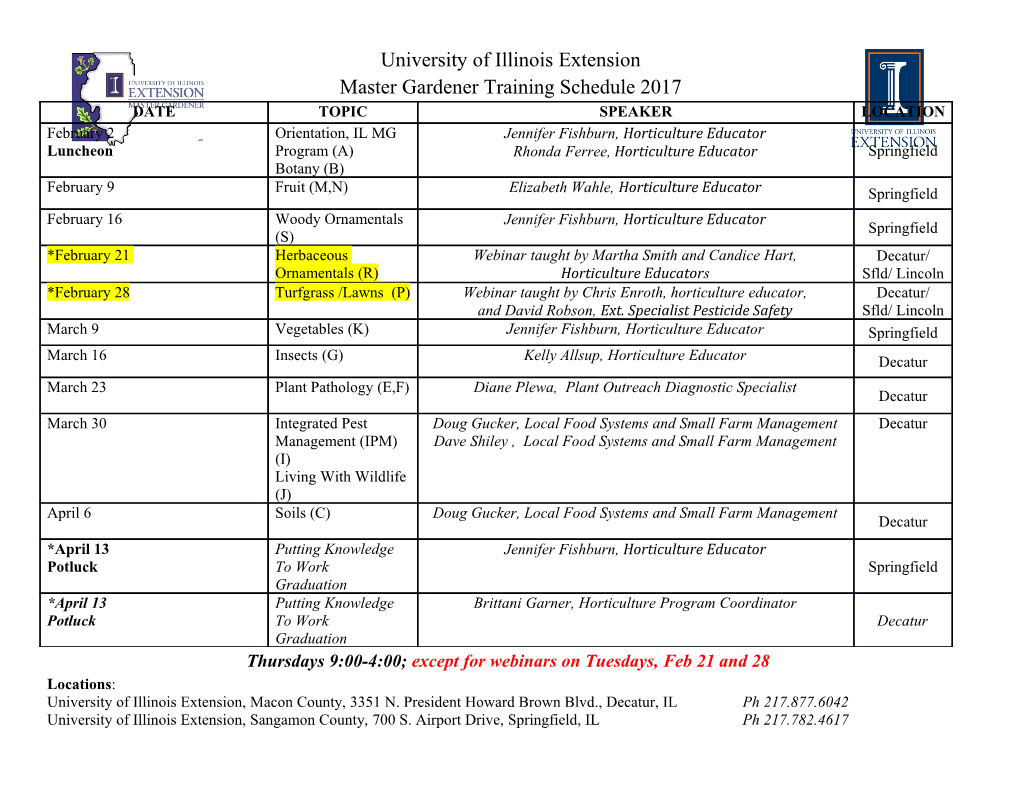
POWERTRAIN SIZING AND ENERGY USAGE ADAPTATION STRATEGY FOR PLUG-IN HYBRID ELECTRIC VEHICLES A Thesis Presented to The Graduate Faculty of The University of Akron In Partial Fulfillment of the Requirements for the Degree Master of Science Soumendu Chanda May, 2008 POWERTRAIN SIZING AND ENERGY USAGE ADAPTATION STRATEGY FOR PLUG-IN HYBRID ELECTRIC VEHICLES Soumendu Chanda Thesis Approved: Accepted: ____________________________ ____________________________ Advisor Department Chair Dr. Iqbal Husain Dr. Jose A. De Abreu Garcia ____________________________ ____________________________ Committee Member Dean of the College Dr. Robert J. Veillette Dr. George K. Haritos ____________________________ ____________________________ Committee Member Dean of the Graduate School Dr. Malik Elbuluk Dr. George R. Newkome ____________________________ Date ii ABSTRACT An energy usage adaptation (EUA) strategy to manage the charge/discharge profile of the energy storage system for plug-in hybrid vehicles is presented in this thesis. The objective of the EUA strategy is to bring the stored energy to a low level at the end of the daily drive cycle, and to limit the number of deep discharge cycles. The EUA algorithm first predicts the energy usage for a given day based on historical usage data. The predicted energy is then compared with the actual energy used and the battery energy available to set the SOC limits in the energy management algorithm. The EUA strategy has been tuned and tested using simulations of both a series and a series-parallel plug-in hybrid vehicle (model) with vehicle control algorithms developed for the purpose. The strategy is shown to improve the fuel economy of the vehicle and to reduce the cost per mile of operation by efficiently using the off board supplied energy. It also helps to extend the life of the battery by limiting the number of deep discharge cycles to no more than one per day. A well-to-wheel analysis of the designed plug-in hybrid is also done using the standard GREET model and through vehicle simulation to investigate the overall efficiency of plug-in hybrid vehicles. The well-to-wheel efficiency of the plug-in hybrids is found to be lower than those of the conventional gasoline and electric vehicles. iii DEDICATION Dedicated to my family and teachers iv ACKNOWLEDGEMENTS I wish to express my deep sense of gratitude and indebtedness to my academic advisor, Dr. Iqbal Husain for his great efforts and lot of enlightening ideas during the course of this research. I also wish to thank Dr. Robert J. Veillette, for his constant support and advice during the course of my research activities. I also wish to express my sincere appreciation to Dr. Malik Elbuluk for being in my advisory committee and for his support in making this research a success. I would like to thank my colleague Gregory Pasquesoone for his help in modeling the vehicle. I also wish to thank Gokhan Sen and Kwadwo Safo who were always there when I needed them. I am thankful to Nayeem for his quick and sharp comments which always had a touch of experience behind them. Finally, I would wish to thank my parents, my brother and sister for their love and encouragement over the years. v TABLE OF CONTENTS Page LIST OF TABLES ix LIST OF FIGURES xi CHAPTER I. INTRODUCTION 1 1.1 History of Grid-Connected Vehicles 3 1.2 Plug-In Hybrid Architectures 5 1.3 Motivation for Research 6 1.4 Overview of Research 7 II. PLUG-IN HYBRID ELECTRIC VEHICLES 9 2.1 Hybrid Vehicle Configurations 9 2.2 PHEV Ratings 11 2.3 Advantages and Disadvantages 11 2.4 Well-to-Wheel Efficiency 14 2.5 PHEV Operating Strategy 17 2.6 PHEV Vehicle Components 18 2.6.1 Energy Storage System: Battery 18 2.6.2 Electric Traction Motor 22 vi 2.6.3 Electronic Circuitry: Power Converters 23 2.6.4 Internal Combustion Engine 24 2.6.5 Generator 24 2.7 Market Status 25 2.8 Intelligent Energy Management 27 2.9 Conclusions 30 III. SERIES PHEV COMPONENT SIZING AND VEHICLE CONTROL 31 3.1 Sizing of Components 32 3.1.1 Traction Motor Power 33 3.1.2 Engine and Generator Power 36 3.1.3 Battery Sizing 37 3.2 Control Strategy 39 3.3 Drive Cycle Simulation 42 3.4 Conclusion 45 IV. SERIES – PARALLEL PHEV COMPONENT SIZING AND VEHICLE CONTROL 47 4.1 Sizing of Components 48 4.1.1 Traction Motor Power 51 4.1.2 Generator Power 52 4.1.3 Battery Sizing 53 4.2 Control Strategy 55 4.3 Drive Cycle Simulation 60 4.4 Conclusion 65 V. PHEV ENERGY USAGE ADAPTATION 66 vii 5.1 Energy Usage Adaptation 68 5.1.1 Prediction Algorithm 69 5.1.2 Energy Management Algorithm 87 5.2 Results from Energy Usage Adaptation Strategy 91 5.3 Conclusions 102 VI. ANALYSIS OF ENERGY ADAPTATION 104 6.1 Fuel Economy and Cost Per Mile 104 6.2 Results: Customer Perspective 106 6.3 Result: Ecological Perspective 120 6.4 Summary of Results 124 VII. CONCLUSIONS AND FUTURE WORK 125 7.1 Summary and Conclusions 125 7.1.1 Plug-in HEV Designs 126 7.1.2 Energy Usage Adaptation 127 7.1.3 Well-to-Wheel Efficiency 129 7.2 Contributions of Research 129 7.3 Future Works 129 REFERENCES 131 APPENDICES 134 APPENDIX A. SERIES PHEV MODEL 135 APPENDIX B. SERIES-PARALLEL PHEV MODEL 140 APPENDIX C. PREDICTION ALGORITHM CODE 146 APPENDIX D. ENERGY MANAGEMENT ALGORITHM 154 viii LIST OF TABLES Table Page 1.1 Proved oil reserves in 2006 [3] 2 2.1 Vehicle Technologies, Passenger Cars: Well-to-Pump Energy Consumption and Emissions 16 3.1 Series plug-in hybrid vehicle specifications 35 3.2 Series plug-in hybrid vehicle component data 39 4.1 Series-parallel plug-in hybrid vehicle specifications 49 4.2 Drive cycle data 53 4.3 Series plug-in hybrid vehicle component data 55 5.1 Main memory data for moving average based prediction 84 5.2 Main and Exception memory data for exception algorithm 85 5.3 Actual energy and predicted energy from Day 12 to Day 22 85 5.4 Initial input data for last eleven days 92 5.5 Input data for the next eleven days 92 6.1 Simulation results for series plug-in HEV with adaptation and no-adaptation technique 111 6.2 Simulation results for series-parallel plug-in HEV with adaptation and no-adaptation technique 112 6.3 Fuel economy and Cost per mile for series-plug-in HEV 115 6.4 Fuel economy and Cost per mile for series-parallel plug-in HEV 118 6.5 Well-to-tank efficiency calculations for the series plug-in HEV 121 ix 6.6 Tank-to-wheel efficiency calculations for the series plug-in HEV 122 6.7 Fuel economy and cost per mile for series and series-parallel PHEV 124 x LIST OF FIGURES Figures Page 2.1 Incremental cost and annual petroleum consumption of plug-in hybrids [2] 13 2.2 Processes involved in well-to-wheel efficiency calculation 14 2.3 Battery life cycles for different depth of discharge 22 2.4 Block diagram of a motor drive system 23 2.5 Block diagram of the intelligent energy management architecture (IEMA) [7] 28 2.6 Intelligent controller based on future vehicle states 29 3.1 Block diagram of a series plug-in hybrid vehicle configuration 31 3.2 Tractive force, power and velocity profile of the series plug-in hybrid vehicle 35 3.3 Traction power requirement at different gradient and vehicle speed 37 3.4 Battery energy consumed for 0-60 mph acceleration demand 38 3.5 Block diagram of communication network of vehicle controller 41 3.6 SOC control strategy 41 3.7 Velocity profile of the series plug-in hybrid vehicle in the acceleration cycle 42 3.8 Electric motor output power for maximum (sustained) acceleration 43 3.9 Steady speed drive cycle for series mode testing 44 xi 3.10 Battery state of charge during series-mode operation 44 3.11 Component power outputs during series mode operation 45 4.1 Block diagram of the series-parallel plug-in hybrid vehicle configuration 47 4.2 Tractive force, power and velocity profile for the series-parallel plug-in hybrid vehicle 50 4.3 Traction power requirement at different gradient and vehicle speed 51 4.4 Acceleration test results with 42-kW engine and different motor ratings 52 4.5 Electrical energy consumed during acceleration 54 4.6 SOC control strategy 56 4.7 Flowchart diagram for mode selection strategy 58 4.8 Acceleration pedal response for acceleration test 58 4.9 Velocity profile of the series-parallel plug-in hybrid vehicle in the acceleration cycle 60 4.10 Motor and engine power during acceleration 61 4.11 Steady-speed drive cycle for series mode testing 61 4.12 Battery state of charge during series-mode operation 62 4.13 Component power outputs during series mode operation 62 4.14 Velocity profile for the multi-mode test 64 4.15 Subcomponent output power for the multi-mode test 64 5.1 State of charge profile in the HWFET cycle 67 5.2 State of charge profile in HWFET_2 cycles 68 5.3 Flowchart diagram for moving average based prediction algorithm 73 5.4 Flowchart diagram for exception based prediction algorithm 77 xii 5.5 HWFET cycles with variation 79 5.6 UDDS cycles with variation 79 5.7 Actual and predicted energy usage graph for eleven days using prediction algorithm based on moving average, Test 1 80 5.8 Actual and predicted energy usage graph for eleven days using prediction algorithm based on exception, Test 1 80 5.9 Actual and predicted energy usage graph for eleven days using prediction algorithm based on moving average, Test 2 83 5.10 Actual and predicted energy usage graph for eleven days using prediction algorithm based on exception, Test 2 83 5.11 Actual and predicted energy usage graph for eleven days using prediction algorithm based on moving average, Test 3 84 5.12 Actual and predicted energy usage graph for eleven days using prediction algorithm based on exception, Test 3 84 5.13 Flowchart for the
Details
-
File Typepdf
-
Upload Time-
-
Content LanguagesEnglish
-
Upload UserAnonymous/Not logged-in
-
File Pages170 Page
-
File Size-