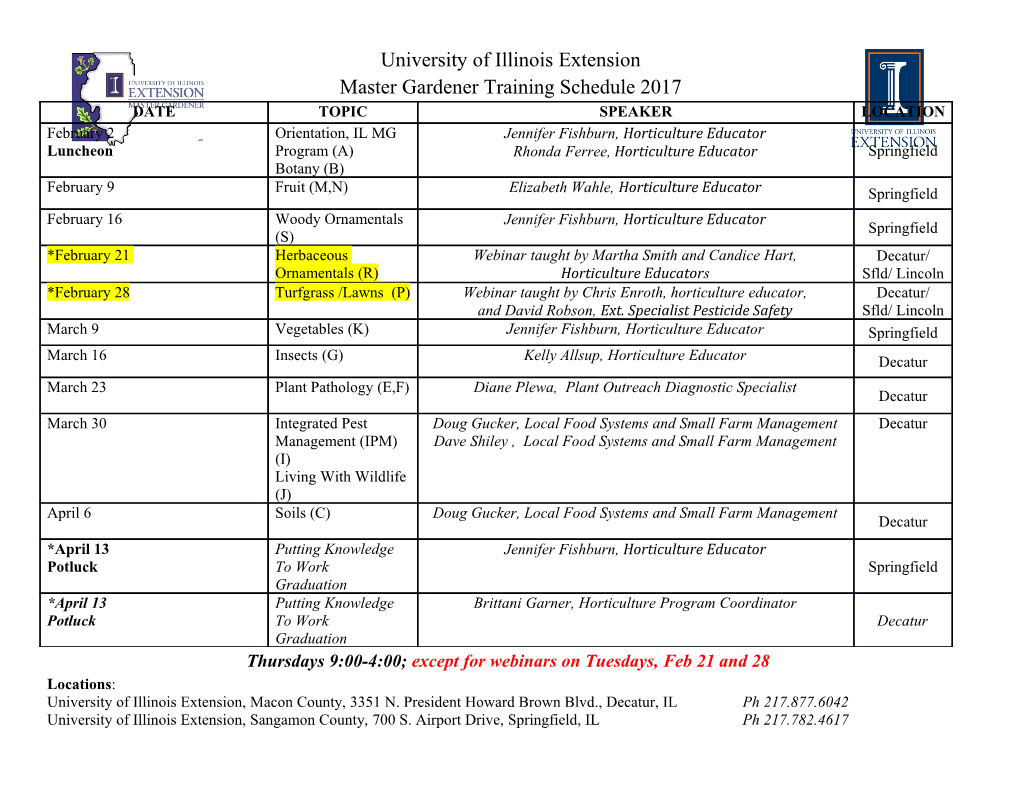
catalysts Article The Catalytic Oxidation of Formaldehyde by FeOx-MnO2-CeO2 Catalyst: Effect of Iron Modification Yaxin Dong , Chenguang Su, Kai Liu, Haomeng Wang, Zheng Zheng, Wei Zhao and Suhong Lu * College of Chemistry and Chemical Engineering, Xi’an Shiyou University, Xi’an 710065, China; [email protected] (Y.D.); [email protected] (C.S.); [email protected] (K.L.); [email protected] (H.W.); [email protected] (Z.Z.); [email protected] (W.Z.) * Correspondence: [email protected]; Tel.: +86-156-1922-8512 Abstract: A series of FeOx-MnO2-CeO2 catalysts were synthesized by the surfactant-templated coprecipitation method and applied for HCHO removal. The influence of Fe/Mn/Ce molar ratio on the catalytic performance was investigated, and the FeOx-MnO2-CeO2 catalyst exhibited excellent catalytic activity, with complete HCHO conversion at low temperatures (40 ◦C) when the molar ratio of Fe/Mn/Ce was 2/5/5. The catalysts were characterized by N2 adsorption and desorption, XRD, H2-TPR, O2-TPD and XPS techniques to illustrate their structure–activity relationships. The result revealed that the introduction of FeOx into MnO2-CeO2 formed a strong interaction between FeOx- MnO2-CeO2, which facilitated the improved dispersion of MnO2-CeO2, subsequently increasing the surface area and aiding pore development. This promotion effect of Fe enhanced the reducibility and produced abundant surface-active oxygen. In addition, a great number of Oα is beneficial to the 3+ intermediate decomposition, whereas the existence of Ce favors the formation of oxygen vacancies on the surface of the catalyst, all of which contributed to HCHO oxidation at low temperatures. Citation: Dong, Y.; Su, C.; Liu, K.; Wang, H.; Zheng, Z.; Zhao, W.; Lu, S. Keywords: formaldehyde; FeOx-MnO2-CeO2; catalytic oxidation; catalytic activity The Catalytic Oxidation of Formaldehyde by FeOx-MnO2-CeO2 Catalyst: Effect of Iron Modification. Catalysts 2021, 11, 555. https:// 1. Introduction doi.org/10.3390/catal11050555 As a common indoor air pollutant, formaldehyde (HCHO), mainly from building and decoration materials, causes strong irritation, teratogenicity and carcinogenicity, and Academic Editor: Angeliki it is therefore harmful to human health. In 2004, the World Health Organization identi- A. Lemonidou fied formaldehyde as a group I carcinogen for humans [1]. Hence, from the perspective of protecting human health and the air environment, it is vital to reduce and eliminate Received: 3 April 2021 formaldehyde. Many technologies have been proposed for indoor HCHO removal, such Accepted: 25 April 2021 Published: 27 April 2021 as adsorption [2], photocatalytic oxidation [3], plasma degradation [4] and catalytic ox- idation [5]. Among these, catalytic oxidation of HCHO has been proven to be the most Publisher’s Note: MDPI stays neutral economical and effective technology, because the process involves the complete conversion with regard to jurisdictional claims in of HCHO into CO2 and H2O without by-products at low or even room temperature [6]. published maps and institutional affil- The key factor of this method lies in the selection and preparation of effective catalysts to iations. eliminate HCHO. Two types of catalysts for the catalytic oxidation of HCHO have been applied in the re- action process, namely supported noble metals and transition metal oxides [7]. Comparing both types of catalysts, supported noble metal catalysts exhibit superior catalytic properties for HCHO elimination at low or even room temperature. However, due to the scarce Copyright: © 2021 by the authors. Licensee MDPI, Basel, Switzerland. resources and high costs of noble metals, many researchers are shifting their attention to This article is an open access article the development of inexpensive and effective transition metal oxide catalysts. It has been distributed under the terms and reported that [MnOx][8], [Co3O4][9], [CeO2][10] and [CuO] [11], being characteristic rich conditions of the Creative Commons oxygen species and exhibiting rapid electron transfer, are promising alternative catalysts for Attribution (CC BY) license (https:// the catalytic oxidation of HCHO. For example, a MnOx-CeO2 catalyst was prepared by the ◦ creativecommons.org/licenses/by/ redox reaction method and it achieved 100% HCHO conversion at 100 C[12]. Additionally, 4.0/). Co3O4-CeO2 was synthesized by a citric acid sol-gel method, and it fully oxidized HCHO Catalysts 2021, 11, 555. https://doi.org/10.3390/catal11050555 https://www.mdpi.com/journal/catalysts Catalysts 2021, 11, 555 2 of 14 at a temperature as low as 80 ◦C[13]. According to the literature [14], the use of metal oxides with promoters for the synthesis of trimetal oxide catalysts can increase the amount of surface-active oxygen species and, thus, significantly enhance the catalytic oxidation processes. Jiang et al. [15] reported that Mn-Cu-Ce mixed oxide networks had higher catalytic activity than Mn-Cu and pure Mn due to the inclusion of Cu, which improved the oxygen activation and transport ability. Lu et al. [16] discovered that the addition of MnOx to Co3O4-CeO2 resulted in high dispersion and easy reducibility of a MnOx-Co3O4-CeO2 catalyst at lower temperatures. However, only a few reports exist on ternary mixed oxide catalysts for the elimination of formaldehyde, and these have failed to address some vital research questions. In an attempt to expand the general knowledge of the application of ternary mixed oxide catalysts for the removal of formaldehyde, it is necessary to develop multi-component metal oxide catalysts for the low-temperature catalytic oxidation of formaldehyde. Therefore, we report the development of Fe-Mn-Ce ternary mixed oxide catalysts for the purification of formaldehyde by the surfactant-templated coprecipitation method. The influence of the Fe/Mn/Ce molar ratio on the structure-activity relationship of the FeOx-MnO2-CeO2 catalysts was investigated. 2. Results and Discussion 2.1. Characterization of the Catalysts 2.1.1. N2 Adsorption and Desorption The N2 adsorption/desorption isotherms and pore size distributions of the Fe-Mn- Ce ternary mixed oxides are presented in Figure1A, B and C, while the specific surface area (SBET), pore diameter and pore volume are summarized in Table1. All the catalysts exhibited the type IV isotherm with H3 hysteresis loops in the relative pressure (P/P0) range of 0.6–1.0; the pore structure of the sample caused agglomeration in the capillary, indicating the existence of mesoporous structures [17,18]. It was noted that the FeOx- MnO2-CeO2-2:5:5(FMC-2:5:5) catalyst significantly increased the amount of adsorbed N2, which indicates that the catalyst had large specific surface area and pore volume. This observation is supported by the data in Table1. The specific surface area and pore volume 2 −1 3 −1 of FMC-2:5:5 catalyst were 99 m g and 0.4 cm g , respectively. The pure CeO2, 2 −1 Fe3O4 and MnO2 presented similar results for surface area (22 m g ) and pore volume of 3 −1 2 −1 (0.1 cm g ), while the SBET values and pore volume of MnO2-CeO2 increased to 73 m g and 0.2 cm3 g−1, respectively. This is consistent with the investigation by Zhu et al. [12], which reported that the interaction between MnO2 and CeO2 could restrain the structure growth of mixed oxide and thus increase the specific surface area. The addition of an Fe promoter further increased the specific surface area and pore volume of the FMC catalyst; while the Fe content increased to 3 mol (FMC-3:5:5), the SBET value of the sample decreased. This indicates that while the introduction of Fe enhanced the dispersion of the FMC catalyst, excessive Fe may lead to the agglomeration of particles and decrease the specific surface area. Meanwhile, the average pore diameter also increased in comparison with that of MnO2-CeO2, which may be due to the formation of developed pores promoted by Fe incorporation into MnO2-CeO2. This is confirmed by the pore size distribution curve shown in Figure1C. However, when the Fe content increased to 3 mol (FMC-3:5:5), the SBET value decreased, indicating that excessive Fe may cause particle agglomeration and decrease the specific surface area. Generally, higher values of SBET and pore volume are beneficial to the adsorption of HCHO and could provide more reactive sites, thus improving the catalytic performance [19]. Catalysts 2021, 11, 555 3 of 14 Catalysts 2021, 11, x FOR PEER REVIEW 3 of 14 Figure 1. 1. (A(A) N)N2 adsorption2 adsorption isotherms, isotherms, (B) N (2B adsorption)N2 adsorption isotherms isotherms of CeO2 ofand CeO (C)2 poreand size (C) dis- pore size tributiondistribution of (a of) CeO (a)2 CeO, (b) 2Fe,(3bO)4, Fe(c)3 OMnO4,(c2,) ( MnOd) MnO2,(2-CeOd) MnO2, (e2)-CeO FMC-1:5:5,2,(e) FMC-1:5:5,(f) FMC-2:5:5 (f )and FMC-2:5:5 (g) and FMC-3:5:5.(g) FMC-3:5:5. Table 1. Specific surface area, average pore diameter and pore volume of the catalysts. Table 1. Specific surface area, average pore diameter and pore volume of the catalysts. SBET Pore Volume Catalyst S Average Pore DiameterAverage (nm) Pore Pore Volume Catalyst (m2·g−1) BET (cm3 g−1) (m2·g−1) Diameter (nm) (cm3 g−1) CeO2 20 9.5 0.1 CeO 20 9.5 0.1 Fe3O4 2 22 25.9 0.2 Fe3O4 22 25.9 0.2 MnO2 22 29.1 0.2 MnO2 22 29.1 0.2 MnO2-CeO2 73 10.6 0.2 MnO2-CeO2 73 10.6 0.2 FMC-1:5:5FMC-1:5:5 87 8716.6 16.60.3 0.3 FMC-2:5:5 99 12.2 0.4 FMC-3:5:5 82 11.6 0.3 Catalysts 2021, 11, x FOR PEER REVIEW 4 of 14 Catalysts 2021, 11, x FOR PEER REVIEW 4 of 14 FMC-2:5:5 99 12.2 0.4 FMC-3:5:5 82 11.6 0.3 Catalysts 2021, 11, 555 FMC-2:5:5 99 12.2 0.4 4 of 14 2.1.2.FMC-3:5:5 XRD Patterns 82 11.6 0.3 The crystal phase of FMC ternary mixed oxide catalysts was characterized by the X- 2.1.2.
Details
-
File Typepdf
-
Upload Time-
-
Content LanguagesEnglish
-
Upload UserAnonymous/Not logged-in
-
File Pages14 Page
-
File Size-