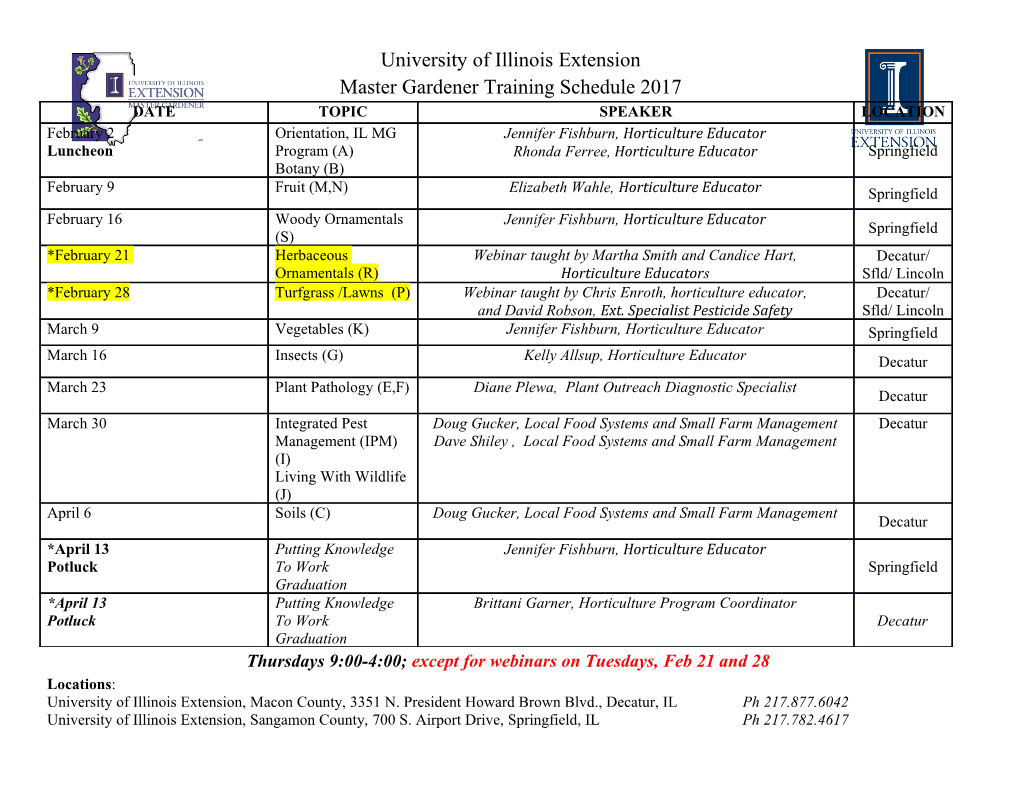
© 2002 ASM International. All Rights Reserved. www.asminternational.org Surface Hardening of Steels: Understanding the Basics (#06952G) CHAPTER 1 Process Selection Guide SURFACE HARDENING, a process that • Thermochemical diffusion methods, which includes a wide variety of techniques (Table 1), modify the chemical composition of the sur- is used to improve the wear resistance of parts face with hardening species such as carbon, without affecting the more soft, tough interior of nitrogen, and boron. Diffusion methods allow the part. This combination of hard surface and effective hardening of the entire surface of a resistance to breakage on impact is useful in part and are generally used when a large num- parts such as a cam or ring gear that must have ber of parts are to be surface hardened. a very hard surface to resist wear, along with a • Applied energy or thermal methods, which tough interior to resist the impact that occurs do not modify the chemical composition of during operation. Further, the surface hardening the surface but rather improve properties by of steel has an advantage over through harden- altering the surface metallurgy; that is, they ing, because less expensive low- and medium- produce a hard quenched surface without carbon steels can be surface hardened without additional alloying species. the problems of distortion and cracking associ- • Surface coating or surface-modification ated with the through hardening of thick sec- methods, which involve the intentional tions. buildup of a new layer on the steel substrate There are three distinctly different ap- or, in the case of ion implantation, alter the proaches to the various methods for surface subsurface chemical composition hardening (Table 1): Each of these approaches for surface harden- ing is briefly reviewed in this chapter, with emphasis placed on process comparisons to Table 1 Engineering methods for surface facilitate process selection. More detailed infor- hardening of steels mation on the various methods described can be found in subsequent chapters. Diffusion methods Carburizing Nitriding Carbonitriding Diffusion Methods Nitrocarburizing Boriding of Surface Hardening Thermal diffusion process Applied energy methods As previously mentioned, surface hardening Flame hardening by diffusion involves the chemical modification Induction hardening of a surface. The basic process used is thermo- Laser beam hardening Electron beam hardening chemical, because some heat is needed to en- hance the diffusion of hardening species into the Coating and surface modification surface and subsurface regions of a part. The Hard chromium plating Electroless nickel plating depth of diffusion exhibits a time-temperature Thermal spraying dependence such that: Weld hardfacing Chemical vapor deposition Case depth ϰ K ͙Tෆimෆeෆ (Eq 1) Physical vapor deposition Ion implantation where the diffusivity constant, K, depends on Laser surface processing temperature, the chemical composition of the © 2002 ASM International. All Rights Reserved. www.asminternational.org Surface Hardening of Steels: Understanding the Basics (#06952G) 2 / Surface Hardening of Steels steel, and the concentration gradient of a given of the absence of oxygen in the furnace at- hardening species. In terms of temperature, the mosphere. Salt bath and pack carburizing have diffusivity constant increases exponentially as a little commercial importance but are still done function of absolute temperature. Concentration occasionally. gradients depend on the surface kinetics and Gas carburizing can be run as a batch or a reactions of a particular process. continuous process. Furnace atmospheres con- Methods of hardening by diffusion include sist of a carrier gas and an enriching gas. The several variations of hardening species (such as carrier gas is supplied at a high flow rate to carbon, nitrogen, or boron) and of the process ensure a positive furnace pressure, minimizing method used to handle and transport the harden- air entry into the furnace. The type of carrier gas ing species to the surface of the part. Process affects the rate of carburization. Carburization methods for exposure involve the handling of by methane is slower than by the decomposition hardening species in forms such as gas, liquid, of carbon monoxide (CO). The enriching gas or ions. These process variations naturally pro- provides the source of carbon and is supplied at duce differences in typical case depth and hard- a rate necessary to satisfy the carbon demand of ness (Table 2). Factors influencing the suitabil- the work load. ity of a particular diffusion method include the Most gas carburizing is done under condi- type of steel, the desired case hardness, and the tions of controlled carbon potential by measure- case depth. ment of the CO and carbon dioxide (CO2) con- It is also important to distinguish between tent. The objective of the control is to maintain total case depth and effective case depth. The a constant carbon potential by matching the loss effective case depth is typically approximately in carbon to the workpiece with the supply of two-thirds to three-fourths the total case depth. enriching gas. The carburization process is The required effective depth must be specified complex, and a comprehensive model of car- so that the heat treater can process the parts for burization requires algorithms that describe the the correct time at the proper temperature. various steps in the process, including carbon diffusion, kinetics of the surface reaction, kinet- ics of the reaction between the endogas and Carburizing enriching gas, purging (for batch processes), Carburizing is the addition of carbon to the and the atmospheric control system. surface of low-carbon steels at temperatures Vacuum carburizing is a nonequilibrium, (generally between 850 and 950 °C, or 1560 and boost-diffusion-type carburizing process in 1740 °F) at which austenite, with its high solu- which austenitizing takes place in a rough vac- bility for carbon, is the stable crystal structure. uum, followed by carburization in a partial pres- Hardening of the component is accomplished sure of hydrocarbon gas, diffusion in a rough by removing the part and quenching or allowing vacuum, and then quenching in either oil or gas. the part to slowly cool and then reheating to the Vacuum carburizing offers the advantages of austenitizing temperature to maintain the very excellent uniformity and reproducibility be- hard surface property. On quenching, a good cause of the improved process control with vac- wear- and fatigue-resistant high-carbon marten- uum furnaces, improved mechanical properties sitic case is superimposed on a tough, low- due to the lack of intergranular oxidation, and carbon steel core. Carburized steels used in case reduced cycle time. The disadvantages of vac- hardening usually have base carbon contents uum carburizing are predominantly related to of approximately 0.2 wt%, with the carbon con- equipment costs and throughput. tent of the carburized layer being fixed between Plasma (ion) carburizing is basically a 0.8 and 1.0 wt%. Carburizing methods include vacuum process using glow-discharge technol- gas carburizing, vacuum carburizing, plasma ogy to introduce carbon-bearing ions to the steel (ion) carburizing, salt bath carburizing, and surface for subsequent diffusion. This process is pack carburizing. These methods introduce car- effective in increasing carburization rates, bon by use of an atmosphere (atmospheric gas, because the process bypasses several dissocia- plasma, and vacuum), liquids (salt bath), or tion steps that produce active soluble carbon. solid compounds (pack). The vast majority of For example, because of the ionizing effect of carburized parts are processed by gas carburiz- the plasmas, active carbon for adsorption can be ing, using natural gas, propane, or butane. Vac- formed directly from methane (CH4) gas. High uum and plasma carburizing are useful because temperatures can be used in plasma carburizing, © 2002 ASM International. All Rights Reserved. www.asminternational.org Surface Hardening of Steels: Understanding the Basics (#06952G) Table 2 Typical characteristics of diffusion treatments Process Typical case Case hardness, Typical base Process Nature of case temperature, °C (°F) depth HRC metals Process characteristics Carburizing Pack Diffused carbon 815–1090 125 µm–1.5 mm 50–63(a) Low-carbon steels, low- Low equipment costs, difficult to control (1500–2000) (5–60 mils) carbon alloy steels case depth accurately Gas Diffused carbon 815–980 75 µm–1.5 mm 50–63(a) Low-carbon steels, low- Good control of case depth, suitable for (1500–1800) (3–60 mils) carbon alloy steels continuous operation, good gas controls required, can be dangerous Liquid Diffused carbon and 815–980 50 µm–1.5 mm 50–65(a) Low-carbon steels, low- Faster than pack and gas processes, can pose possibly nitrogen (1500–1800) (2–60 mils) carbon alloy steels salt disposal problem, salt baths require frequent maintenance Vacuum Diffused carbon 815–1090 75 µm–1.5 mm 50–63(a) Low-carbon steels, low- Excellent process control, bright parts, faster (1500–2000) (3–60 mils) carbon alloy steels than gas carburizing, high equipment costs Nitriding Gas Diffused nitrogen, 480–590 125 µm–0.75 mm 50–70 Alloy steels, nitriding Hardest cases from nitriding steels, nitrogen compounds (900–1100) (5–30 mils) steels, stainless steels quenching not required, low distortion, process is slow, is usually a batch process Salt Diffused nitrogen, 510–565 2.5 µm–0.75 mm 50–70 Most ferrous metals
Details
-
File Typepdf
-
Upload Time-
-
Content LanguagesEnglish
-
Upload UserAnonymous/Not logged-in
-
File Pages16 Page
-
File Size-