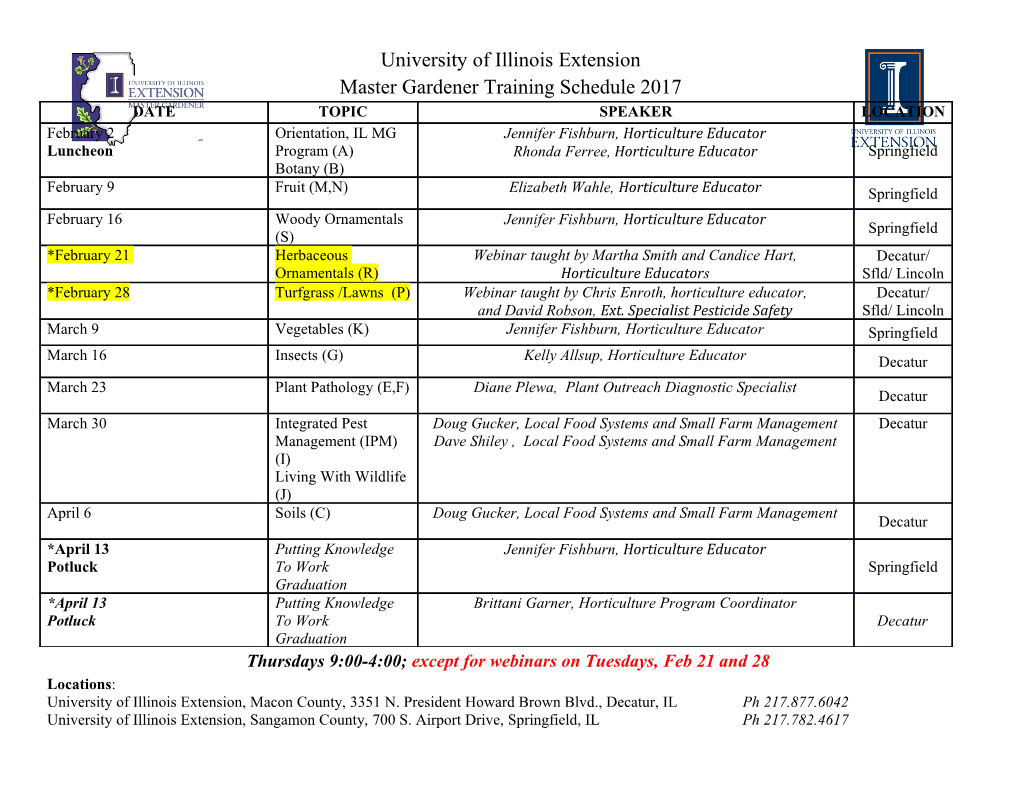
EXPERIMENTAL AND NUMERICAL ANALYSIS OF THERMAL FORMING PROCESSES FOR PRECISION OPTICS DISSERTATION Presented in Partial Fulfillment of the Requirements for the Degree Doctor of Philosophy in the Graduate School of The Ohio State University By Lijuan Su Graduate Program in Industrial and Systems Engineering The Ohio State University 2010 Dissertation Committee: Dr. Allen Y. Yi, Adviser Dr. Jose M. Castro Dr. Betty L. Anderson Copyright by Lijuan Su 2010 ABSTRACT Glass has been fabricated into different optical elements including aspherical lenses and freeform mirrors. However, aspherical lenses are very difficult to manufacture using traditional methods since they were specially developed for spherical lenses. On the other hand, large size mirrors are also difficult to make especially for high precision applications or if designed with complicated shapes. Recently developed two closely related thermal forming processes, i.e. compression molding and thermal slumping, have emerged as two promising methods for manufacturing aspherical lenses and freeform mirrors efficiently. Compression molding has already been used in industry to fabricate consumer products such as the lenses for digital cameras, while thermal slumping has been aggressively tested to create x-ray mirrors for space-based telescopes as well as solar panels. Although both process showed great potentials, there are a quite few technical challenges that prevent them from being readily implemented in industry for high volume production. This dissertation research seeks a fundamental understanding of the thermal forming processes for both precision glass lenses and freeform mirrors by using a combined experimental, analytical and numerical modeling approach. First, a finite element method ii (FEM) based methodology was presented to predict the refractive index change of glass material occurred during cooling. The FEM prediction was then validated using experimental results. Second, experiments were also conducted on glass samples with different cooling rates to study the refractive index variation caused by non-uniform cooling. A Shack-Hartmann Sensor (SHS) test setup was built to measure the index variations of thermally treated glass samples. Again, an FEM simulation model was developed to predict the refractive index variation. The prediction was compared with the experimental result, and the effects of different parameters were evaluated. In the last phase of this dissertation research, an FEM simulation model was developed to study the thin glass slumping processes on both concave and convex mandrels. Simulation of thin glass sheet slumping on convex mandrel was performed to study the effects of different process parameters, i.e. thickness of the glass sheet, cooling and heating rate, soaking time and soaking temperature. Finally, experiments of thermal slumping glass plates on a parabolic concave mandrel were performed to study the thickness effect on slumping process and the final surface contour of the upper surface of the glass plate. Simulation was again conducted to predict the surface contour. The comparison between simulation and experiments showed that the FEM simulation is adequate for predicting the surface contour if the glass was fully slumped. It was also discovered that for process conditions used, thinner glass sheets were not fully slumped. ii DEDICATION This document is dedicated to my family. iii ACKNOWLEDGEMENTS I would like to express my gratitude to my adviser, Prof. Allen. Yi for providing me with an opportunity to work in a very exciting field of precision optical engineering. I would like to thank Prof. Yi for his trust, guidance, enthusiasm and insight during my research. I also would like to thank Dr. William W. Zhang from Goddard Space Flight Center at NASA for providing financial support on the x-ray mirror development project. I also appreciate the suggestions, assistance and comments of other faculty members at OSU whom I had the opportunities to work with during the course of this research: Prof. Jose Castro, Prof. Betty Lise Anderson, and Prof. Rebecca Dupaix. I am especially in debt to Prof. Castro for the time he spent helping with my questions and patiently guiding me with explanation. I also would like to thank Prof. Anderson for her assistance to listen and suggestions for optical methods to test the lens performance. I would like to thank Dr. Thomas Raasch for assistance in setting up the Shack-Hartmann Sensor (SHS) measuring system. iv I want to thank Prof. Fritz Klocke, Axel Demmer, Dr. Olaf Dambon, Guido Pongs, and Fei Wang at the Institute for Production Technology (IPT), Aachen, Germany for providing some of the experimental support reported in this research. I acknowledge the help from Mary Hartzler at the Department of Integrated Systems Engineering for assisting in the Coordinate Measuring Machine operation. Sincere thanks are extended to all my colleagues and fellow PhD students, for their suggestions and assistance in different parts of this research. I would like to thank Dr. Anurag Jain and Dr. Yang Chen for suggestions in glass forming simulation and their assistance in using different finite element method software programs. Special thanks also go to Dr. Lei Li, Dr. Chunning Huang, Dr. Wei Zhao, Peng He, and Likai Li. In the end, I would also like to take this opportunity to acknowledge the encouragement and moral support provided by my family. v VITA April 1981 ......................................................Born, WuHu, China July 2003 .......................................................B. S. Measuring and Controlling Technique and Instrumentation, University of Science and Technique of China, Hefei, China June 2006 .......................................................M.S. Optical Engineering, Xi'an Institute of Optics and Precision Mechanics of China Academic of Science, Xi'an, China June 2006 to 2010 .........................................Graduate Research Associate, Integrated System Engineering Department, The Ohio State University, Columbus, Ohio vi PUBLICATIONS JOURNAL PUBLICATIONS: 1. L. Su, Y. Chen, A. Y. Yi, F. Klocke, G. Pongs, “Refractive Index Variation in Compression Molding of Precision Glass Optical Components”, Applied Optics, 47 (10), 1662-1667, 2008. 2. Y. Chen, L. Su, A. Y. Yi, F. Klocke, G. Pongs, “Numerical Simulation and Experimental Study of Residual Stresses in Compression Molding of Precision Glass Optical Components,” Journal of Manufacturing Science and Engineering, 130 (5), 051012-1-8, 2008. FIELDS OF INTERESTS Major Field: Industrial and Systems Engineering Studies in: Precision engineering, Precision optics, Glass thermal forming vii LIST OF CONTENTS ABSTRACT ........................................................................................................................ ii DEDICATION ................................................................................................................... iii ACKNOWLEDGEMENTS ............................................................................................... iv VITA .................................................................................................................................. vi LIST OF CONTENTS ........................................................................................................ ii LIST OF TABLES ............................................................................................................. vi LIST OF FIGURE............................................................................................................ viii Chapter 1: INTRODUCTION ........................................................................................ 1 1.1 Compression Molding of Glass Lenses ................................................................ 2 1.2 Thermal Slumping of Glass Mirror ...................................................................... 4 Chapter 2: RESEARCH OBJECTIVE ........................................................................... 7 Chapter 3: STATE OF THE ART ................................................................................ 10 3.1 Glass Rheology .................................................................................................. 10 ii 3.1.1 Viscosity ..................................................................................................... 10 3.1.2 Viscoelasticity in Glass Transition Region ................................................. 13 3.1.3 Viscoelastic models .................................................................................... 16 3.2 Numerical Modeling of Glass Thermal Forming Processes .............................. 18 Chapter 4: GLASS INDEX CHANGE AS A RESULT OF THERMAL TREATMENT 22 4.1 Theory ................................................................................................................ 23 4.1.1 Structural Relaxation .................................................................................. 23 4.1.2 Density Change ........................................................................................... 28 4.1.3 Relation between the Density and the Refractive Index ............................. 31 4.2 FEM Modeling of Glass Cooling ....................................................................... 33 4.3 Simulation Results and Discussions ................................................................... 36 4.3.1 The Effect of Thermal Expansion Coefficient Ratio .................................. 38 4.3.2 The Effect of Cooling Rate
Details
-
File Typepdf
-
Upload Time-
-
Content LanguagesEnglish
-
Upload UserAnonymous/Not logged-in
-
File Pages175 Page
-
File Size-