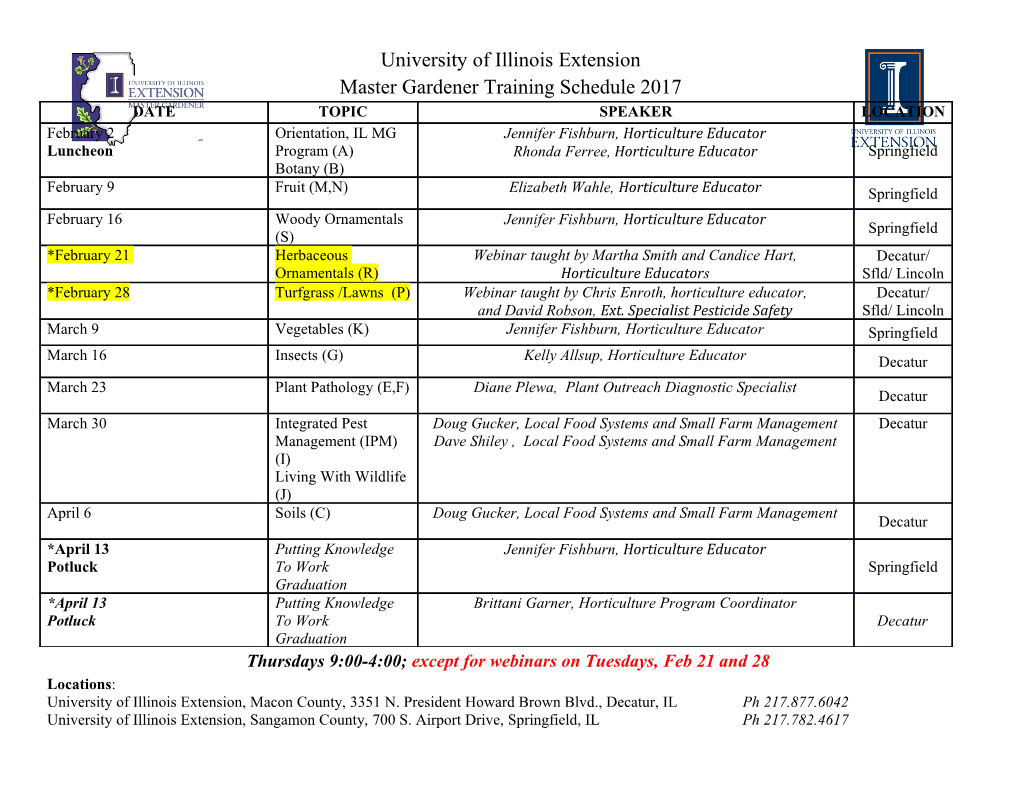
3. FRICTION LAWS SPRING 2009 3.1 Drag coefficients 3.2 Flat-plate boundary layer 3.3 Pipe flow 3.4 Frictional losses Examples 3.1 Drag Coefficients The local contributions to forces on a body can be quantified by the ratio of a stress (force per unit area) to the dynamic pressure : w w ( shear stress ) skin-friction coefficient c = (1) f 1 2 2 U 0 p p ( pressure /normal stress ) pressure coefficient c = (2) p 1 2 2 U 0 The reference velocity U0 is taken as: – the free-stream velocity ( Ue) for external boundary layers; – the average velocity ( Uav ) for internal flows (e.g. pipes or channels). The total streamwise force F on a body in a flow can be non-dimensionalised by dividing by (dynamic pressure × area ) as: F drag coefficient c = (3) D 1 2 2 U 0 A In general, this drag force has both pressure (“form drag”) and viscous parts, with the former dominating for separated flows (bluff bodies) and the latter for streamlined bodies. For bluff bodies (separated flow): ⌠ U • force is predominantly pressure drag , − p dA 0 ⌡ x A • A is the projected area • cD = O(1) For streamlined bodies (no flow separation): ⌠ U0 • force is predominantly viscous drag dA ⌡ wx A • A is the plan area • cD « 1 This course will focus almost exclusively on attached boundary layers and the viscous contribution to drag (but see the Examples for section 1 for estimation of the pressure drag on an object). Turbulent Boundary Layers 3 - 1 David Apsley dx b y δ x L For boundary layers, the frictional drag on a plate of span b and length L is L = ⌠ F w b dx ⌡0 F 1 ⌠ L c (L) = = c dx = average skin friction coefficient (4) D 1 2 f 2 U 0 (bL ) L ⌡0 Remember from Section 2 that boundary-layer velocity profiles are typically given in terms of the friction velocity uτ defined by 2 = w u (5) Substituting (5) in (1), the skin-friction coefficient and friction velocity are related by ¡ ¢ c = u 2 u = f c f (2 ) or (6) U 0 U 0 2 Many valuable friction laws can be derived from the observation that the logarithmic velocity profile (with Coles wake extension in the case of an external flow): U 1 u £ y 2 y = ln + B + f ( ) u £ is often a good approximation right across the shear layer. We use this in two ways: • for an external flow (flat-plate boundary layer): – apply the formula at the edge of the boundary layer – relate the free-stream velocity to wall friction; • for an internal flow (pipe or channel): – integrate across the duct – relate the average velocity to wall friction. Turbulent Boundary Layers 3 - 2 David Apsley 3.2 Flat-Plate Boundary Layer Reynolds numbers: U x U ≡ e ≡ e streamwise: Re x ; cross-stream: Re (7) Applying the velocity law at the edge of the boundary layer: U 1 u ¡ 2 e = ln + B + (8) u ¡ Noting that u ¢ c f = U e 2 and £ u U u £ c = e = f Re ¢ U e 2 equation (8) can be rewritten as 2 1 ¤ c f 2 = ln(Re ) + B + c f 2 With = 0.41, B = 5.0 and = 0.45 this gives 2 ¥ c = 44.2 ln(Re f ) + 20.7 (9) c f 2 This gives cf implicitly in terms of Re ¦ . A more convenient form is found by solving it for a few representative values of Re ¦ and fitting a power-law approximation (see the Examples). Rearranging (9) into a convenient form for iteration: 2 c = f 2 § + 44.2[ ln(Re c f )2/ 20.7 ] then solving iteratively gives 3 4 5 6 7 Re ¦ 10 10 10 10 10 cf 0.00682 0.00409 0.00270 0.00190 0.00141 A suitable power-law fit (see the figure below) is: − 6/1 = ¨ c f .0 0205 Re (10) Turbulent Boundary Layers 3 - 3 David Apsley Skin-Friction Coefficient 0.010 y = 0.0205x -0.1702 f c 0.001 1.0E+03 1.0E+04 1.0E+05 1.0E+06 1.0E+07 Re δδδ This is only useful if (x) and hence Re ¦ is known. We shall derive this by an integral analysis in Section 4. For now we quote the result: 7/6 = Re .0 166 Re x Then = − 7/1 c f .0 0277 Re x (11a) 7 − c (L) = c (L) = .0 032 Re 7/1 (11b) D 6 f L These friction laws may be used, for example, to give a simple estimate of the viscous drag on thin aerofoils or other streamlined shapes (see Questions 3 and 4 in the Examples). The above relations are for a smooth-walled boundary layer. Schlichting gives the following approximate formulae for the fully-rough regime: = + x − 5.2 c f 87.2[ 58.1 log 10 ( )] (12a) ks = + L − 5.2 cD (L) 89.1[ 62.1 log 10 ( )] (12b) ks Turbulent Boundary Layers 3 - 4 David Apsley 3.3 Pipe Flow The Reynolds number is usually defined in terms of diameter D and average velocity Uav : U D Re = av (13) 3.3.1 Smooth-Walled Pipes To a good approximation the logarithmic velocity profile holds right across (but see the note below) a D pipe of radius R: r U 1 + R = ln Ey , ( = 41.0 , E = 76.7 ) U(y) y u where y = R – r is the distance from the pipe wall. If Uav is the average velocity and Q the flow rate, then R 2 = = ⌠ U av R Q U 2 r dr dr ⌡0 R r ¡ 2 = ⌠ u u ¡ y − ⇒ U av R 2 ln (E () R y) dy ⌡0 R U 2 ⌠ u ¡ y y dy ⇒ av = ln (E 1() − ) u ¡ ⌡0 R R Change variables to the boundary-layer variable η = y/R : 1 U 2 ⌠ u ¡ R av = ln (E 1() − ) d u ¡ ⌡0 This integrates to give U 1 u ¡ R 3 av = ln( E ) − (14) u ¡ 2 Noting that ¢ ¡ u c u R 1 U D u ¡ 1 c = f and = av = Re f U av 2 2 U av 2 2 then − 2/3 Re c 1 = 1 e E = f ln( Re c f ) 72.1 ln( ) c f 2 2 2 63.1 The logarithm is traditionally converted to base 10 (for “engineering” reasons?): Re c 1 = f 0.4 log 10 ( ) c f 63.1 Prandtl deduced this in 1935, and then adjusted the constants to give a better fit to actual pipe flow data. The result is Turbulent Boundary Layers 3 - 5 David Apsley Re c 1 = f 0.4 log 10 ( ) (15) c f 26.1 Important note . Applying the log law right across the pipe would imply a negative velocity very close to the wall (when y+ < 1/ E). Fortunately, the actual contribution to the flow rate from this region is negligible. Fortunately also, the integral of the logarithm converges (since ln x integrates to xln x − x , which tends to 0 as x → 0). 3.3.2 Rough-Walled Pipes ¢ > For fully-rough pipes (k su / 70 ) the mean velocity profile may be written U = 1 y + ln( ) 5.8 u k s An exactly comparable analysis to that above (see Question 7 in the examples) yields 1 = 7.3 D 0.4 log 10 ( ) (16) c f ks In practice, for commercial pipes, (a) the roughness distribution is very different to that of uniformly-distributed sand; (b) roughness and viscous effects are both significant. The smooth-wall and fully-rough limits were accommodated by the Colebrook-White formula , which can be written in terms of the skin-friction coefficient as: k 1 = − s + 26.1 0.4 log 10 ( ) (17) c f 7.3 D Re c f In the context of pipe flow it is common to use a friction factor rather than skin-friction coefficient. Unfortunately, different authors define this as cf or 4 cf (calling them the Fanning friction factor and Darcy friction factor, respectively). Adopting the definition = 4cf (which gives the most convenient frictional head-loss formula – see below) yields the more common version of the Colebrook-White formula: k 1 = − s + 51.2 0.2 log 10 ( ) , = 4cf (18) 7.3 D Re Colebrook (1939) and Moody (1944) helped compile equivalent sand roughness k s for commercial pipe materials. Typical values are of order 0.01 to 0.1 mm. Moody plotted solutions of (17) for friction factor in terms of Re for a set of typical values of ks in his so-called Moody chart . Turbulent Boundary Layers 3 - 6 David Apsley 0.10 0.09 ks/D 0.08 0.07 0.05 0.06 0.03 0.05 Laminar 0.02 λ Transition 0.04 = 64/Re 0.01 λ 0.03 0.005 0.002 0.02 0.001 0.0004 0.0002 0.0001 smooth-walled limit 0.00001 0.00005 0.01 100 1,000 10,000 100,000 1,000,000 10,000,000 Re = VD/ ν Turbulent Boundary Layers 3 - 7 David Apsley 3.4 Frictional Losses L τ w p D θ p+∆p θ mg Balancing pressure, weight and friction forces along the pipe axis in fully-developed flow, D 2 − p × + mg sin − × DL = 0 4 w Substituting D 2 m = L , sin = − z / L 4 where z is the height of the pipe centreline, this gives D 2 − ( p + gz ) × = × DL 4 w or, dividing by the cross-sectional area, L − ( p + gz ) = 4 w D p + gz is called the piezometric pressure , p*.
Details
-
File Typepdf
-
Upload Time-
-
Content LanguagesEnglish
-
Upload UserAnonymous/Not logged-in
-
File Pages14 Page
-
File Size-