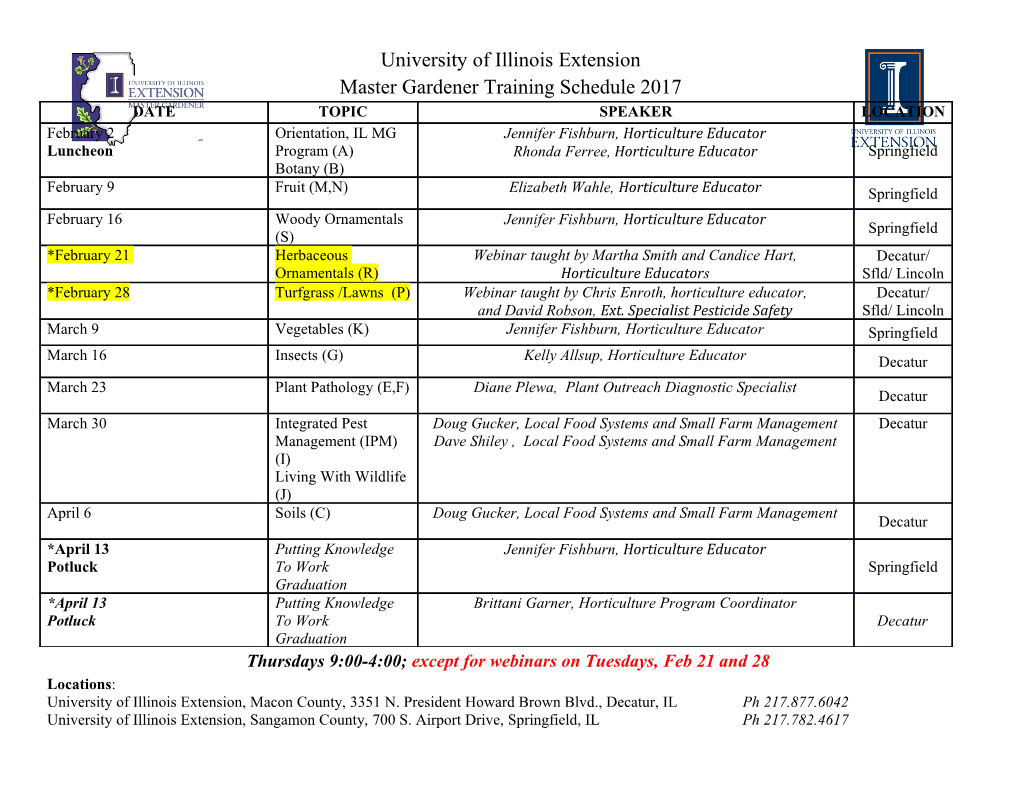
Journal of Thermal Energy Systems Volume 4 Issue 1 Thermal Properties of Epoxy Composites Reinforced with Hollow Glass Microsphere Particulates Pawan Patle1*, Alok Agrawal2 1M.Tech. Scholar, Department of Mechanical Engineering, Sagar Institute of Research & Technology, Bhopal, Madhya Pradesh, India, 2 Assistant professor, Department of Mechanical Engineering, Sagar Institute of Research & Technology, Bhopal, Madhya Pradesh, India Email: [email protected] Abstract Composite materials are emerging as a potential material which are now being used in various applications which includes aircraft, helicopters, space-craft, satellites, ships, submarines, microelectronics, building purpose etc. This composite material has grown deep interest of many researchers all around the world. Among the various class of available composite material, polymeric composites have emerged as important materials because of their light weight, high specific strength and stiffness, excellent fatigue resistance and outstanding corrosion resistance compared to most common metallic alloys. In that respect, the present work aims at developing a class of polymer composites consisting of epoxy as a matrix material with hollow glass microsphere as a reinforcing material. A set of composites with varying loading of filler content ranging up to 25 wt. % has been fabricated using simple hand lay-up technique. The effect of filler content on thermal properties of such fabricated samples is investigated. The various thermal property evaluated are thermal conductivity, glass transition temperature and coefficient of thermal expansion. From the experimental results, it is found that hollow glass micro-sphere filled epoxy composites exhibit improved thermal insulation property, increased glass transition temperature and reduced coefficient of thermal expansion. With modified thermal property, the presently fabricated composites have the potential to be used in applications where thermal insulation is of prime importance. Also with improved glass transition temperature and coefficient of thermal expansion material can find its application where resistance to thermal fatigue is required. Keywords: Polymer composites, hollow glass microsphere, thermal conductivity, glass transition temperature, coefficient of thermal expansion. INTRODUCTION and combining the constituents by various A composite is a mixture of two or more means. distinct constituents or phases. In addition three other criteria are generally fulfilled The most common matrix materials for before we call a material a composite. composites are considered to be Firstly, both constituents have to be polymeric. The reasons for this are present in reasonable proportions. twofold. Firstly, in general the mechanical Secondly, the constituent phases should properties of polymers are inadequate for have distinctly different properties, such many structural purposes. In particular that the composite’s properties are their strength and stiffness are low noticeably different from the properties of compared with other matrix materials i.e. the constituents. Lastly, a composite is metals and ceramics. This means that there usually produced by deliberately mixing is a considerable benefit to be gained by reinforcing polymers, and that the 41 Page 41-47 © MAT Journals 2019. All Rights Reserved Journal of Thermal Energy Systems Volume 4 Issue 1 reinforcement does not have to have tensile and impact properties of HGM exceptional properties. Secondly, and most filled PVC composites where he found that importantly, the processing of polymer Young’s modulus increases and tensile matrix composites (PMCs) need not yield strength decreases linearly with filler involve high pressures and does not content, whereas, impact strength require high temperatures. decreases even with low filler concentration of about 5 vol % and after Among the various reinforcement material, that it remain almost constant with further glass as reinforcement is always on upper increase in filler loading [3]. Gupta and hand for polymer composites but mostly in Woldesenbet [5] done morphological fiber form. Glass in the form of sphere is study of epoxy/HGM composite and of two type’s i.e. solid glass microsphere perform a compression microscopic (SGM) and hollow glass microsphere examination of their compressive fracture (HGM). SGMs are a kind of small solid features. spherical particles with a smooth surface, whereas HGMs consist of an outer smooth In a more recent work, Rue et al. [6] stiff glass and an inner space filled with developed a temperature resistance inert gas. Both types of glass microspheres buoyancy material with the help of tert- are considered as potential fillers for butyl alcohol gelcasting process taking polymer resin which are being used in borosilicate glass as a matrix material and various industries. hollow glass microspheres as filler within matrix body. Zhang et al. [7] studied the Micro-sized hollow spheres of glass are mechanical properties of polymers filled being manufactured for a wide variety of with hollow glass microsphere. They uses in research, medicine, consumer investigated the compressive and tensile goods and various industries. But its trends of mentioned polymers under the potential as a reinforcing element in condition of low strain rate, whereas under polymers has not been adequately the condition of high strain rate they went explored. Hollow-glass micro-spheres through only compressive behavior. have several advantages and can be Recently, Yu et al. [8] prepared preferred over irregular ones in many honeycomb like structure using hollow engineering applications due to their low glass microsphere in epoxy resin and surface area to volume ratio, low density, added polystyrene beads in to it. Against high flowing ability and close sizing etc. this background, an attempt has been made Nijenhuis et al. [1] prepared nylon-6/HGM in this research work to develop hollow composites, which led to the emergence of glass microsphere (HGM) based epoxy a new material with reduced density. They composites using simple hand lay-up showed the stiffness and shear modulus of technique and to study their thermal these composites increase with filler behavior under controlled laboratory concentration. Later, Patton et al. [2] also conditions. took the advantage of low density of HGM with the presence of high concentration of Material Used hydrogen in it and reinforced it in LDPE The most popular epoxy monomers is used resin and suggested its application as as matrix material in present study. It radiation shield. While doing extensive provides a solvent free room temperature research on SGM filled polymer curing system when it is combined with composites, Liang also documented the hardener tri-ethylene-tetramine properties of composites when HGM is (TETA) which is an aliphatic primary reinforced in different polymer resins [3- amine with commercial designation K- 4]. He first gave an insight about the 6.The epoxy resin with its corresponding 42 Page 41-47 © MAT Journals 2019. All Rights Reserved Journal of Thermal Energy Systems Volume 4 Issue 1 hardener is procured from M/s Atul 10:1 by weight as recommended. Limited, Bhopal. The present research 2. Hollow glass micro-sphere will then work aimed to develop polymer composite added to the epoxy-hardener using hollow glass microsphere (HGM) as combination and mixed thoroughly by filler material. For this, hollow glass hand stirring. microspheres of average size of 75m are 3. Before pouring the epoxy/filler the primary filler materials to be used in mixture in the mould, a silicon spray is the present research work. The glass done over the mold so that it will easy microspheres used in present investigation to remove the composite after curing. were procured from Scientific Ltd, Bhopal. The uniformly mixed dough is then slowly poured into the mouldso as to COMPOSITE FABRICATION get specimens of size as per ASTM In the present investigation, particulate standards. filled polymer composite is fabricated 4. The cast is than cured for 12 hours using simple hand lay-up technique. The before it was removed from the mould. fabrication of composite using hand lay-up Composites were fabricated with method involves following steps: different weight fraction of filler 1. The room temperature curing epoxy ranging from 0 to 25 wt. %. The list of resin (L-12) and corresponding fabricated composite in present work is hardener (K-6) are mixed in a ratio presented in table 1. Table 1: List of epoxy based composites filled with SGM S.No. Set Composition 1 Set 1 Neat Epoxy 2 Set 2 Epoxy + 5 % by weight HGM 3 Set 3 Epoxy + 10 % by weight HGM 4 Set 4 Epoxy + 15 % by weight HGM 5 Set 5 Epoxy + 20 % by weight HGM 6 Set 6 Epoxy + 25 % by weight HGM CHARACTERIZATION Coefficient of thermal expansion of the Thermal conductivity of the fabricated composites are measured with a Perkin composites are measured by Unitherm Elmer DSC-7 Thermal Mechanical Model 2022.The tests are in accordance Analyzer. During the measurement, the with ASTM E-1530 Standard. A sample specimen is heated from 30 to 150°C at a of the material which is tested is held heating rate of 5°C/min. For each under a uniform compressive load between measurement, two heating scans are used. two polished surfaces, each controlled at a The first heating scan is used to eliminate different temperature. The heat flows from any possible internal stress and moisture in the upper surface, to the lower surface, the sample which is likely to be generated
Details
-
File Typepdf
-
Upload Time-
-
Content LanguagesEnglish
-
Upload UserAnonymous/Not logged-in
-
File Pages7 Page
-
File Size-