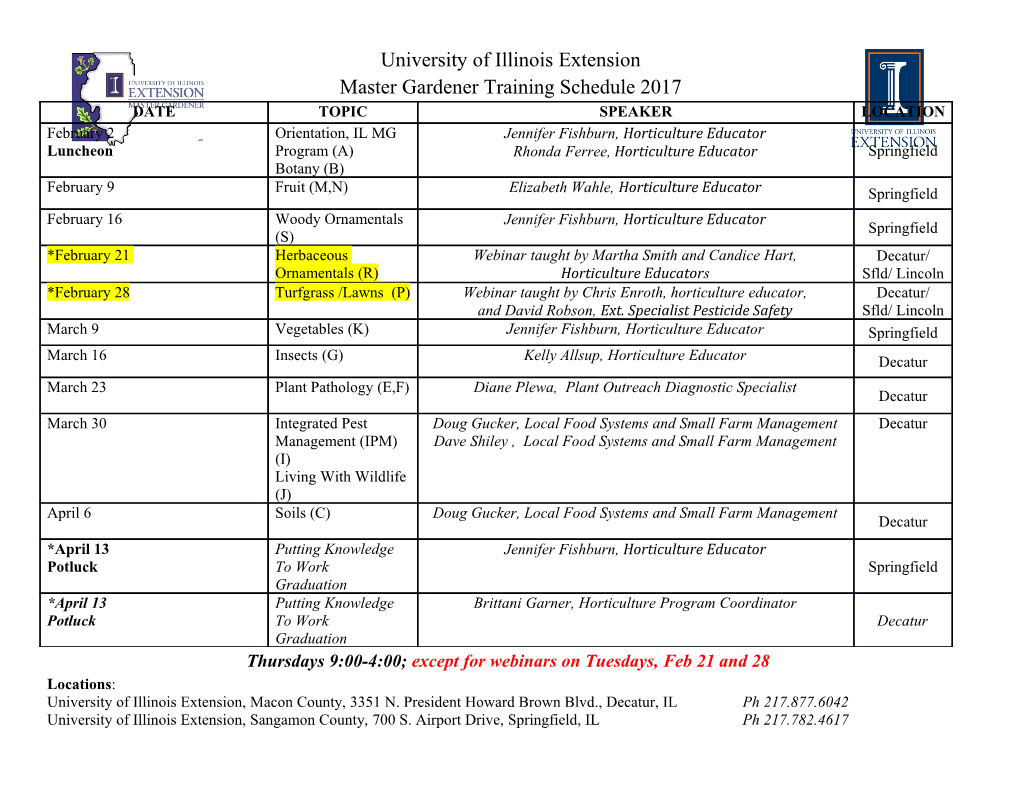
P2C2 Design of a Mechanism for Testing Dynamics of a Rotating Shaft with a Moving Support Sponsored by Dr. Hagay Bamberger and the University of Michigan Engineering Research Center for Reconfigurable Manufacturing Systems Matthew Carpenter, Design Engineer, P2C2 Alexander Cicerone, Design Engineer, P2C2 Lisa Perez, Design Engineer, P2C2 Jessica Port, Design Engineer, P2C2 December 15, 2009 Date: December 15, 2009 To: Dr. Hagay Bamberger, Post‐Doctorate, University of Michigan Cc: Dr. Yoram Koren, Professor, University of Michigan From: Matthew Carpenter, Design Engineer, P2C2 Alexander Cicerone, Design Engineer, P2C2 Lisa Perez, Design Engineer, P2C2 Jessica Port, Design Engineer, P2C2 Subject: Design of a Mechanism for Testing Dynamics of a Rotating Shaft with a Moving Support Abstract The goal of this project was to measure the dynamic response – namely, the displacement of a shaft from its static configuration – at the free end of an unbalanced shaft that was clamped and rotated by an existing machine. To accomplish this, the team designed and fabricated a system that was implemented in the vertical mill. This system allowed motion of a simple support along the shaft’s length while a sensor monitored the displacement from static configuration. Once the team completed this, they ran the system and generated an estimation of the displacements. 2 Executive Summary Dr. Hagay Bamberger of the Engineering Research Center for Reconfigurable Manufacturing Systems contracted P2C2 to design, fabricate, and operate a mechanism to measure the dynamics, specifically, the amplitude of vibration, at the free end of an unbalanced rotating shaft. This mechanism was to have a simple support that traverses along the length of the shaft. The customer requested that the design have the ability to do the following: (1) be structurally integrated with the mill or lathe of the team’s selection, (2) continuously collect data while the shaft support traverses along the shaft, and (3) accurately and precisely measure the shaft dynamics. Additionally, it was to be easily operable, maintainable, manufacturable, low‐cost, and completed no later than December 10, 2009. Upon analysis of the engineering specifications that the team established with the customer, P2C2 decomposed the design into four main functions: (1) rotate shaft, (2) support shaft, (3) traverse support, and (4) measure displacement. For the first function, the team narrowed down a shaft design and selected a particular mill based on the customer’s requests. For the next three functions, the team generated concepts and analyzed them, creating an alpha design that consisted of a direct‐driven platform and laser triangulation sensors. Taking material and safety into consideration, the team narrowed down specific components that they would use in their final design. They determined how the mechanical aspects of the design would be integrated through both CAD and full‐scale paper layouts in the Fadal mill. Similarly, they considered how the electrical and coding aspects of their design (based on the specifications of the sensors and the motor) would be integrated. P2C2 created detailed manufacturing, testing, and safety procedures on which they were to base any further work on the design. They procured their parts and performed their machining, assembly, and integration. Upon completion of these tasks, they began their validation of the components of the design and their operation of the design. Although the team was able to complete component validation, they only obtained a few sets of data from their design operation before the shaft hit resonance 1,500 RPM before its expected resonance point, creating large deflections in the shaft, and ultimately rendering the design unrecoverable. In reaction to this result, P2C2 broke down the failure step‐by‐step and determined the multiple improvement points necessary to further the project. The following report discusses the information presented above in greater detail. 3 Contents Abstract ........................................................................................................................................... 2 Executive Summary ......................................................................................................................... 3 Contents .......................................................................................................................................... 4 Problem Description ....................................................................................................................... 9 Background Information ................................................................................................................. 9 Dynamics of Rotating Shafts ....................................................................................................... 9 Prior Art ..................................................................................................................................... 10 Customer Requirements ............................................................................................................... 10 Engineering Specifications ............................................................................................................ 11 Functional Decomposition ............................................................................................................ 11 Shaft Selection .............................................................................................................................. 12 Machine .................................................................................................................................... 12 Material ..................................................................................................................................... 12 Dimensions ................................................................................................................................ 13 Concept Generation and Selection ............................................................................................... 18 Support Shaft ............................................................................................................................ 18 Self‐aligning ball bearing or spherical roller bearing ............................................................ 18 Ball bearing with no inner race ............................................................................................. 18 Externally mounted ball bearings ......................................................................................... 19 Polymer sleeve bearing ......................................................................................................... 19 Self‐aligning bearing and sleeve bearing .............................................................................. 20 Forces on bearing .................................................................................................................. 20 Concept selection .................................................................................................................. 22 Move Platform .......................................................................................................................... 23 Dual screw drive with stepper motor(s) ............................................................................... 23 Scissor lift with pneumatic actuators ................................................................................... 23 Platform off linear motor ...................................................................................................... 24 Four post structure with linear motor .................................................................................. 24 Concept selection .................................................................................................................. 25 Added Mass Options ................................................................................................................. 25 Threaded hole in shaft .......................................................................................................... 25 Threaded collar tightened to shaft ....................................................................................... 26 4 Nuts on end of shaft ............................................................................................................. 26 Concept selection .................................................................................................................. 27 Measure Displacement ............................................................................................................. 27 Laser triangulation ................................................................................................................ 28 Confocal ................................................................................................................................ 28 Thru‐beam ............................................................................................................................. 29 LVDT ...................................................................................................................................... 29 Concept selection .................................................................................................................. 30 Alpha Design ................................................................................................................................
Details
-
File Typepdf
-
Upload Time-
-
Content LanguagesEnglish
-
Upload UserAnonymous/Not logged-in
-
File Pages137 Page
-
File Size-