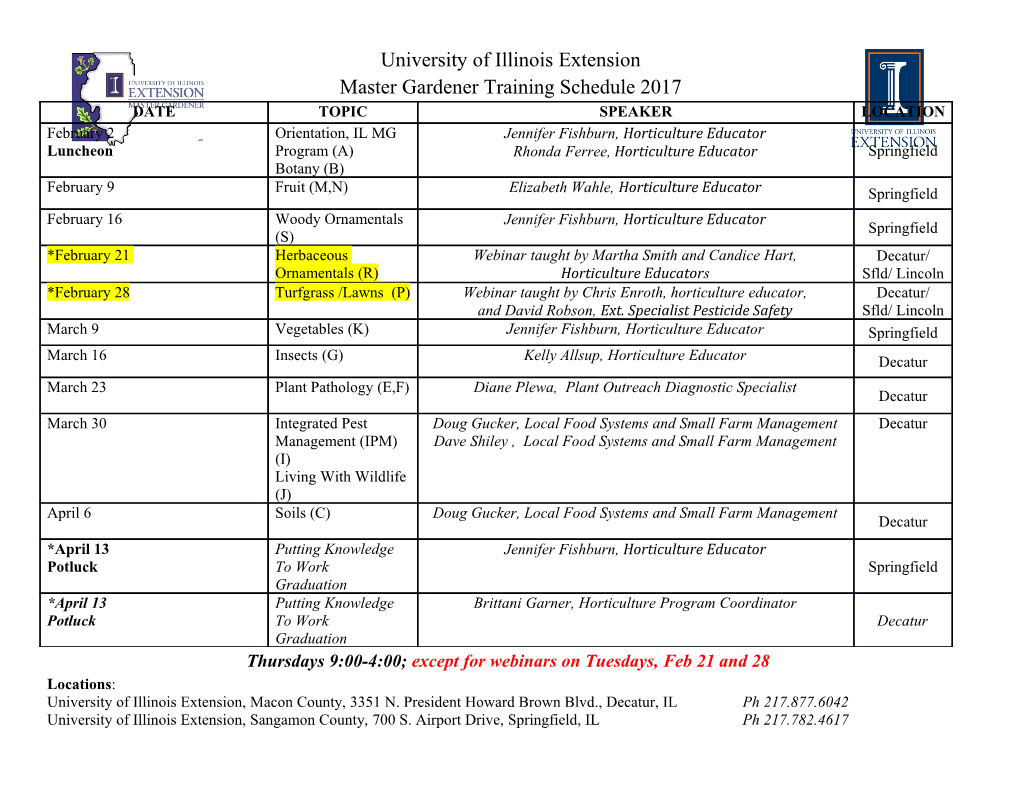
Electromagnetic Flyer Plate Technology and Development of a Novel Current Distribution Sensor A doctoral thesis by Kaashif A. M. Omar (MPhys. Physics with Astrophysics, University of Leicester, 2007) Submitted in partial fulfilment of the requirements for the award of the degree of Doctor of Philosophy of Loughborough University November 2014 To the School of Electronic, Electrical and Systems Engineering, Loughborough University, Loughborough, UK © British Crown Owned Copyright 2014/AWE Acknowledgements With the grace and blessing of Allah (SWT), I have been able to complete this work, and I hope to continue in the pursuit of knowledge as is commanded by him… Completing this research project and writing up this thesis has been full of ups and downs and it has been a very long journey, I can vaguely recall a young(er) single scientist who began this work not knowing where it would lead to; now, I am happily married to my wife Humna, having just celebrated our first wedding anniversary, and about to start the next big chapter in my life, which is to become a father… On that note I would like to take this opportunity to firstly thank my father, Mr Abdul Majid Omar and my mother, Mrs Shenaz A M Omar; who have always encouraged me to push myself and instilled within me the confidence that I can achieve anything I put my mind to. Without their constant support I would never have even been able to complete my first degree In physics with Astrophysics at Leicester University, let alone have the opportunity to complete a PhD. It is purely a testament of their dedication to their children that I am now able to stand here at the pinnacle of educational achievement, and I hope that I have made them proud. The past five years have provided me with some of the most memorable times of my life and have allowed me to develop a great relationship with members of staff at the School of Electronic, Electrical and Systems Engineering at Loughborough University. In particular I would like to acknowledge my academic PhD supervisors, Prof. Bucur Novac and Prof. Ivor Smith, who supported me and tirelessly reviewed and re-reviewed various versions of my thesis without ever complaining. They allowed me the freedom to discover my own path and to pursue areas of research which interested me, which is something I am truly grateful for. A special thanks also goes to Dr Peter Neal Graneau at AWE who acted as my industrial supervisor and is someone with whom I have worked very closely over the past 7 years; together we have developed a new research facility at AWE and his experience in the field proved to be invaluable in providing me with the confidence to pursue novel areas of research. In addition, I would like to put on record my heartfelt gratitude to my employer, AWE as without their financial support, I would never have been able to take on this incredible journey. A big thank you goes out to my colleagues both in the UK and the wider pulsed power community who encouraged me to continue my research by showing genuine interest in my work at international conferences. I would also like to make a mention of my close family and friends who were willing to provide unbiased critiques on my work (whether I wanted to hear them or not!), which ultimately allowed me to bring my work up to a standard where I was presented with student awards at a number of international conferences. Thank you all Acknowledgements Table of contents Abstract I Thesis Summary III Chapter 1 Background information and review of various electromagnetic accelerator techniques 1 1.1 – Railgun 3 1.1.1 Limitations of the rail gun 5 1.1.2 Rail gun theory 6 1.1.3 Applicability to foil-slap experiments 7 1.2 – Coil Gun 8 1.2.1 Reluctance gun overview 8 1.2.2 Induction gun overview 10 1.2.3 Applicability of coil guns (reluctance 12 and induction) to foil-slap experiments 1.3 – Induction plate launcher 12 1.3.1 Applicability of Induction plate launcher to foil-slap experiments 12 1.4 – Strip line Accelerator 13 1.4.1 Strip line Accelerator overview 14 1.4.2 Applicability to foil-slap 14 1.5 – Exploding Foil Accelerators 15 1.5.1 Exploding Foil Accelerator Overview 15 1.5.2 Applicability to Foil-slap 16 i 1.6 – Comparison of proposed technologies 17 1.7 – Proposed way ahead 19 Chapter 2 Development of two independent electromagnetic stripline accelerator facilities 21 2.1 – Development of the AMPERE facility 22 2.1.1 AMPERE Electrical Circuit 22 2.1.2 AMPERE CAD drawing 23 2.1.3 AMPERE capacitor Safety 25 2.1.4 AMPERE switching 26 2.1.5 AMPERE safety systems 29 2.1.6 AMPERE SALUS system 29 AMPERE SALUS layout 30 2.1.7 AMPERE electrical performance and current pulse damping 30 2.1.8 Commissioning the AMPERE facility 34 2.2 – QUATTRO bank overview 35 2.2.1 QUATTRO refurbishment 36 2.2.2 QUATTRO current pulse damping 39 2.2.3 QUATTRO Safety systems 43 2.2.4 QUATTRO commissioning 43 Chapter 3 Accelerator system component characterisation 45 3.1 – AMPERE characterisation experiments 46 ii 3.1.1 – Calculation from directly measurable parameters 48 3.2 – Differential solver used to predict current trace 50 3.2.1 MathCAD equation input 52 3.2.2 Parameter results from differential solver 53 3.2.3 Comparison of the two approaches 54 Chapter 4 High current pulse shaping 56 4.1 – AMPERE Current Shaping 57 4.1.1 EFDR Quenching Medium 58 4.1.2 Fuse action integral 59 4.1.3 Aluminium temperature – resistivity data 61 4.1.4 Development of fuse containment 63 4.2 – EFDR Model development 67 4.2.1 Changes to the MathCAD model 69 4.2.2 Exploding wire resistivity (Aluminium) 70 4.2.3 Changes to the Differential solver 71 4.2.4 Initial results from differential solver 73 4.3 – Current Flow modelling 76 4.3.1 Model Development 77 4.3.2 Modified solver to account for dual current paths 80 4.3.3 Results of modified solver 81 4.3.4 Voltage across bridge 83 4.4 – QUATTRO Modelling 86 4.4.1 Non-Destructive damping 87 4.4.2 Damping using stainless steel 88 4.4.3 Installation of damper on Quattro bank 90 iii 4.4.4 Stainless steel resistivity model 92 4.4.5 Stainless steel section 99 Chapter 5 Flyer-plate experiments and modelling flyer motion 102 5.1 – Modelling assumptions 103 5.2 – Accelerating forces 104 5.2.1 Electromagnetic accelerating force 104 5.2.2 Aerodynamic drag 106 5.2.3 Gravity 106 5.2.4 Adiabatic compression of air 107 5.2.5 Net force calculation 109 5.3 – Changes made to the computer model 109 5.3.1 Updated Differential solver 110 5.4 – Flyer motion 113 5.4.1 Experimental results 116 5.4.2 Capacitor bank voltage prior to discharge 119 5.4.3 Effect of capacitor bank bleeding 121 5.4.4 Model correction and results 122 5.4.5 Magnitude of forces during discharge 124 5.4.6 Flyer displacement 126 Chapter 6 Pre-existing diagnostic techniques 128 6.1 – Standard diagnostics 128 iv Chapter 7 Initial development and calibration of novel sensor 130 7.1 – Background 130 7.2 – Filamentary model overview 131 7.3 – Modelled effects of current distribution 133 7.3.1 Flyer 2-D dynamics 134 7.3.2 2-D model predictions 134 7.4 – MIDOT sensor arrangement 138 7.5 – Initial experiments 140 7.6 – Experimental data 149 7.7 – Filamentary stripline geometry 153 7.8 – Development of initial MIDOT array 160 7.9 – Initial high voltage test 165 Chapter 8 Development of second generation MIDOT array 169 8.1 – New array assembly 170 8.2 – Confirming performance of each loop individually 172 8.3 – Confirmation of previous results 175 v 8.4 – Initial experimental results 178 8.5 – Full array performance and consistency tests 181 8.6 – Effect of adjacent source loops 185 8.7 – Dual source stripline analogue tests 188 8.8 – Determining resolution limit of array 192 8.9 – Non-equal source current experiments 200 8.10 – Interpreting results assuming a continuous stripline 207 Chapter 9 Conclusions 210 9.1 – Inductive sensor 210 9.1.1 Inductive sensor performance and operation 210 1) Model validation mode 211 2) Direct measurement 211 9.1.2 High voltage tests 211 9.2 – Computer model 212 9.3 – Empirical model for the EFDR 212 9.4 –Future work 213 9.4.1 Sensor optimisation 213 1) Design of sensor array 213 2) Optimised geometry 214 9.4.2 Further use of the sensor 214 vi 9.4.3 Alternative techniques to determine localised current flow 214 9.4.4 The way forward 215 9.4.5 Further uses of EFDR 215 References 216 List of associated publications 223 Appendix Appendix A – AMPERE safety systems Appendix B – AMPERE facility commissioning Appendix C – QUATTRO Safety systems Appendix D – Derivation resistance and inductance expressions Appendix E – Determining circuit parameters from measured data Appendix F – MathCAD differential solver Appendix G – Electromagnetic accelerating force derivation Appendix H – Review of existing experimental diagnostics vii Abstract The main driver in conducting this research was to simulate the mechanical shockwave imparted to a target material by the deposition of cold x-rays. Simulating the mechanical effects of cold x-rays is of paramount importance when qualifying new and existing heat shield materials for survival in hostile environments.
Details
-
File Typepdf
-
Upload Time-
-
Content LanguagesEnglish
-
Upload UserAnonymous/Not logged-in
-
File Pages307 Page
-
File Size-