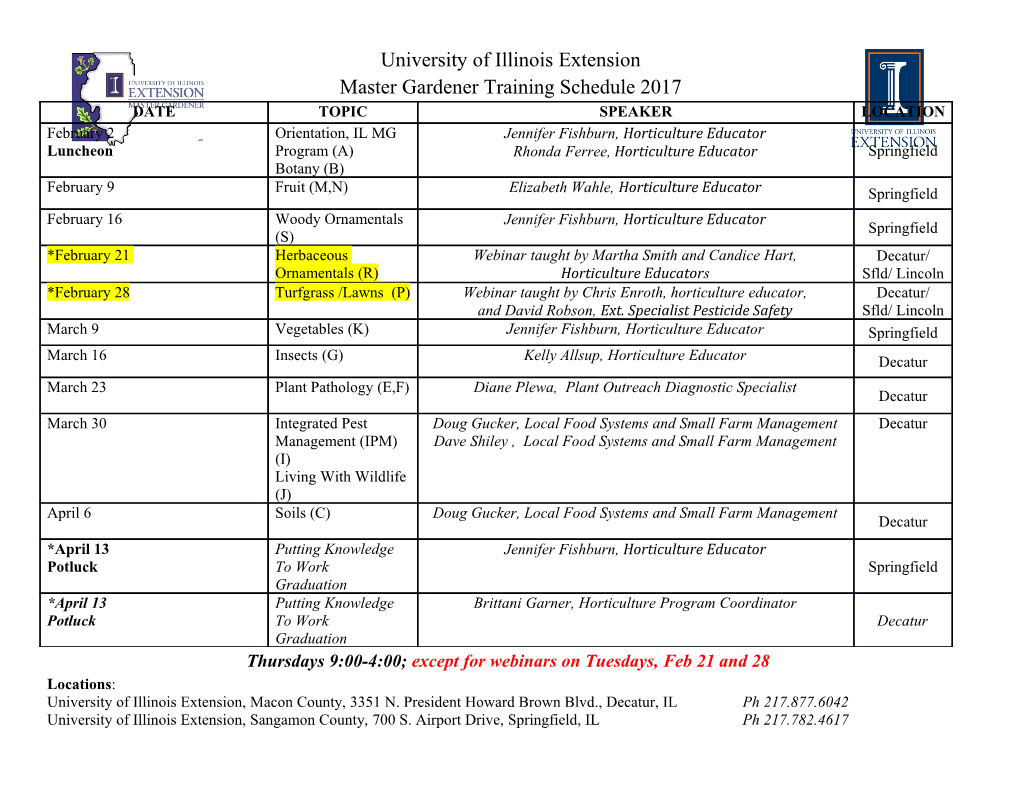
Final Report on Strategic Development of Bio-Energy (SDB) Project Technical report Combustion, Gasification & Propulsion Laboratory (CGPL) Department of Aerospace Engineering Indian Institute of Science Bangalore 560 012 SDB Report 2006, CGPL, Dept of Aerospace Engineering, IISc, Bangalore Page No.1 Page Nos. Contents EXECUTIVE SUMMARY 3 PART I Preface 10 Chapter I The Gasification Process 11 Chapter II Gasifiers with Biomass Briquettes and Low Grade 17 Fuels for Power Generation for Industrial Application Introduction Chapter III Biomass Gasification systems for High Grade 46 Thermal Application in the Industrial Sector Chapter IV Development of Power Package for Plastic Residues 51 and Effluents from the Industrial and Urban Wastes Chapter V Field Testing and Evaluations 58 PART II Preface 71 Chapter I Introduction and Literature Review 73 Chapter II Producer gas Properties 83 Chapter III The Experimental Work 85 Chapter IV Zero-Dimensional Model Formulation 116 Chapter V Laminar Burning Velocity Calculations 124 Chapter VI CFD Modelling 132 Chapter VII Predictions of Zero-D Model 151 Chapter VIII Adaptation of Cummins Gas Engines for Use with 186 Gasifiers for Power Generation Chapter IX Development of Environmentally Clean Applications 194 with Biomass Gasifiers for Power Generation Chapter X Overview 204 Chapter XI Non-Edible Seed-Oils for Power Generation with 207 Engines in Single or Dual Fuel Mode PART III Preface 225 Chapter I Package Development for Power Generation by 226 Coconut Shell Based Agro-Residue Gasification with Generation of Activated Carbon Chapter II Precipitated Silica from Rice Husk Ash 240 IPSIT (Indian Institute of Science Precipitated Silica Technology) Chapter III Biomass Preparation systems 244 Chapter IV Water Treatment for Gasification 259 SDB Report 2006, CGPL, Dept of Aerospace Engineering, IISc, Bangalore Page No.2 Executive Summary This work is related to developing and establishing a gasifier technology to handle a range of bio-fuels in a single system. The establishment of the gasifier technology implies the development of the reactor, the cooling and cleaning system, and aspects of biomass processing at appropriate scales, drying the biomass, and a process for treating the effluents (of the cooling water) so that they can be recycled. It was important to understand and establish the operation with a reciprocating gas engine on producer gas by doing necessary basic research as such a research has not been performed adequately internationally. Also the aspects of generating value added products like activated carbon and precipitated silica were intended to be addressed to improve the plant economics. This is the reason for terming this project Strategic Development of Bio-energy. As will be seen in this report, all the aims of this project have been fulfilled. It is relevant to bring out that this project is a sequel to another on pulverizable fuels, called “POBIG” that was intended to deal with mostly agro-residues like rice husk, and sugarcane trash. Towards the end of this project POBIG in 1997, the central issues on the boundaries of performance were clear. The key idea of obliterating the origins of the fuel by pulverizing them was considered reasonable to start with. Several aspects and differences of cyclone type gasifiers from solid fuel gasifiers were recognized, particularly because open top downdraft re-burn gasifiers were being tested in the laboratory and operated in the field for reasonable times It was only using wood or wood like agro-residues – coconut shell or corncobs (those with high density and low ash content) . These differences are brought out as under. a. The process of gasification in cyclone type systems needed control on the fuel and air flow rates on a continuous basis. The response time of the system being of the order of seconds would result in changes in air-to-fuel ratio too quickly. This would result in the operation deviating from the set value to both richer and leaner sides leading to compositional variations. This in itself can be combated by an intermediate storage. But if it went richer, the tar generated could become more than acceptable. In the case of solid fuel gasifiers of downdraft open top re-burn type, the air-to-fuel ratio adjustment would be self-governed over the turn-down ratio. b. A fundamental feature that was being researched during this period on liquid bio-fuels from thermo-chemical conversion route in different laboratories across the world became known. To produce higher liquid fraction from the biomass, the biomass had to be heated at a very high heating rate (about 1000 C/s). This was possible only if the fuel was pulverized. Thus the route that was being adopted through cyclone gasification was good for generating liquid fuels. If we take that larger fraction of liquid are generated in the cyclone gasifiers, it would be necessary to provide sufficient residence time in the high temperature zones inside the reactor for cracking down the liquids to gases. This was intended due to other aspects of the design and it was considered that the residence time would be adequate (about a few seconds). It must also be remarked that significant cracking would be taking place. Even so the “hot tar” level observed was in the range of a 1000 ppm, a value that is several times compared to what would be obtained in a solid fuel system. It was inferred that the operation of cyclone gasifiers had to accept this limitation because of the approach – using pulverized fuels. Hence, one would need to conclude that cyclone gasifiers SDB Report 2006, CGPL, Dept of Aerospace Engineering, IISc, Bangalore Page No.3 would not be able to produce engine quality gas unless there is more elaborate tar clean up system, something not required for a solid fuel gasification system. c. One could imagine that because the processing of the fuel limits itself to drying and pulverizing, there will be economic advantages in their use in this manner at least for thermal applications. Even if one were to overcome the fluctuations in the air-to-fuel ratio through a responsive control system, the fine particulate matter that would escape the cyclone gasifier would need to be captured to limit the emissions from any system that uses this approach. It was in consideration of these facts that it was thought more appropriate to add one additional step to pre-processing. The briquetting process could be expected to densify the biomass about a 1000 kg/m3. There was an accompanying economic benefit – transportation would be made more economic since the material is densified. Thus a new thinking process that was wholesome was put together. Biomass drying, pulverizing and briquetting could be contemplated at various locations and the material transported to the power station. This would allow distributed operations and hence greater job opportunities and a more professional power plant operation that receives prepared good fuel. This implied that one had to investigate the IISc design of open downdraft re-burn system to determine the design aspects for accepting the agro-residue based briquettes. Agro-residues are characterized by significant inorganic content and the presence of problematic inorganic element, namely, potassium. The problem posed by potassium in classical combustion systems used by high pressure boilers (for power generation) is that potassium compounds, more particularly, potassium oxide related deposits in the sections of boiler tubing in a manner that even soot blowing is inadequate to dislodge the deposits. Hence the heat transfer process is affected over a relatively short period of time and the entire tubing has to be replaced. The alternate solution is to use the fuel in a gasification system, clean the gas and use in the combustion system (or even a reciprocating engine). This creates another problem. Potassium salts have the propensity to bring down the ash fusion temperature. Most agro-residues carry with them varying amounts of potassium depending on the amount of fertilizer applied during the agricultural operations. It is therefore important to determine the ash fusion temperature and more particularly, if the briquettes have the problem of ash fusion when used in the gasification system. In the case of closed top systems, the local temperatures that are generated at locations close to the air injection nozzles, exceed 1300 0C in most cases. Such a condition is sure to lead to ash fusion and this will prevent the gasifier operation from the moment ash fusion has occurred. In the case of IISc design, there is facility to share the air flow between the open top and the side air nozzles; it is possible to control the temperature distribution through the reactor because the flow velocities and the oxygen levels will get controlled. In the case of large reactors for large power levels, the IISc design has to use air injection at multiple locations along the reactor to ensure that air flow is distributed across the section as uniformly as possible. The presence of significant amount of ash demands a positive way to extracting it and it was thought that the approach of shaking the grate would be far from being adequate and no where near a positive way of extraction. To achieve this, a screw extraction technique was adopted. This was developed over several laboratory experiments and field experiences. The way the char would arrange itself inside the bottom section, the flow velocities through the bed and in the bottom section had to be limited to ensure little material carry over into the cyclone (the next element in the flow path). A vertical grate was introduced and its height SDB Report 2006, CGPL, Dept of Aerospace Engineering, IISc, Bangalore Page No.4 was found critical to smooth operation. Subsequently, two short vertical grates were introduced.
Details
-
File Typepdf
-
Upload Time-
-
Content LanguagesEnglish
-
Upload UserAnonymous/Not logged-in
-
File Pages264 Page
-
File Size-