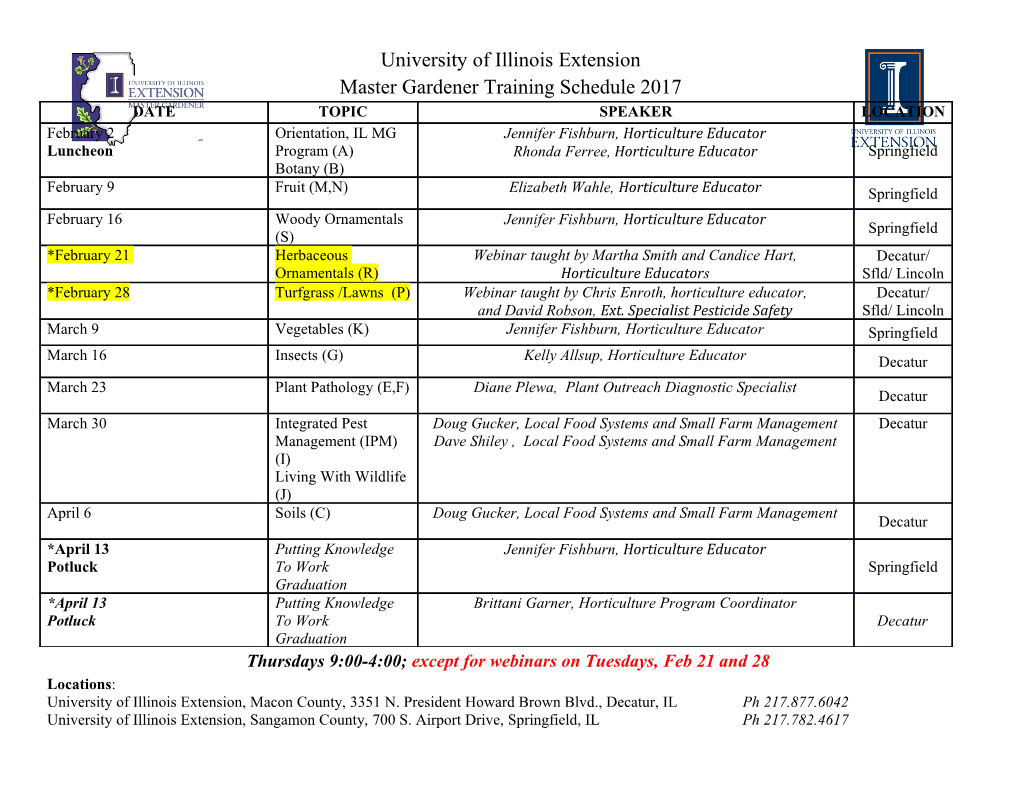
Phil. Trans. R. Soc. A (2008) 366, 1499–1537 doi:10.1098/rsta.2007.2170 Published online 11 January 2008 Nanotribology and nanomechanics in nano/biotechnology BY BHARAT BHUSHAN* Nanotribology Laboratory for Information Storage and MEMS/NEMS, The Ohio State University, 201 West 19th Avenue, Columbus, OH 43210-1142, USA Owing to larger surface area in micro/nanoelectromechanical systems (MEMS/NEMS), surface forces such as adhesion, friction, and meniscus and viscous drag forces become large when compared with inertial and electromagnetic forces. There is a need to develop lubricants and identify lubrication methods that are suitable for MEMS/NEMS. For BioMEMS/BioNEMS, adhesion between biological molecular layers and the substrate, and friction and wear of biological layers may be important, and methods to enhance adhesion between biomolecules and the device surface need to be developed. There is a need for development of a fundamental understanding of adhesion, friction/stiction, wear, the role of surface contamination and environment, and lubrication. MEMS/NEMS materials need to exhibit good mechanical and tribological properties on the micro/nanoscale. Most mechanical properties are known to be scale dependent. Therefore, the properties of nanoscale structures need to be measured. Component- level studies are required to provide a better understanding of the tribological phenomena occurring in MEMS/NEMS. The emergence of micro/nanotribology and atomic force microscopy-based techniques has provided researchers with a viable approach to address these problems. This paper presents an overview of micro/nanoscale adhesion, friction, and wear studies of materials and lubrication studies for MEMS/NEMS and BioMEMS/BioNEMS. It also presents a review of scale-dependent mechanical properties, and stress and deformation analysis of nanostructures. Keywords: nanotribology; nanomechanics; microelectromechanical systems; nanoelectromechanical systems; bioMEMS; bioNEMS 1. Introduction Microelectromechanical systems (MEMS) refer to microscopic devices that have a characteristic length of less than 1 mm but more than 100 nm and combine electrical and mechanical components. Nanoelectromechanical systems (NEMS) refer to nanoscopic devices that have a characteristic length of less than 100 nm and combine electrical and mechanical components. In mesoscale devices, if the functional components are on micro- or nanoscale, they may be referred to as MEMS or NEMS, respectively. These are referred to as an intelligent miniaturized *[email protected] One contribution of 7 to a Theme Issue ‘Nanotribology, nanomechanics and applications to nanotechnology II’. 1499 This journal is q 2008 The Royal Society 1500 B. Bhushan Table 1. Dimensions and masses in perspective. (a) dimensions in perspective human hair w75 000 nm in diameter biological cells in the range of thousands of nm in diameter DNA molecules w2.5 nm wide individual atoms typically a fraction of a nm in diameter NEMS characteristic length !100 nm MEMS characteristic length !1 mm and O100 nm molecular gear w10 nm vertical SWCNT transistor w15 nm quantum-dots transistor 300 nm digital micromirror 12 000 nm (b) weight in perspective NEMS built with cross sections as low as 10K20 N of approximately 10 nm micromachined silicon structure as low as 1 nN water droplet w10 mN eyelash w100 nN system comprising sensing, processing and/or actuating functions, and combine electrical and mechanical components. The acronym MEMS originated in the USA. The term commonly used in Europe is microsystem technology (MST) and in Japan is micromachines. Another term generally used is micro/nanodevices. MEMS/NEMS terms are also now used in a broad sense and include electrical, mechanical, fluidic, optical and/or biological functions. MEMS/NEMS for optical applications are referred to as micro/nanooptoelectromechanical systems (MOEMS/NOEMS). MEMS/NEMS for electronic applications are referred to as radiofrequency MEMS/NEMS or RF-MEMS/RF-NEMS. MEMS/NEMS for biological applications are referred to as BioMEMS/BioNEMS. These devices are produced by either top–down (lithographic, non-lithographic or micromachining) or bottom–up (nanochemistry) processes. To put the dimensions of MEMS and NEMS in perspective, see table 1. Individual atoms are typically a fraction of one nanometre in diameter, DNA molecules are approximately 2.5 nm wide, biological cells are in the range of thousands of nanometres in diameter and human hair is approximately 75 mmin diameter. Three NEMS reported in the table range in size from 10 to 300 nm and one MEMS reported is 12 000 nm. The weight of a micromachined silicon structure can be as low as 1 nN, and NEMS can be built with weight as low as 10K20 N with cross sections of approximately 10 nm. In comparison, the weight of a drop of water is approximately 10 mN and that of an eyelash is approximately 100 nN. A broad class of MEMS/NEMS are used in electromechanical, electronics, information/communication, chemical and biological applications (Bhushan 2007a). MEMS for mechanical applications include acceleration, pressure, flow and gas sensors, linear and rotary actuators, and other microstructures or microcomponents such as electric motors, gear chains, gas turbine engines, fluid pumps, fluid valves, switches, grippers and tweezers. MEMS for chemical applications include chemical sensors and various analytical instruments. MOEMS are the devices that include Phil. Trans. R. Soc. A (2008) Nanotribology and nanomechanics 1501 optical components, such as micromirror arrays for displays, infrared image sensors, spectrometers, bar code readers and optical switches. RF-MEMS include inductors, capacitors, antennas and RF switches. High aspect ratio MEMS (HARMEMS) have also been introduced. Examples of NEMS include microcantilevers with integrated sharp nanotips for scanning tunnelling microscopy (STM) and atomic force microscopy (AFM), quantum corral are formed using STM by placing atoms one by one, AFM cantilever array (Millipede) for data storage, STM and AFM tips for nanolithography, dip pen nanolithography for printing molecules, nanowires, carbon nanotubes, quantum wires (QWRs), quantum boxes (QBs), quantum transistors, nanotube-based sensors, biological (DNA) motors, molecular gears by attaching benzene molecules to the outer walls of carbon nanotubes, devices incorporating nanometre-thick films (e.g. in giant magnetoresistive or GMR read/ write magnetic heads and magnetic media for magnetic rigid disk and magnetic tape drives), nanopatterned magnetic rigid disks and nanoparticles (e.g. nanoparticles in magnetic tape substrates and nanomagnetic particles in magnetic tape coatings). BioMEMS/BioNEMS are increasingly used in commercial and defence applications (Bhushan 2007a). They are used for chemical and biochemical analyses (biosensors) in medical diagnostics (e.g. DNA, RNA, proteins, cells, blood pressure and assays and toxin identification), tissue engineering and implantable pharmaceutical drug delivery. Biosensors, also referred to as biochips, deal with liquids and gases. There are two types of biosensors. A large variety of biosensors are based on micro/nanofluidics. Micro/nanofluidic devices offer the ability to work with smaller reagent volumes and shorter reaction times, and perform analyses of multiple types at once. The second type of biosensors includes micro/nanoarrays that perform one type of analysis thousands of times. (a ) Examples of devices with tribological issues in MEMS/NEMS and BioMEMS/BioNEMS Tribological issues are important in MEMS/NEMS and BioMEMS/BioNEMS requiring intended and/or unintended relative motion. In these devices, various forces associated with the device scale down with the size. When the length of the machine decreases from 1 mm to 1 mm, the surface area decreases by a factor of a million and the volume decreases by a factor of a billion. As a result, surface forces such as adhesion, friction, meniscus forces, viscous drag forces and surface tension that are proportional to surface area become a thousand times larger than the forces proportional to the volume, such as inertial and electromagnetic forces. In addition to the consequences of the large surface-to-volume ratios, the small tolerances that these devices are designed for make physical contacts more likely, thereby making them particularly vulnerable to adhesion between adjacent components. Slight particulate or chemical contamination present at the interface can be detrimental. Furthermore, the small start-up forces and the torques available to overcome retarding forces are small, and the increase in resistive forces such as adhesion and friction becomes a serious tribological concern, which limits the durability and reliability of MEMS/NEMS (Bhushan 1998). A large lateral force required to initiate relative motion between two surfaces, large static friction, is referred to as ‘stiction’, which has been studied extensively in tribology of magnetic storage systems (Bhushan 1996, 1999a,b, 2001, 2002, 2003, 2005a,b, 2007b). The source of stiction is generally Phil. Trans. R. Soc. A (2008) 1502 B. Bhushan (a) supporting springs suspended mass stationary plates suspended mass stationary plates (b) mirror –10° mirror +10° hinge yoke tip landing hinge site yoke CMOS landing site spring tip substrate Figure 1. Examples of (a) an accelerometer MEMS device (Sulouff 1998) and (b) a MOEMS device having commercial use that experiences tribological problems (Hornbeck 1999). liquid-mediated adhesion with the source of
Details
-
File Typepdf
-
Upload Time-
-
Content LanguagesEnglish
-
Upload UserAnonymous/Not logged-in
-
File Pages39 Page
-
File Size-