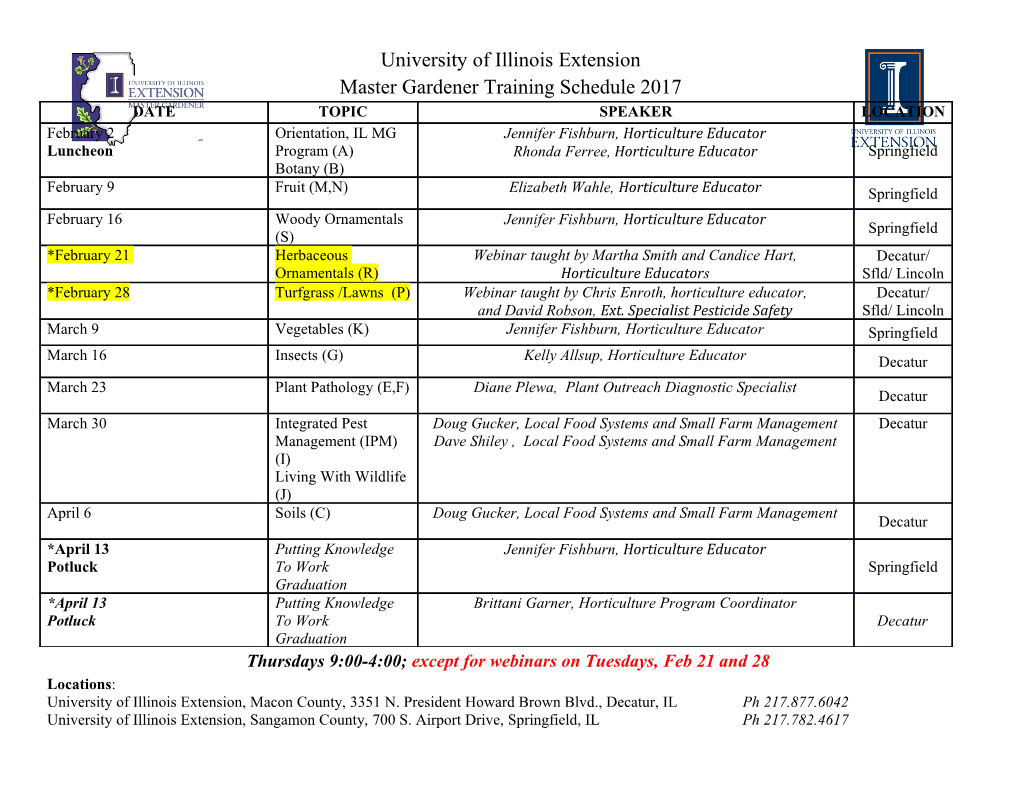
FULLY INTEGRATED MASS FLOW, PRESSURE, DENSITY AND VISCOSITY SENSOR FOR BOTH LIQUIDS AND GASES T.V.P. Schut1, D. Alveringh1, W. Sparreboom2, J. Groenesteijn2 R.J. Wiegerink1, and J.C. Lötters1,2 1 MESA+ Institute for Nanotechnology, University of Twente, Enschede, THE NETHERLANDS 2 Bronkhorst High-Tech BV, Ruurlo, THE NETHERLANDS ABSTRACT This paper reports on a fluid viscosity sensor consisting of pressure sensors fully integrated with a Coriolis mass flow sensor. The sensor is capable of measuring viscosities of both liquids and gases through a mathematical model. For liquids, this model is simply the Hagen-Poiseuille equation. For gases, a more elaborate model is derived, taking into account compressibility and additional pressure losses due to channel geometry. Viscosities of (mixtures of) water and isopropanol were measured and correspond well with values found in literature. Viscosities of nitrogen and argon were measured with accuracies of ∼0-12%, depending on input pressure and mass flow rate. Improvement of the Figure 1: Overview of the sensor. Pressure sensors upstream mathematical model could lead to higher accuracy and less and downstream of a Coriolis mass flow sensor are used to determine the pressure drop over the channel. Various fluid dependence on mass flow or pressure. parameters can be determined using the sensor. INTRODUCTION In many applications, knowledge of flow rate and fluid composition is of great importance, e.g. mixing of chemicals in (bio)chemical processes. Fluid composition can be determined from parameters such as pressure, mass flow rate, density and viscosity. In this paper, a sensor is presented which can measure all of the above mentioned Figure 2: Schematic representation of the sensor modes. Left: Actuation/Twist mode. Right: Detection/Swing mode. properties. The sensor consists of a micro Coriolis mass flow sensor integrated with resistive pressure sensors. drop over a Coriolis mass flow sensor, taking into account A micro Coriolis mass flow sensor [1] measures both compressibility and the aforementioned additional losses. mass flow and fluid density. The relation between mass flow and pressure drop over the channel can be used to determine DESIGN fluid viscosity. This is the most straightforward way to obtain An overview of the sensor is presented in Figure 1. viscosity [2] although other techniques have been proposed, The figure describes how the various fluid parameters are e.g. [3–5]. Lötters et al. presented a Coriolis-based multi- determined. parameter sensor [6] with external pressure sensors which Coriolis mass flow sensor could measure viscosities of liquids and gases within 10% accuracy. However, the gas viscosities were determined only The Coriolis mass flow sensor design is based on the for low flows, where compressibility could be neglected. sensor presented in [1]. The sensor has been characterized A subsequent sensor was presented in [7] with integrated in this paper by Sparreboom et al. The sensor works by capacitive pressure sensors. In [8], it was proposed to bringing it into resonance in the twist mode, see Figure integrate resistive pressure sensors with a Coriolis mass 2. When a flow is introduced, this results in a vibration flow sensor. Combining the latter sensor with a new model in the swing mode. The amplitude of this vibration is a for the pressure drop gives a means of measuring viscosities measure for the flow and can be measured with comb C ; C of liquids and gases for the full laminar flow range. In drive capacitors ( 1 2) positioned at the free end of the case of liquids, the Hagen-Poiseuille equation is applicable channel. The density of the fluid inside the channel can be and pressure drop is directly proportional to viscosity. For determined from the resonance frequency. gases, a more elaborate model is needed. This is because: Pressure sensors 1) gases are compressible, i.e. gas density will change over The pressure sensors consist of resistive strain gauges the length of the channel, and 2) kinetic energy losses due patterned on top of the channel upstream and downstream of to sharp bends in the channel cannot be neglected due the Coriolis mass flow sensor (see Figure 1). The design and to high(er) flow velocities. A model was derived which characterization of the pressure sensors has been presented can be used to determine gas viscosity from the pressure in [8]. The operation of the sensors is explained in Figure 3. that the density will also vary throughout the channel. Furthermore, sharp bends and junctions in the channel introduce additional pressure drop. Due to high(er) flow velocities in gas flow, this effect cannot be neglected. A relation for the pressure drop over a straight channel can be derived from the basic energy relations for flow [10, 11]: u v dP + du + δU = 0 (4) β dis Figure 3: Schematic representation of the pressure sensors. Where the first term represents a change in energy contained A pressure inside the channel results in deformation of the in a volume (per unit mass) of fluid v due to a change roof and elongation/compression of the strain gauges. The in pressure dP. The second term represents a change in resistances R R will decrease while R R increase. 1 & 4 2 & 3 kinetic energy, where u is the flow velocity and β is a MATHEMATICAL MODEL correction factor. The value of β depends on the flow regime Density (Turbulent: β = 1, Laminar: β = 0:5). Finally, the third and The actuation mode of the Coriolis mass flow sensor last term represents the dissipated energy due to friction. can be modelled as a second order system with resonance Laminar flow is assumed, Re < 2000 & β = 0:5, where Re frequency: is the Reynolds number. After various steps of substitution r k and integration, equation 4 becomes: !0 = (1) m 2 2 2 2 P − P φm P1 l φm With k the modal spring constant and m the modal mass. The 2 1 + 2 ln + 2 f = 0 (5) 2RT A P r A relation between resonance frequency, pressure and density 2 is different for liquid- and gas flow due to compressibility. Where A is the cross sectional area of the channel and f is This leads to two expressions for the resonance frequency: the friction factor, which is dependent on viscosity: s s k¹Pº k + αP 8 4µπr ! = = 0 f = = (for Re < 2000) (6) liquid Re φm ρflVch + mch ρflVch + mch (2) s s Where µ is the dynamic viscosity. Thus, the dynamic k¹Pº k0 + αP !gas = = viscosity of a gas flowing through a straight channel can be ρ ¹PºV + m PV /RT + m fl ch ch ch ch determined with equation 5. However, as already mentioned, the channel contains sharp bends and junctions which Where k¹Pº is the pressure dependent spring constant, k0 introduce additional pressure drop. This additional pressure is the spring constant at atmospheric pressure, ρfl is the drop due to these bends and junctions can be characterized density of the fluid inside the channel, Vch is the inner by a loss coefficient κ [9]: volume of the channel and mch is the mass of the channel itself. For gas, ρ = P/RT according to the ideal gas fl 1 1 κφ2 RT law [9], with pressure P, specific gas constant R and ∆P = ρu2κ = m (7) 2 2 PA2 temperature T. The spring constant is pressure dependent due to deformation of the channel by an applied pressure. Where ∆P is the pressure drop over the turn/junction and The resulting pressure dependency coefficient α can be fitted P is the pressure just before the turn/junction. The channel from measurement data. When α is known, fluid density can contains junctions where it splits into three equally large easily be determined from the resonance frequency. channels and it contains junctions where these channels Viscosity are joined back together. These junctions can be modelled The viscosity of the fluid inside the channel can as sudden expansion/contraction of the channel. These be determined from the relation between mass flow and junctions and the 90 degree bends are characterized each by pressure drop. For liquid flow, this relation is simply the their own loss coefficient. Table 1 shows the loss coefficient Hagen-Poiseuille equation: for each situation. Now the total pressure drop over the channel can be 8l estimated. Equation 5 can be used to calculate the pressure P − P = ηφm · (3) 2 1 πr4 drop over the straight channel sections. By combining equations 5 and 7, the pressure drop over the junctions/turns Where P1/2 is the up-/downstream pressure, η is the kinematic viscosity, φm is the mass flow rate and l; r are Symbol Description Value the channel length and effective radius respectively. κse Sudden expansion of the channel 0.44 κ Sudden contraction of the channel 0.28 For gas flow, the relation between pressure drop and sc κturn 90 degree turn in the channel 0.40 viscosity is not linear. The pressure throughout the channel is not constant. Since gas is compressible, this means Table 1: Loss coefficients for the different situations. [9] 1000 950 ) 3 900 850 Density (kg/m Literature Sensor at 3 bar 800 Sensor at 4 bar Sensor at 5 bar Sensor at 6 bar 750 0 20 40 60 80 100 Percentage of isopropan-2-ol (%) Figure 4: Scanning electron microscope image of the sensor. Figure 6: Measured densities of the liquids in comparison with experimentally determined values from [13]. ) −1 K 300 −2 s 2 275 250 225 200 175 N2: Literature Ar: Literature Measured Measured Figure 5: Schematic representation of the measurement 150 setup. Specific gas constant (m 5 6 7 8 Applied pressure (bar) can be calculated.
Details
-
File Typepdf
-
Upload Time-
-
Content LanguagesEnglish
-
Upload UserAnonymous/Not logged-in
-
File Pages4 Page
-
File Size-