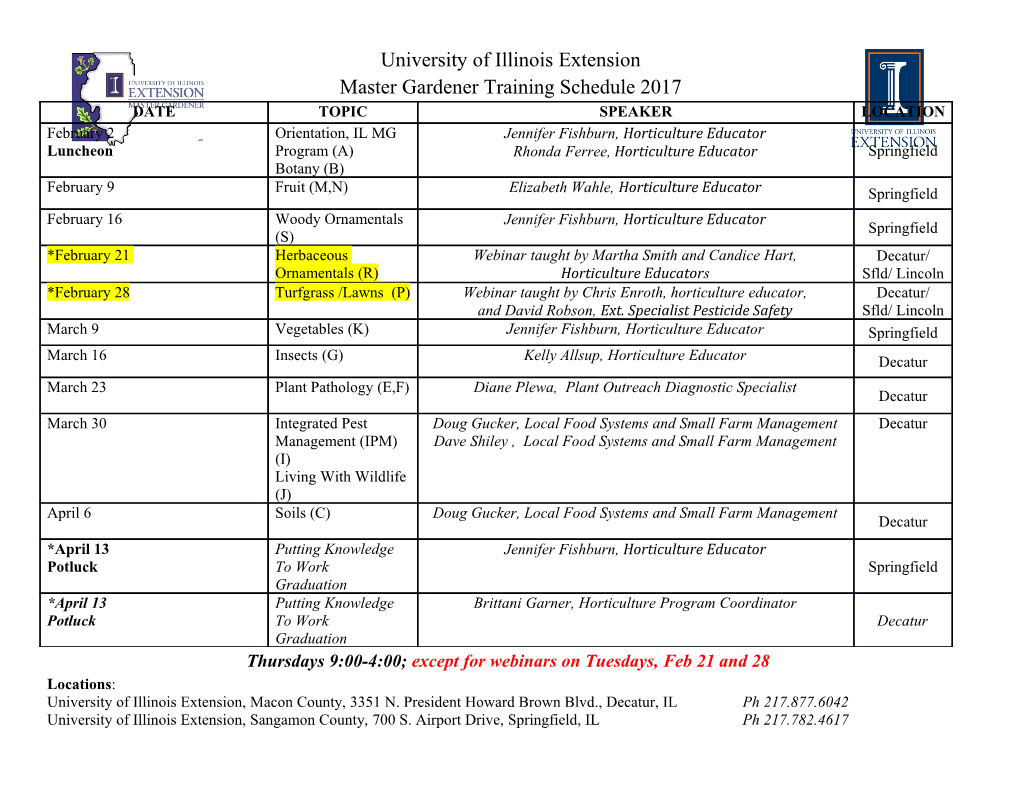
V-22 Osprey Aerodynamic Development - A Progress Review Michael A. McVeigh John Liu StephenJ. O'Toole Boeing Defense & Space Group, Helicopters Division and Steven Woods U.S. Navy Summary jmmmmmmmmmmmmm~mmmm Concapt Formufa!lon Events in the aerodynamic development of the multi- p, ehm· service V-22 Osprey tiltrotor are reviewed, with em- •nary I~'f M~;=~ " ltage I 1 D phasis on recent flight test findings and the solutions "'"l t I,... .. S~go ~ 11 developed. A discussion of the performance in the Full-Scale . f Ooslgn and Fabrication USMC, Navy, and SOCOM missions is presented. Development l r Flrst ~llgh! I Test and Evaluation {, EMD' Contract' ' Mod!fy and Test 2 FSD Introduction EnginLL Alrcralt and . First Flight . , ' ... The V-22 Osprey (Figure 1) is a multi-service, multi­ rcri~t~:y:g Low Aato Initial F iZ::iL:i Plodultlon ~.!lT_ ::z mission tiltrotor aircraft that incorporates advanced 1 AAC CA technology to achieve a variety of military tasks. The aircraft combines the hover capabilities of a helicopter Figure 2. V-22 Program Schedule with the high-speed, high-altitude performance of a fixed-wing airplane. In 1983, the V-22 design emerged on the FSD aircraft. Figure 3 shows the extent of envelope expansion achieved to date. Since the begin­ ning of the progran1, much has been learned concern­ ing the aerodynamics and perforn1ance of tiltrotors. During the initial design period, the broad dimen­ sions of the aircraft configuration were largely defined by the shipboard-compatibility requirement to fold 28,000 20,000 f--+-/-t---+--J~:'£'1~:,..-.,-1---l ;;:_ ill :2 16,000 J---,,LJ---J----J--e-r,;,f,< <( Figure 1. The Bell-Boeing V-22 Osprey -~ 12,000 1-fc_+--1-c--+C,.:;f.->~f:- a; Cl r·rom the concept forn1ulation stage (Figure 2) and entered the preliininary design stage of development Since then, development has grown thmugh the Full Scale Development (FSD) phase, wh;ch included '' flight test progrmn, to the Engineering Ivlanufacturin~: 50 100 150 200 250 300 350 Development (EMD) phase, wherein four produc True Airspeed (Knots) lion--representative aircraft are being built and High: !cslcd. Ovt~r llOO flight hours have been accun1Ldalcd Figure 3. \f.·.?.2 Dcsi,l{ll and Fhght 'Test Envelope and stow on LHA-class ships, and by the requirement the Boeing Transonic Wind Tunnel (BTWT). When the to load and carry internally an F-404 engine. These FSD configuration was essentially finalized, it was requirements are illustrated in Figure 4, which shows tested up to M~0.72 in the 16-foot transonic tunnel at the clearances required and how these defined the Arnold Engineering Development Center (AEDC), rotor diameter, wing span, and rear fuselage upsweep. Tullahoma, Tennessee. Thus, no aerodynamic considerations were involved The initial low-speed wind tunnel tests concentrated in establishing the most important dimensions of this on the development of wing/ fuselage shape, overwing rotary wing V/STOL aircraft. However, having set fairing lines, rear fuselage upsweep, and tail configu­ these dimensions without reference to aerodynamics, ration. The configuration decisions as to wing sweep, the best efficiency then had to be obtained within these thickness-to-chord ratio, dihedral, and tail configura­ constraints. This was largely achieved by selection of tion are documented in detail in Reference 1. wing and rotor airfoils, blade twist, rotor solidity, and wing chord. The results of final tests to determine the full-scale, trimmed, unpowered, low-speed drag polar are shown in Figure 5. The polar was obtained from the unpowered model with vortex generators on the wing leading edge to simulate full-scale Reynolds number effects on CLmax· The data is corrected for the effects of tunnel buoyancy, tunnel walls, and the drag of the flow-through nacelles. Figure 6 shows the variation of the Oswald induced efficiency factor, e, with lift coef­ ficient. For this wing of aspect ratio 5.5, over the normal operating range of lift, e ~ 0.82. This value reflects the favorable end-plating effect of the large nacelles. 1.5 Gi a: __j () ~ Operating __j 1.0 CL ~ cQ) ·c:; ;;= 0.5 Q) 0 () 5 Ft (1.52 M) t::=::=======:;~7~~=r~~ ~ -+Deck Edge __j 0 Clearance 0 0.5 1.0 1.5 2.0 Drag Coefficient (Co I Co ) Figure 4. V-22 Osprey Dimensions Are Defined By Ref. Shipboard Compatibility Requirements Figure 5. V-22 Trimmed Drag Polar Airframe configuration definition, performance de­ velopment, and rotor performance validation pro­ ,., 1.0 gressed in parallel, with the Navy emphasizing vali­ (.) c dation by testing. This philosophy necessitated an Q) 0.8 ·c:; extensive program of wind tunnel testing and tests of ;;= - a large-scale rotor. This was followed by flight testing w 0.6 OJ of aircraft No.1 through No.4 to provide interim data c Operatingt on the FSD configuration, while the modifications to ~ 0.4 - CL "0 arrive at the EMD configuration were being designed (ij and incorporated in aircraft 7 through 10. 0.2 - 0""' 0 ' ' Airframe Development 0 0.5 1.0 1.5 Wine! Tunnel Testing Lift Coefficient (CL I CL Ref) A series of low-speed wind tunnel tests on the emerg­ Figure 6. V-22 Airplane Mode Wing Efficiency ing configuration were conducted from 1983 through 1986. Most took place in the 20 feet x 20 feet Boeing Helicopters' large subsonic V/STOL wind tunnel As discussed in Reference 2, the presence of the large (BVWT). A number of low-speed configuration de­ proprotors produces changes in the airframe drag. velopment tests on powered and unpowered models Up-inboard rotation of the rotors induces a forward were conductect and a high-speed test was made in inclination of the local lift vectors whose components 34.2 in the free-stream direction act to reduce drag. Based ness improvement increased CLmax by 9% and that on tests on a powered model, Figure 7 presents the the addition of VGs raised maximum lift by a further variation of this drag reduction with lift coefficient for 29%, bringing the results close to the wind tunnel two typical values of thrust coefficient. levels. The wing VGs, which were installed at 10% chord, are now part of the configuration. Figure 9 Lift Coefficient (CL) presents the effect on drag, where it is seen that the 0 0.2 0.4 0.6 0.8 1.0 clean-up lowered the drag by about 6 percent at CLf CLRef = 0.65 and by 15% at CLfCLRef = 0.85. ,.._ Fairing TMrough Test Data ·0.2 "',._}I Analysis (Ref. 2) 1.2 ..----------....,.,----. '-o-~ Q5 1.1 Baseline + Cleanup + 0 ·0.4 '-o a: Wing Vortex Generators ......., _J /:::,. (.) 1.0 ~ ~ = 0.35 ~ \ "' ·0.6 ~ cT = o.oo2o _J ~ Flaps Up 1( 0.. 0.9 Baseline 0 s +Cleanup ,£; c ·0.8 Q) \ c Analysis (Ref~) ~". '(3 0.8 0 Baseline it= u Q) ::> 0.7 "0 ·1.0 0 Q) 70 (.) cc Fairing Through Test Data CT = 0.0036 ::J 0.6 -1.2L------------~~ "" --11-- S% 0.5 '---'--'---'--'---'--'---'----' Figure 7. Effects of Up-Inboard Rotor Rotation 0.3 0.4 0.5 0.6 0.7 0.8 0.9 1.0 1.1 On Reduction of Aircraft Drag Drag Coefficient (Co I c0 Ref) Flight Test Drag Cleanup Figure 9. Improvement in Drag Due and Drag Reduction Program to Aerodynamic Cleanup Early flight tests conducted on FSD aircraft No.1 re­ vealed that the drag was higher, and the maximum lift Drag Control Program less, than expected from the wind tunnel results. De­ tailed inspection of the aircraft showed that there was In order to ensure that there will be minimal excres­ room for improvementin the quality of surface smooth­ cence drag on the EMD aircraft, a drag control pro­ ness, gaps, and steps. The aircraft was therefore gram was instituted. An aerodynamic smootlmess subjected to an intensive clean-up program of filling criteria document was issued defining the guidelines and fairing, the addition of louvers to exhaust exit for surface fit-and-finish. All engineering design work holes, and the application of vortex generators (VGs) that affected the wetted surface of the aircraft was to the wing and overwing fairing. Flight test data reviewed to ensure compliance with the smoothness (References 3 and 4) showed that the effort was suc­ guidelines. To further ensure compliance, the aircraft cessful and that the lift and drag were more closely in was inspected regularly as they were being built. agreement with the wind tunnel results. Figure 8 Inevitably, during manufacture, changes that might presents the lift curve showing that the surface smooth- irtcrease drag were required and these were evaluated 1.8 r-------------, by the aero staff on a case-by-case basis. Figure 10 shows the minimum drag history since the end ofFSD, Q5 1.6 Baseline+ Cleanup+ Wind Tunnel a: Wing Vortex Generators Ol 1.0 _J ;/ ~ End of FSD 0 0 1.4 Baseline \ ..... Performance ~ + c Calculations _J +Cleanup 29% Q) 0.9 r­ 1.2 (ij at this Level S2. f t > c 9% '5 F-·------- ------r (]) 1.0 0.8 '(3 ~ it= t E (]) 0.8 ::> 0 0 § 0.7 1- ·1=' 0.6 :;:: ::J I "0 0.4 I .~ 0.6 First Flight 0 0.2 0.4 0.6 0.8 1.0 1.2 1.4 1.6 1.8 2.0 C(i December 1996 Angle of Attack (a/ a Ref) § 0.5 ''I'' s z 1992 1993 1994 1995 1996 1997 Figure 8. Improvement in Lift Due to Aerodynamic Cleanup Figare 10. V-22 Drag Reductio11 Program 34.3 when the minimum pre-cleanup drag level of aircraft because of rotor downwash being recirculated back No.
Details
-
File Typepdf
-
Upload Time-
-
Content LanguagesEnglish
-
Upload UserAnonymous/Not logged-in
-
File Pages14 Page
-
File Size-