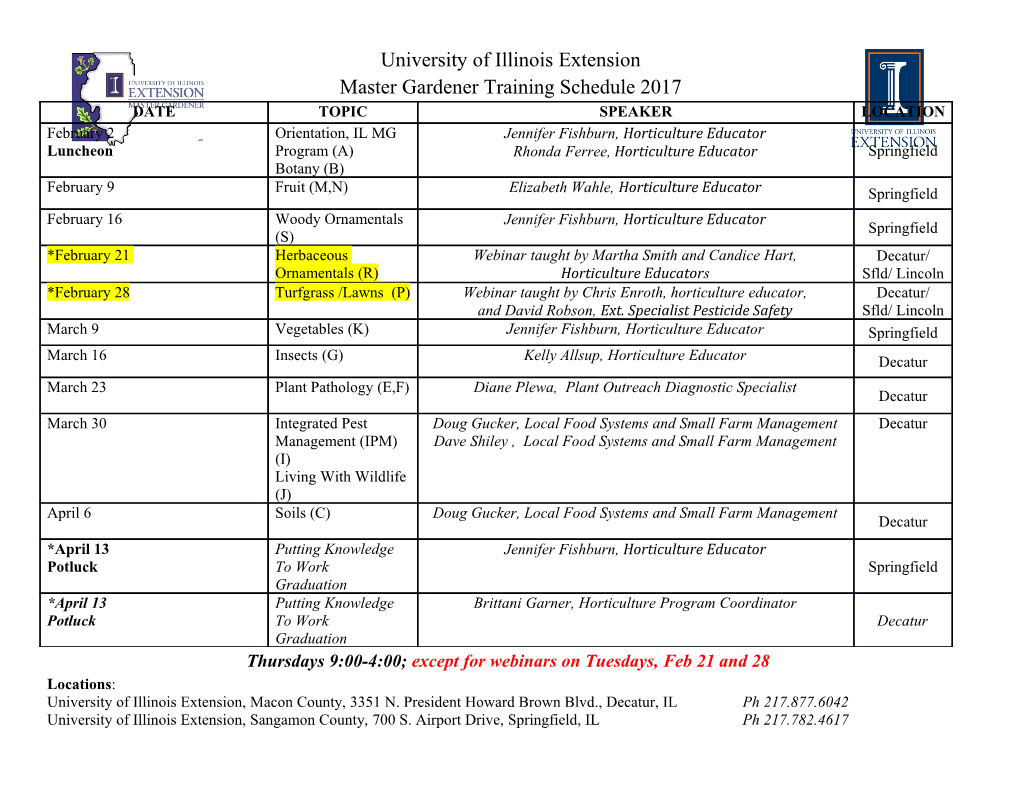
Transactions on Engineering Sciences vol 13, © 1996 WIT Press, www.witpress.com, ISSN 1743-3533 The significance of the fatigue threshold for metallic materials A. Hadrboletz, B. Weiss, R. Stickler Introduction and Basic Considerations The fatigue threshold may be defined as the critical limit below which cracks cease to propagate under cyclic loading. As the fatigue threshold represents an important parameter in design and failure analysis much research effort has been devoted during the last decades to reveal underlying principles. The first case of a fatigue threshold referred to in the literature is the fatigue limit or endurance limit deduced from conventional S-N curves. This fatigue limit is currently still used as an essential parameter in design activities based on the so-called "total life approach". The high-cycle fatigue limit of polycrystalline metals and alloys has been defined as the threshold stress for propagation of small cracks which may have nucleated but did not grow further during subsequent cyclic loading at this particular stress amplitude. In many cases of engineering practice the design against fatigue failure is based on the concept of admissible defects ("defect tolerant approach"). This concept makes use of the threshold stress for the growth of long fatigue cracks as the essential parameter. Thus the question arises which criteria govern the threshold condition for the growth of such fatigue cracks. Several criteria have been proposed to describe the onset of the fatigue damage process which eventually results in catastrophic fatigue failure. These criteria Transactions on Engineering Sciences vol 13, © 1996 WIT Press, www.witpress.com, ISSN 1743-3533 206 Localized Damage include stress or strain concepts, stress intensity concepts based on linear elastic fracture mechanics, J-integral approach based on elastic-plastic fracture mechanics and crack growth effects related to crack opening displacement. The most widely applied concept to describe the long-crack fatigue threshold is based on linear elastic fracture mechanics (LEFM). Under the assumption of a homogenous isotropic elastic material a stress intensity factor, K, was defined which describes the elastic stress singularity associated with the crack tip in a stress field. This stress intensity factor is given by equation 1: K = a \7ia • F with a = external applied stress (1) a = crack length refined by a geometric correction factor F appropriate for various specimen geometries and different loading modes. The K-concept initially developed for unstable crack propagation under tensile loading was applied for the case of cyclic deformation by Paris [1], AK = Aa • Vrca • F (2) with AK = Kmax " ^min and the cyclic stress amplitude range ACJ = With respect to the fatigue threshold considerations under low-amplitude loading (i.e. high-cycle fatigue conditions) a critical AK value is defined below which practically no crack growth should occur. This value was termed threshold stress intensity range, AK^. The near threshold crack propagation rate is very sensitive to minor changes in AK resulting in large variations of da/dN. Crack growth in this region plays a predominant role since in reality a fatigue crack may spend an overwhelming portion of its live in this regime of low da/dN. The threshold stress intensity range, AK^, was initially assumed to be a material parameter. However, numerous experimental results showed that this AKfli is dependent on several intrinsic and extrinsic parameters. It could be shown that the number of affecting parameters can be reduced by taking into account various mechanisms thought to be responsible for the prevention of a fatigue crack to close under reduced loads (2). Introducing the concept of crack closure (3) the threshold stress intensity was replaced by an effective (or intrinsic) fatigue threshold stress intensity, equation 3: Transactions on Engineering Sciences vol 13, © 1996 WIT Press, www.witpress.com, ISSN 1743-3533 Localized Damage 207 AKth,eff = Kthmax - KC! ^h,max - niax.stress intensity (3) K£\ = closure stress intensity which is considered to be a true material constant. Extended measurements revealed that the AK-concept can be applied successfully to long fatigue cracks (longer than several millimeters). Parameters affecting the fatigue threshold Several extrinsic and intrinsic parameters may affect the AK^h values. The effects of some of these parameters were interpreted to be related to crack closure as the most common criteria, Table 1. Essential features of crack closure Based on LEFM considerations it is assumed that a fatigue crack is completely open during the tensile portion of the loading cycle. Under these conditions the crack tip experiences the full stress intensity range computed from the externally applied stress range. In reality a different behavior was observed (3) as shown in the dependence of the crack opening displacement (COD) on external load, G, Fig.l. For G < Gel (closure stress) only a minor COD is observed. For a > Gel the crack exhibits an opening behavior as expected from elastic considerations. This means that only above Gel the crack tip experiences the full applied load. This crack closing (synonymously also called crack opening) behavior was explained in part as a result of plasticity effects in the wake of the crack tip. During the growth of the fatigue crack the material at the crack tip is plastically strained. Due to the restraint of the surrounding elastic material on this residual stretch, a retardation of crack growth due to closing of the crack faces is observed. Since a fatigue crack cannot propagate while it remains closed, the actual AK value experienced at the crack tip is reduced by this closure value to an effective value, AKeff. That a fatigue crack may be closed over a part of its loading range was pointed out earlier (4), Fig.2. Various closure mechanisms are listed in the literature (2, 5), the most important being: plasticity induced, fracture surface roughness induced, geometrical (crack deflection and bifurcation), oxide induced and viscous liquid induced. These mechanisms have been more or less successfully invoked to explain the dependence of AKth on different parameters, Table 1. For details see Ref.(2). Transactions on Engineering Sciences vol 13, © 1996 WIT Press, www.witpress.com, ISSN 1743-3533 20 I • 9 8 Localize Extrinsic u Max. values of AKth at R=0 roughness induced closure: decreasing AKth-values with increasing positive and rough fracture surface at R = 0 d increasing negative R-values smooth fracture surface at higher R-vaiues Damag significant influence for coarse grained material; AKth almostno R-dependenc if Kmin>Kcl independent of R for fine grained material I tensile overload reduction of near threshold fatigue crack growth plasticity induced closure (crack has to transmit an 1 enlarged plastic zone) | 1 compressive acceleration of near AKth fatigue crack growth reduced crack closure due to flattening of the 1 e 1 overload fracture surface asperities | • C C g O higher AKth in bending compared to tension-compression influence eliminated by closure (inhomogeneous plastic deformation) | test-frequency minor increase of AKth with increasing frequency formation of oxides on the crack surfaces test-temperature AKth increases with rising temperatures increased closure due to the fonnation of corrosion products (mainly oxides), predominantly roughness- and oxide induced closure environment AKth is to be almost independent of R in an inert lack of oxide induced closure, absence of environment compared to air roughness induced closure which is enhanced by fretting corrosion (loose particles), increased AKth in oil compared to inert, gaseous viscous induced closure environment grain size AKth increases with increasing grain size coarser structures exhibit rougher fracture surfaces leading to pronounced roughness induced closure J " 3 c 3 Z . higher AKth-valucs compared to single-phase materials roughness induced closure and a meandering crack path (geometrical closure). 1 metal-matrix AKth varies both with volume fraction and the average size AKth.eff depends only on the mean particle size; | composites of the reinforcing hard particles there is no function of its volume fraction texture AKth depends on the angle between crack plane and fracture surface roughness varies with the crack- crystallographic orientation orientation (roughness-induced closure), large changes in crack path orientation cause geometrical induced closure short cracks Microstructurally and physically short cracks have smaller gradual build up of closure during transition from AKth values and larger near-threshold propagation rates than short cracks to long cracks long cracks Transactions on Engineering Sciences vol 13, © 1996 WIT Press, www.witpress.com, ISSN 1743-3533 Localized Damage 209 a, K COD TIME Figure 1. Stress (or K) -crack opening Figure 2. Definition of fatigue (COD) curve; schematic threshold parameters (4) Critical evaluation of crack closure In general, the AKth,eff value called also the "intrinsic threshold value" should more correctly describe the crack growth behavior under cyclic loading. An accurate determination of the amount of crack closure is therefore essential to calculate AKth,eff according to equation (3). Various procedures have been proposed to determine the closure contribution (2). Idealized crack opening curves have the form as shown schematically in Fig. 3a. This ideal curve consists of two straight-lines. The branch between K^^x and K^ reflects the closing of the crack with diminishing external load. At KCI the ideal crack is completely closed and further unloading corresponds to the elastic behavior of a crack-free specimen. The compliance of a specimen with an open crack is larger than that of a specimen containing a closed crack, the slope of the branch below K^ is steeper. In this idealized case, for Kmin < %d ^e AK^eff corresponds to the difference between K^ax and K^, while AKtfi is usually defined as K^^ - ^min- In a real material the change in closure behavior is not as abrupt as drawn in Fig.3a but rather gradual as shown schematically in Fig.3b.
Details
-
File Typepdf
-
Upload Time-
-
Content LanguagesEnglish
-
Upload UserAnonymous/Not logged-in
-
File Pages9 Page
-
File Size-