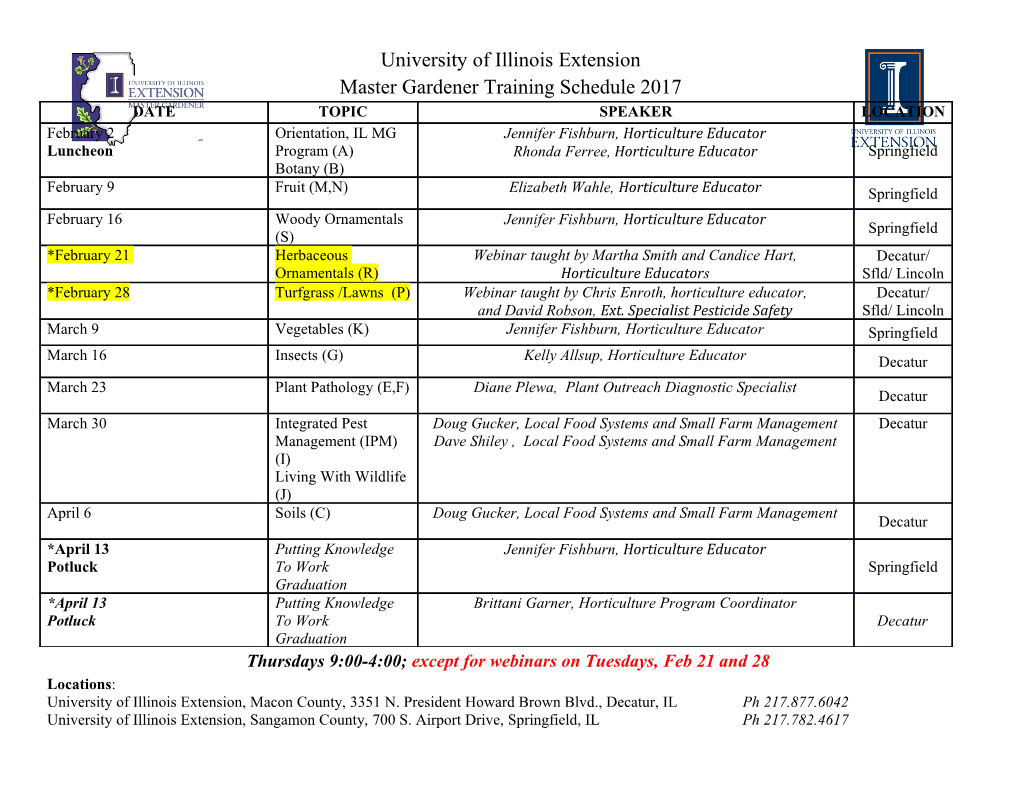
International transference of lean production systems: managerial lessons from Toyota transplants in the USA, Australia, and India A thesis submitted in fulfilment of the requirements for the award of the degree DOCTOR OF PHILOSOPHY from SWINBURNE UNIVERSITY OF TECHNOLOGY (Faculty of Business and Enterprise) by Reynold Peter James BSc (Osmania University, Hyderabad, India) MBA (Xavier’s Labour Relations Institute, Jamshedpur, India) 2012 1 Abstract The purpose of this thesis is to analyse how Toyota went about the process of transplanting its lean production system into three heavily unionized environments in the USA, Australia, and India, namely NUMMI (New United Motor Manufacturing Inc), TMCA (Toyota Motor Corporation of Australia), and TKM (Toyota Kirloskar Motors). Two research questions are embedded within this broad purpose, namely, what resistance did Toyota meet when attempting to transplant its production system into each of these three countries, and what strategies did it employ to manage this resistance? Toyota generally tries to avoid extremely pluralistic-unionised environments when choosing transplantation sites across the world. Its organisational culture is strongly aligned with a unitarist approach in which its operations are conducted within a family-like atmosphere. Therefore, how Toyota conducts its operations in circumstances dissimilar to this is of considerable interest. In this respect, the research conducted in this thesis provides an additional and unique aspect to the literature. The thesis takes a qualitative, emergent approach to addressing this research purpose and research questions, employing the methodology of conceptual ordering within a framework of a comparative case study analysis. The thesis identifies three distinct models of the transplantation process pursued by each of the Toyota transplants: hybrid (NUMMI), slow and piecemeal (TMCA), and authoritarian (TKM). Within the context of these three processes the thesis identifies five comparison features which characterise the transplantation pathways of the Toyota transplants – industrial peace, the extent and pace of TPS introduction, teamworking. cultural consonance, and organisational learning. By identifying these five comparison features the thesis then analyses why each of the transplants has attained different levels of success in achieving each of these features (for instance, industrial peace) within the context of their respective transplantation processes. The thesis has implications for understanding the forms of resistance, and the strategies to be adopted in managing such resistance, when organisations employing lean manufacturing techniques (such as Toyota) attempt to transplant these techniques across national borders into heavily pluralistic and unionised environments. 2 Acknowledgements I wish to sincerely thank the following people who made it possible for me to complete my doctoral study. Professor Bob Jones, my supervisor, for sharing with me his vast repertoire of research skills, knowledge, and experience, for his patience and maturity, for allowing me the freedom to manoeuvre, and whose just-in-time and on-the-job approach to guidance suited me well as an organisational person transitioning into academia. Being Bob’s student has been a privilege. Dr Samir Shrivastava, for introducing me to academia, refining my perspective, immensely reducing my learning curve, constant intellectual and moral support, and for ‘being there’. Dr James Latham, my associate supervisor, for his encouragement and varied inputs especially during field trips. Hayley, Natasha, and Peter, my family, for their many silent sacrifices and support all through The Coopers, for their unfailing back-up when most needed Above all I owe this thesis to my parents who provided me with the platform that everything else rests on and for the value they attached to education. 3 Declaration I, Reynold Peter James, declare that this thesis, submitted in fulfilment of the requirements for the award of Doctor of Philosophy from the Faculty of Business and Enterprise, Swinburne University of technology, Melbourne, Australia: 1. Contains no material which has been accepted for the award to myself of any other degree or diploma, except where due reference is made in the text of this thesis; 2. To the best of my knowledge contains no material previously published or written by any other person except where due reference is made in the text of this thesis. Ethics Approval This thesis has been approved by the Swinburne University Human Research Ethics Committee in terms of SUHREC Project 2009/238 I certify that all conditions pertaining to this ethics clearance have been properly met and that annual reports and a final report have been submitted Signed Reynold Peter James 4 Dedicated to my parents 5 Table of Contents CHAPTER ONE: Purpose, Significance, and Context of the Thesis ………………… 1 Purpose and scope of the thesis……………………………………………………………. 1 Significance of the thesis…………………………………………………………………... 2 Toyota Production System and the Toyota Way…………………………………………… 3 Lean production……………………………………………………………………………. 6 Transplanting TPS and lean production…………………………………………………… 12 Background to the automobile industry in the USA, Australia, and India………………… 17 Background to the US automobile industry………………………………………………. 17 Background to the Australian automobile industry………………………………………. 20 Background to the Indian automobile industry…………………………………………… 24 Structure of the thesis……………………………………………………………………... 27 CHAPTER TWO: Literature, Methodology, and Data Collection and Analysis…… 30 Significant research studies in the transplantation literature……………………………… 30 Ward (1999)………………………………………………………………………………. 32 De Jong et al (2002)………………………………………………………………………. 32 Abo (1994)………………………………………………………………………………… 35 Elger and Smith (1994)……………………………………………………………………. 37 Westney (1999)……………………………………………………………………………. 40 Summary of key points from the literature……………………………………………… 43 Methodology and data collection and analysis……………………………………………. 44 Qualitative methodology………………………………………………………………… 45 Emergent approach………………………………………………………………………. 46 Case study framework……………………………………………………………………. 47 Conceptual ordering………………………………………………………………………. 49 6 Data collection, coding, and analysis…………………………………………………… 49 NUMMI (New United Motor Manufacturing Inc)……………………………………… 49 TMCA (Toyota Motor Corporation Australia)………………………………………….. 55 TKM (Toyota Kirloskar Motors)………………………………………………………… 57 Summary of the overall analysis…………………………………………………………. 60 Evaluation criteria………………………………………………………………………… 62 CHAPTER THREE: Toyota in the USA: New United Motor Manufacturing Inc (NUMMI)………………………………………………………………………………… 68 Chronological listing of significant events……………………………………………….. 68 Union-management relations……………………………………………………………… 73 Labour-management relations: strategic considerations………………………………….. 79 No-lay-off policy and the test of the first crisis…………………………………………… 82 Pitfalls in NUMMI’s labour-management relations………………………………………. 83 Toyota Production System, lean manufacturing, and teams……………………………… 86 Culture and organisational learning……………………………………………………….. 97 Culture, the role of trust, and the test of the first crisis……………………………………. 103 Organisational learning……………………………………………………………………. 105 CHAPTER FOUR: Toyota in Australia: Toyota Motor Corporation Australia (TMCA)…………………………………………………………………………………. 114 Chronological listing of significant events………………………………………………. 114 Union-management relations…………………………………………………………….. 121 Toyota Production System, lean manufacturing, and teams…………………………….. 129 Quality and performance………………………………………………………………… 136 Performance and productivity…………………………………………………………… 141 Teams and leadership……………………………………………………………………. 144 7 Culture and organisational learning…………………………………………………….. 148 CHAPTER FIVE: Toyota in India: Toyota Kirloskar Motors (TKM)……………. 164 Chronological listing of significant events…………………………………………….. 164 Union-management relations…………………………………………………………… 168 Plant-level industrial relations issues at TKM………………………………………….. 175 The 2001 strike………………………………………………………………………….. 177 The 2006 strike………………………………………………………………………….. 179 Toyota Production System, lean manufacturing, and teams…………………………… 186 Nature of TPS in TKM…………………………………………………………………. 189 Production, quality, and productivity…………………………………………………... 195 Teams at TKM…………………………………………………………………………. 199 Culture and organisational learning……………………………………………………. 202 Japan versus India: cultural conduciveness to TPS and lean………………………….. 202 Company-level cultural issues…………………………………………………………. 206 CHAPTER SIX: Similarities, Differences, Comparison Features, and Integrative Questions: NUMMI, TMCA, and TKM……………………………………………... 218 Union-management relations…………………………………………………………… 219 Comparison feature (i): Industrial peace……………………………………………….. 219 TPS, lean manufacturing, and teams…………………………………………………… 226 Comparison feature (ii): Introduction of TPS: extent and pace………………………... 226 Comparison feature (iii): Teamworking………………………………………………... 233 Culture and organisational learning……………………………………………………. 238 Comparison feature (iv): Cultural consonance………………………………………… 238 Comparison feature (v): Organisational learning……………………………………… 246 8 CHAPTER SEVEN: Conclusion: Uniqueness, Significance, and Implications of the Thesis………………………………………………………………………….. 260 Uniqueness and significance of the thesis…………………………………………….. 260 Models of the transplantation process………………………………………………… 261 Assertions from the findings of the thesis…………………………………………….
Details
-
File Typepdf
-
Upload Time-
-
Content LanguagesEnglish
-
Upload UserAnonymous/Not logged-in
-
File Pages311 Page
-
File Size-