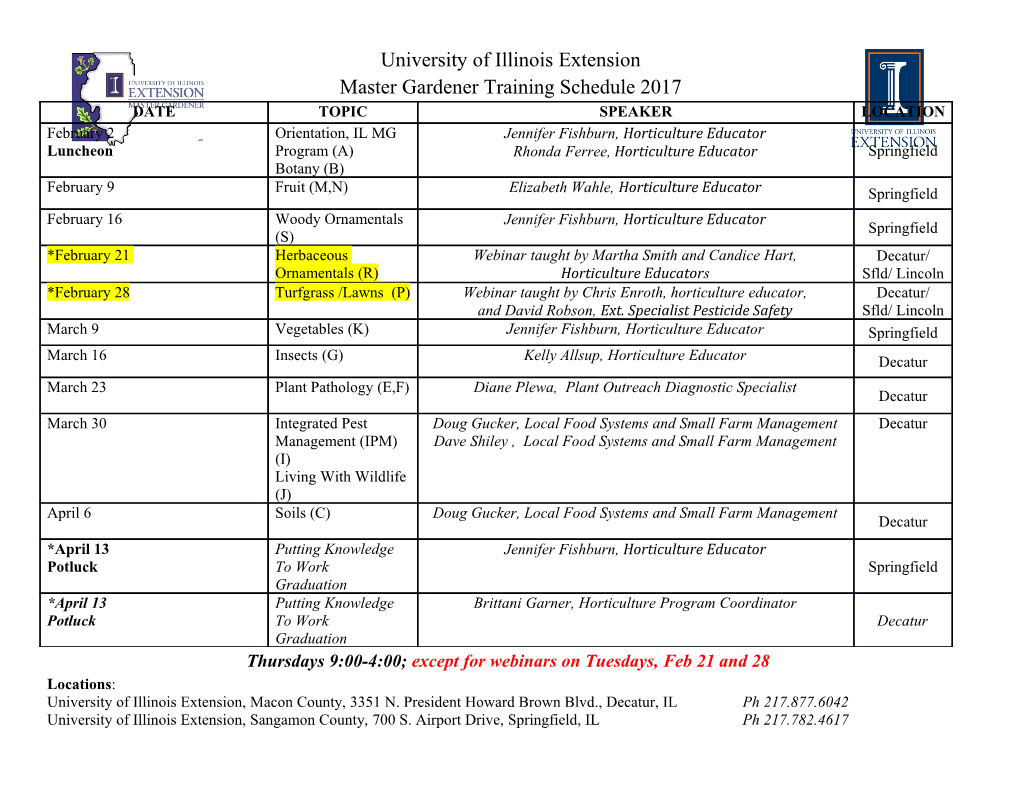
Hydraulic Screw-in Cartridge Valves (SiCV) Technical reference HIC manifold design guidelines, tooling, torque specifications, port and cavity dimensions Technical reference GENERAL GUIDELINES FOR HYDRAULIC INTEGRATED CIRCUITS (HIC) ......................................................M-4 PREFERRED TOOLING FOR MACHINING OF CUSTOM MANIFOLDS .............................................................M-7 PREFERRED TOOLING FOR MACHINING CUSTOM MANIFOLDS ...................................................................M-8 TORQUE SPECIFICATIONS .................................................................................................................................M-9 PORT INFORMATION......................................................................................................................................... M-10 CAVITY TOOLS ...................................................................................................................................................M-12 C–**–2(P) ............................................................................................................................................................M-14 C-**-2 CAVITY DIMENSIONS ...........................................................................................................................M-15 C-**-3 CAVITY DIMENSIONS ...........................................................................................................................M-16 C-**-3S CAVITY DIMENSIONS ......................................................................................................................... M-17 C-**-4 CAVITY DIMENSIONS ........................................................................................................................... M-18 C-**-4U CAVITY DIMENSIONS ......................................................................................................................... M-19 C-**-5S CAVITYDIMENSIONS ..........................................................................................................................M-20 CARTRIDGE CAVITIES .......................................................................................................................................M-21 TC CAVITY ..........................................................................................................................................................M-34 Eaton Hydraulic Screw-in Cartridge Valves (SiCV) E-VLSC-MC001-E6—January 2018 www.eaton.com M-3 General guidelines for hydraulic integrated circuits (HIC) Reviewing circuit Initial design Material sizes Datum point All designs begin with a Once the circuit is fully To obtain an optimal cost The datum point or origin point schematic circuit design understood, it is advisable to manifold it is desirable to (0,0,0) on machining drawings inspired by the application. lay the design out by hand select a standard material size is the upper left corner when Before the planning stage, first. Things to consider while for the manifold, compare the facing the front view. review the design utilizing the planning the design are: block size with the standard following steps: material size table. See Assembly dimensioning • Block size is often specified Standard Material Sizes (page Dimension all ports, mounting • Match schematic symbols by customer. holes and overall envelope to model codes. M-5). If a standard size is not • Specify an overall available, a cut plate may be size. • Note size and cavity of envelope size, in addition used. each valve and write it on to the specified block External clearances schematic. size. Overall envelope size Hydraulic schematic Allow enough room for • Note port numbers of the includes block size and any If a schematic is desired clearance around solenoid valves and write them on valves or fittings protruding on the assembly, it may coils, handknobs, levers and schematic. from the manifold block. be created from existing wrench clearance for fittings. • Note manifold port types • Restrictions specified for symbols. As an alternative, the If 90° elbow fittings are to be and sizes specified by a mounting surface of the entire circuit may be created used, some may be required customer. manifold block. Valves and outside of an assembly and to swing a full 360 arc. ports may be restricted imported as a symbol (block). • Note pressure, flow and Assembly notes from a particular surface. All of the Vickers screw- material of manifold block Notes are added for standard • Specify mounting holes, in cartridge valves have (steel or aluminum). or special assembly, handling, threaded holes and thru schematic symbols which can or shipping instructions, as Circuit questions should be holes (if necessary). be found in the SICV Cartridge Valve Library of Symbols well as special stampings. answered by the customer • Arrange valves in a logical before beginning a design. manner. Valves and ports in CD, used in conjunction with Port table It is also recommended that AutoCad software. Schematic the same regions should be Include a port table with schematic hydraulic regions symbols not found in the located in close proximity to names and sizes of all ports. or networks be color coded each other. library may be created on an using color pens. Regions “as needed” basis. Standard tooling or networks may be broken • Eliminate as many turns in the regions as possible to Accurate design In order to obtain fast down in individual colors turnaround on designs, limit reduce the number of cross All dimensions on CAD design (pressure, tank, pilot, etc.) but the tooling used to that listed drill holes or construction must be accurate and to it may be easier to design if in the standard tooling table. lines. This helps keep scale in order to be utilized by regions are broken down into See Preferred Tooling for pressure drops ( DP) and CAM software in conjunction sub-regions such as pressure Machining Manifolds manufacturing costs down. with CNC machine tools. from port one of a solenoid (page M-6). valve to port two of a relief Manually or interactively valve. Colored layers may modified dimension cannot be be assigned later to match tolerated. schematic circuit coloring. o ot:N Failure to ensure that CAD dimensions are accurate and to scale may result in improper machinery by CNC Machine Tools. Warning This information is designed to assist the engineering professional in the design of manifold blocks and related hydraulic systems. It is the designer’s responsibility to verify the adequacy of the design through approporate M verifications, review and testing of the final design. Where measurements are critical request certified drawings. We reserve the right to change specifications without notice. M-4 Eaton Hydraulic Screw-in Cartridge Valves (SiCV) E-VLSC-MC001-E6—January 2018 www.eaton.com General guidelines for hydraulic integrated circuits (HIC) Datum Point Example in orthographic Use of expander plugs and third angle projection: zero leak gold sae o-ring plugs On small HIC packages, expander plugs can be used to block off construction drilling at the surface of a face. Larger than a 12mm expander plug are not recommended in (a) aluminum. Any construction drillings larger than 0.4” (10 mm) are plugged with zero leak gold SAE O-Ring plugs (internal hex type). The machining Squaring up the block Machining depths callout for these plugs can be Always “square up” the raw All machining depths are to either the industry standard block before machining the the corner of the full diameter SAE straight thread O-ring cavities, ports and holes. This as opposed to the drill point. boss port configuration or the is to eliminate any potential All depths are measured from straight thread O-ring boss “drill walk” which leads to the face plane (surface) of a short port configuration. Refer scrapped manifolds. When manifold block. (b) to Port Dimensions (page M-9 squaring up a block, remove Avoid any drill depths greater and M-10). approximately 0.015” of than 25 diameters. material from each face for Spotface depths Surface treatments Aluminum blocks and 0.030” Additional line lengths may All SAE ports and cavities Any manifold face that calls of material from each face result in increasing pressure have spotface depths of .031” for a surface mounted (gasket for steel blocks. This is done drops. (.8 mm) unless otherwise mounted) valve such as a to ensure that all six faces specified. BSPP ports have DG4V type directional control Machining notes are parallel or perpendicular. spotface depths of .060” valve, or a pump or motor Finished machining should Machining notes are to be (1.5 mm) unless otherwise interface, should have a reflect the squared up added for standard or special specified. minimum roughness callout dimensions. See Standard machining, handling and of 63 microinches (.0016mm) Material Sizes (Table 1). shipping instructions. Counterbores and a flatness callout of .002” In counterbore cases, the actual Example: 4.0” x 5.0” x 6.0” Drillings (.05mm). See examples cavity spotface is located at (101.6 mm x 127 mm x below. Drillings that go completely the depth of the counterbore. 152.4 mm) block will be through a cavity port area When counterbore depths dimensioned to 3.97” x should be on the center are greater than 0.125”, the 4.97”x 5.97” (100.8 mm x 63 axis of the cavity wherever following diameters should 126.2 mm x 151.6 mm). .002 possible; see Figure (a). be used: Otherwise it should intersect Creation of machining table the cavity tangent to the Create
Details
-
File Typepdf
-
Upload Time-
-
Content LanguagesEnglish
-
Upload UserAnonymous/Not logged-in
-
File Pages35 Page
-
File Size-