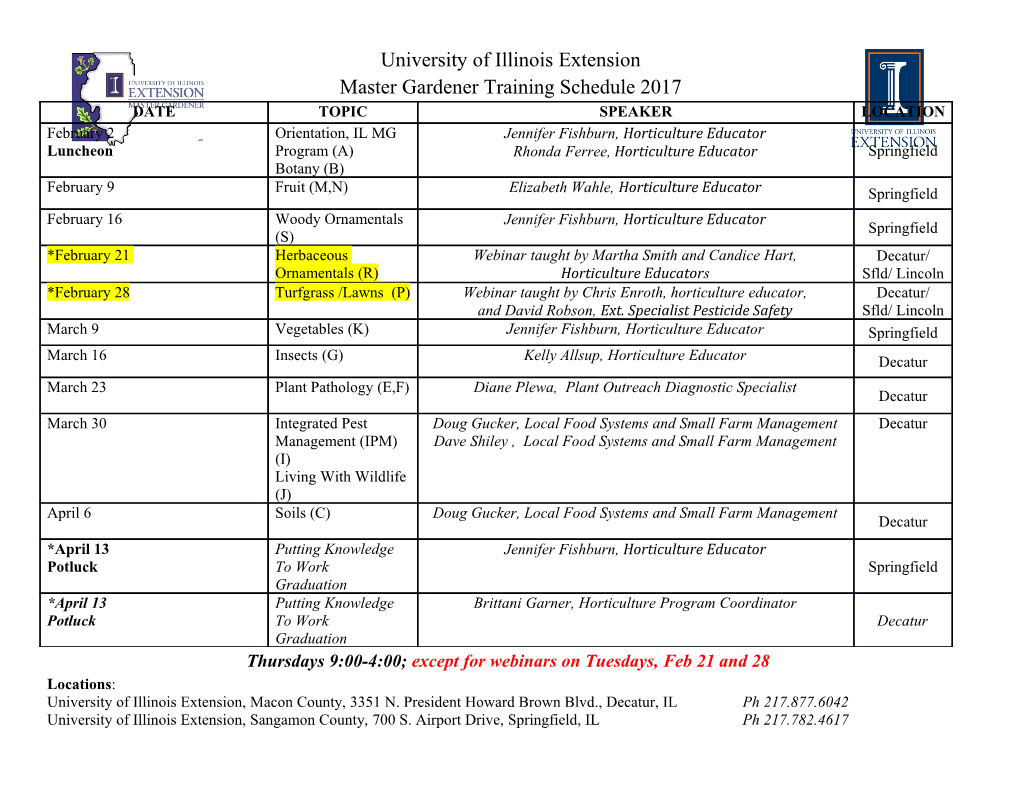
PCCP PAPER Superheating and melting within aluminum core–oxide shell nanoparticles for a broad Cite this: Phys. Chem. Chem. Phys., 2016, 18, 28835 range of heating rates: multiphysics phase field modeling Yong Seok Hwanga and Valery I. Levitas*b The external surface of metallic particles is usually covered by a thin and strong oxide shell, which significantly affects superheating and melting of particles. The effects of geometric parameters and heating rate on characteristic melting and superheating temperatures and melting behavior of aluminum nanoparticles covered by an oxide shell were studied numerically. For this purpose, the multiphysics model that includes the phase field model for surface melting, a dynamic equation of motion, a mechanical model for stress and strain simulations, interface and surface stresses, and the thermal conduction model including thermoelastic and thermo-phase transformation coupling as well as transformation dissipation rate was formulated. Several nontrivial phenomena were revealed. In com- parison with a bare particle, the pressure generated in a core due to different thermal expansions of the core and shell and transformation volumetric expansion during melting, increases melting temperatures with the Clausius–Clapeyron factor of 60 K GPaÀ1. For the heating rates Q r 109 KsÀ1, melting tem- peratures (surface and bulk start and finish melting temperatures, and maximum superheating tempera- ture) are independent of Q. For Q Z 1012 KsÀ1, increasing Q generally increases melting temperatures and temperature for the shell fracture. Unconventional effects start for Q Z 1012 KsÀ1 due to kinetic Received 5th June 2016, superheating combined with heterogeneous melting and geometry. The obtained results are applied to Accepted 23rd September 2016 shed light on the initial stage of the melt-dispersion-mechanism of the reaction of Al nanoparticles. DOI: 10.1039/c6cp03897b Various physical phenomena that promote or suppress melting and affect melting temperatures and temperature of the shell fracture for different heating-rate ranges are summarized in the corre- www.rsc.org/pccp sponding schemes. Melting temperature of materials and melting mechanisms (including the effect of mechanics) for low6,7 and high10,11 depend on various parameters: size, shape, condition at the heating rates. Similar studies were performed for spherical surface, pressure (or, more generally, stress tensor), and heating particles without mechanics5,6 and with mechanics in quasi- rate, as well as on their interaction. Melting temperature depres- static formulation.6,7 Strong effects of the width of the external sion with reduction of the particle radius is well-known from surface and thermally activated nucleation were revealed within experiments,1,2 thermodynamic treatments,1,2 molecular dynamics the phase field approach in ref. 12. If the external surface of the simulations,3,4 and phase field studies without mechanics5,6 and material under study represents an interface with another solid, with mechanics (but without inertia effects).6,7 surface melting depends on the type of interface. The low-energy Reduction in surface energy during melting leads to pre- coherent interfaces increase energy during melting and, con- melting below melting temperature followed by surface melting sequently, suppress surface nucleation and promote super- and solid–melt interface propagation through the entire sample heating.13,14 On the other hand, an incoherent interface, whose with increasing temperature. This was studied using the phase energy reduces during melting, promotes surface melting.2 field approach for the plane surface analytically8,9 and numerically Hydrostatic pressure inside a shell which can be created for materials with volume expansion during melting suppresses p melting and increases equilibrium melting temperature T eq a Department of Aerospace Engineering, Iowa State University, Ames, Iowa 50011, according to the Clausius–Clapeyron relationship. The effect of USA. E-mail: [email protected] b Departments of Aerospace Engineering, Mechanical Engineering, and Material pressure appears automatically within the phase field approach 6,15 Science and Engineering, Iowa State University, Ames, Iowa 50011, USA. if proper thermodynamic potential is implemented. Under E-mail: [email protected]; Fax: +1 801 788 0026; Tel: +1 515 294 9691 non-hydrostatic internal stresses that relax during melting, This journal is © the Owner Societies 2016 Phys. Chem. Chem. Phys., 2016, 18, 28835--28853 | 28835 Paper PCCP e.g. under biaxial stresses due to constraint, melting tempera- leads to a wide spectrum of behavior from the reduction of the ture reduces. See thermodynamic11,16 and phase field11 treat- melting temperature due to size effect to a minor superheating ments for a layer. Melting temperature drastically decreases of up to 15 K32–35 due to sufficient time for stress relaxation. during very high strain-rate uniaxial compression in a strong Stress measurement in Al nanoparticles was performed in shock wave, as it was predicted thermodynamically and con- ref. 32 and 34–36. In contrast, fast heating with the rate higher firmed by molecular dynamics simulations.17 than 106–108 KsÀ1 can lead to the estimated superheating Metal can be kinetically superheated above its equilibrium by several hundred K due to the pressure increase37 because melting temperature when it is subjected to an extremely fast there is not sufficient time for phase transformations and other heating rate, for example, during irradiation by an ultra-fast laser stress relaxation mechanisms in the shell. For the higher with high energy, such as picosecond (ps) and femtosecond (fs) heating rates of 1011–1014 KsÀ1 used in experiments,38–40 both lasers. It has been observed in experiments18–20 and phase field the pressure-induced increase in melting temperature and kinetic simulations10,11 that an aluminum layer can be superheated up superheating are expected. to at least 1400 K,20 which is far above its equilibrium tempera- Thus, for understanding and quantifying melting of metallic ture, Teq = 933.67 K. The major reason for kinetic superheating, nanoparticles in a broad range of heating rates, one has to when heterogeneous surface melting initiates the process, is include and study the effect of an oxide shell and major physical the slower kinetics of solid–melt interface propagation than processes involved in melting, in particular, the effect of the heating.10,21 For very high heating rates Q Z 1012 KsÀ1, elastic generated pressure, kinetic superheating, heterogeneity of tem- wave propagation can affect the temperature of the material perature and stress fields, dynamics of elastic wave propagation, through thermoelastic coupling and melting temperature surface and interface energies and stresses, and coupling of the through the effect of stresses.22 Melting also influences the above processes. This is a basic outstanding multiphysics pro- temperature of materials through thermo-phase transforma- blem to be solved. Most of these processes strongly depend on tion coupling, mostly due to latent heat. the core radius Ri and the oxide shell thickness d; thus, their Thus, an analysis of kinetic superheating of materials effect should be studied in detail. should take several physical processes and their couplings into The understanding of the melting of Al nanoparticles at a account. Recently, there has been some research and suggested high heating rate is also very important for understanding and models23–27 to describe ultra-fast heating and melting with or controlling the mechanisms of their oxidation and combus- without mechanics, including thermoelastic coupling or thermo- tion.31,37,41 According to the melt-dispersion mechanism of the phase transformation coupling. However, those models neither reaction of Al particles,31,37,41 high pressure in the melt and describe a complete set of participated physical phenomena nor hoop stresses in the shell, caused by the volume increase include correct coupling terms rigorously derived from the during melting, break and spall the alumina shell. Then, the thermodynamic laws. Recently, we have developed a novel phase pressure at the bare Al surface drops to (almost) zero, while field model, which includes all of the above physical phenomena pressure within the Al core is not initially altered. An unloading and couplings in a single framework.10,11,22 spherical wave propagating to the center of the Al core generates a However, all the above modeling results have been obtained tensile pressure of up to 3 GPa at the center, which reaches 8 GPa for melting bare metallic nanostructures. In reality, metallic in the reflected wave. The magnitude of tensile pressure signifi- (e.g., Al, Fe, Cu, and others) particles and layers have a strong cantly exceeds the cavitation strength of liquid Al and disperses passivation oxide layer at the external surface. Thus, nano- the Al molten core into small bare drops. Consequently, the particles form a core–shell structure. The aluminum oxide or melt-dispersion mechanism breaks a single Al particle covered alumina passivation layer can be formed even at room tem- by an oxide shell into multiple smaller bare drops, which is perature28 by transporting Al cations driven by the non- not limited by diffusion through the initial shell. This mecha- equilibrium electrostatic field, the so-called Cabrera–Mott nism was extended for micron-scale particles42,43 and utilized mechanism.29,30 Aluminum oxide has a lower
Details
-
File Typepdf
-
Upload Time-
-
Content LanguagesEnglish
-
Upload UserAnonymous/Not logged-in
-
File Pages19 Page
-
File Size-