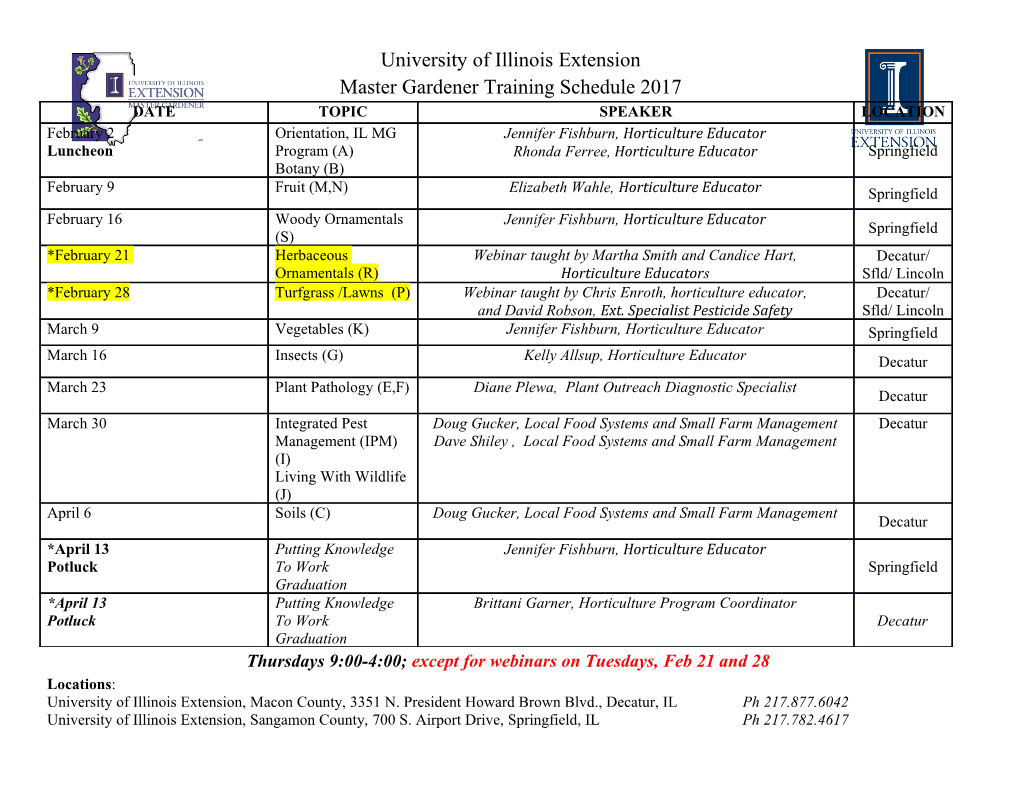
JCB DIESELMAX EMERGING TECHNOLOGIES A JCB Fastrac about to push start the JCB Dieselmax on the Bonneville Salt Flats, helping save wear-and-tear on clutches and tyres JCB DIESELMAX POWERING THE WORLD’S FASTEST DIESEL VEHICLE It was one of the most unusual challenges of recent engineering in the UK. How to turn a humble 140 bhp diesel engine from its usual use, powering a JCB digger, into a 750 bhp racing unit capable of winning a land speed record? David Tremayne, who has reported on many speed record attempts, describes the engineering achievements involved in creating the JCB Dieselmax streamliner. 40 INGENIA ISSUE 32 SEPTEMBER 2007 INGENIA ISSUE 32 SEPTEMBER 2007 41 JCB DIESELMAX EMERGING TECHNOLOGIES A turbo system with inter-stage and after- PISTON AND FUEL crank degrees, that’s what makes it a challenge with the cooling was developed in order to deliver the SYSTEM fuel system. DEVELOPMENT “You need to put an awful required air flow across the engine speed The pistons were always one lot of fuel in, in a very, very range. A water injection system provided a of the biggest risk areas in short space of time, and the JCB444 LSR engine. you’ve got to put it through a further level of charge cooling to protect the Ricardo needed to run the minute orifice to get the fuel aluminium components at to mix. Diesel fuel is not as pistons and valves. “Getting the fuel and air in very, very high thermal and prone to mixing as gasoline was the single most difficult thing as far as I mechanical loads, in the sort because it’s a heavy fuel so it of extreme circumstances at doesn’t evaporate, so you was concerned”, said Matt Beasley, Chief which the metal normally don’t have the time to do that degrades. But there was no and you have to inject it Engineer for the engine on the Dieselmax option: the material through a tiny pinprick hole project. “The fuel system was a big challenge, minimised weight, facilitating at massive pressure in a tiny an engine speed almost space of time. That’s why the getting the engine to run the speed we twice the unit’s norm. The fuel system on any diesel associated piston problems engine is a major challenge.” needed to achieve the power we needed.” were a corollary of the fuel JCB invested huge effort system that was necessary to to create reliable achieve the high power components, as the bore ‘pick output. up’ problems continued. With In a gasoline engine, fuel the original 108 mm piston can easily be used as a design the upright engine coolant. In some high achieved almost performance turbocharged 700 bhp (680) in December applications, it is common to 2005. However as the alleviate thermal problems by inclined engine switched to a The JCB Dieselmax team prep the car prior to a run during the Bonneville Speed Week cooling the pistons with fuel 109 mm Federal Mogul piston spray and enduring the in February 2006, the associated high fuel problems really began and Once Sir Anthony Bamford, requirement posed a bedplate (the plate at the dictates how much fuel can be “Getting the fuel and air in was consumption. But in a the focus of troubleshooting Chairman of JCB, had set his phenomenal challenge to the bottom of the engine, which pumped in and thus how much the single most difficult thing as turbocharged diesel became the brand new dry- heart on breaking the land team, led by JCB’s Group closes the crankcase and gives it power the engine can generate. far as I was concerned”, said Matt application that would only sump lubrication system and speed record for diesel-powered Engineering Director Dr Tim extra rigidity). Beasley, Chief Engineer for the create smoke. its oil scavenging shortfall. vehicles, he was adamant about Leverton and in particular to The challenge was to engine on the Dieselmax As Ian Penny explained, There was so much oil flow one thing, he wanted to prove ‘Ricardo’, the consultant multiply the digger engine’s ENGINE OVERHAUL project. “The fuel system was a The first step was easily “Because of that we because, in order to control the versatility of JCB’s standard engineering company whose specific power output by a big challenge, getting the achievable – the engine was inherently run very hot. The the piston, there had to be a 444 engine and to validate it in a responsibility it was to develop factor of five, since two engines engine to run the speed we bored and stroked to five litres. old turbocharged Formula six-time increase in its oil totally different and extremely the power units to enable a and 1500 bhp were required to needed to achieve the power The greatest challenge lay in One engines were very well cooling. demanding engineering project target speed of 350 mph hit the target speed of 350 mph. we needed.” getting sufficient air and fuel engineered, but there wasn’t “You have got oil spraying environment. The backhoe (563 km/h). This was exacerbated when The combustion and fuel into it to increase power, and anything special to stop the the underside of the piston digger power unit thus had to Leverton insisted that the systems were very much the then managing that air and fuel pistons melting, just lots of which then just creates a big be the heart of his team’s car. engine had to retain the heart of the engine. Ricardo flow and the associated heat fuel. In a port-injected foaming mess, so there is an ‘Visioneering’ were STANDARD standard block and fundamental used its High Speed Diesel Race generated by two-stage gasoline engine you inject awful lot of oil flow and 6 bar contracted to build the car in SPECIFICATIONS architecture: “It had to be (HSDR) direct injection turbocharging operating fuel into the port or manifold boost,”continued Penny. “That Coventry. The former F1 The standard JCB 444 engine recognisably the JCB 444 engine. combustion technology wherein at over 6 bar. over about two or three means there is a huge engineer John Piper designed met four key design targets: We ended up with a stock block, fuel was delivered via two A turbo system with inter- hundred crank degrees. It amount of gas flow through the car, with the crucial strong construction; high torque with only internal tweaks, parallel, high pressure pumps to stage and after-cooling was evaporates, it gets sucked in, the engine and latterly you aerodynamics handled by Ron at low engine speeds; reduced cylinder head and bedplate.” a common rail system delivering developed in order to deliver the induction, compression, all get blow-by into the Ayers. It was Ayers’s genius that noise levels; and future-proofing There were further an injection pressure of 1600 bar. required air flow across the nicely mixed, spark, burn. crankcase, so in terms of had helped to create ThrustSSC, for the next steps in emissions drawbacks. The basic engine The cylinder head had to be engine speed range. A water We’ve got to inject within managing the dry sump the world’s only supersonic car. legislations. Also in its favour weighed 470 kg. With high- modified slightly to encompass injection system provided a about 30 crank degrees, system you have got an awful That side of the operation was were a very strong crankshaft, an powered diesels, the ideal is to the larger injectors required, and further level of charge cooling to you’ve got to inject the mix lot of oil and air flow to relatively straightforward. exceptionally stiff cylinder block have multiple cylinders. This is the actuation time for each protect the pistons and valves. and burn it within about 50 control.” However, Bamford’s bold and a substantial cast-iron because the number of injectors injector was subtly modified. 42 INGENIA ISSUE 32 SEPTEMBER 2007 INGENIA ISSUE 32 SEPTEMBER 2007 43 JCB DIESELMAX EMERGING TECHNOLOGIESFEATURE A cross-section of the completed JCB Dieselmax shows that the two JCB444-LSR engines were mounted rigidly to the chassis, one ahead and one behind the driver’s cockpit. The engines were not linked mechanically as it was felt that, given similar output and running speeds, each engine would regulate themselves independent of each other. Transmission was linked, however, and comprised Xtrac six-speed transaxles and JCB stepper boxes between each JCB Dieselmax at 365mph on the Bonneville Salt Flats. This was the first pass on engine and the gearbox. For steering, a conventional rack and pin system with the run that was to take JCB Dieselmax over the 350mph mark seven degrees of lock was employed CUSTOMISING THE standard 444’s rotational speed) “We have talked this through, LAST MINUTE and peak torque to 1500Nm. and so long as the engines are PISTONS The JCB444 LSR engine therefore close enough to each other in HITCHES While the valve train was generated more than five times specific output and run at the It transpired that the rear unit essentially carried over in its the power of the production same speed, they will regulate was merely going along for the original form with the exception version and, at 150bhp/litre, themselves mechanically,” ride, acting like a brake! This was of high temperature exhaust exceeded even motorsports Leverton explained. But once a vexing problem, but would valve material and uprated applications as the world’s the car began running in tests at prove to be the only unreliability springs, the pistons were totally highest specific power diesel car RAF Wittering in the UK in July, the highly tuned engines new with a large, quiescent engine.
Details
-
File Typepdf
-
Upload Time-
-
Content LanguagesEnglish
-
Upload UserAnonymous/Not logged-in
-
File Pages4 Page
-
File Size-