototype testing; The heat exchanger was made of a 3. Final design. cylindrical copper pipe of 0.018/0.015 mm The testing was required to evaluate in (outer and inner diameter), resistant to real operation condition during winter the corrosion, having a very high thermal efficiency of the heat exchanger measured conductivity. as fuel temperature increase and the time The calculation was based on classical needed to reach the desired temperature. heat transfer between two fluids separated by a cylindrical wall, neglecting the heat 2.1. Preliminary Design transfer of the tank with the air and considering the heat exchanger ideal. The Paradoxically, the engine coolant subscript 1 refers to the heater agent and becomes the heating fluid of the fuel in the subscript 2 to the heated one. preheating system. The appropriate type of On the coolant side, when the coolant heat exchanger was considered to be the passes through the circular section of the helical coiled one, with higher heat transfer coil, its velocity, , is calculated with coefficients than straight tubes due to the 1 Equation: secondary flow produced by centrifugal force induces in curved tube [3]. m 1 The helical coil heat exchanger was 1 2 . (1) designed to operate immersed in a high di 1 capacity tank according to the procedure 4 described in [2]. The fluid characteristics were approximately in the first iteration as The Reynolds number, Re, calculated for those of pure water and diesel fuel for the water viscosity at the mean temperature automotive use. between inlet and outlet, considered to be The flow rates of the agents (coolant, 70 °C, indicated a turbulent flow: diesel fuel) were provided by technical documents of the engine and auxiliaries d Re 1 i . (2) [10]; the coolant temperatures were 1 collected from test reports on cabin heating 1 Sandu, V.: Diesel Fuel Heater Using Engine Coolant for Cold Weather Operation 3 4 For Reynolds number higher than 10 it 2 1 -1 gravity g = 9.81 m/s , 0.0033 K ). is recommended the following criterial Tbl equation which correlates Nusselt number, The wall temperature on fuel side t2w Nu, with Reynolds number and Prandtl was initially considered 70 °C and the number, Pr: tbl = 32.5 °C resulting Gr2 = 196959, 2 0.25 Nu2 = 25.4 and 2 = 155 W/m K. Pr 0.8 0.43 1 . (3) By introduction of 2 in the equation of Nu1 0.021 Re1 Pr1 Prw heat transfer per unit length of pipe: Prandtl number at the wall temperature, d11(t1 t1w) d22 (t2w t2 ) , (7) Prw, is assumed to be the same with Pr1 number of the fluid. The convection it can be calculated the temperature of the coefficient 1 from water to the coil wall wall on the water side, resulting can be written in the form: t1w = 67.8 °C. The temperature drop in the wall is considered negligible due to very 1 1 Nu1 . (4) low thermal resistence, so (t1w – t2w) 0, in di the first iteration. In the second iteration starting with On the fuel side, diesel fuel in the tank is t1w = 67.8 °C Grashof number becomes 2 supposed to be heated from 5 to 20 °C Gr2 = 189944 and 2 = 153.7 W/m K with and the flow is laminar due to high tank an error towards previous calculation less capacity and gravity, being recommended than 1%. the criterial equation which correlates By equalizing Equation (7) with heat Nusselt number with Grashof number, Gr, transfer in the pipe wall: and Prandtl number: 2 d (t t ) w (t t ) , (8) Nu 0.4 (Gr Pr )0.25 , (5) 1 1 1 1w d 1w 2w 2 2 2 ln 1 d2 3 gde (t2w t2bl ) Gr2 . (6) 2 it results the real temperature drop in the 2 wall of 0.06 °C. For the diesel fuel, the properties were The convection coefficient from the 2 calculated at the temperature of the thermal coil wall towards the fuel is similar to Equation (4). The calculations considered boundary layer, t2bl, as arithmetic mean of t2w and t2i. water properties (mass flow rate, 3 The rate of heat Q1 transmitted from m 1 0.08 kg/s, density, 1 = 977 kg/m , 6 2 water is calculated as follows: viscosity at 70 °C, 1 = 0.4210 m /s, Prandtl number Pr1 = 2.4, thermal Q m c (t t ) . (9) conductivity 1 = 0.663 W/mK), wall 1 1 p1 1i 1e properties (copper thermal conductivity, w = 300 W/mK) and diesel fuel (density, Finally, the linear overall heat transfer, k, 3 2 = 838 kg/m , viscosity at tbl = 33.2 °C, takes into account the thermal resistances 6 2 2 = 610 m /s, Prandtl number Pr2 = 83.3, for each environment: water, copper wall thermal conductivity 2 = 0.11 W/mK, and diesel fuel: 4 Bulletin of the Transilvania University of Braşov • Series I • Vol. 9 (58) No. 2 - 2016 measure of the straight portion, Ls, k . (10) l 1 1 d 1 becomes 170 mm. ln e d 2 d d 1 i w i 2 e 2.2. Prototype Testing The linear rate of heat between fluids is The heat exchanger designed according calculated with the formula: to values from Chapter 2.1 was manufactured and then the heating l kl (t1i t2i ) . (11) installation was assembled and tested on the facilities of Road Vehicle Institute For the intermediate values α1 = 3207 (INAR Braşov). 2 2 W/m K, α2 = 153.8 W/m K, kl = 8.22 W/mK, The heating system was adapted to the it results Φl = 633W/m. configuration of the truck AB 7120F The total minimum length, L, of the manufactured at Roman Truck company, helical coil results from the formula: series 0205, which was equipped with a 798-05 diesel engine, series 04598, derated Q to 120 HP@2500 rpm.
Details
-
File Typepdf
-
Upload Time-
-
Content LanguagesEnglish
-
Upload UserAnonymous/Not logged-in
-
File Pages8 Page
-
File Size-