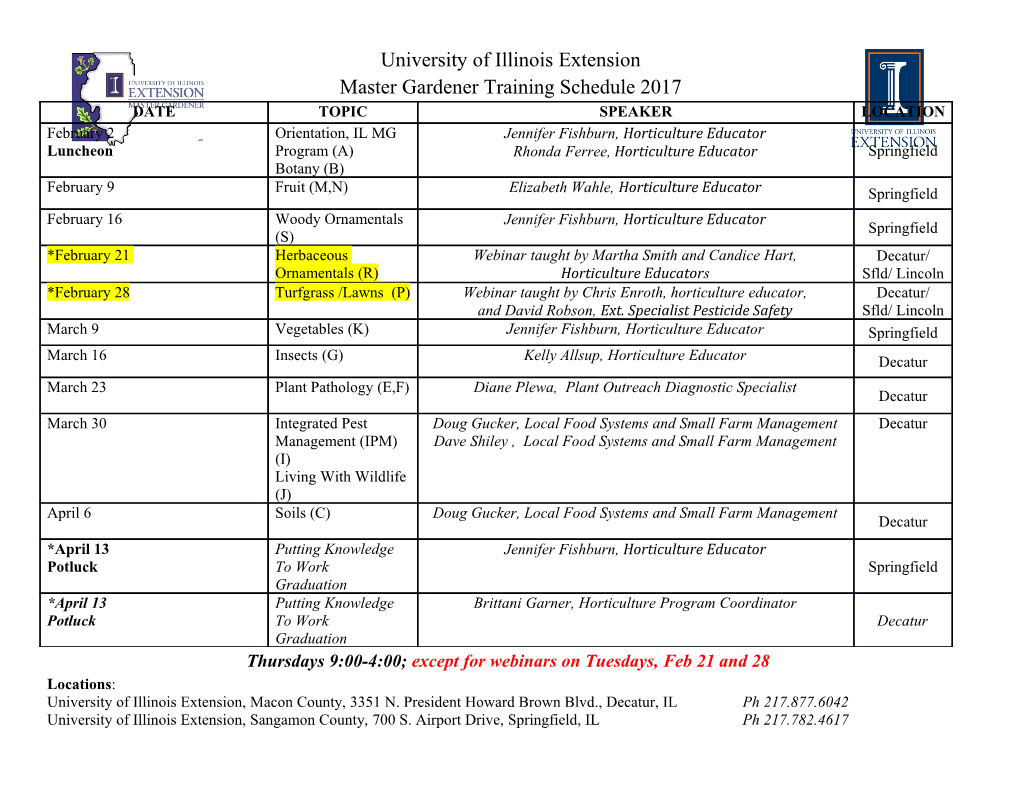
Project ANALYZE, CONSOLIDATE AND IMPROVE THE PRODUCT DEVELOPMENT PROCESS AT PARKER HANNIFIN QCDE Degree THROUGH IMPLEMENTATION OF DFMA PRINCIPLES Bachelor degree project in Product Design Engineering Level G2E 22,5 ECTS Autumn 2016 Sofia Barlas Adriana Buerba Supervisor: Nathanaël Kuipers Cosupervisor: Erik Brolin Company supervisor: Tobias Mattsson Examiner: Anna Brolin Bachelor Bachelor Assurance of own work This project report has on 27/01/17 been submitted by Sofia Barlas and Adriana Buerba to University of Skövde as a part in obtaining credits on basic level G2E within Product Design Engineering. We hereby confirm that for all the material included in this report which is not our own, we have reported a source and that we have not - for obtaining credits - included any material that we have earlier obtained credits within our academic studies. II Abstract Parker Hannifin QCDE aim to eliminate as much wasted time, materials and resources as achievable by implementing Design for Manufacturing and Assembly principles into a modified version of their Product Development Process. The modified Product Development Process was developed within this project with the objective of aiding the company to remain competitive within their field, as well as continue to efficiently develop and produce high quality products. A literature study was performed to gain a greater understanding of the multiple Design for Excellence methods and their possibilities to enhance the Product Development Process at Parker Hannifin QCDE. The literature study included various sources such as academic books and scientific articles. An empirical study was conducted and the use of the current Internal Product Development Process was evaluated in conjunction with a detailed evaluation of the designated coupling. An additional aspect that was explored includes an evaluation of the extent of Design for Manufacturing and Assembly that is implemented into the current Internal Product Development Process. The Generation chapter of this thesis outlines the sequence and process implemented for generating the modified Internal Product Development Process and implementing Design for Manufacturing and Assembly. The results of this thesis project included implementing Design for Manufacturing and Assembly in the form of checklists. The multiple Design for Excellence checklists were inspired in part by the information obtained from the literature study and the authors interpretation. The finished concept has been provided to Parker Hannifin QCDE in the form of a pamphlet including instructions of how to implement the checklists into the modified Internal Product development process. The discussion chapter within this report consists of a conclusion and deliberation regarding the methodology used within this thesis. The results obtained from this thesis have been dissected and evaluated along with implications and potential weaknesses in the work. III Table of Contents 1 INTRODUCTION 1 1.1 PROBLEM DESCRIPTION 1 1.2 AIM AND OBJECTIVES 1 1.3 METHODOLOGY 1 2 LITERATURE STUDY 4 2.1 CONCURRENT ENGINEERING 4 2.2 LEAN PRODUCT DEVELOPMENT 4 2.3 PRODUCT DEVELOPMENT AS A PROCESS 5 2.4 DESIGN FOR ASSEMBLY 6 DFA GUIDELINES 6 DFA AS AN EVALUATION METHOD 6 2.5 DESIGN FOR MANUFACTURING 8 RETHINKING THE CONCEPTUAL PRODUCT DESIGN BY FOCUSING ON DFM 9 MANUFACTURABILITY MEASURED IN EIGHT DIMENSIONS 10 2.6 DESIGN FOR MANUFACTURING AND ASSEMBLY 10 IMPLEMENTATION OF DFMA 10 2.7 DESIGN FOR ENVIRONMENT 11 2.8 SUMMARY OF THE LITERATURE STUDY 12 CONCURRENT ENGINEERING AND ITS CONNECTION TO DFMA 12 LEAN PRODUCT DEVELOPMENT AND ITS CONNECTION TO DFMA 12 DFA AND ITS CONNECTION TO DFMA 12 DFM AND ITS CONNECTION TO DFMA 12 DFE AND ITS CONNECTION TO DFMA 12 2.9 CONCLUSION; LITERATURE STUDY 13 3 EMPIRICAL STUDY AND DATA COLLECTION 14 3.1 INTERNAL PDP 14 3.2 ANALYSIS OF THE CURRENT INTERNAL PDP 17 RESULT OF THE INTERNAL PDP ANALYSIS 17 CONCLUSION; ANALYSIS OF THE INTERNAL PDP 17 3.3 WINOVATION PDP 18 3.4 ANALYSIS OF THE CURRENT WINOVATION PDP 18 RESULT OF THE WINOVATION PDP ANALYSIS 18 DISCUSSION AND CONCLUSION OF THE WINOVATION PDP ANALYSIS 18 3.5 PRODUCT DESCRIPTION 19 3.6 COMPONENT ANALYSIS 19 3.7 PART DESCRIPTION 19 DISCUSSION AND CONCLUSION CONCERNING THE PART ANALYSIS 21 3.8 DFA PROCESS AND RESULTS 21 3.9 DFA COMPLEXITY 21 RESULTS FROM THE DFA COMPLEXITY CALCULATIONS 22 3.10 DETERMINE RELATIVE PART COST LEVELS 22 3.11 COST BREAKDOWN 22 COST BREAKDOWN RESULTS 23 ANALYSIS OF ALL METRICS 23 3.12 FUNCTION ANALYSIS 24 FUNCTION ANALYSIS RESULTS 24 3.13 STANDARDIZING PARTS 25 RESULTS AND DISCUSSION OF THE PART STANDARDIZATION 25 3.14 THEORETICAL PART COUNT EFFICIENCY 25 IV RESULTS AND DISCUSSION OF THE THEORETICAL PART COUNT EFFICIENCY 25 3.15 OPPORTUNITY IDENTIFICATION 25 3.16 USER SCENARIO METHOD 26 CONCLUSION 26 3.17 SCALE QUESTIONS FOR THE PERSONNEL WITHIN THE IF/FF ASSEMBLY DEPARTMENT 26 CONCLUSION 26 3.18 STEPS TAKEN WITHIN THE IF/FF ASSEMBLY DEPARTMENT 27 3.19 ANALYZING AND DOCUMENTING THE STEPS TAKEN WITHIN THE IF/FF ASSEMBLY DEPARTMENT 28 RESULTS OF THE DOCUMENTED THE STEPS 29 CONCLUSION OF THE DOCUMENTED STEPS 29 3.20 STATIONS AND WORKSHEETS WITHIN THE IF/FF ASSEMBLY DEPARTMENT 29 RESULTS 30 CONCLUSION 30 3.21 DFM, SUPPLYING COMPANY FOR PARKER 31 CONCLUSION OF THE VISIT 32 3.22 SUMMARY OF THE EMPIRICAL STUDY 33 4 GENERATION 35 4.1 MIND MAPPING 35 CONCLUSION 36 4.2 BRAINSTORMING 36 4.3 BRAINSTORMING SESSION NR.1 36 RESULTS FROM FIRST BRAIN STORMING SESSION 36 CONCLUSION 37 4.4 BRAINSTORMING SESSION NR.2 37 RESULTS FROM THE SECOND BRAIN STORMING SESSION 37 CONCLUSION OF THE BRAIN STORMING SESSIONS 37 4.5 FUNCTION ANALYSIS METHOD 38 CONCLUSION 39 4.6 GENERATING THE FOUNDATION OF THE INTERNAL PDP 39 CONCLUSION 39 4.7 INTERNAL PDP GENERATION 40 4.8 INPUTS AND OUTPUTS WITHIN THE INTERNAL PDP 41 4.9 CHECKLIST GENERATION 41 4.10 DFA CHECKLIST 42 DFA CHECKLIST DESCRIPTION 43 4.11 DESIGN EFFICIENCY CHECKLIST 45 DESIGN EFFICIENCY CHECKLIST DESCRIPTION 45 4.12 DFM CHECKLIST 45 DFM CHECKLIST DESCRIPTION 46 4.13 DFE CHECKLIST 46 DFE CHECKLIST DESCRIPTION 46 4.14 LEAN PRODUCT DEVELOPMENT CHECKLIST 47 LEAN CHECKLIST DESCRIPTION 47 4.15 CONCURRENT ENGINEERING CHECKLIST 47 CONCURRENT ENGINEERING CHECKLIST DESCRIPTION 48 4.16 IMPLEMENTING THE CHECKLISTS INTO THE INTERNAL PDP 48 4.17 SUMMARY OF THE GENERATION CHAPTER 50 5 EVALUATION OF THE MODIFIED INTERNAL PDP 51 5.1 FOCUS GROUP; ENGINEER DEPARTMENT 51 RESULTS FROM THE FOCUS GROUP EVALUATION 51 V 5.2 FIRST CHECKLIST EVALUATION 51 DFA CHECKLIST 52 DESIGN EFFICIENCY CHECKLIST 52 DFM CHECKLIST 52 LEAN AND CONCURRENT ENGINEERING CHECKLISTS 53 5.3 FOCUS GROUP WITH THE CROSS-FUNCTION TEAM 54 RESULTS OBTAINED FROM THE CROSS-FUNCTION EVALUATION 54 5.4 DFA EVALUATION WITH THE LUCAS METHOD 55 HANDLING ANALYSIS 55 FITTING ANALYSIS 56 5.5 CONCLUSIONS OF EVALUATION 57 5.6 SUMMARY OF THE EVALUATION CHAPTER 57 6 FINAL CONCEPT 58 6.1 MODIFIED INTERNAL PDP 58 6.2 MODIFIED CHECKLIST 59 6.3 FINISHED PAMPHLET CONCEPT 59 7 DISCUSSION 60 7.1 PROBLEM DESCRIPTION 60 7.2 SCALE QUESTIONS FOR THE PERSONNEL WITHIN THE IF/FF ASSEMBLY DEPARTMENT 61 7.3 BEHAVIORAL MAPPING 61 7.4 MANUFACTURER VISIT AND DFM 62 7.5 MIND MAPPING 62 7.6 BRAIN STORMING 62 7.7 FOCUS GROUP; CROSS-FUNCTIONAL TEAM EVALUATION OF THE DFA CHECKLIST 63 7.8 CASE STUDY 63 8 SUGGESTIONS FOR FURTHER INVESTIGATION 64 VI 1 Introduction Parker Hannifin QCDE, Quick Coupling Division Europe, in Skövde primary focus is providing customers with high quality and reliable couplings for use in Climate Control, Construction, Forestry & Mining, Factory Automation, Food & Beverage, Industrial Manufacturing, Industrial Processing & Refining, Life Sciences & Healthcare, Off-Road Transportation, On Road, Rail & Marine Transportation and Power Generation, In order to remain competitive within their field, Parker Hannifin QCDE, henceforth Parker, seeks to improve their current Internal Product Development Process, henceforth PDP, with the help of DFMA, Design for Manufacturing and Assembly, in focus. Currently Parker’s product development primarily consists of modifying existing products to suit their client’s needs. These products are developed foremost with experience within the Parker personnel (internal expertise and judgement) of the company rather than following the steps within the PDPs. 1.1 Problem description The Internal PDP at Parker aligns with the larger PDP internationally used at all Parker locations, called Winovation, yet it is significantly reduced according to the number of steps, resources and time needed. Currently minimal documentation is performed regarding the amount of work applied and performed within the Internal PDP. Due to the lack of documentation, it is difficult for personnel as well as departments within Parker to advocate and confirm their work. The staff rarely executes the existing Internal PDP. This is due to the extent of time needed to perform the tasks within each section. The absence of a solid and beneficial process weakens the current PDP and can reduce the effectiveness of communication between Parker and their clients. The lack of post-launch communication between Parker and their clients has been highlighted as a major disadvantage and in need of immediate attention. 1.2 Aim and Objectives Parker aims to eliminate as much wasted time, materials and resources as possible within their current Internal PDP with the help of DFMA. The main objective of this project is to improve and simplify the Internal PDP at Parker for the company to remain competitive within their field, as well as continue to efficiently develop and produce high quality products. The foundations of the modified Internal PDP will be based on DFMA as requested by the company. To demonstrate that the modified Internal PDP is successful, an existing coupling provided by the company will be analyzed according to the new framework established.
Details
-
File Typepdf
-
Upload Time-
-
Content LanguagesEnglish
-
Upload UserAnonymous/Not logged-in
-
File Pages82 Page
-
File Size-