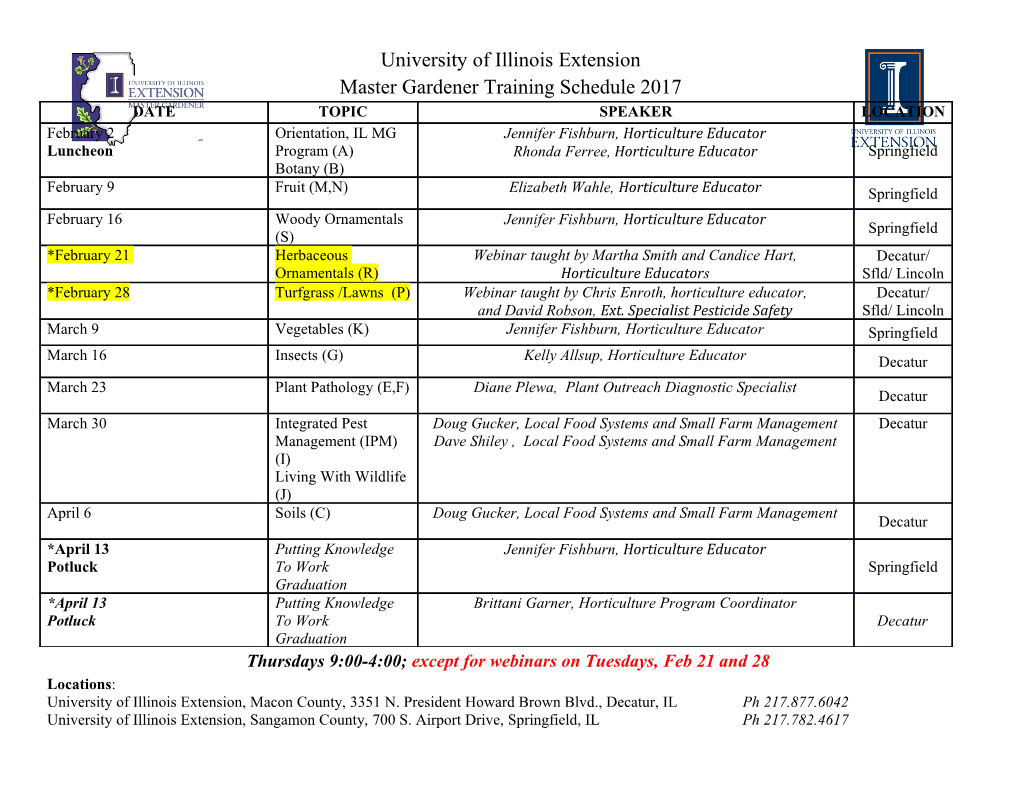
TECHNOLOGY FORESIGHT SEMI-SOLID FORMING HIGH-STRENGTH ALUMINIUM CASTINGS THROUGH SEMI-SOLID FORMING Lightweighting of automobiles has become a major goal for vehicle manufacturers, due to high fuel costs, strict- er emission norms, energy security worries and recycling concerns. Heavy steel parts have to be replaced with light metal alloy parts that match the excellent material properties provided by the steel varieties. The design and fabrication of such high-strength aluminium components needs new knowledge and intensive processes with precise process controls. The automotive industry is willing to accept only high volume production process- es, with low per part costs. They are also ready to accept higher initial capital investments and sophisticated processes, when it enables fast, accurate and reliable fabrication methods. © T. W. van Urk / shutterstock 18 www.autotechreview.com AUTHORS INTRODUCTION Romeo, and car body components by Audi, Fiat and DaimlerChrysler, 1. In the automotive industry currently, The basis of SSF is casting in a semi- there is a strong preference for using high solid state (i.e. between solidus and liqui- pressure die casting process for shaping of dus temperature), which ensures non-tur- aluminium parts, due to its high produc- bulent mould filling and better control of tion rate, low cost and the ability to form the microstructure of the cast product. SAJID MUBASHIR small complex parts. High pressure die The key advantages are: is Director/ Scientist F at TIFAC, Department of Science & casting’s main drawback comes from an :: It eliminates air entrapment, and hence Technology, Government of India inability to control the melt flow inside the cast product will have negligible the mould cavity. When molten liquid porosity and can be welded and heat aluminium is injected into a die cavity treated. Since the molten material is under high pressures, the fluid flow tends cast as slurry, containing a high per- to be turbulent. This leads to air entrap- centage of solid fractions, SSF operates ment, oxide inclusions and formation of at a lower temperature and hence less gas bubbles in the cast part, thus increas- expensive die moulds can be used. PROF KSS MURTHY ing the porosity of the cast part and mak- :: The solidification shrinkage is negligi- is Professor (Retired), Foundry Science, Metal Joining, Structure ing it difficult to machine, anodise, weld, ble. The cast parts have near net shape Property Correlation, Non- or heat treat. and high surface finish, and would not Destructive Testing at The improved or variant processes that need machining or surface treatments. IISc, Bangalore have been developed to overcome these :: The semi-solid slurry is thixotropic in limitations include squeeze casting, vac- nature (i.e. shear thinning). This prop- uum casting, and fully automated die erty enables smooth flow through thin- casting. Another approach is the develop- ner sections in the die, thus facilitating ment of new aluminium alloys that are production of components of intricate more suited to high pressure die casting shapes. processes. :: The superior mechanical properties are SURESH BABU MUTTANA is Scientist C at TIFAC, Department The Semi-Solid Forming (SSF) process nearly equal to forged components, of Science & Technology, is another emerging technology, which is and unlike forging, SSF can produce Government of India ideal for lightweighting of automobiles. It complex geometry components also. is suitable for high volume-of-production Currently, SSF utilises aluminium cast die casting technology for light metals alloys, and this limits the strength such as aluminium, copper and magne- properties that can be achieved. If sium. The process has been used for man- wrought alloys can be used for SSF, ufacturing chassis by automakers, includ- then the properties can match those ing Porsche, DaimlerChrysler and Alfa achieved through the forging process. PROF PRADIP DUTTA is Professor, Heat Transfer in Manufacturing, Computational Methods at IISC, Bangalore Aluminium sub-frames owing to its properties can better divert forces autotechreview July 2012 Volume 1 | Issue 7 19 TECHNOLOGY FORESIGHT SEMI-SOLID FORMING Rheocasting Thixocasting Partical solidifi cation and agitation Solidifi cation Billet with Reheated spherical Semisolid garains globular feedstock 1 Semi-Solid Forming routes An example is the research collabora- casting machines. A number of applied dritic billets, and followed it up with a tion between Rio Tinto Alcan and a research groups are active in this area, cooling slope technique as a cheaper and leading Canadian SSF research group 2. simpler alternative to do the same. Subse- to modify aluminium wrought alloys to In India, a National Facility for Semi quently, they partnered with couple of make them suitable for SSF process. Solid Forming at IISc, Bangalore has been leading automotive companies for semi- So why is SSF not commercially wide- set-up with pilot production facility to solid manufacturing of some automotive spread? One reason is that it relies heavily carry out applied research. It has indige- components. on pre-processed aluminium feedstock nously developed a linear electromagnetic This article discusses the state-of-the- (billets) having appropriate crystalline stirring process for production of non-den- art SSF technology, the main technology structure. This makes it slightly more expensive. The other reason may be related to its knowledge intensive design requirements, the precise process controls and more elaborate die tool design with provision for controlling the cooling rate. Semi-solid forming is also a significant deviation from conventional die casting processes, and the multitude of process parameters makes it difficult for industries to standardise the process. It was origi- nally developed at MIT during the 1970s, and the critical material preparation tech- niques that are needed for the SSF process was protected with many patents. By 1980s, other research groups developed slightly different feedstock preparation techniques. After the patents expired, the research work has spread across the world during the last two decades. The SSF feedstock is now available from companies like SAG (Austria), Stampal (Italy), AFT & Ormet (USA) and Pechiney (France) and some companies developed new heating tech- nologies and online-controlled pressure Aluminium suspension strut mounts and V-pattern strut 20 www.autotechreview.com variants, the required alloys and die solid forming process, within a year. APPLICATIONS OF SSF IN THE moulds, and the process control issues. Thixotropy can be explained simply: AUTOMOTIVE SECTOR: We do not discuss, (a) the modelling/ when one wants to vigorously stir “New- Thin walled Cast nodes for new space simulation issues, which needs an under- tonian” fluids like water, it is required to castings frame chassis standing of fluid flow thermodynamics, put more effort to get to higher speed of High strength Engine mounts, knuckles, and (b) the related die-tool designs. These stirring. In thixotropic material, this is not parts suspension components, two subjects also represent the challenges required, as the viscosity of the materials wheels to be overcome, for widespread commer- decreases with increased force (or shear Wear resi- Compression pistons, bra- cial use of semi-solid forming technology. rate). So, Mayonnaise (a “non-Newto- stant parts ke drums, steering systems nian” fluid) would be highly viscous, Parts with Master brake cylinders, air when still or stirred slowly and becomes high degree conditioner compressor BASIC PRINCIPLE OF SSF less viscous, when stirred vigorously. of tightness housing and safety critical The SSF metal alloy is a slurry of solid parts A major problem faced in conventional spheroidal particles embedded in a 3 Various semi-solid forming applications die casting is the formation of dendritic molten liquid phase, when the tempera- crystalline aggregates within the die cast ture is maintained between its solidus and part, as the molten metal cools and solidi- liquidus temperatures. Good thixotropic Potentially, the SSF process can be fies. Dendritic microstructure growth flow behaviour is obtained when the solid used for several light metals like alumin- leads to zones of weakness and reduces fragments is between 30-65 %. This semi- ium, magnesium, copper, zinc, titanium its mechanical integrity of the cast part. solid material can stand freely (like a alloys and metal-metal-composites. SSF This partly explains the high rejection rate solid), when it is not subjected to pres- material can be processed by casting, in aluminium cast industry in India, sure, and will behave like a fluid when forging or extrusion. However, its use in which stands at an astonishing 20 %! subjected to deformation forces. So, SSF aluminium casting is the most advanced In 1970, the researchers at MIT were billets can be handled as if they were commercially. Applications of semi-solid studying the viscosity of molten metal, completely solid, prior to the casting oper- forming in the automotive sector are and when they fragmented the dendrite ation. And during the casting process, the explained in 3. formation through a stirring mechanism, material flows like a viscous liquid and the resulting molten metal slurry devel- energy required to move it is quite low, oped a large fraction of solids with globu- when compared to other solid forming SSF TECHNOLOGIES lar shape. More interestingly, this mushy processes. This behaviour has something
Details
-
File Typepdf
-
Upload Time-
-
Content LanguagesEnglish
-
Upload UserAnonymous/Not logged-in
-
File Pages7 Page
-
File Size-