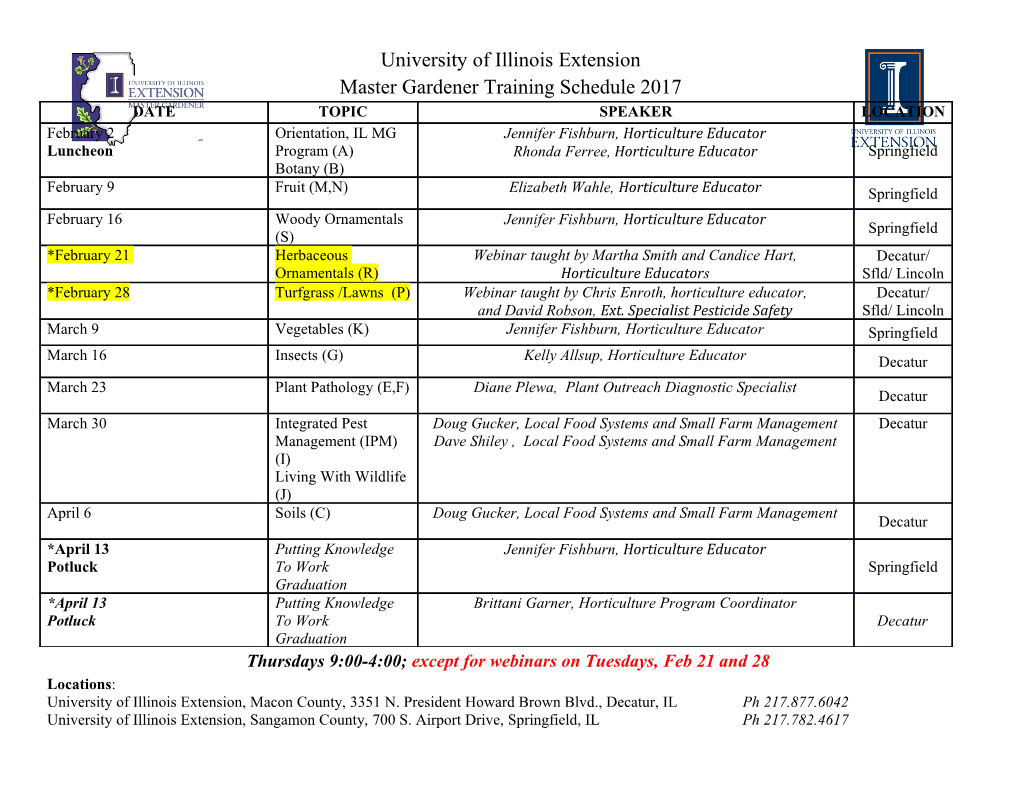
Westinghouse Non-Proprietary Class 3 Award Number DE-NE0000566 Development of LWR Fuels with Enhanced Accident Tolerance DRAFT Final Technical Report RT-TR-15-34 October 30, 2015 Westinghouse Electric Company LLC 1000 Cranberry Woods Drive Cranberry Woods, PA 16066 Principal Investigator: Edward J. Lahoda Project Manager: Frank A. Boylan Team Member Authors Edison Welding Institute General Atomics Idaho National Laboratory Los Alamos National Laboratory Massachusetts Institute of Technology Southern Nuclear Company Texas A&M University Westinghouse Electric Company LLC Table of Contents List of Tables.................................................................................................................. 3 Executive Summary..................................................................................................... 4 1. Introduction .............................................................................................................. 7 2. Accident Tolerant Fuel Development Efforts................................................. 7 2.1 Proposed ATF Fuel Technical Concept Description.............................................................................8 2.2 Research and Development Required for ATF Commercialization...................................................10 2.3 Licensing Path for ATF.......................................................................................................................11 2.4 Business Case Development for ATF.................................................................................................12 2.5 U3Si2 Powder Manufacture and Pelleting .........................................................................................14 2.6 UN/U3Si2 Composite Pellets Manufacture........................................................................................14 2.7 Zirconium Coating Development, Testing and Results .....................................................................15 2.8 SiC composite Cladding Development ..............................................................................................16 2.9 SiC In-reactor Testing........................................................................................................................17 2.10 SiC High Temperature Oxidation Tests ...........................................................................................17 2.11 Oxidation Tests on UN, U3Si2 and UO2 ............................................................................................19 3. Work Products........................................................................................................19 3.1 Publication List ..................................................................................................................................19 3.2 Patent Applications List.....................................................................................................................21 3.3 CARAT Network.................................................................................................................................21 3.4 Deliverables.......................................................................................................................................23 4. Conclusions and Recommendations ...............................................................23 4.1 Conclusions .......................................................................................................................................23 4.2 Recommendations ............................................................................................................................26 4. References................................................................................................................26 5. Acronyms..................................................................................................................27 6. Appendices...............................................................................................................30 2 List of Tables Table 1: Composite pellet densities and uranium content.........................................................................15 Table 2: In-Reactor Corrosion Results for SiC cladding...............................................................................17 Table 3: Initial Oxidation Temperatures of UO2, UN, and U3Si2 ..................................................................19 Table 4: List of Patents Submitted as Pert of ATF Program........................................................................21 Table 5: Program Deliverables....................................................................................................................23 3 Executive Summary Significant progress was made on the technical, licensing, and business aspects of the Westinghouse Electric Company’s Enhanced Accident Tolerant Fuel (ATF) by the Westinghouse ATF team. The fuel 15 pellet options included waterproofed U N and U3Si2 and the cladding options SiC composites and zirconium alloys with surface treatments. Technology was developed that resulted in U3Si2 pellets with densities of >94% being achieved at the Idaho National Laboratory (INL). The use of U3Si2 will represent a 15% increase in U235 loadings over those in UO2 fuel pellets. This technology was then applied to manufacture pellets for 6 test rodlets which were inserted in the Advanced Test Reactor (ATR) in early 2015 in zirconium alloy cladding. The first of these rodlets are expected to be removed in about 2017. Key characteristics to be determined include verification of the centerline temperature calculations, thermal conductivity, fission gas release, swelling and degree of amorphization. Waterproofed UN pellets have achieved >94% density for a 32% U3Si2/68% UN composite pellet at Texas A&M University. This represents a U235 increase of about 31% over current UO2 pellets. Pellets and powders of UO2, UN, and U3Si2the were tested by Westinghouse and Los Alamos National Laboratory (LANL) using differential scanning calorimetry to determine what their steam and 20% oxygen corrosion temperatures were as compared to UO2. Results from this work are summarized as follows: • The oxidation of U3Si2 and UN to U3O8 occurs by a single step reaction compared to the previously determined 2 step oxidation reaction of UO2. • The Westinghouse results of the temperature of oxidation reaction initiation (Tox, i) for these 3 U bearing fuel compounds in powder form can be ranked as follows. Tox, i (20% O2 in He) = UO2 < UN < U3Si2 . Tox, i (steam) = UN < U3Si2 • The LANL results of the temperature of oxidation reaction initiation (Tox, i) for these 3 U bearing fuel compounds in pellet form can be ranked as follows. Tox, i (synthetic air) = U3Si2< UN< UO2 • The oxidation reaction enthalpy for these 3 U bearing fuel compounds can be ranked as follows. RXN enthalpy (syn. air) = UO2 << UN < U3Si2 • U3Si2 and UN when compared to UO2 are on order of magnitude more reactive during oxidation and the proper precautions should be taken during the processing and handling of U3Si2 and UN. Cold spray application of either the amorphous steel or the Ti2AlC was successful in forming an adherent ~20 micron coating that remained after testing at 420°C in a steam autoclave. The coatings were limited to 20 microns to minimize their effect on the neutron economy of the fuel since many of the coating components have relatively high thermal neutron cross-sections. Tests at 1200°C in 100% steam on coatings for Zr alloy have not been successful possibly due to the low density of the coatings which allowed steam transport to the base zirconium metal. Further testing supported this hypothesis since 4 coating thicknesses of ~80 to 90 microns significantly reduced the zirconium oxidation rate. Mechanical testing of the coatings indicated good bonding for the cold-spray applied coatings. Significant modeling and testing has been carried out for the SiC/SiC composite/SiC monolith structures developed by General Atomics (GA). Early modeling efforts indicated that the original monolith on the inside and composite on the outside would not maintain hermeticity in a neutron flux with a thermal gradient applied. This was due to the fact that both the monolith and the composite had the same swelling characteristics. GA then developed a structure with the monolith on the outside and composite on the inside which is the current baseline structure and a SiC to SiC tube closure approach. GA has also developed permeability tests and mechanical tests to verify the operation of the SiC cladding. Steam autoclave (420°C), high temperature (1200°C) flowing steam tests and quench tests have been carried out at the Massachusetts Institute of Technology (MIT) with minimal corrosion, mechanical or hermeticity degradation effect on the SiC cladding or end plug closure. However, in-reactor loop tests carried out in the MIT reactor indicated an unacceptable degree of corrosion, likely due to the corrosive effect of radiolysis products which attacked the SiC. The approaches being applied to rectify this issue include additional hydrogen overpressure to more quickly react these radiolysis products and the addition of catalysts to further accelerate the reaction between the hydrogen and the radiolysis products. A detailed, preliminary regulatory examination has also been completed based on the current Westinghouse ATF designs. The following table highlights the estimated regulatory frame work, timeline, and costs required
Details
-
File Typepdf
-
Upload Time-
-
Content LanguagesEnglish
-
Upload UserAnonymous/Not logged-in
-
File Pages30 Page
-
File Size-