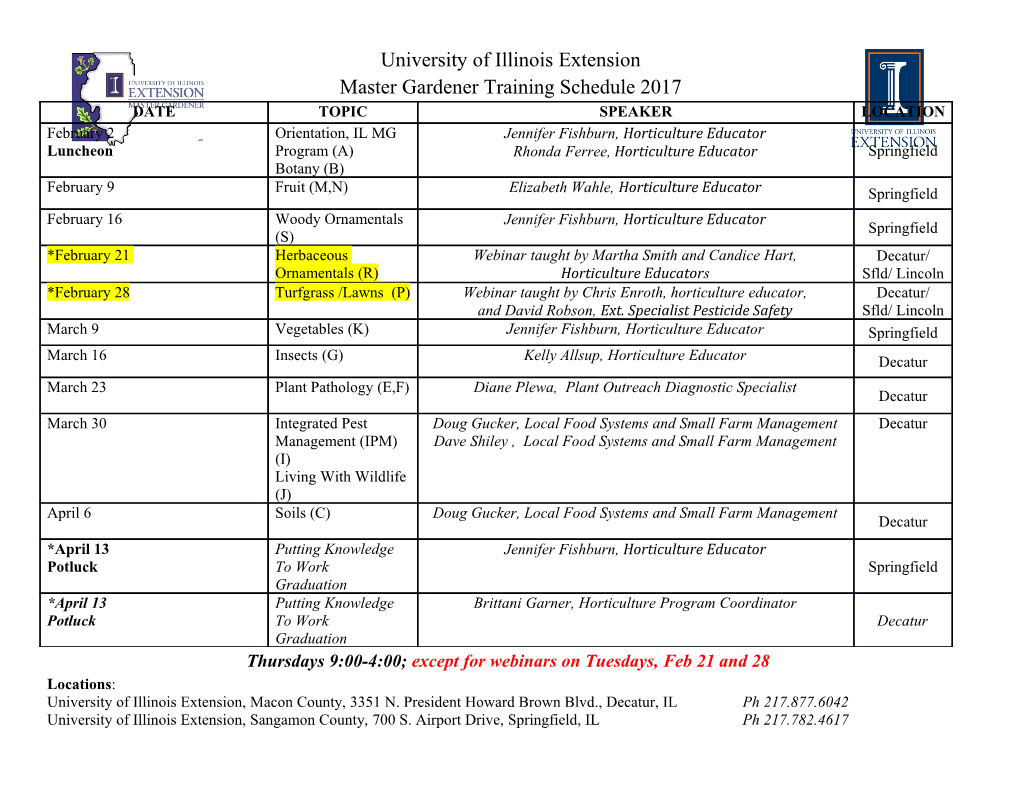
OVERVIEW OF CYANIDE TREATMENT METHODS Michael M. Botz Elbow Creek Engineering, Inc. [email protected] ABSTRACT cyanide is also used in low concentrations as a flotation reagent for the recovery of base metals An integral and key component of many water such as copper, lead and zinc. At these management systems at mining sites is the operations, cyanide treatment systems may be approach adopted to manage cyanide-containing required to address potential toxicity issues in solutions and slurries. Excluding the bulk regard to wildlife, waterfowl and/or aquatic life. storage of cyanide reagents such as sodium This may include the removal of cyanide from cyanide, most cyanide present at mining sites one or more of the following: will be present in water solutions. Therefore, to a great extent the management of water and the Slurry tailings from milling operations management of cyanide can be considered as one and the same and should be simultaneously Bleed solution from Merrill-Crowe considered when developing water management operations and cyanide management plans. Excess solution from heap or vat leaching All mining sites that utilize cyanide for metals operations recovery should have a comprehensive and well- maintained cyanide management plan. A good Supernatant solution from tailings cyanide management plan will include impoundments descriptions of how cyanide-containing solutions and slurries are to be handled, stored, contained Seepage collected from ponds or tailings and monitored, and in many cases the plan will impoundments also include a description of treatment plants used to remove cyanide from solutions or The term ‘cyanide’ refers to one of three slurries. This article is included in this special classifications of cyanide, and it is critical to edition of Mining Environmental Management to define the class of cyanide that is to be removed describe cyanide treatment processes that have in a treatment plant. The three classes of cyanide been successfully proven on a full-scale at a are: (1) total cyanide; (2) weak acid dissociable number of mining sites worldwide. (WAD) cyanide; and (3) free cyanide as shown in Figure 1. BACKGROUND In the mining industry, cyanide is primarily used for extracting silver and gold from ores, but 1 Overview of Cyanide Treatment Methods Strong Metal-Cyanide Complexes of Fe Weak and Moderately Strong Total Metal-Cyanide Complexes of Cyanide WAD Ag, Cd, Cu, Hg, Ni and Zn Cyanide Free CN- Cyanide HCN Figure 1 Classifications of Cyanides The appropriate selection for most situations is CYANIDE DESTRUCTION WAD cyanide since this includes the toxicologically important forms of cyanide, Most cyanide destruction processes operate on including free cyanide and moderately and the principle of converting cyanide into a less weakly complexed metal-cyanides. Total toxic compound through an oxidation reaction. cyanide includes free cyanide, WAD cyanide There are several destruction processes that are plus the relatively non-toxic iron-cyanide well proven to produce treated solutions or complexes. slurries with low levels of cyanide as well as metals. Cyanide treatment processes are classified as either a destruction-based process or a recovery- INCO Sulfur Dioxide/Air based process. In a destruction process, either The sulfur dioxide (SO2) and air process was chemical or biological reactions are utilized to developed by INCO Limited in the 1980’s and is convert cyanide into another less toxic currently in operation at over thirty sites compound. Recovery processes are a recycling worldwide. The process utilizes SO2 and air in approach in which cyanide is removed from the the presence of a soluble copper catalyst to solution or slurry and then re-used in a oxidize cyanide to the less toxic compound metallurgical circuit. cyanate (OCN-). - Cu 2 Catalyst Selection of an appropriate cyanide treatment SO2 + O2 + H2O + CN - -2 + process involves the consideration of many OCN + SO4 + 2H factors, but generally the number of candidate processes for a particular application can be The primary application of the sulfur dioxide and narrowed following an inspection of the air process is with slurry tailings, but it is also untreated solution/slurry chemistry and the effective for the treatment of solutions for the desired level of treatment. In the following oxidation of free and WAD cyanides. Iron sections, several destruction and recovery cyanides are removed in the process through processes are discussed along with their typical precipitation of insoluble copper-iron-cyanide areas of application. With all of these processes, complexes. laboratory and/or pilot testing is required to confirm the level of treatment achievable and to evaluate the associated reagent consumptions. 2 M. Botz Overview of Cyanide Treatment Methods The theoretical usage of SO2 in the process is The primary application of the hydrogen - 2.46 grams SO2 per gram of CN oxidized, but in peroxide process is with solutions rather than practice the actual usage ranges from about 3.5 slurries due to the high consumption of hydrogen - to 4.5 grams SO2 per gram of CN oxidized. The peroxide in slurry applications. The process is SO2 required in the reaction can be supplied typically applied to treat relatively low levels of either as liquid sulfur dioxide or as sodium cyanide to achieve cyanide levels that may be metabisulfite (Na2S2O5). suitable for discharge. The hydrogen peroxide process is effective for the treatment of solutions Oxygen (O2) is also required in the reaction and for the oxidation of free and WAD cyanides, and this is generally supplied by sparging iron cyanides are removed through precipitation atmospheric air into the reaction vessels. The of insoluble copper-iron-cyanide complexes. As reaction is typically carried out at a pH of about indicated in the above reaction, hydrogen 8.0 to 9.0 in one ore more agitated tanks, and peroxide reacts to form cyanate and water, a lime is added to neutralize the acid (H+) formed process which limits the build-up of dissolved in the reaction to maintain the pH in this range. solids in the solution being treated. Lime usage is generally on the order of about 3.0 - to 5.0 grams per gram of CN oxidized. As The theoretical usage of H2O2 in the process is +2 - indicated, copper (Cu ) is required as a catalyst, 1.31 grams H2O2 per gram of CN oxidized, but which is usually added as a solution of copper in practice the actual usage ranges from about - sulfate (CuSO4-5H20) to provide a copper 2.0 to 8.0 grams H2O2 per gram of CN oxidized. concentration in the range of about 10 to 50 The H2O2 used in the process is typically mg/L. Upon completion of the indicated provided as a liquid in 50% strength. reaction, metals previously complexed with cyanide, such as copper, nickel and zinc, are The reaction is typically carried out at a pH of precipitated as metal-hydroxide compounds. about 9.0 to 9.5 for optimal removal of cyanide and metals such as copper, nickel and zinc. This process is capable of achieving low levels However, if iron cyanide must also be removed of both cyanide and metals. Generally, the best to low levels, then the pH is lowered somewhat application of this process is with slurries to increase the precipitation of copper-iron- containing low to moderately high initial levels cyanides at the expense of lowering the removal of cyanide when treated cyanide levels of less efficiencies of copper, nickel and zinc. As than about 1 to 5 mg/L are required. In some indicated, copper (Cu+2) is required as a soluble cases, solutions treated with this process may be catalyst, which is usually added as a solution of of suitable quality to permit their discharge. copper sulfate (CuSO4-5H20) to provide a copper concentration in the range of about 10% to 20% Hydrogen Peroxide of the initial WAD cyanide concentration. Upon The hydrogen peroxide treatment process completion of the indicated reaction, metals chemistry is similar to that described for the previously complexed with cyanide, such as INCO process, but hydrogen peroxide is utilized copper, nickel and zinc, are precipitated as rather than sulfur dioxide and air. With this metal-hydroxide compounds. process, soluble copper is also required as a catalyst and the end product of the reaction is cyanate. - Cu 2 Catalyst - H2O2 + CN OCN + H2O 3 M. Botz Overview of Cyanide Treatment Methods This process is capable of achieving low levels cyanide is converted to cyanogen chloride of both cyanide and metals. Generally, the best (CNCl) and the second step in which cyanogen application of this process is with solutions chloride hydrolyzes to yield cyanate. containing relatively low initial levels of cyanide - - when treated cyanide levels of less than about 1 Cl2 + CN CNCl + Cl mg/L are required. Oftentimes, solutions treated - - + with this process may be of suitable quality to CNCl + H2O OCN + Cl + 2H permit their discharge. In the presence of a slight excess of chlorine, Caro’s Acid cyanate is further hydrolyzed to yield ammonia Peroxymonosulfuric acid (H2SO5), also known in a catalytic type of reaction. as Caro’s acid, is a reagent used in a recently developed cyanide treatment process that has - Cl2 Catalyst OCN + 3H2O found application at a few sites. + - - NH4 + HCO3 + OH - - -2 + H2SO5 + CN OCN + SO4 + 2H If sufficient excess chlorine is available, the reaction continues through ‘breakpoint Caro’s acid used in the process must be produced chlorination’ in which ammonia is fully oxidized on-site using sulfuric acid and hydrogen to nitrogen gas (N2). peroxide since Caro’s acid decomposes rather quickly (Norcross, 1996). Caro’s acid is used in + - + 3Cl2 + 2NH4 N2 + 6Cl + 8H slurry treatment applications where the addition of a copper catalyst is not desirable, which is In addition to reacting with cyanide, cyanate and typically only in situations where the sulfur ammonia, the alkaline chlorination process will dioxide and air process is not suited.
Details
-
File Typepdf
-
Upload Time-
-
Content LanguagesEnglish
-
Upload UserAnonymous/Not logged-in
-
File Pages10 Page
-
File Size-