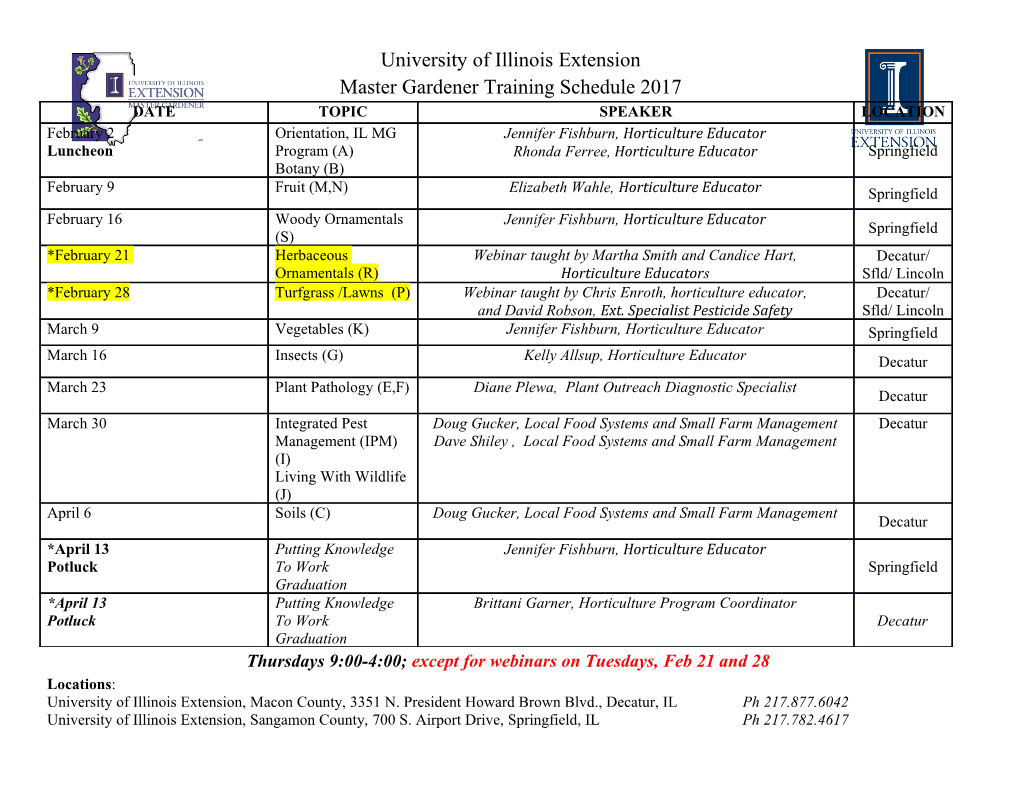
Wind Turbine Drivetrain Development Chris Halse, Engineering Manager, Romax Technology Inc., USA Wind Technical Center CONFIDENTIAL @ Copyright 2012 Romax Technology Inc. CONFIDENTIAL SHARING INNOVATION IN BEARING, GEARBOX & DRIVELINE @ Copyright 2012 Romax Technology Inc. CONFIDENTIAL SHARING INNOVATION IN BEARING, GEARBOX & DRIVELINE @ Copyright 2012 Systems Engineering for Wind Turbine Drivetrains “Britain's offshore windpower costs twice The Challenge as much as coal and gas generated electricity” 16th September 2012 “Offshore wind power cost could fall one­ The Aim third by 2020” 13th June 2012 What the “Collaboration through the supply chain, to deliver more cost­optimised integrated drivetrain design approaches to the turbine designer system (turbine, tower, foundation, can do electrics)” CONFIDENTIAL SHARING INNOVATION IN BEARING, GEARBOX & DRIVELINE @ Copyright 2012 Systems Engineering for Wind Turbine Drivetrains • “Over the wall” component design does not result in Lifecycle costing an optimum drivetrain • Better systems engineering can help achieve a lower cost of energy Supply chain flexibility Reliability focus in concept selection System interactions – aero/ electrical/ dynamic • Demonstrated in the development of our Romax ButterflyTM platform CONFIDENTIAL SHARING INNOVATION IN BEARING, GEARBOX & DRIVELINE @ Copyright 2012 Cost of Energy Analysis – Lifecycle Costing • Rotating machinery lifecycle cost model ­ based on o CAPEX (capital expenditure) of drivetrain components • Generated from our work developing 25 GL­certified gearboxes for a variety of size wind turbine drivetrains • $/kg for gearbox shafts, housing, gearing, bearing ­ estimated based on known purchase cost for various gearbox sizes and types o OPEX (operations & maintenance) for drivetrain components • Based on experience with wind farm operators • Includes realistic failure rates of bearings/gear stages/generator • Increased expense of offshore O&M is included • Variations with size (kNm) are included • Cost model is used early – in concept selection CONFIDENTIAL SHARING INNOVATION IN BEARING, GEARBOX & DRIVELINE @ Copyright 2012 Cost of Energy Model in Concept Design Step 5: Step 4: Step 1: Step 2: Step 3: Detail Cost of Comparison of Select Generate subcomponent energy Direct Drive vs. possible analysis. fundamental calculation of High Speed vs. Qualitative & architecture layouts all feasible Medium Speed quantitative down layouts selection Increased Reliability: Our Approach CONFIDENTIAL SHARING INNOVATION IN BEARING, GEARBOX & DRIVELINE @ Copyright 2012 6.xMW Drivetrain Cost Model Off­shore Results Annual Cost of Energy � High speed systemHigh gearbox vs. Speed generator relative contributionsOffshore Drivetrain to COE Annual Cost of Energy Gearbox Gearbox Generator O&M capex capex 59% 11% 6% Generator O&M 24% Cost Med. Speed gearbox vs.Medium Speed generator(2 stage) relative contributionsOffshore Drivetrain to COE Annual Cost of Energy Gearbox Gearbox O&M capex 33% Direct Drive Medium Speed Medium Speed High Speed 14% (1 stage ) (2 stage) Generator capex 16% Generator O&M 37% CONFIDENTIAL SHARING INNOVATION IN BEARING, GEARBOX & DRIVELINE @ Copyright 2012 Reducing Cost of Energy • To reduce Cost of Energy by 1%, we need o A moderate reduction in drivetrain O&M cost (7%) o A massive reduction in drivetrain CAPEX (25%) Investing in reliable drivetrains has a major impact on COE 6MW Wind Turbine Cost of Energy CONFIDENTIAL SHARING INNOVATION IN BEARING, GEARBOX & DRIVELINE @ Copyright 2012 Concept Design Findings • High speed gear stage issues o Failure data indicates 64% of gearbox failures are due to high speed shaft gear & bearing failure o Pitch line velocities are such that heat generated is significant – issues arise: gear scuffing, controlling bearing preload etc. • Gearbox/Generator alignment Potential for high misalignment o Mounting and bedplate flexibility can cause high misalignment between the gearbox & generator o Generator can be incorrectly positioned or sink over time as the rubber mounts degrade + it also moves due to dynamic loading • Butterfly™ drivetrain o 3 modules aligned using housing connections o No high speed stage CONFIDENTIAL SHARING INNOVATION IN BEARING, GEARBOX & DRIVELINE @ Copyright 2012 Engineering the System for Flexible O&M • Service items are easy to replace with nacelle hoist • Gearbox & generator modules are designed for fast replacement Rotor module can be replaced complete with bearings. Bearing Generator can be quickly pre­load is therefore set in the removed and replaced as factory and not in the tower sealed and tested item Generator driven from down wind end Patented rotor shaft to gearbox face spline connection Gearbox can be quickly Gearbox and generator can be Slip rings, brakes & separated from the rotor removed together or the coupling placed at rear for module for fast replacement generator can remain in the easy replacement without as a sealed and tested item nacelle and only the gear stages are replaced removing generator CONFIDENTIAL SHARING INNOVATION IN BEARING, GEARBOX & DRIVELINE @ Copyright 2012 Engineering the System for Supply Chain Flexibility • Lifecycle costs after prototyping are key Turbine Manufacturer • Flexible supply chain will help keep future costs down Turbine Designer Double row taper Compatibility with roller bearing multiple generator (Moment) bearing technologies rotor assembly, or Drivetrain Systems 2x taper bearing assembly Integrator Gearbox Generator Coupling Brake designer designer supplier supplier Opportunity to source locally Gearbox Generator Flexible supply chain manufacturer manufacturer CONFIDENTIAL SHARING INNOVATION IN BEARING, GEARBOX & DRIVELINE @ Copyright 2012 Drivetrain Interaction with Aerodynamic Loads • Nacelle mainframe, main bearings and main shafts are integral parts of the drivetrain system and react the aerodynamic loading • Even with two large main bearings, some system deflections and forces may be transferred into the gearbox Understanding of the interaction between bearing forces and system deflections is key for mainframe design Structural deflection of the rotor bearing support structure can Butterfly™ ­ Unique Romax designed rotor shaft cause uneven loading of the to gearbox ‘flexi­shaft’ connection to minimise the rotor bearings & premature bending load transferred from the rotor shaft into failure the gearbox (patent pending) CONFIDENTIAL SHARING INNOVATION IN BEARING, GEARBOX & DRIVELINE @ Copyright 2012 Drivetrain Interaction with Control System • Active blade control systems can reduce bending moments on drivetrain, hence reduce stress, and increase life of components • Existing control systems may be “tuned” to reduce bending moments Example baseplate stress w & w/o Active Blade control Base AALC (from work presented by Dale Berg, Sandia Labs, Wind Turbine Structural Path Stress & Fatigue Reductions Resulting from Active Aerodynamics, AWEA Windpower 2011) CONFIDENTIAL SHARING INNOVATION IN BEARING, GEARBOX & DRIVELINE @ Copyright 2012 Drivetrain Interaction with Dynamic System • AGMA, ISO and GL Guidelines require a drivetrain dynamics assessment • Wind turbine aero­elastic loads models (e.g. FAST, GH Bladed) has only a few lumped inertias for the drivetrain • Interactions between the lower frequency modes of the drivetrain and blade modes may be missed • Therefore an additional model is required including more detail of the drivetrain with a simple blade model to check for resonances CONFIDENTIAL SHARING INNOVATION IN BEARING, GEARBOX & DRIVELINE @ Copyright 2012 Drivetrain Response to Grid and Electrical Loads • Effect of electrical phenomena on mechanical components o Shock loading effect on component durability • Standard life calculations assume steady operation • Romax are developing an analytical method for capturing fatigue cycles in components after impact. • Romax are working with NREL/DoE on a new medium speed drivetrain where we will use NREL’s new grid­simulator to investigate this further • Further research is underway on the effect of drivetrain deflection on generator air­gap and combined generator/gearbox noise and vibration transfer CONFIDENTIAL SHARING INNOVATION IN BEARING, GEARBOX & DRIVELINE @ Copyright 2012 Systems Engineering Applied Increased reliability Complete drivetrain ‘tube’ can be lifted into position as one assembly Supply chain flexibility Reduced time to market 3 self contained ‘modules’ for ease of assembly & Flexible O&M strategy Multiple suppliers replacement available for all components & sub systems Simple drivetrain assembly & alignment Design scalable to 10MW Designed for Romax InSight – integrated health management system Fast replacement of all serviceable items Analysis of drivetrain dynamics and system ­ level behaviour Advanced Romax gearbox Innovative lubrication design with patented system technology CONFIDENTIAL SHARING INNOVATION IN BEARING, GEARBOX & DRIVELINE @ Copyright 2012 Wind Turbine Drivetrain Development Please visit our website for further information or use the contact details below: www.romaxtech.com Contact details: Chris Halse – Engineering Manager E­mail: [email protected] CONFIDENTIAL @ Copyright 2012 .
Details
-
File Typepdf
-
Upload Time-
-
Content LanguagesEnglish
-
Upload UserAnonymous/Not logged-in
-
File Pages18 Page
-
File Size-