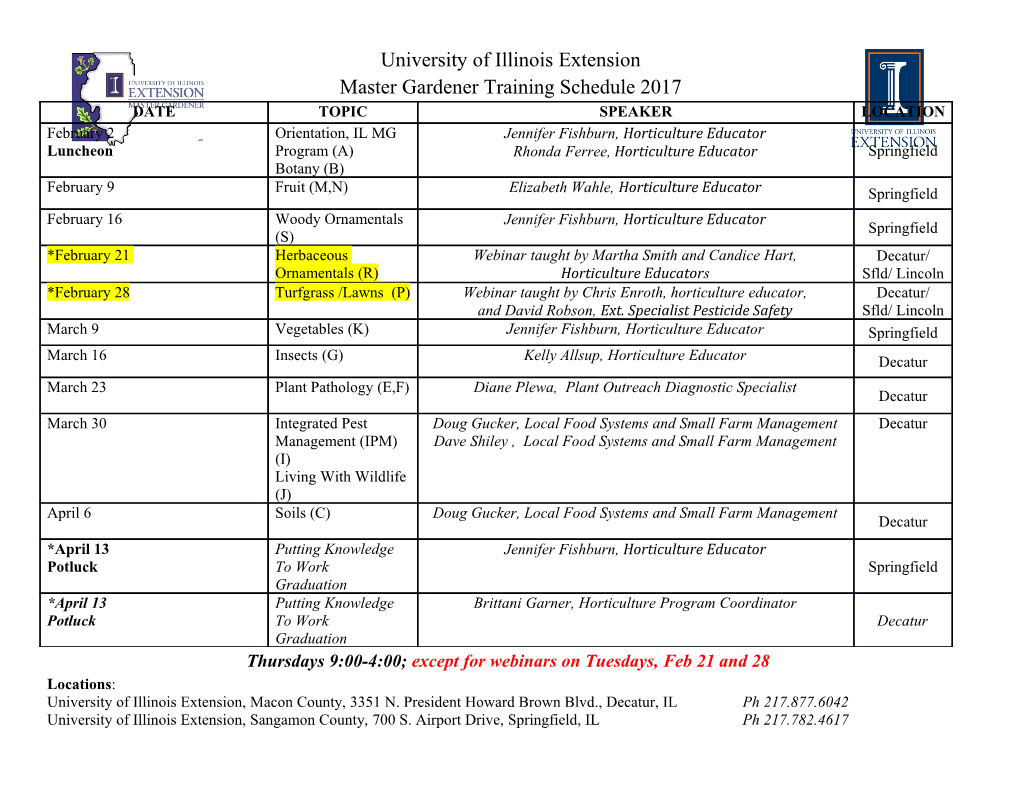
2007:14 DOCTORAL T H E SI S Influence of Green Pellet Properties on Pelletizing of Magnetite Iron Ore Seija Forsmo Luleå University of Technology Department of Chemical Engineering and Geosciences Division of Process Metallurgy 2007:14|: -1544|: - -- 07⁄14 -- Influence of Green Pellet Properties on Pelletizing of Magnetite Iron Ore Seija Pirkko Elina Forsmo Doctoral Thesis Lule Department of Chemical Engineering and Geosciences Division of Process Metallurgy SE-971 87 Lule Sweden 2007 Cover illustration: A schematic drawing visualizing the influence of green pellet properties on pelletizing of magnetite iron ore. Mechanical strength in green pellets (sphere on top): A SEM image showing packing of particles on the surface of a green pellet. Oxidation (sphere to the left): A microscope image showing hematite needles in a partially oxidized green pellet. Sintering (sphere to the right): A SEM image showing the structure in a sintered pellet. Magnetite iron ore green pellets are produced by balling moist concentrates to green pellets, which are then dried, oxidized to hematite, sintered, cooled and transported to steelmaking plants. The existing theory for balling is based on the capillary theory, but its applicability under industrial balling conditions is unclear. The aim of this study has been to clarify the principal mechanisms controlling the properties of iron ore green pellets. Special attention has been paid to studying how variations in raw material fineness influence green pellets behaviour during balling, oxidation and sintering. This knowledge of the principal mechanisms is needed to provide a sound basis for a successful process control strategy. The applied approach was to further develop the laboratory methods used in green pellet characterization. Oxidation in green pellets was measured by thermogravimetry and sintering was followed by dilatometry. A new measuring device for the characterization of green pellet strength was built and a new measuring method for green pellet plasticity was developed. The optimum moisture content in balling was defined as the moisture content resulting in a given degree of plasticity in green pellets. Pellet feeds with steeper particle size distributions required a higher moisture content in balling. Properties of green pellets prepared from different raw materials should be compared at constant plasticity (under realistic balling conditions), not at constant moisture content, as has been done earlier. At constant plasticity and with 0.5% bentonite binder, variations in the fineness of the magnetite concentrate did not influence the green pellet wet strength, within the limits studied in this work. This is because in the presence of the bentonite binder, green pellet wet strength was mainly controlled by the viscous forces of the binder liquid. A marked degradation in green pellet mechanical strength both in wet and dry states was found in the presence of a surface-active flotation collector reagent. This loss in green pellet quality was explained by a strong attachment of air bubbles in the green pellet structure. High-speed camera images showed multi- breakage patterns due to crack propagation between the air bubbles. This explains the increased generation of dust observed at the pellet plant. The negative effects of the flotation collector reagent on balling diminished during storage of the pellet feed. The results emphasize the importance of minimizing the reagent dosages in flotation and maximizing the residence time of the pellet feed in the homogenizing storage before balling. When a pellet starts to oxidize, a shell of hematite is formed while the pellet core is still magnetite. Thermal volume changes in these two phases were studied. Sintering in the magnetite phase started earlier (950 1 phase (1100Therefore, the difference in sintering rates between the magnetite and hematite phases was largest at around 1100oC. The sintering rate increased in both phases with increasing fineness in the magnetite concentrate. A finer grind in the raw material would, therefore, promote the formation of the unwanted duplex structures with a more heavily sintered core pulling off from the shell. At constant original porosity in green pellets, the oxidation rate decreased as the magnetite concentrate became finer, because of the enhanced sintering. However, in practical balling, finer raw materials would necessitate the use of more water in balling, which results in an increase in green pellet porosity. These two opposite effects levelled out and the oxidation time became constant. Under process conditions, differences in the duplex structure would still be expected. This is because only partial oxidation takes place before sintering in the kiln. Olivine, which is used as an additive in LKAB blast furnace pellets, was found to initiate the dissociation of hematite back to magnetite already at temperatures that can occur during oxidation in the PH zone. The rate of dissociation was largely influenced by the olivine fineness. If the dissociation temperature is exceeded, the resulting decrease in the oxidation rate increases the size of the un-oxidized core exposed to sintering before oxidation. Also, dilatometer measurements showed opposite thermal volume changes in the oxidized hematite shell and in the magnetite core in the presence of olivine. Dissociation caused a large volume increase in the oxidized hematite shell, while the olivine addition further enhanced the sintering of the magnetite core. These mechanisms lead to increased structural stress between the hematite shell and the magnetite core. This knowledge was applied at the LKAB Svappavaara pelletizing plant. Coarser grinding of the olivine additive resulted in a marked improvement in the low- temperature reduction strength (LTD) in pellets. The final conclusion, then, is that excessive grinding of the pelletizing raw materials, both the magnetite concentrate and the additives, can cause severe problems and step-wise changes in the oxidation and sintering mechanisms without resulting in any additional gain in terms of green pellet mechanical strength. The capillary theory failed to describe the properties of wet green pellets under industrial balling conditions. The results also clearly point out that continuous in raw material properties would cause complex fluctuations in both balling and induration. Agglomeration; Pelletizing; Iron ore; Magnetite; Green pellets; Oxidation; Dilatation; Particle size 2 !" !! I wish to thank the Agricola Research Centre (ARC) for giving me the possibility to perform these studies. I also wish to thank my company, Luossavaara- Kiirunavaara AB (LKAB), for encouraging me to accomplish this thesis. I have been met with enthusiasm and interest at LKAB. I hope I managed to fulfil at least some of your high expectations. My sincerest thanks go to my supervisors, Professor Bo Bj at LTU, Division of Process Metallurgy and Per-Olof Samskog, Manager Strategic Research Projects at LKAB. You both have an extraordinary ability to find the essential questions. I am deeply grateful for your highly valuable and kind advice. I have felt very confident in working under your guidance. Per-Olof, you have been my boss at LKAB for 17 years. You have worked persistently through all these years to make this research possible. You also convinced me that I would manage with the doctoral studies and finally, when ARC was established, I took the challenge. I am most grateful for your initiative and support. I also want to thank Professor Willis Forsling, the leader of ARC, for all the conferences: I enjoyed them. Thanks also for introducing me to the press and giving me a chance to try a career as a movie star ,Iwasalsogiventhe opportunity to attend the inspiring lectures of such luminaries as Professors John Ralston, Janusz Laskowski and J Building of the Pellet Multi Press instrument was one of the major breakthroughs in the practical laboratory work. We started by building a simple prototype, but I soon understood that what we really needed was an accurate instrument with comprehensive software. Building the Pellet Multi Press was teamwork at its best. Running the first samples and taking the first films was like opening Christmas presents. Many people were involved in this development work. Special thanks go to my colleagues Anders Apelqvist and Kjell-Ove Mickelsson for their competent way of running the development project and making the dreams come true. I also want to thank the external companies involved: Urban Holmdahl at Optimation AB, John Erik Larsson at MBV systems AB and Thomas Nordmark, Dan R ! "$-Benima. My present supervisor, Kent Tano, General Manager Process Technology at LKAB, thank you for your encouragement and for allowing me the time to write this thesis. It is a pleasure working with you. Thanks also to all my colleagues at LKAB R&D who have encouraged me during the studies. Special thanks go to Sten-Evert Forsmo for our inspiring discussions concerning problems and possibilities in agglomeration and for Magnus Rutfors for our discussions about balling in full scale. To Anders Apelqvist, I extend my sincerest thanks for the 3 numerous times you have helped me with data handling problems of various kinds. Lena Fjellstr%many thanks for your energetic and initiative work with implementing the new knowledge of green pellet properties at LKAB. Anna- Karin Rosberg, thank you for your help with studying the behaviour of bentonite suspensions. I also want to acknowledge Benny Andreasson, Manager Minerals Process Technology at LKAB, for his work as a project leader during the reconstruction of the olivine grinding circuit at the LKAB Svappavaara plants. Many thanks also to Eva Alld&-') *, Senior Process Engineer at LKAB and my former colleague at R&D, for your co-operation and support. I have had the pleasure to work at LKAB surrounded by glad and enthusiastic people. Maria Rova and Maria Johansson, many thanks for your excellent work with micro-balling and for your efforts during the in-house training sessions. Carola Yngman, thank you for launching the new porosity measurement in daily use at the Metallurgical Laboratory and for preparing the polished samples.
Details
-
File Typepdf
-
Upload Time-
-
Content LanguagesEnglish
-
Upload UserAnonymous/Not logged-in
-
File Pages235 Page
-
File Size-