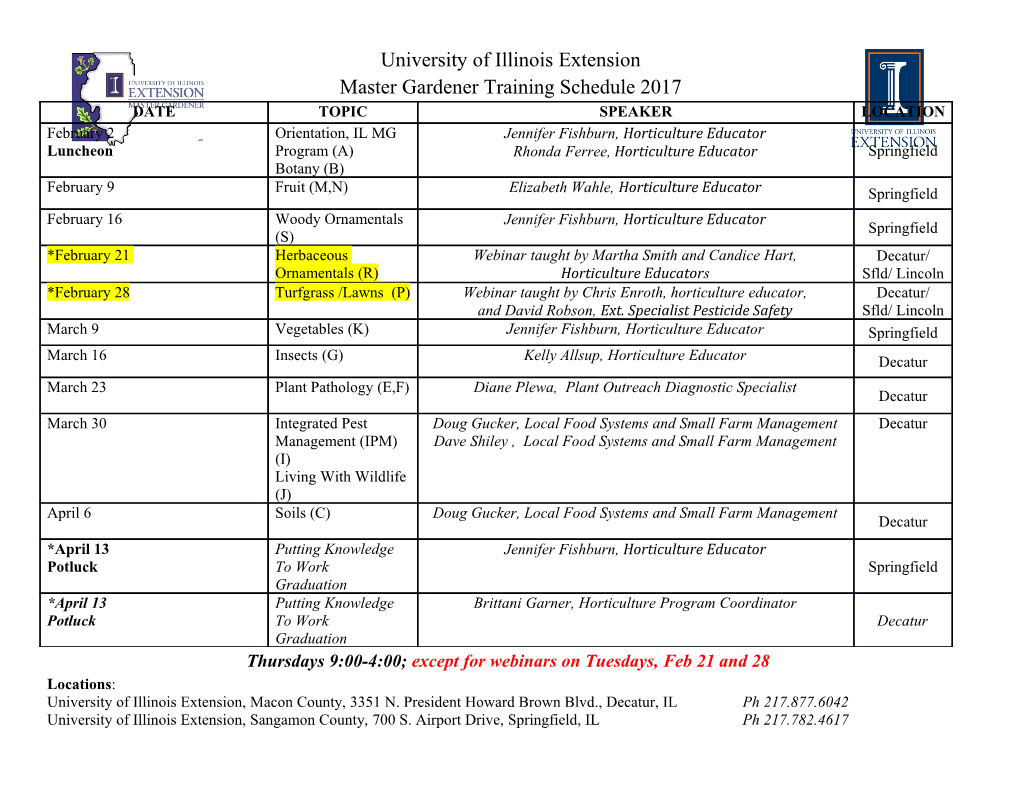
Modeling and Implementation of the Direct Torque Control Technique Used in a Relevant PV-powered Pumping Application Sebastien Jacques, Zahra Mokrani, Said Aissou, Djamila Rekioua, Toufik Rekioua To cite this version: Sebastien Jacques, Zahra Mokrani, Said Aissou, Djamila Rekioua, Toufik Rekioua. Modeling and Implementation of the Direct Torque Control Technique Used in a Relevant PV-powered Pumping Application. Journal of Electrical Engineering (JEE), 2018. hal-02296862 HAL Id: hal-02296862 https://hal-univ-tours.archives-ouvertes.fr/hal-02296862 Submitted on 25 Sep 2019 HAL is a multi-disciplinary open access L’archive ouverte pluridisciplinaire HAL, est archive for the deposit and dissemination of sci- destinée au dépôt et à la diffusion de documents entific research documents, whether they are pub- scientifiques de niveau recherche, publiés ou non, lished or not. The documents may come from émanant des établissements d’enseignement et de teaching and research institutions in France or recherche français ou étrangers, des laboratoires abroad, or from public or private research centers. publics ou privés. Journal of Electrical Engineering www.jee.ro Modeling and Implementation of the Direct Torque Control Technique Used in a Relevant PV-powered Pumping Application Sébastien JACQUES University of Tours, GREMAN CNRS UMR 7347 INSA CVL, Tours, France 7 avenue Marcel Dassault, 37200 Tours, France, Phone: +33 7 604 071 42, Email: [email protected] Zahra MOKRANI Said AISSOU Djamila REKIOUA Toufik REKIOUA Electrical Engineering Department, University of Bejaia, Algeria Bejaia, 0600, Algeria Abstract: The main purpose of this paper is to model and example, regarding brush DC motors, these conditions implement the direct torque control technique for driving a may increase the wear-out of the brushes and accelerate single phase induction motor in a low-cost and easily the breakdown of the commutator and bearings. The transportable photovoltaic-powered pumping system. To use of brushless DC (BLDC) motors makes it possible achieve this goal, a comparative investigation of the to partly overcome these difficulties. However, BLDC performance characteristics of different control techniques, such as closed loop scalar control (voltage/frequency) and motors need sophisticated electronic control circuitry as indirect field oriented control Technique, is presented. well as some way to continuously determine the From this study and according to complexity, robustness, position of the rotor [4]. difficulty of implementation and cost, an accurate and AC electric motors and particularly induction simple photovoltaic water pumping sys-tem is developed. motors (IM) have obtained special interests from the This system is based on a single-phase motor supplied by a industry since their invention. Indeed, these motors do three-phase inverter using the direct torque control method. not require mechanical commutation, separate- This standalone photovoltaic system is dedicated to water excitation or self-excitation for all or part of the energy pumping, especially in rural areas that have no access to transferred from stator to rotor, as for instance in DC national grid but have sufficient amount of solar radiation. motors. IM are currently used in variable-frequency Simulation modeling (Matlab / Simulink) and experimental drive (VFD) applications such as in variable-torque test results are presented to demonstrate the effectiveness and relevance of the proposed system designed for centrifugal fan, pump or compressor load applications industrial use. [5]. Despite some disadvantages such as high starting Key words: Direct torque control (DTC), single phase current and speed control that may uneasy to drive, the induction motor (SPIM), low cost and transportable reasons for this success are amongst others: higher photovoltaic pumping system. reliability due to the absence of brushes, higher robustness, easiness to build, inexpensive, and higher 1. Introduction efficiency (about 80%). However, the use of an For many years now, electric motors have been induction motor in any application is challenging, commonly used in a wide range of industrial because of its complex mathematical model, its non- applications such as fans, pumps, machine tools, linear behavior during saturation mode and the household appliances or, in an original way, electrical parameters’ oscillation which is particularly implantable medical devices [1,2]. Whatever the type temperature-dependent. As a consequence, the control of motor (direct current or DC, alternating current or of an induction motor is still a major issue [6]. AC), there are two key elements. The first one is In recent years, application of advanced control composed of an armature (a conductive coil) techniques has increased significantly for induction surrounded by a field magnet responsible for creating motor drive systems owing to the technological an electromotive force that causes the shaft to rotate, improvements, especially in power electronics and generating mechanical torque. The second one is a microprocessor technologies. commutator composed of a set of contacts attached to The scalar control, also called V/f control, well- the armature shaft. Its role is to keep reversing the known for its simplicity, was the first command direction of current flow in the armature as it turns, introduced in the industry. This technique consists in thus ensuring that the motor continues to turn. monitoring the induction motor speed by adjusting the Even if DC motors have a very long history, magnitude of stator voltages and frequency in such a including the fact that they offer the easiest way to way that the air gap flux is always maintained at the control the flux and torque in any application requiring desired value in steady-state. drives with variable speed and position, harsh Nevertheless, using this technique, field orientation applications (in particular, dry and warm of the motor is not used. Indeed, the frequency and the environments) can greatly affect their lifetime [3]. For voltage are the main control variables and are applied 1 Journal of Electrical Engineering www.jee.ro to the stator windings. The status of the rotor is implementation of the DTC method to control the ignored, meaning that no speed or position signal is fed induction motor. Then, a comprehensive overview of back. Therefore, torque can-not be controlled with any control techniques for electrical machines is proposed. degree of accuracy. The aim is to justify the choice of the DTC method. The field oriented control (FOC), which is one of The fourth section of this paper is dedicated to the the vector control methods, is currently a particularly DTC technique modeling and its relevance through interesting research area [7]. This technique consists in experimental measurements. Finally, a discussion is separately controlling the torque producing and proposed to compare the model outputs and test results. magnetizing flux components. Thus, the stator currents are represented by a vector. In a sense, the aim is to 2. Review of the Background and Motivations imitate DC motors’ operation by transforming a three Water pumping is one of the most significant phase time and speed de-pendent system into a two photovoltaic (PV) applications, especially to overcome coordinate time invariant sys-tem. The implementation the need for water in mountainous or remote locations of FOC may be complex because it requires current and improve isolated populations’ life. Moreover it regulator, coordinate transformation, generator of pulse reduces the negative impact of diesel installations on width modulation (PWM) signals and timers. the environment. For example, on average, for an Direct torque control (DTC) has been developed to operating time of 5 hours per day, 1,000 PV-pumps, re-place traditional PWM drives of the open- and each with a nominal power equal to 950 W, can closed-loop type used in FOC [8]. This method support the reduction of CO2 emissions by 4.2 tons a describes the way in which the control of torque and year. This positive outcome shows the interest of such speed are directly based on the electromagnetic state of a PV system in industrial applications, such as water the motor in comparison with PWM drives which use pumping [9]. input frequency and voltage. There are many benefits Although the single phase induction motor (SPIM) of the DTC technique: torque response, accurate torque is not widely accepted in literature, it can be an control at low frequencies, torque repeatability, motor excellent choice due to consideration of cost, static and dynamic speed accuracy. availability, simplicity of control and operation. The ultimate challenge of this paper is to model and Regarding irrigation and pumping water applications, implement the DTC technique to control a 370 W the water flow regulation is needed. The control induction motor used in a low-cost and easily techniques applied to induction machine allow this transportable photo-voltaic-powered pumping system regulation and offer the best performances [10,11]. (35 l/min). Figure 1 shows the general architecture of a PV First of all, the present manuscript describes the pumping system. application requirements and the reasons related to the Fig. 1. General architecture of the photovoltaic-powered pumping application. It is composed of six 80 Wp PV modules, a DC-DC The starting capacitance was suppressed to control the converter (boost converter) controlled by a maximum SPIM, and
Details
-
File Typepdf
-
Upload Time-
-
Content LanguagesEnglish
-
Upload UserAnonymous/Not logged-in
-
File Pages11 Page
-
File Size-