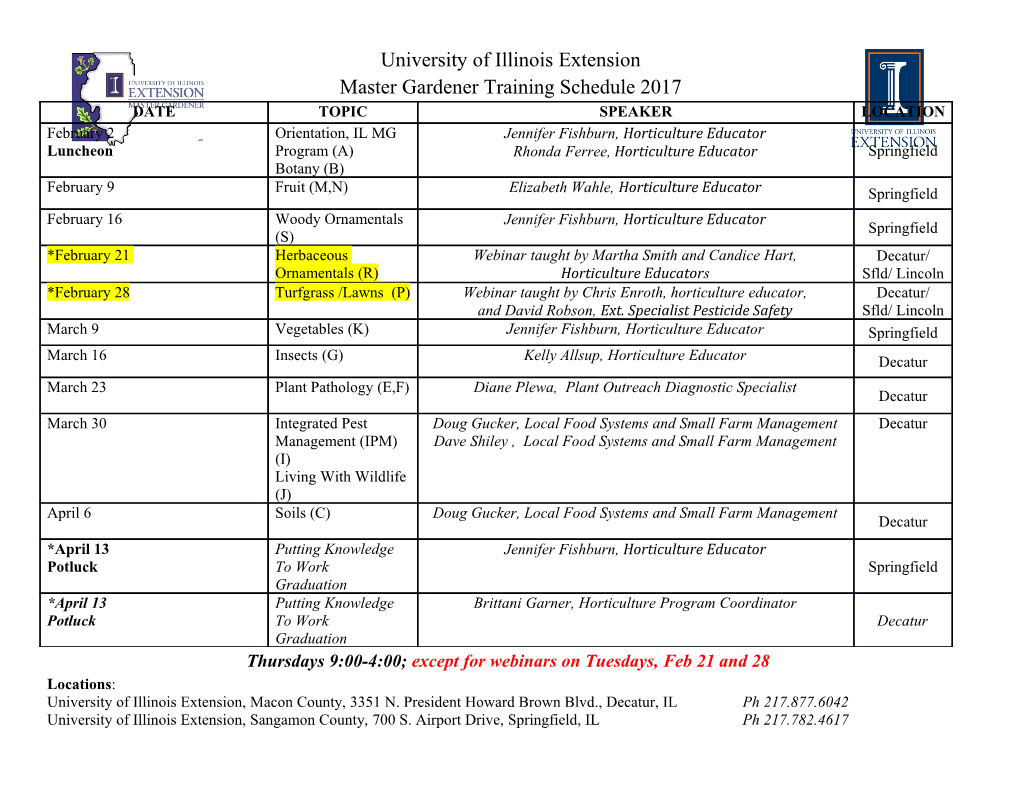
Kinematical characteristic of mechanical frictional variable speed drive D. Herák1, V. Šleger1, R. Chotěborský2, K. Houška3, E. Janča1 1Department of Mechanics and Engineering, Technical Faculty, Czech University of Agriculture in Prague, Prague, Czech Republic 2Department of Material and Engineering Technology, Technical Faculty, Czech University of Agriculture in Prague, Prague, Czech Republic 3HouseMax International, Ltd., Prague, Czech Republic Abstract: The paper describes a new system of mechanical spherical conical friction drive. In the present a row of simple friction, belt, chain, wave and differential variable speed drives is published. For the required range of speed variation they are altogether unfit. The currently used power transmissions are of low efficiency (60–70%). Therefore the better power transmission efficiency is required. The possibility of multicontact power transmission appears as the most suitable principle of the power transmission. Using the designed function model, which was made according to the small tractor producers requirements, the real output kinematical characteristic was measured. It is derived the complete drive conversion unit kinematics and the theoretical kinematical characteristic design. The theoretical design is compared with the real characteristic determined by measuring using the test station. From the measured values we determined that the geometrical characteristic, i.e. the relation between output speed and ring position, corresponds in the ring position range (2.8÷14) mm to the theoretical premise. Keywords: variable speed drive; friction drive; kinematical characteristic; kinematical design The transmission of power from the drive motor almost 10 years due to their law efficiency (65–75%). to the travel wheel of a road or rail vehicle does not Today this efficiency is reached using hydrostatical dispense with a transmission mechanism, which can drives or expensive and complicated multispeed be designed by a simple one-stage mechanical gear gearboxes. Moreover the conversion of mechani- transmission as at the electric drive of a rail vehicle cal energy to other energy type – pressure head or axle up to a complicated gear of a commercial vehicle, electric energy – heightens the capital assets of oth- passenger car or bus, which contains a combination erwise simple machine and generally decreases the of a hydraulic and mechanical drive and a compli- operating reliability of small tractors. The variable cated automatic control (Kopáček 1997). speed drives using pulleys with adjustable sheaves In practice mechanical variable speed drives are assign a low pulleys service life and significantly often used. They are transmission mechanisms with decrease the operating costs. a stepless drive ratio. Speed drives field of application Therefore the low efficiency of currently used is very different reaching from medical instruments power transmissions causes the requirement of the to heavy presses in scrap yards. The stepless drive motor better energy utilization. ratio makes possible the optimization of the ma- chine capacity at a given load. For powers to 50 kW Designed variable speed drive the classical mechanical speed drives are noted for a small control range, which does not correspond to A row of variable speed drives using friction, belts, requirements of producers of small tractors, passen- chains etc. which are unsuitable for the demanded ger cars and other mobile engineering (Zachariáš speed range has been published (Bolek & Koch- 2005). man 1989, 1990; Švec 1999). Therefore the Czech tractor producers clamour for Consumers are interested in small tractors, mobile a mechanical variable speed drives development for pavement cleaners and little snow-plough carriers RES. AGR. ENG., 52, 2006 (2): 61–68 61 Figure 1. Kinematical diagram of the vari- able speed drive ≡ with a petrol engine of 4 to 10 kW power. There- B P34 Analysis of motion 31= 34 + 41 fore producers accept this demand and rather buy ω31 × ρ3 = –ω41 × R4 (2) suitable four-stroke engines from various produc- ≡ ers, e.g. Honda motor, P = 4 kW at revolutions C P54 Analysis of motion 51 = 56 + 61, n = 3750 1/min. resp. 51 = 54 + 41 The use of the friction multi-contact power trans- (v51 = v41) mission appears as the most useful (Zachariáš ω41 × R4 = ω56 × ρ5 + ω61× R4 (3) 2005). ≡ In collaboration with an industrial enterprise the D P52 Analysis of motion 51 = 56 + 61, friction planetary infinitely variable speed drive was resp. 51 = 52 + 21 designed in our department. It fulfils all theoretical (v51 = v52) conditions of the optimal working. ω21 × R2 = –ω56 × R5 + ω61× R4 (4) The frictional spherical planetary speed drive is arranged according to the kinematical diagram in Expression of ρ3, ρ5 radiuses (Figure 1) Figure 1. It is fitted with a system of five cones 3 lo- b cated on fixed axes and with a system of five cones 5, ρ3 = – x × sin ϑ which create the planet wheels. ( 2 ) The input shaft 2 rotates with a constant speed and the output shaft rotates with various speeds, b which depend on the displacement of the ring 4. By ρ5 = – x × sin ϑ the displacement of the ring 4 we get the stepless ( 2 ) variable speeds. The angular velocities are directly proportional to For the contact forces adjustment on the abscissas the revolutions, and in the places A, B, C, D the ring 4 is arranged π × n as the close coupling which is created by the parted ω = sleeve with the pair of outer sleeves planted with 30 screws. where: n (min). The displacement of the ring 4 is realized by means According to the equation (1) the constant revolu- of the motion screw. The input shaft of the motion tions are screw is controlled by means of a speed governor R (Herák 2005). n = 2 × n (5) 31 R 21 3 Kinematical solution of the variable speed drive According to the equation (2) it is true –ρ R b Analysis of the transmission elements n = 3 × n = –n × 2 × – x × sin ϑ (6) 41 R 31 21 R × R 2 The choice of the rolling points and angular veloc- 3 3 4 ( ) ity vectors is shown in Figure 1. The ring 4 revolutions vary with the change of x. The ring rotates reverse to the drive shaft 2. ≡ We multiply the equation (3) by R , the equation A P32 Analysis of motion 31 = 32 + 21 5 (4) by ρ and we add both equations. Then we get ω31 × R3 = ω21 × R2 (1) 5 62 RES. AGR. ENG., 52, 2006 (2): 61–68 n41 × R4 × R5 + n21 × R2 × ρ5 = n61 × (R4 × R5 + R2 × ρ5) R2 x – k After substitution for n41 n56 = n21 × × (11) R5 x + k R × R n × – 2 5× ρ + R × ρ = n × (R R + R × ρ ) Regarding to the fact that the constant length k is 21 R 3 2 5 61 4 5 2 5 ( 3 ) always major than the length × the rotation of the From here the total drive ratio of the variable- cone set 5 is of opposite direction than the presup- speed drive at R3 = R5 posed direction (Figure 1) (the angular velocity ω56 R arrow is of opposite direction). R × ρ – 5 × ρ The choice of the input shaft 2 rotational speed n 2 5 R 3 2 × x × sinϑ 61 = ( 3 )= = depends on the value of the maximum transmitted n R4 R5 21 × b R4 × R5 power. For the standard motors of small tractors the R2× ρ5 + x × sinϑ + × sinϑ + R2 2 R power of P = 4.5 kW is used and the input shaft ( 2 max ) revolutions are as a rule of n = 2920 1/min. 2 × x 21 = (7) Except the values of power and revolutions the b R × R 4 5 choice of basic sizes is required for the design. x + + 2 R2× sinϑ The dimensions of the variable speed drive are Briefly we name the summary of constant values following: in the denominator by the letter k. R2 = R3 = R5 =18 mm R = 50 mm b R × R 4 k = + 4 5 (8) ϑ = 36°, β = 18°, γ = 8° 2 R2× sinϑ The total drive ratio Technical arrangement n 2 × x µ = 61 = (9) The variable speed drive is arranged in form of the 26 n x + k 21 two-planetary gearbox with the infinitely variable For completion the rotational speed of the cone set satellite diameter. The power is supplied by the input 5 with regard to the carrier 6. shaft, which is supported on two angular-contact From the equation (4) it follows ball bearings. The shaft turns the inner cones, which n n R R R n cause the rotation of the outer cones (Figure 2). 56 = 61 × 2 – = 2 × 61 – 1 (10) The outer cones near the input shaft are mounted n n R R R n 21 21 5 5 3 ( 21 ) using the angular-contact ball bearings. The bear- After the substitution for ings are pressed on the pins which are pressed on n the flange. The flange is bolted on the drive hous- 61 ing. The outer cones near to the output shaft are n 21 mounted using bearings and pins, too. The pins are from the equation (5) and after a simple adjustment pressed on the output shaft, which is their carrier. we get The outer cones near to the output shaft rotate not only around their rotary axes (anyhow the cones near to the input shaft) but around the output shaft axis, too. The rotation of the outer cones near to the motion shaft input causes the ring rotation. This ring causes the rotation of outer cones near to the output shaft. In this way we reach the before mentioned combined motion of the cones. The change in the satellite input shaft output shaft diameter is caused by the ring traverse (see the previous chapter).
Details
-
File Typepdf
-
Upload Time-
-
Content LanguagesEnglish
-
Upload UserAnonymous/Not logged-in
-
File Pages8 Page
-
File Size-