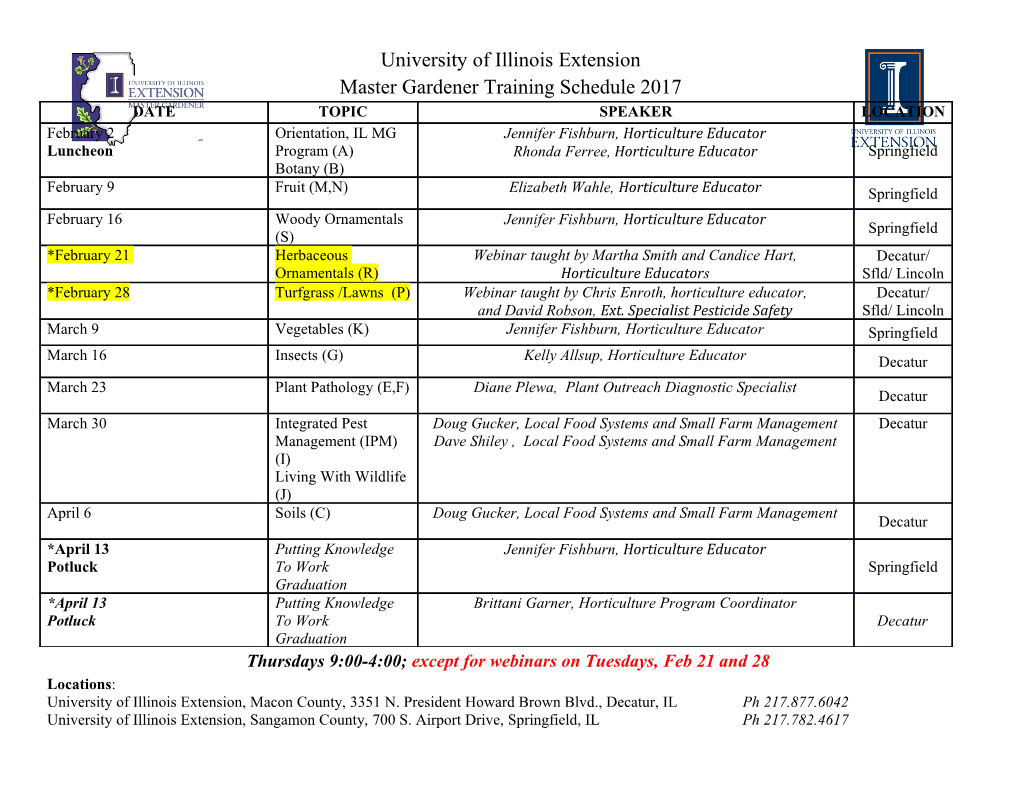
1.2.1 1.2.1-1 Introduction Different Types of Gasifi ers and Their Integration with What is gasifi cation? Gas Turbines Gasifi cation is a process in which combustible materials are partially oxi- dized or partially combusted. The product of gasifi cation is a combustible synthesis gas, or syngas. Because gasifi cation involves the partial, rather than complete, oxi- dization of the feed, gasifi cation processes operate in an oxygen-lean environment. As fi gure 1 indicates, the stoichiometric oxygen-to-coal ratio for combustion is al- most four times the stoichiometric oxygen-to-coal ratio for gasifi cation of Illinois #6 coal. Fig. 1. Diagram showing the products of reaction as a function of oxygen-to- coal ratio ( Reprinted from M. Ramezan, “Coal-based Gasifi cation Technolo- gies: An Overview” NETL Gasifi cation Technologies Training Course, Sept. 2004.) Just as most combustion-based processes such as power plants operate with excess oxygen to ensure complete conversion of the fuel, gasifi cation processes also typically operate above their stoichiometric oxygen-to-fuel ratio to ensure near com- plete conversion to syngas. The amount of oxygen used in gasifi cation, however, is Jeffrey Phillips always far less than that used in combustion and typically is less than half. In addition to coal, gasifi cation processes can use petroleum coke, biomass, EPRI / Advanced Coal Generation heavy oil, or even natural gas as the feedstock; however, this document will focus on P.O. Box 217097 coal gasifi cation processes. Charlotte, NC 28221 Comparison to coal combustion phone: (704) 595-2250 (advantages/disadvantages) email: [email protected] As indicated in fi gure 1, the products of reaction change signifi cantly as the oxygen-to-fuel ratio changes from combustion to gasifi cation conditions. These changes are summarized in table 1. Because the mixture under gasifying conditions is fuel-rich, there are not enough oxygen atoms available to fully react with the feed. Consequently, instead of producing CO2, the carbon in the feed is converted primar- ily to CO, and the hydrogen in the fuel is converted mostly to H2 rather than H2O. Both CO and H2 are excellent fuels for use in a combustion turbine; however, their combustion characteristics are signifi cantly different from natural gas. 67 Fig. 1. Diagram showing the products of reaction as a function of oxygen-to-coal ratio ( Reprinted from M. Ramezan, “Coal-based Gasification Technologies: An Overview” ( NETL Gasification Technologies Training Course, Sept. 2004.) Just as most combustion-based processes such as power plants operate with excess oxygen to ensure complete conversion of the fuel, gasification processes also typically operate above their stoichiometric oxygen-to-fuel ratio to ensure near complete conversion to syngas. The amount of oxygen used in gasification, however, is always far less than that used in combustion and typically is less than half. In addition to coal, gasification processes can use petroleum coke, biomass, heavy oil, or even natural gas as the feedstock; however, this document will focus on coal gasification processes. ���������� �� ���� ���������� �������������������������� As indicated in Fig. 1, the products of reaction change significantly as the oxygen-to-fuel ratio changes from combustion to gasification conditions. These changes are summarized in Table 1. Because the mixture under gasify conditions is fuel-rich, there are not enough oxygen atoms available to fully react with the feed. Consequently, instead of producing CO2, the carbon in the feed is converted primarily to CO, and the hydrogen in the fuel is converted mostly to H2 rather than H2O. Both CO and H2 are excellent fuels for use in a combustion turbine; however, their combustion characteristics are significantly different from natural gas. The implications of this will be fully covered in Section 3.1. Comparison of the primary products created by the ����� � Comparison of tTablehe pr im1 ary products created by the main fuel constituents in combustion and main fuel constituents in combustion and gasification gasification ���������� ������������ Carbon CO2 CO Hydrogen H2O H2 Nitrogen NO, NO2 HCN, NH3 or N2 Sulfur SO2 or SO3 H2S or COS Water H2O H2 TheThe fatefat eofo thef th fuel’se fuel ’nitrogens nitrog anden a sulfurnd su linfu ar igasificationn a gasific aprocesstion pr hasoce simportants has im pandort abeneficialnt and b econsequencesneficial on the environ- mental performance of an IGCC. Fuel-bound nitrogen, which is predominantly converted to NOx in combustion, is converted to N , consequences on the environmental performance of an IGCC. Fuel-bound nitrogen, which is 2 NH or HCN in gasification. As discussed in the “Syngas Clean-up Requirements” section of this chapter, both NH and HCN can be 3 predominantly converted to NOx in combustion, is converted to N2, NH3 or HCN in gasification3. As removed to very low levels with the resulting cleaned syngas having essentially no fuel-bound nitrogen. This significantly limits NOx emissionsd ofis canus IGCC.sed in the “Syngas Clean-up Requirements” section of this chapter, both NH3 and HCN can be Therem sulfuroved into fuelvery produceslow lev eSOls w init hcombustionthe result iprocessesng clean ebutd s isyn convertedgas havin tog eHssSe nandtia lCOSly no inf ugasificationel-bound n conditions.itrogen. As will This significantly limits NOxx emissions of an IGCC. 2 be described further on, both H2S and COS can be removed from the syngas using technology developed for the natural gas industry to levels of less than 20 ppm, which means that more than 99% of the sulfur can be removed from the fuel and will not be emitted as The sulfur in fuel produces SOx in combustion processes but is converted to H2S and COS in gasification SOx. Anotherconditi omajorns. A differences will be betweendescrib ecombustiond further o andn, b gasificationoth H2S an isd theCO amountS can b ofe rheatemo thatved isf rreleasedom the bysy nthega schemicalusing reactions. In combustion,techn allolo ofgy thede fuel’svelop chemicaled for th eenergynatur isal releasedgas ind uass theatry to (assuminglevels of itle isss fullythan converted),20 ppm, w buthic inh gasificationmeans that mostmor eof the fuel’s chemical energythan 9 9is% notof releasedthe sulf uasr cheat.an b eInr efact,mov aned importantfrom the measurefuel and ofw theill nefficiencyot be em ioftte ad gasificationas SOx. process is the fraction of the feedstock’s chemical energy, or heating value, which remains in the product syngas. This fraction is termed the “cold gas efficiency,” and most commercial-scaleAnother major d gasificationifference b eprocessestween co havembu as tcoldion agasnd efficiencygasificati oofn atis leastthe a65%mou andnt o somef hea exceedt that i s80%.rele a sed by the Becausechemic asignificantlyl reactions. lessIn cheatom bisu releasedstion, al lbyo ftheth egasificationfuel’s che process,mical en ite risg yimportantis releas toed limitas h etheat (amountassum iofng heatit is thatful lisy trans- ferred outc ofon theve rzoneted), wherebut in thega sgasificationification m reactionsost of th earefu occurring.el’s chem iIfca not,l en theerg ytemperaturesis not relea withinsed as thehe agasificationt. In fact, azonen could be too o o low to allowimp theort areactionsnt meas utor egoo fforwardthe eff i(aci eminimumncy of a ofga 1000sificaCti oorn 1800proceFs sisi stypicallythe frac neededtion of toth gasifye feed scoal).tock ’ sConsequently,chemical unlike a boiler whereene thergy ,entireor h efireboxating v isal ulinede, w hwithich water-filledremains in tubesthe p rthatodu capturect syng athes. heatThi sreleasedfractio nbyis theter mprocessed the and“co produceld gas steam, many gasifiers areeff refractory-linediciency,” and m withost cnoom watermer ccoolingial-sca ltoe gensureasific aasti olittlen pr heatoces lossses hasa vpossible.e a cold gGasifiersas effic ialsoenc ytypicallyof at le aoperatest 65% at elevated pressure, sometimes as high as 6.2 MPa (900 psia), which allows them to have very compact construction with minimum surface area and some exceed 80%. and minimal heat loss. Because significantly less heat is released by the gasification process, it is important to limit the amount of 1.2.1-2h e aGenerict that is tran sTypesferred ou oft of Gasifiersthe zone where the gasification reactions are occurring. If not, the temperatures within the gasification zone could be too low to allow the reactions to go forward (a minimum Movingo fBed1000ºC or 1800ºF is typically needed to gasify coal). Consequently, unlike a boiler where the entire Af idiagramrebox is ofli na egenericd with movingwater- fbedille dgasifiertubes isth shownat cap tinu rfiguree the 2.he Movingat relea sbeded gasifiersby the p areroc countercurrentess and produ flowce st reactorseam, in which the coal entersmany atg theasi ftopier sofa rthee r ereactorfracto randy-li naired orw oxygenith no wentersater cato othelin bottom.g to en s uAsre theas lcoalittle slowlyheat lo movesss as p downossib throughle. Gas ithefie rreactor,s it is gasifieda andlso ttheyp iremainingcally oper ashate dropsat ele voutate ofd pthere sbottomsure, s oofm theeti mreactor.es as h iBecausegh as 6 .of2 MtheP acountercurrent(900 psia), w flowhich arrangement,allows them theto heat of reaction fromhave theve rgasificationy compact reactionsconstruc tservesion w itoth pre-heatminimu them s coalurfa cbeforee area ita nentersd mi ntheim agasificationl heat loss .reaction zone. Consequently, the temperature of the syngas exiting the gasifier is significantly lower than the temperature needed for complete conversion of the coal. ������� ������� ����� �� ��������� ������ ��� A diagram of a generic moving bed gasifier is shown in Fig. 2. Moving bed gasifiers are countercurrent flow reactors in which the coal enters at the top of the reactor and air or oxygen enters at the bottom. As the coal slowly moves down through the reactor, it is gasified and the remaining ash drops out of the bottom of the reactor. Because of the countercurrent flow arrangement, the heat of reaction from the gasification reactions serves to pre-heat the coal before it enters the gasification reaction zone.
Details
-
File Typepdf
-
Upload Time-
-
Content LanguagesEnglish
-
Upload UserAnonymous/Not logged-in
-
File Pages11 Page
-
File Size-