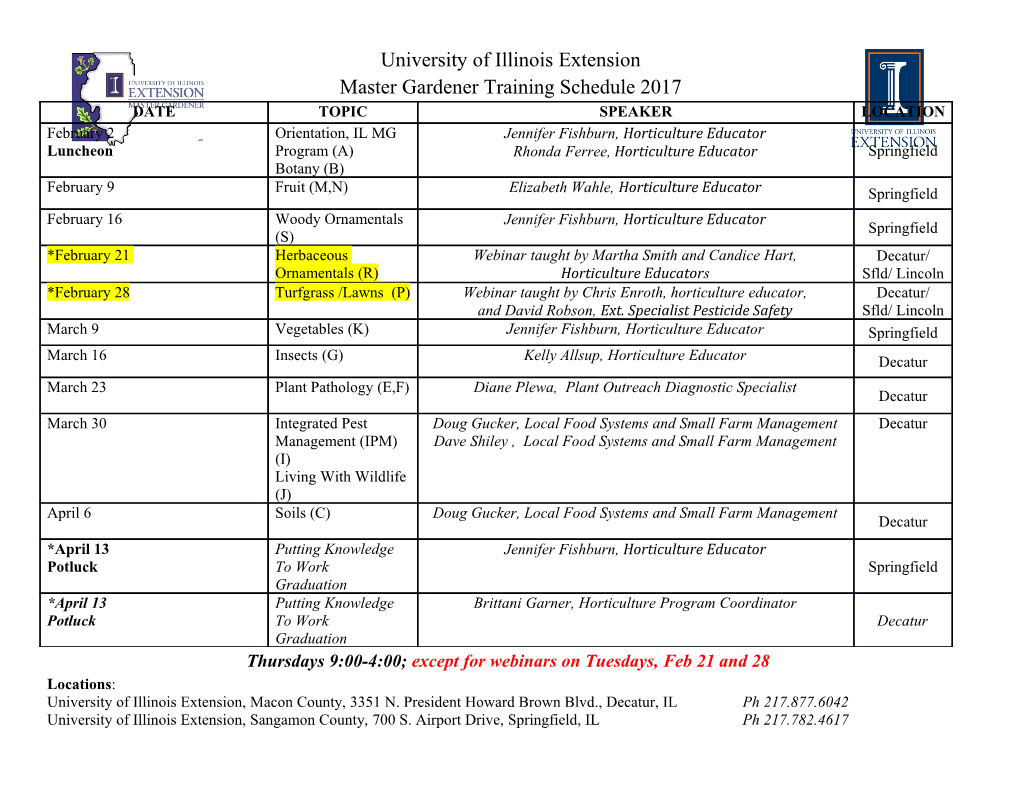
View metadata, citation and similar papers at core.ac.uk brought to you by CORE provided by Queensland University of Technology ePrints Archive Plasma-controlled metal catalyst saturation and the initial stage of carbon nanostructure array growth I. Levchenko, K. Ostrikov, D. Mariotti, and A. B. Murphy Citation: Journal of Applied Physics 104, 073308 (2008); doi: 10.1063/1.2996272 View online: http://dx.doi.org/10.1063/1.2996272 View Table of Contents: http://scitation.aip.org/content/aip/journal/jap/104/7?ver=pdfcov Published by the AIP Publishing Articles you may be interested in Plasma stabilisation of metallic nanoparticles on silicon for the growth of carbon nanotubes J. Appl. Phys. 112, 034303 (2012); 10.1063/1.4740468 Control of dense carbon nanotube arrays via hierarchical multilayer catalyst Appl. Phys. Lett. 99, 143104 (2011); 10.1063/1.3645625 Growth of carbon nanocone arrays on a metal catalyst: The effect of carbon flux ionization Phys. Plasmas 15, 103501 (2008); 10.1063/1.2988781 Plasma/ion-controlled metal catalyst saturation: Enabling simultaneous growth of carbon nanotube/nanocone arrays Appl. Phys. Lett. 92, 063108 (2008); 10.1063/1.2841845 Enhanced electron emission from carbon nanotubes through density control using in situ plasma treatment of catalyst metal J. Appl. Phys. 94, 487 (2003); 10.1063/1.1581377 [This article is copyrighted as indicated in the article. Reuse of AIP content is subject to the terms at: http://scitation.aip.org/termsconditions. Downloaded to ] IP: 131.181.251.131 On: Mon, 14 Jul 2014 23:11:30 JOURNAL OF APPLIED PHYSICS 104, 073308 ͑2008͒ Plasma-controlled metal catalyst saturation and the initial stage of carbon nanostructure array growth ͒ I. Levchenko,1,a K. Ostrikov,2,1 D. Mariotti,3 and A. B. Murphy2 1Plasma Nanoscience, School of Physics, The University of Sydney, Sydney NSW 2006, Australia 2CSIRO Materials Science and Engineering, P. O. Box 218, Lindfield NSW 2070, Australia 3Department of Microelectronic Engineering, Rochester Institute of Technology, Rochester, New York 14623, USA ͑Received 11 July 2008; accepted 18 August 2008; published online 14 October 2008͒ The kinetics of the nucleation and growth of carbon nanotube and nanocone arrays on Ni catalyst nanoparticles on a silicon surface exposed to a low-temperature plasma are investigated numerically, using a complex model that includes surface diffusion and ion motion equations. It is found that the degree of ionization of the carbon flux strongly affects the kinetics of nanotube and nanocone nucleation on partially saturated catalyst patterns. The use of highly ionized carbon flux allows formation of a nanotube array with a very narrow height distribution of half-width 7 nm. Similar results are obtained for carbon nanocone arrays, with an even narrower height distribution, using a highly ionized carbon flux. As the deposition time increases, nanostructure arrays develop without widening the height distribution when the flux ionization degree is high, in contrast to the fairly broad nanostructure height distributions obtained when the degree of ionization is low. © 2008 American Institute of Physics. ͓DOI: 10.1063/1.2996272͔ I. INTRODUCTION disorder and concentrate on the first factor and, in particular, on the early stages of nanostructure formation. Arrays of vertically aligned carbon nanostructures ͑e.g., The temporal nonuniformity of nanostructure formation nanotubes, nanorods, and nanocones͒ on a conductive sub- is determined by the conditions of their nucleation. In this strate are attractive for advanced technological applications work, we consider one of the most popular techniques for such as gas sensors,1 electron emitters,2 and various nano- nanostructure growth, namely, the catalytic process in which electronic devices.3–8 In most of these applications, high as- each vertically aligned nanostructure grows on a metal cata- pect ratio and vertically aligned nanostructures9 can sustain a lyst particle. Thus, the pattern of the nanostructure array rep- high electron current and strong electron field emission from licates the catalyst pattern, which is prefabricated on the sub- 13 the sharp tips, which often have a radius of curvature of strate surface. The catalyst pattern can be formed by several nanometers.10–12 various methods, for example, by chemical vapor deposition Such applications impose very strict requirements on the of a metal film onto a substrate surface followed by fragmen- height uniformity of the carbon nanostructures throughout tation of the film into an array of surface-bound metal 14 the entire array. Indeed, a nonuniform array that consists of nanoparticles. Most of these methods produce catalyst pat- nanostructures of different lengths cannot provide adequate terns with quite broad nanoparticle size distributions. Since emission parameters ͑e.g., current density and service life- the nucleation and growth of the nanostructures on catalyst time͒ due to overload. For example, very high emission cur- nanoparticles require complete saturation of the metal cata- ͑ ͒ ͑ rents from the tallest nanostructures eventually result in their lyst typically, Ni with carbon, a finite saturation time the ͒ overheating and the subsequent degradation of the sharp catalyst incubation time is required at the initial stage of nanostructure formation. During the incubation time, each emission tips. After burnout of the tallest nanostructures, catalyst nanoparticle is subject to a flux of carbon from the those nanostructures that then become the highest will in turn surface ͑the surface diffusion flux͒ and directly from the pro- be overloaded, and this process continues until the complete cess environment ͑the spatial flux͒. The time required to destruction of the entire array. It is apparent that the achiev- reach saturation for each individual catalyst nanoparticle de- able emission current and service lifetime are reduced in this pends on various factors, the most important being the nano- regime, and thus maximizing the height uniformity of the particle size ͑which determines the number of carbon atoms entire array of nanostructures is of paramount importance. that have to be dissolved in the nanoparticle͒ and the total Height nonuniformity of a nanostructure array is mainly carbon flux to the nanoparticle. The total time required for attributable to two factors: first the nonsimultaneous and un- saturation of the catalyst pattern is not important from the correlated nucleation and growth of individual nanostruc- point of view of the height nonuniformity of the nanostruc- tures, and second the nonuniformity in growth as a conse- tures. However, dispersion of individual saturation ͑incuba- quence of disordered distribution of the nanostructures on tion͒ times may lead to nonsimultaneous nucleation of the the substrate surface. In this work we do not consider spatial nanostructures on catalyst nanoparticles, and thus to nonuni- form growth.15,16 ͒ a Electronic mail: [email protected]. In a recent letter, we demonstrated that the use of a 0021-8979/2008/104͑7͒/073308/8/$23.00104, 073308-1 © 2008 American Institute of Physics [This article is copyrighted as indicated in the article. Reuse of AIP content is subject to the terms at: http://scitation.aip.org/termsconditions. Downloaded to ] IP: 131.181.251.131 On: Mon, 14 Jul 2014 23:11:30 073308-2 Levchenko et al. J. Appl. Phys. 104, 073308 ͑2008͒ TABLE I. Main simulation parameters. Parameter Notation Value Mean catalyst radius rm 2.5 nm Number of nanostructures in the pattern Nn 5000 Electron temperature in the Te 2eV low-temperature plasma 14 −3 Plasma density np up to 10 m Neutral gas temperature Tg 300 K Substrate bias US 20 V Surface coverage 0.1 ϫ FIG. 1. ͑Color online͒͑a͒ Balance of carbon fluxes on surface-bound cata- Total substrate area SS 1000 1000 nm ͑ ͒ lyst nanoparticles/carbon nanostructures and b the seven main stages of the Surface temperature Ts 800 K formation of the carbon nanostructure pattern on the surface: ͑1͒ nucleation Ion energy at the sheath edge 1.0 eV ͑ i of metal catalyst nanoparticles on the surface formation of the initial cata- Number of ions in Monte Carlo simulation N 2ϫ105 lyst pattern͒, ͑2͒ growth of metal catalyst nanoparticles on the substrate i Total carbon influx to the substrate ⌿ 0.1 ML s−1 surface, ͑3͒ carbon supply to the surface, formation of carbon fluxes on the C ϫ 13 −1 substrate surface between the catalyst nanoparticles, initial saturation of Frequency of lattice atom oscillations 0 3.3 10 s metal catalyst nanoparticles with carbon, ͑4͒ formation of carbon-saturated Time of deposition td 5–250 s metal nanoparticles, ͑5͒ nucleation of carbon nanostructures on the carbon- saturated metal catalyst particles, ͑6͒ growth of nanostructures nanocones on the carbon-saturated metal catalyst particles due to carbon influx through Ni, and ͑7͒ vertical growth due to carbon influx through Ni and carbon removal tation of the film. Second, the initial pattern evolves into a due to sputtering. The case of carbon nanotube growth is illustrated. This pattern with each catalyst nanoparticle of a size appropriate scenario is also applicable to CNCs and some other vertically aligned carbon ͑ nanostructures. for nanostructure nucleation and growth several nanom- eters͒. During these two initial stages, there is no carbon flux to the substrate surface. In the third stage, a carbon flux to plasma, or atomic fluxes of a high degree of ionization, en- the surface is provided to ensure saturation of the catalyst sures more simultaneous saturation of the metal catalyst with nanoparticles with carbon; in this stage, the carbon is pre- carbon.15 In this work we have significantly expanded the dominantly deposited on the substrate surface between the range of the nanostructures and physical effects considered metal nanoparticles, from where it can diffuse along the sur- by taking into consideration the nucleation and growth of the face to the nanoparticles. During the next stage, the catalyst carbon nanotubes and nanocones on partially saturated metal nanoparticles start to reach conditions suitable for nanostruc- catalyst nanoparticles.
Details
-
File Typepdf
-
Upload Time-
-
Content LanguagesEnglish
-
Upload UserAnonymous/Not logged-in
-
File Pages9 Page
-
File Size-