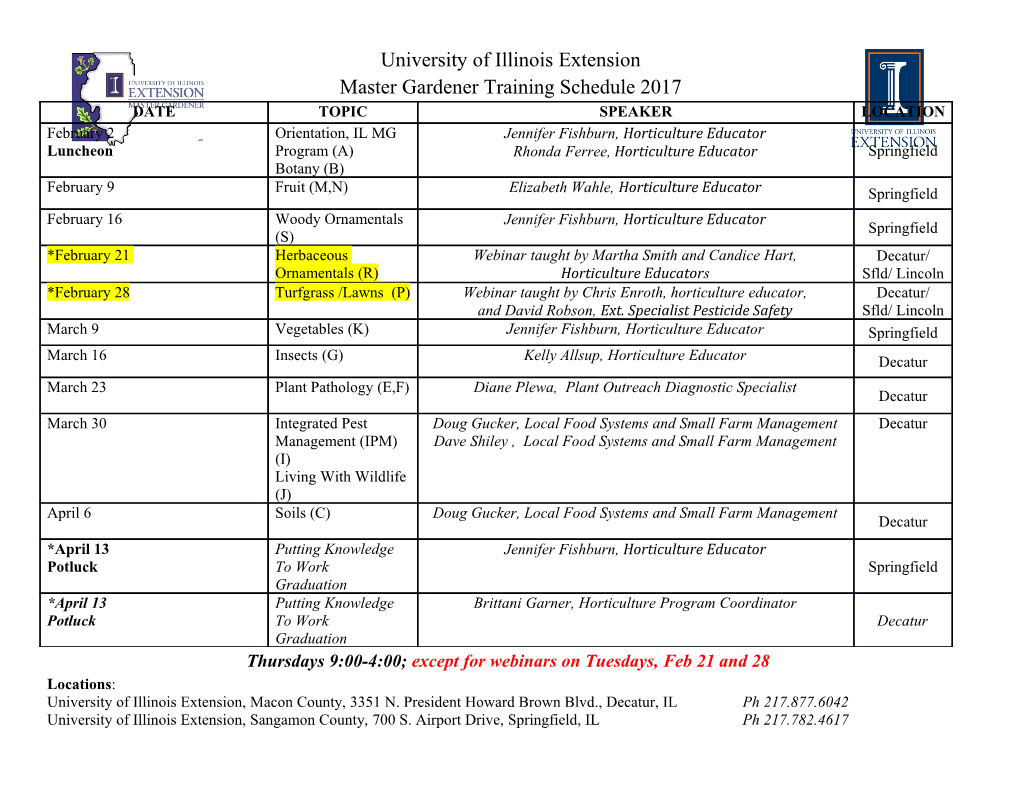
Trans. of the Society of Instrumentation and Control Engineers Vol.E-1, No.1, 230/237 (2001) Mass Measurement Using a Dynamic Vibration Absorber under Weightless Conditions Takeshi MIZUNO* and Kenji ARAKI** A new type of mass-measurement system under weightless conditions is proposed which uses a dynamic vibration absorber as a measuring device. In this system, an object to be measured is fixed to a rotating table (rotor) at a distance from the rotation axis. Since it makes the rotor unbalanced, a centrifugal force whose amplitude is proportional to the mass is generated during rotation. It works as a harmonic excitation and forces a structure supporting the table to vibrate. However, a dynamic vibration absorber attached to the structure is tuned or controlled to reduce the vibration to zero. When the structure does not move at all, the absorber mass vibrates in such a way that the product of the mass and the displacement amplitude is equal to the amount of unbalance, that is, the product of the mass to be measured and its distance from the rotation axis. Therefore, the mass of the object is determined by measuring the displacement amplitude of the absorber mass. In this study, the principles and features of the proposed mass-measurement system are clarified. Experiments are carried out with a developed apparatus having an active dynamic vibration absorber. This apparatus can perform measurement at various rotational speeds because the absorber’s natural frequency can be tuned by a feedback parameter. Experimental results demonstrate the feasibility of the proposed mass-measurement system. Keywords: mass measurement, weightless conditions, dynamic vibration absorber, centrifugal force, anti-resonance 1. Introduction (3) Measure the centrifugal force in rotating an object 3). The first method is sensitive to vibration transmitted from Various weightless or micro-gravity experiments have the surroundings; it takes longer time to measure in the been carried out on the Space Shuttle. A number of new presence of such vibration. The second method needs phenomena, which could not be observed on earth, have sophisticated mass-estimation algorithms including the been disclosed in the experiments. The production of new compensation of sensor dynamics; it does not seem clear materials and medicines in space is expected to start in the how to improve the accuracy of measurement. The third near future. Mass measurement under weightless method has a critical problem that centrifugal forces conditions will be necessary to perform such production. generated during measurement may cause vibration in the Conventional methods of mass measurement are surroundings; the distance of the center of gravity mass of classified into two types 1): an object from the rotation axis must be identified precisely. (1) Compare the weight force acting on an object of If the distance is unknown, two centrifugal forces must be unknown mass with those of reference weights, measured whereby the object is placed at two different (2) Measure the change in length of a spring that is distances 3). proportional to the weight force acting on an object. In this paper, a new type of mass-measurement system is Both of them cannot perform measurement in space proposed in which a dynamic vibration absorber works as a because they are based on gravitational acceleration on device for both mass-measurement and vibration control. earth. This method uses centrifugal force in principles so that the There are several methods proposed for mass distance from the rotation axis must be identified. However, measurement under weightless conditions: the vibratory force is cancelled by the absorber during (1) Measure the natural frequency of a spring-mass measurement so that there is no vibration transmitted to the system. surroundings. It is, therefore, suitable for measuring in (2) Apply the concept of the dynamic measurement vibration-sensitive environments such as space structures. method 2). The principles and features of the proposed mass- * Department of Mechanical Engineering, Saitama University, measurement system are clarified in this paper. An Shimo-Okubo 255, Saitama ** Emeritus Professor of Saitama University apparatus using an active dynamic vibration absorber with T. SICE Vol.E-1 No.1 2001 231 an electromagnetic servomechanism is developed. Several 1 m rω 2 X = ⋅ u ,(6) a 2 2 experiments carried out with the apparatus are reported. k ω ω k k p (1+ a − )(1− ) − a k ω 2 ω 2 k 2. Principles and Characteristics of Measurement p p a p where 2.1 Using an Undamped Dynamic Vibration Absorber k p A basic model of the proposed mass-measuring system ω p = ,(7) m p that uses an undamped dynamic vibration absorber is shown in Fig.1. An object to be measured mu is fixed to a ka ωa = .(8) turning table at a distance r from the axis of rotation. The ma frame supporting the table is mounted to the base through When the rotational frequency ω is equal to the absorber's spring k p . A dynamic vibration absorber consisting of an natural frequency ωa , it is derived from (5) that absorber mass ma and spring ka is attached to the frame. When the table is rotating at a velocity ω, the equations of X p = 0 ,(9) motion are derived as follows. so that the steady-state vibration of the frame becomes zero. m p &x&p (t) = −k p x p (t) − ka (x p (t) − xa (t)) , From (6), the absorber mass vibrates to satisfy + m rω 2 cosωt ,(1) u mu r X a = − . (10) ma ma &x&a (t) = −ka (xa (t) − x p (t)) ,(2) From (10), we get where m p is the total mass suspended by the spring. To obtain the stationary solutions, we represent the ma X a mu = .(11) variables in such a form: r x p (t) = X p cosωt ,(3)Therefore, the mass of the object is given by dividing the product of the absorber mass ma and its displacement xa (t) = X a cosωt .(4) amplitude X a by the distance of the object from the From (1) to (4), we get rotation axis r . The principle of measurement is summarized as follows. ω 2 1− (1) Fix an object on the turning table at a predetermined ω 2 m rω 2 X = a ⋅ u ,(5) position. p 2 2 k ω ω k k p (1+ a − )(1− ) − a (2) Coincide the rotating speed of the table with the k 2 2 k p ω p ω a p absorber's natural frequency so as to stop the vibration of the frame. ω (3) Measure the displacement amplitude of the absorber Sample mass. r 2.2 Using an Active Dynamic Vibration Absorber m u As explained in the previous section, the absorber’s natural frequency must equal the rotational frequency when an undamped dynamic vibration absorber is used. One Turning table method of achieving it is to use an active dynamic m p m a vibration absorber and adjust its natural frequency by changing the feedback gain. When an active dynamic k ka p vibration absorber is used, however, the principle of measurement can be more generalized. It will be explained Frame xa in the following. Figure 2 shows a basic model when an active dynamic xp vibration absorber is used. The spring k p in the passive Fig.1 Mass measurement system with an undamped absorber is replaced by an actuator. Electromagnet, linear dynamic vibration absorber motor and piezoelectric device are available as an actuator. T. SICE Vol.E-1 No.1 2001 232 To make general formulation, the actuator is modeled as a previous section. In the second and third methods, the device generating force F(t) . Then the equations of control input is constructed to cancel the centrifugal force. motion are: The second methods are subdivided into two methods: 2 (2-1) Build a disturbance observer and cancel the effects m p &x&p (t) = −k p x p (t) − F(t) + mu rω cosωt , (12) of the disturbance asymptotically using the estimated 4), 5) ma &x&a (t) = F(t) . (13) signals . (2-2) Insert a model of disturbance into the feedback Assuming that the motion of the frame is regulated by loop 6). active control as According to the third method, the control input canceling x p (t) = 0 , (14) the periodical excitation is made iteratively by modifying the input based on the results during the last period 7)-9). we get When an active dynamic vibration absorber is used, 2 therefore, various active control methods are applicable to ma &x&a = mu rω cosωt , (15) eliminate the vibration of the frame. independently of the applied control method. Substituting 2.3 Measurement Using a Counter Weight (4) into (15) gives Equations (10) and (16) indicate that the motion of the mu r ma X a absorber mass becomes larger in proportion to the mass of X a = − ∴mu = . (16) ma r an object to be measured. When the vibration amplitude of the absorber mass becomes so large to exceed the operation Therefore, m is estimated according to the same equation u range of the spring or the actuator, measurement cannot be as an undamped dynamic vibration absorber is used. performed. Equation (12) indicates that the vibration of the When the stroke of the absorber mass is limited by a supporting structure must be eliminated during value of X amax , the measurement range is given by measurement. There are several control methods applicable for this purpose: ma X amax mu ≤ . (17) (1) Use the absorber as an undamped dynamic vibration r absorber. This range can be widened by decreasing r. However, it (2) Apply the theory of output regulation with internal causes measurement inaccuracy because measurement 4) - 6) stability .
Details
-
File Typepdf
-
Upload Time-
-
Content LanguagesEnglish
-
Upload UserAnonymous/Not logged-in
-
File Pages8 Page
-
File Size-