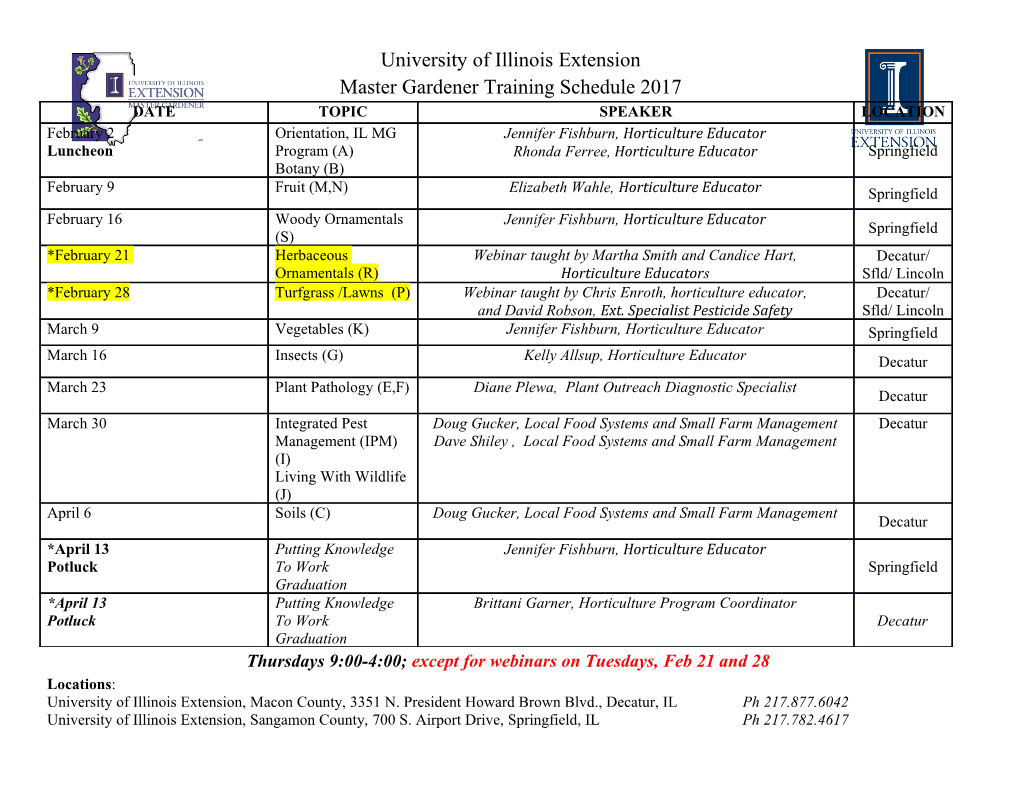
Santa Clara University Scholar Commons Mechanical Engineering Senior Theses Engineering Senior Theses 6-2018 3D Printed Carbon Fiber Electric Mountain Bike Frame Chris Edwards Santa Clara University, [email protected] Fionn Ruder Santa Clara University, [email protected] Joseph Hurley Santa Clara University, [email protected] Micah Thomas Santa Clara University, [email protected] Mitch Spinelli Santa Clara University, [email protected] See next page for additional authors Follow this and additional works at: https://scholarcommons.scu.edu/mech_senior Part of the Mechanical Engineering Commons Recommended Citation Edwards, Chris; Ruder, Fionn; Hurley, Joseph; Thomas, Micah; Spinelli, Mitch; and Gribb, Parker, "3D Printed Carbon Fiber Electric Mountain Bike Frame" (2018). Mechanical Engineering Senior Theses. 83. https://scholarcommons.scu.edu/mech_senior/83 This Thesis is brought to you for free and open access by the Engineering Senior Theses at Scholar Commons. It has been accepted for inclusion in Mechanical Engineering Senior Theses by an authorized administrator of Scholar Commons. For more information, please contact [email protected]. Author Chris Edwards, Fionn Ruder, Joseph Hurley, Micah Thomas, Mitch Spinelli, and Parker Gribb This thesis is available at Scholar Commons: https://scholarcommons.scu.edu/mech_senior/83 3D PRINTED CARBON FIBER ELECTRIC MOUNTAIN BIKE FRAME By Chris Edwards, Fionn Ruder, Joseph Hurley, Micah Thomas, Mitch Spinelli, Parker Gribb SENIOR DESIGN PROJECT REPORT Submitted to the Department of Mechanical Engineering of SANTA CLARA UNIVERSITY in Partial Fulfillment of the Requirements for the degree of Bachelor of Science in Mechanical Engineering Santa Clara, California 2018 Abstract 3D printing of carbon fiber composites has been a developing technology for about 5 years, and in this time, Arevo Labs has established itself as a leader in the field. Our team joined forces with Arevo, who sponsored our project as we showcased their new, innovative carbon fiber manufac- turing process. To do so, we focused on the conceptual design, analysis, assembly, and material testing of an electric mountain-bike frame printed with Arevo’s continuous carbon fiber printing technology. Our bike consists of the main frame and a chain stay subsystem, which connects the rear wheel to the rest of the frame and interfaces with a suspension system. Understanding how the capabilities of the printer, the properties of the materials, and the typical loading scenarios expe- rienced by mountain bikes all worked together was paramount in analysis, simulation, and design optimization and iteration. Thus, the focus of this project is to design a mountain bike capable of withstanding typical loading patterns with a high level of safety. Further, the team aimed to optimize a bike frame which used the minimal amount of material necessary to reduce weight and cost for the user. iii Acknowledgements The Car6on Senior Design Team would like to acknowledge the following for their guidance, sup- port, and feedback from the inception of the project to the finalized design: Robert Marks, Ph.D. Peter Woytowitz, Ph.D. Timothy Hight, Ph.D. The Arevo Engineering Team Santa Clara University Department of Mechanical Engineering iv Contents Abstract iii Acknowledgments iv List of Figures viii List of Tables viii Introduction 1 Review of Literature . .2 Systems-Level Chapter 7 Customer Needs . .7 System Sketch and User Scenarios . .8 Functional Analysis . .8 Functional Decomposition . .8 Inputs and Outputs . .9 Similar Products on the Market . 10 System-Level Issues . 20 System-Level Design . 21 Team and Project Management . 22 Subsystem Chapters 27 Top level system justification . 28 Main Frame . 29 Physical Frame . 29 Electronics . 31 Rear Frame . 31 The Actual Frame . 32 Rear Suspension Design . 33 Rear Suspension Design . 34 FEA Analysis of final frame design . 35 Static Loading Simulation and Analysis . 36 Vibration Mode Analysis . 39 System Integration, Tests, and Results 42 Costing Analysis 45 Business Plan 46 Executive Summary . 46 Introduction . 46 Goals and Objectives . 46 Product Description . 46 v Potential Markets . 47 Manufacturing Plans . 47 Product Cost and Price . 48 Service and Warranties . 48 Financial Plan and ROI . 49 Engineering Standards and Realistic Constraints 50 Manufacturability . 50 Health & Safety . 51 Social . 53 Environmental Impact and Sustainability . 54 Economic . 55 Summary and Conclusions 56 Bibliography . 58 Appendices 60 Appendix A: Decision Matrices . 60 Appendix B: Sketches . 64 Appendix C: Budget . 66 Appendix D: Timeline . 67 Appendix E: Environmental Impact Report . 68 Appendix F: PDSO . 75 Appendix G: Safety Review . 80 Appendix H: Fatigue Data Report . 83 vi List of Figures 1 Stress Tensor Illustration . .2 2 System Sketch . .8 3 Example of Bladder Molding Technique . 12 4 Initial printed layer . 13 5 Secondary printed features . 13 6 Final build layer . 13 7 Example profile sketch with spline control vertices . 14 8 Cross section view of initial design . 15 9 First frame design . 15 10 Second major design iteration . 16 11 Cross section of second major design iteration . 17 12 Motor drive system purchased from Bafang . 17 13 Motor-frame interface design . 18 14 Isometric view of final frame design . 19 15 Cross sectional view of final frame design . 19 16 System Connectivity Chart . 21 17 Final design model with labeled subsections . 27 18 Two early conceptual CAD designs, comparing a hard-tail frame with a full-suspension frame. 29 19 Real examples of two of the different conceptual design options for the seat tube on the main-frame (images printed without permission from media.4rgos.it and icanbikes.com). 30 20 Real examples of two of the different conceptual design options for the rear sub- frame (images printed without permission from trek.scene7.com and cdn.road.cc). 32 21 FEA comparison of final sub-frame design options . 33 22 Rear suspension design. 35 23 Finite element simulation frame loading scenarios . 36 24 Finite element simulation of a 2500 lb load applied exclusively the seat of the bike frame with a von Mises stress contour plot on the model. The maximum vM stress is 235 MPa. 38 25 Finite element simulation of a 2500 lb load applied exclusively the pedals of the bike frame with a von Mises stress contour plot on the model. The maximum vM stress is 101 MPa. 39 26 Hand calculation to find the frequency of a rotating 28” bicycle wheel while rid- ing at 50 mph. This frequency is the main concern when considering bike frame vibration modes. 40 27 Finite element simulation of the bike frame, used to find the first mode of vibration. The mode is at 61 Hz. 41 28 Specimen #1, Force and Stiffness vs. Number of Cycles. 43 29 Specimen #2, Stiffness vs. Number of Cycles. 43 30 Specimen #3, Stiffness vs. Number of Cycles. 44 31 Skeleton Frame, printed at Arevo. 50 32 Hand Wrapped Frame and Rear Stays. 51 vii 33 CAD Illustration of Shock Pivot Cup Part. 53 34 Weighted criteria used to choose between the trade-offs shown in the following decision matrices. 60 35 Decision matrix, used to score and help choose the suspension system for the bike. 61 36 Decision matrix, used to score and help choose the design of the main-frame of the bike........................................... 62 37 Decision matrix, used to score and help choose the design of the sub-frame of the bike........................................... 63 38 Initial sketches used to make basic conceptual decisions about the design of the frame. ..
Details
-
File Typepdf
-
Upload Time-
-
Content LanguagesEnglish
-
Upload UserAnonymous/Not logged-in
-
File Pages104 Page
-
File Size-