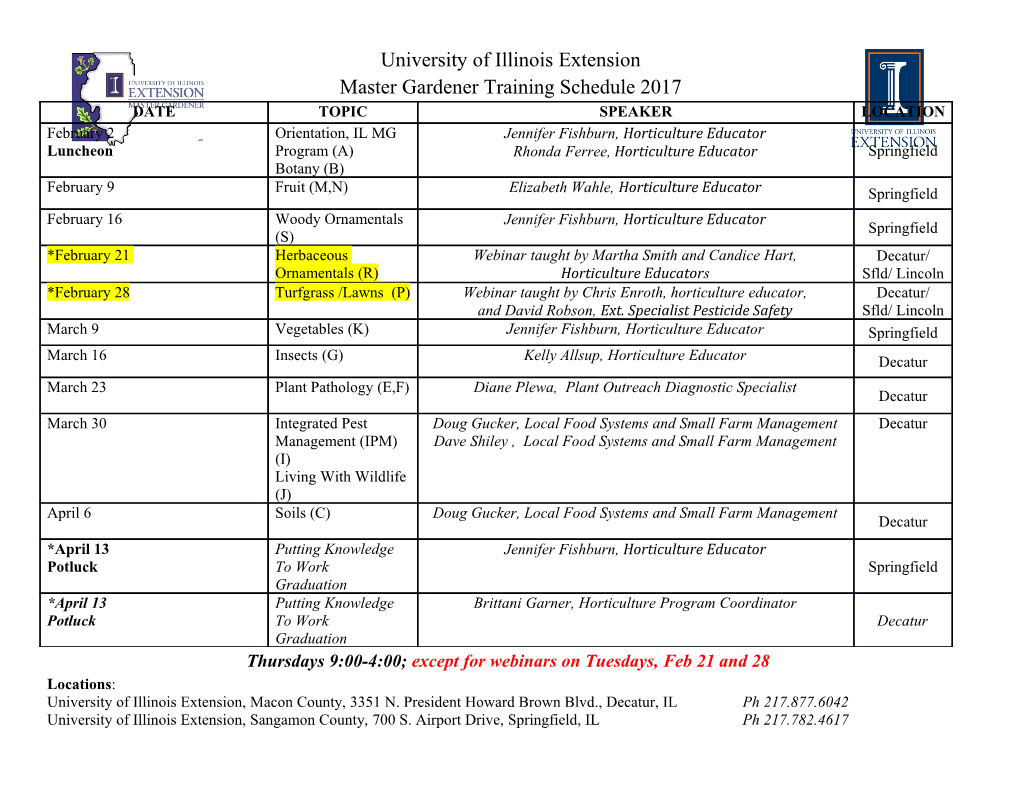
processes Article Direct Solid Oxide Electrolysis of Carbon Dioxide: Analysis of Performance and Processes 1, 1,2, 1 1 1,2 Severin Foit y , Lucy Dittrich y, Tobias Duyster , Izaak Vinke , Rüdiger-A. Eichel and L. G. J. (Bert) de Haart 1,* 1 Institute of Energy and Climate Research, Fundamental Electrochemistry (IEK-9), Forschungszentrum Jülich GmbH, 52425 Jülich, Germany; [email protected] (S.F.); [email protected] (L.D.); [email protected] (T.D.); [email protected] (I.V.); [email protected] (R.-A.E.) 2 Institute of Physical Chemistry, RWTH Aachen University, 52074 Aachen, Germany * Correspondence: [email protected] Authors with equal contribution. y Received: 1 October 2020; Accepted: 26 October 2020; Published: 31 October 2020 Abstract: Chemical industries rely heavily on fossil resources for the production of carbon-based chemicals. A possible transformation towards sustainability is the usage of carbon dioxide as a source of carbon. Carbon dioxide is activated for follow-up reactions by its conversion to carbon monoxide. This can be accomplished by electrochemical reduction in solid oxide cells. In this work, we investigate the process performance of the direct high-temperature CO2 electrolysis by current-voltage characteristics (iV) and Electrochemical Impedance Spectroscopy (EIS) experiments. Variations of the operation parameters temperature, load, fuel utilization, feed gas ratio and flow rate show the versatility of the procedure with maintaining high current densities of 0.75 up to 1.5 A cm 2, therefore resulting in high conversion rates. The potential of the high-temperature carbon · − dioxide electrolysis as a suitable enabler for the activation of CO2 as a chemical feedstock is therefore appointed and shown. Keywords: carbon dioxide; solid oxide electrolysis; carbon dioxide utilization; CO2-electrolysis; high-temperature electrolysis; carbon dioxide reduction 1. Introduction The world-wide chemical industry is currently depending on fossil resources for the production of carbon based chemicals. To reach full sustainability in the sector of chemical industry, the necessity of circular carbon economy is evident. This is not possible by exploiting fossil resources. An abundant compound containing carbon is carbon dioxide (CO2). Even in a scenario of 100% renewable energy generation, emissions of carbon dioxide by processes within the chemical sector is in the range of multiple hundred million metric megatons per year [1]. As CO2 has a low energetic value and is therefore rather inert, it has to be activated to be used as a starting material in value-chains of the chemical industry. Carbon monoxide (CO) is already a bulk chemical in industrial chemistry. It is used as a building block in polymers like e.g., polyurethanes and polycarbonates, but can also be transformed to a vast range of products as the carbon containing part in syngas, a mixture of carbon monoxide and hydrogen [2–7]. Hence, a sustainable conversion of carbon dioxide to carbon monoxide is enabling the processes of carbon capture and utilization (CCU) and power-to-x [8]. Using renewable energy, the electrochemical reduction of CO2 to CO is an interesting and seemingly simple process for the solution of the above mentioned challenges. This reaction has been examined both for low-temperature and high-temperature procedures with vast differences in performance, efficiencies and general operation parameters [9]. The high-temperature electrolysis of Processes 2020, 8, 1390; doi:10.3390/pr8111390 www.mdpi.com/journal/processes Processes 2020, 8, 1390 2 of 14 CO2 to CO on ceramic solid oxide cells seems superior in these regards with a faradaic efficiency of 100% and overall energetic efficiencies of over 75%. This conversion has been attempted mostly as a part of syngas production by using water and carbon dioxide simultaneously as starting feeds [10], which is not a direct electrolysis of carbon dioxide in particular. Concerning the electrolysis of pure carbon dioxide, a few aspects have been viewed at, however with a focus on materials [11–18]. We present the process investigation of the variation of different operation parameters temperature, load, fuel utilization, feed gas ratios and flow rates of the high-temperature solid oxide electrolysis of carbon dioxide to carbon monoxide. 2. Materials and Methods The commercially available single button cells (Elcogen®, Tallinn, Estonia) used in the following experiments consist of a cathode-supported porous NiO-8YSZ-cermet fuel cathode, a 8%-Yttria-stabilized zirconia (8YSZ) electrolyte, a Gadolinium-doped ceria (GDC) and a porous La0.6Sr0.4CoO3-δ (LSC) oxygen anode. The cathode, electrolyte and GDC layer have a diameter of 20 mm and a totalled thickness of 300 30 µm. The anode has a diameter of 10 mm and a thickness of ± 15 5 µm, giving an active area of 0.79 cm2 ± The single-cells are installed in a two-electrode conductivity & impedance spectroscopy Probostat-setup (Norwegian Electro Cermaics® NORECS, Oslo, Norway). A gold ring is used as a sealing sample between the anodic side of the cell and the inner ceramic gas chamber to separate the air and fuel side. The current collector on the fuel side consists of a nickel and a platinum mesh. On the air side, only platinum is used for the current collection. The setup is enclosed and heated up with a furnace from the company Carbolite Gero®(Neuhausen, Germany). The heating rate is kept at 2 C min 1 throughout all the measurements to protect the materials from thermomechanical ◦ · − stress. The reduction of the fuel electrode from NiO-YSZ to Ni-YSZ to activate the catalyst properties of Nickel is carried out at 900 ◦C with a stepwise increase of hydrogen concentration in the fuel feed gas starting at 0% up to 100% with nitrogen as balance gas. In this work, we have chosen the temperatures 800 and 850 ◦C for the investigation of effects of variating operation parameters. This is a suitable compromise, by which cell performance and material stability can be guaranteed. Besides, a temperature series between 700–900 ◦C in equivalent 1 1 T− /K− -steps with the volumetric fuel composition of 80:20 of CO2:CO has been performed to apply the Arrhenius equation. The supply of the gases H2,N2, CO2, CO (fuel side) and air (air side) is controlled by mass flow controllers (MFC, Bronkhorst Nord®, Kamen, Germany). A constant volume flow of 6 L h 1 · − is applied to both gas chambers, when not specified differently. Current-voltage characteristics (iV) and Electrochemical Impedance Spectroscopy (EIS) experiments are managed via a Vertex 5A Potentiostat/Galvanostat (Ivium Technologies®, Eindhoven, Netherlands) using a two-electrode system. The cell performance is measured consecutively twice by applying a differential current with a scan rate of 10 mA s 1 from open cell voltage (OCV) up to 1.4 V. The area-specific resistance (ASR) is · − calculated using the numerical differential of the iV curves at OCV and 350 mA cm 1. · − The process analysis of the cell is determined by AC characterization at OCV and 350 mA cm 2. · − The spectra are recorded in a frequency range from 110 kHz to 0.11 Hz with 73 measuring points and an applied amplitude of 20 mA. 3. Results 3.1. Performance The performance of high-temperature CO2-electrolysis was studied by dc current-voltage measurements. The resulting iV curves for various CO2 partial pressures, temperatures and flow rates are shown in Figure1a–c, respectively. Processes 2020, 8, 1390 3 of 14 Processes 2020, 8, x FOR PEER REVIEW 3 of 14 1.4 1.4 1.3 1.3 1.2 1.2 700 °C 717 °C 734 °C E / V / E 1.1 V / E 1.1 752 °C 771 °C 50 CO 791 °C 1.0 2 1.0 811 °C 60 CO2 70 CO 832 °C 0.9 2 853 °C 80 CO 0.9 2 874 °C 90 CO2 900 °C 0.8 0.8 0.0 0.5 1.0 1.5 0.0 0.5 1.0 1.5 -2 -2 |i|normalized / A·cm |i| / A·cm normalized (a) (b) 1.4 1.3 1.2 1.0 l·h-1 E / V / E 1.1 1.5 l·h-1 2.0 l·h-1 1.0 2.5 l·h-1 3.0 l·h-1 -1 0.9 4.0 l·h 5.0 l·h-1 6.0 l·h-1 0.8 0.0 0.5 1.0 1.5 |i| / A·cm-2 normalized (c) -1 FigureFigure 1. iViV curves curves at at various various operating operating parameters: parameters: (a) ( avariation) variation of CO of CO2:CO2:CO ratio ratio at 800 at 800°C and◦C and6 l·h 6; 1 1 L(bh) variation;(b) variation of temperature of temperature for a ratio for of a ratio CO2:CO of CO of 80:20:CO ofat 80:206 l·h −1 at; (c 6) Lvariationh ;(c) of variation flow rate of for flow a ratio rate · − 2 · − forof CO a ratio2:CO of of CO 80:202:CO at of800 80:20 °C. at 800 ◦C. TheThe variationvariation ofof COCO22 partial pressurepressure waswas balancedbalanced byby CO.CO. ThatThat meansmeans reducingreducing COCO22 partialpartial pressurepressure waswas accompaniedaccompanied byby increasingincreasing COCO andand vicevice versa.versa. TheThe obtainedobtained areaarea specificspecific resistancesresistances (ASR)(ASR) and current current densities densities at at 1.4 1.4 V V(i1.4 (i V1.4) for V) variation for variation of CO of2 partial CO2 partial pressure pressure are presented are presented in Figure in Figure2a (values2a (values in Table in Table A1). A1For in increasing Appendix theA). ForCO2 increasing partial pressure, the CO the2 partial ASR pressure,at OCV increases the ASR atwith OCV a increases with a factor of 1.6 from 0.34 W cm2 at 50% CO to 0.56 W cm2 at 90% CO .
Details
-
File Typepdf
-
Upload Time-
-
Content LanguagesEnglish
-
Upload UserAnonymous/Not logged-in
-
File Pages14 Page
-
File Size-