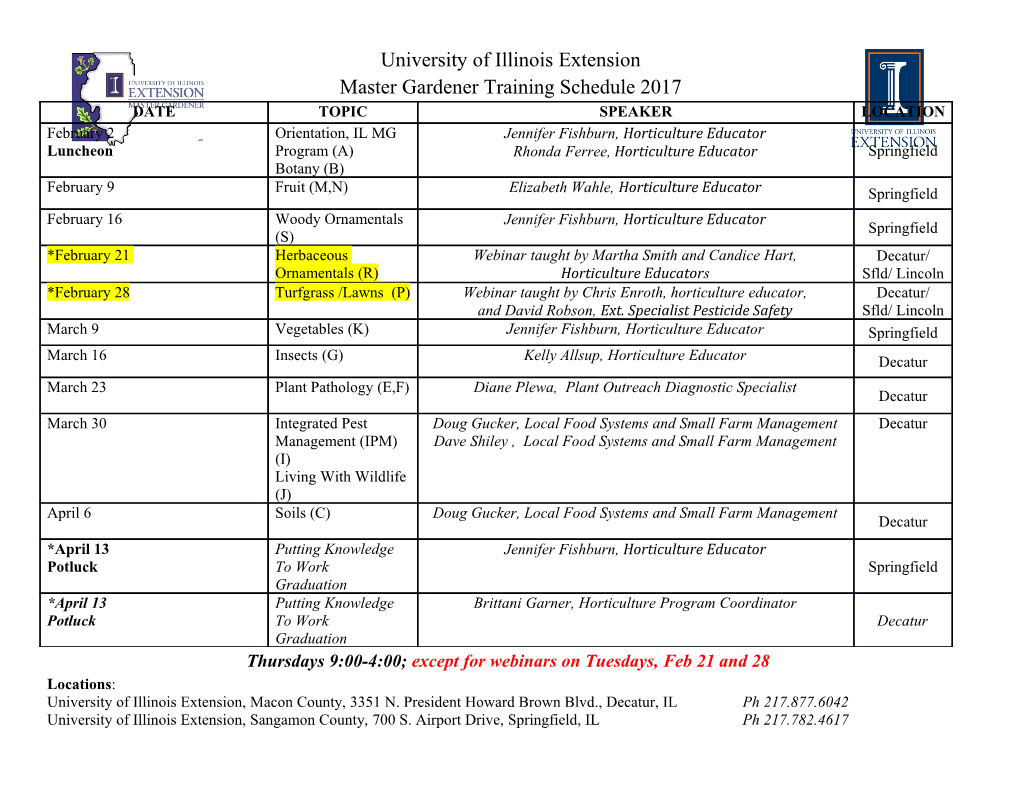
Optimisation of Defoamer in a Bio-Reactor James Mangundu A research report submitted to the Faculty of Engineering and the Built Environment, Faculty of Engineering and the Built Environment, University of the Witwatersrand, Johannesburg, in partial fulfilment of the requirements for the degree of Master of Science in Engineering. Johannesburg 2017 Table of Contents ACKNOWLEDGEMENTS ............................................ i ABSTRACT ............................................................... ii LIST OF FIGURES ................................................... iii LIST OF TABLES ..................................................... iv SECTION 1 ............................................................. 1 INTRODUCTION ...................................................................................................... 1 1.1 Brief introduction to the use of activated sludge processes ................. 1 1.2 Problems of excessive foaming in activated sludge processes ............. 3 1.3 Methods of foam control in activated sludge processes ........................ 4 1.4 Aim ........................................................................................................... 6 1.5 Objectives ................................................................................................ 6 1.6 Report layout ........................................................................................... 6 SECTION 2 ............................................................. 8 LITERATURE REVIEW: ACTIVATED-SLUDGE SYSTEM OPERATION, CHALLENGES AND SOLUTIONS........................................................................... 8 2.1 Historical development of the activated-sludge process ....................... 8 2.2 Description of the activated-sludge process .......................................... 8 2.3 Reactor configurations of the activated sludge processes ...................10 2.4 Key factors on design of activated sludge processes ...........................11 2.5 Process Control Parameters ...................................................................17 2.6 Operational problems of the activated sludge process.........................18 2.7 Excessive foaming problems in the activated sludge process ..............19 2.8 A review of foam control methods – Case studies ................................22 2.9 Overview of the history of studies of antifoams ...................................27 2.10 A review on different antifoam types and how they work ...................29 2.11 Deactivation of mixed solid-oil compounds ..........................................32 2.12 Motivation of this study .........................................................................32 SECTION 3 ............................................................ 35 SITE DESCRIPTION .............................................................................................. 35 3.1 Description of the bio-plant ...................................................................35 3.2 Description of foam control on site .......................................................38 SECTION 4 ............................................................ 42 MATERIALS AND METHODS ............................................................................... 42 4.1 Batch Experiments .................................................................................42 4.2 Plant Trials ..............................................................................................49 SECTION 5 ............................................................ 55 RESULTS AND DISCUSSION ............................................................................... 55 5.1 Batch laboratory experiment results .....................................................55 5.2 Plant trial results ....................................................................................61 5.3 Economic Evaluation of plant trial results .............................................65 5.4 Discussion of batch experiment results ................................................66 5.5 Discussion of plant trial results .............................................................68 SECTION 6 ............................................................ 70 CONCLUSION AND RECOMMENDATIONS ......................................................... 70 REFERENCES ......................................................... 72 APPENDIX A ......................................................... 76 APPENDIX A2........................................................ 79 APPENDIX B .......................................................... 84 APPENDIX C .......................................................... 85 APPENDIX D ......................................................... 86 APPENDIX E .......................................................... 88 ACKNOWLEDGEMENTS Zetachem (Pty) Ltd is acknowledged for providing the reagents, samples and equipment used for the purpose of this study and for authorizing this work to be done. Further acknowledgement is extended to the Management of the “host” company for granting permission for plant trials on their site. The following people are also acknowledged for their contribution to the successful completion of this study: my Supervisor, Doctor Kevin Harding, for his patience in giving valuable guidance in academic research protocols; Mr. Mohau B. Mofokeng for all the assistance he offered me, and my son Tatenda Mangundu for his understanding and co- operation when I had to spend long hours away from him studying and putting together this work. i ABSTRACT The success rate in the use of defoamers for controlling foam lies in finding the optimal concentration of defoamer for each foam type. Due to the dynamic nature of the foaming conditions in bio-reactors, using one concentration of defoamer across all foaming conditions may not be efficient. Where the plant design requires the use of defoamers for foam control, finding the right defoamer concentration ideal for each foam type becomes key. The objective of this study was to examine the following questions: first, can a more dilute form of Zeta Airspel 300® defoamer achieve complete foam knock-down and lengthy foam stay down times in the bio-reactor? And second, can this be achieved at a lesser cost than using 100% concentrated defoamer. To examine these questions, two sets of experiments were performed, batch experiments and plant trials, with defoamer concentrations ranging from 1%-100%. Defoamer samples with 40% concentration and above managed to completely reduce foam in both the batch experiment and in the bio-reactor. The rates of foam decay were faster with increase in defoamer concentration and foam suppression times were lengthier with increase in defoamer concentration. The economic evaluation of the plant trial results showed that 90% defoamer concentration was the least costly option of all. This discovery suggests that different defoamer concentrations can be used optimally depending on foaming conditions present in the bio-reactor at each given time. Future studies should focus on conducting longer plant trials during periods of different foaming conditions to be able to develop a model that predicts the most cost effective defoamer concentration for each particular foam type. ii LIST OF FIGURES FIGURE 2 1: SCHEMATIC REPRESENTATION OF A SUSPENDED GROWTH BIOLOGICAL TREATMENT PROCESS ADAPTED FROM (TCHOBANOGLOUS ET AL., 2003) ..................................................... 9 FIGURE 2 2: INFORMATION ON THE COD FRACTIONATION USED IN DETAILED DESIGN OF ACTIVATED-SLUDGE PROCESSES. MODIFIED FROM (TCHOBANOGLOUS ET AL., 2003) ............ 13 FIGURE 2 3: FRACTIONATION OF NITROGEN IN WASTEWATER USED IN DETAILED DESIGN OF NITRIFICATION AND DENITRIFICATION. MODIFIED FROM (TCHOBANOGLOUS ET AL., 2003) ... 15 FIGURE 3 1: SCHEMATIC DIAGRAM OF THE BIO-PLANT .................................................................. 36 FIGURE 3 2: LAYOUT OF THE DEFOAMER DOSING STATION ........................................................... 38 FIGURE 3.3: FOAM HEIGHT LEVEL PROBE IN THE BIO-BASIN: FOAM HEIGHT SCENARIO (ON SITE). 39 FIGURE 4.1: THE DYNAMIC FOAM RISE TEST EQUIPMENT FOR BATCH EXPERIMENTS ..................... 46 FIGURE 5 1: GRAPHS OF 0% AND 10% DEFOAMER CONCENTRATIONS DURING BATCH EXPERIMENTS ............................................................................................................................................... 56 FIGURE 5 2: GRAPHS SHOWING FOAM BEHAVIOR AFTER DOSING 20% AND 30% DEFOAMER CONCENTRATIONS DURING BATCH EXPERIMENTS ................................................................... 56 FIGURE 5 4: GRAPHS SHOWING FOAM BEHAVIOR AFTER DOSING DEFOAMER CONCENTRATIONS OF 80%, 90% AND 100% ............................................................................................................ 60 APPENDIX B 1: BATCH EXPERIMENT GRAPHS FOR 50% AND 60% DEFOAMER CONCENTRATION. .. 84 APPENDIX D 1: BIO-REACTOR DEFOAMER CONSUMPTION JUNE 2016 .......................................... 86 APPENDIX D 2: HISTORICAL SCADA DUMP: DEFOAMER DOSING PUMP OUTPUT VS FOAM HEIGHT IN A BIO-REACTOR ..................................................................................................................... 86 APPENDIX D 3: BIO-REACTOR DEFOAMER CONSUMPTION JUNE 2016 .......................................... 87 iii LIST OF TABLES TABLE 3 1: OPERATING PARAMETERS OF BIO-REACTOR ON SITE ................................................... 37 TABLE 4 1: BREAKDOWN OF MASS CONSTITUENTS
Details
-
File Typepdf
-
Upload Time-
-
Content LanguagesEnglish
-
Upload UserAnonymous/Not logged-in
-
File Pages97 Page
-
File Size-