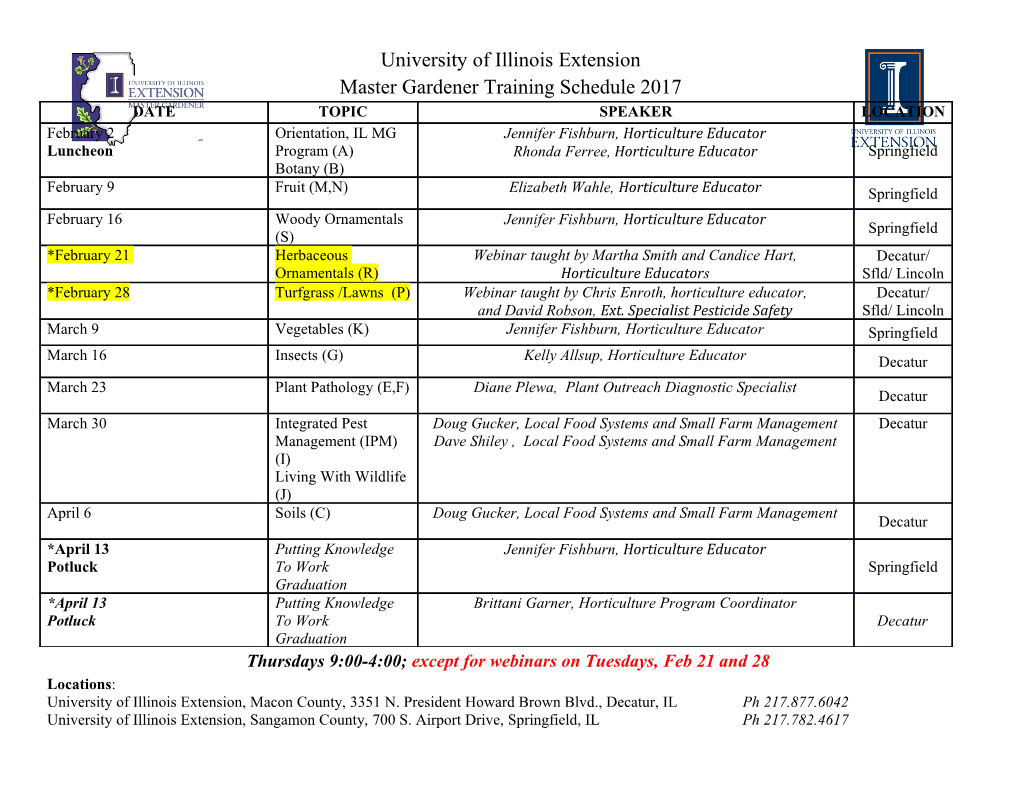
Scientific Technical Review,Vol.LIV,No.3-4,2004 45 UDK: 533.6.011.72:623.451.74 COSATI: 01-01 Testing of the Calibration Model ONERA M4 in the Subsonic Wind Tunnel T-35 Goran Ocokoljić, BSc (Eng)1) In this paper, testing results of the calibration model ONERA M4 in the wind tunnel T-35, VTI, at Mach number M=0.25 are shown. The paper also contains comparative analysis with the testing results of ONERA M1 model in the wind tunnel N.A.E. 5ft x 5ft. Testing conditions for both model M4 and model M1 are the same. The goal is to check the functionality and reliability of the model support system (MSS) and establish its influence on the flow parameters in the wind tunnel test section. Six-component balance ABLE 2” MK XVIII is used for measuring the aerodynamic forces and moments. Key words: aerodynamic testing, aerodynamic model, aerodynamic tunnel, subsonic flow. Labels Introduction LOW quality research in wind tunnels is a significant C − drag coefficient x Fpart of experimental aerodynamics, which includes a − side force coefficient Cy number of different methods. C − lift coefficient First, there are methods based on pressure distribution z measurements with probes or scanning devices. These − rolling moment coefficient C1 methods enable the determination of velocity field and − pitching moment coefficient Cm pressure field, calculation of the Mach number of flow − yawing moment coefficient Cn examination of boundary layer nature and width, etc. C − base drag coefficient Second significant group encompasses anemometric xb methods: laser Doppler anemometry, hot-wire and hot-film − base pressure coefficient Cpb anemometry, acoustic anemometry, anemometry based on D − diameter of the model, (m) particles image, etc. These methods enable direct − diameter of the model base, (m) Db measurement of flow velocity, determination of flow L − length of the model, m velocity vector field, Mach number and turbulence − referent length of the model, (m) intensity. Lref 2 Unavoidable methods for flow quality examination are − area of the model base, (m ) Sb also visualization methods. Optical methods are dominant, − referent area of the model, (m2) Sref with the largest possibilities and the broadest applications M − Mach number (Schlieren method, holography and holographic interferometry). There are also visualization methods with p − base pressure, (bar) b smoke, threads, coats, etc. Methods for Reynolds number − static pressure, (bar) pst and aerodynamic noise are also used. − total pressure, (bar) Confirmation of flow quality in the test section and its p0 q − dynamic pressure, (bar) verification are possible after testing of calibration (standard) models, comparing results obtained in the test Re − Reynolds number with the results obtained in the tests of the same model in − total temperature, (К) T0 internationally recognised laboratories α − angle of attack, (º) In this test, calibration model ONERA M4 is used. β − sideslip angle, (º) ONERA models are made on several scales, to enable φ − rolling angle, º comparison of results obtained in a number of wind tunnels ONER − Office National d’Etudes et de Recherches with different test section dimensions. As this was the first A Aeronautiques testing of ONERA M4 model in this velocity range, results N.A.E. − National Aeronautical Establishment which are obtained are compared with the results of testing ONERA M1 model in the wind tunnel N.A.E. 5ft x 5ft, under the same aerodynamic conditions. 1) Military Technical Institute (VTI), Ratka Resanovića, 11132 Belgrade, SERBIA 46 G.OCOKOLJIĆ: TESTING OF CALIBRATION MODEL ONERA M4 IN THE SUBSONIC WIND TUNNEL T - 35 Test includes the determination of model aerodynamic 75% of the diameter of the model base. Sting is cylindrical coefficients, based on which qualitative estimation of at the length of three diameters of the model base, and its functionality and reliability of the wind tunnel's T-35 new rear part is a cone with the angle of 15˚. test section “C”, and also preliminary estimation of the test Experimental results of testing ONERA M1 model in the section flow quality. wind tunnel N.A.E. 5ft x 5ft were used in comparative In this article, testing results are shown in the form of analysis, and therefore the basic geometric parameters of tables and diagrams. both models are given in Table 1. Along with the calibration model ONERA M4, the wind tunnel T-35, instrumentation, methods of data acquisition Table 1. and reduction, and the course of experiment, are described. Fuselage Wing Wing Fuselage Maximum cross- I Comparative analysis of the results of aerodynamic ONERA diameter area span sat length section model [m] coefficients measurement is also given. In the conclusion, [m] [m2] [m] [m] [ m2 ] results of the examination are summed up. M1 0.036 0.011 0.287 0.040 0.309 0.0015 M4 0.102 0.088 0.800 0.112 0.861 0.0079 Experiment Testing of the calibration model ONERA M4 in the wind tunnel T-35 is a part of the project of flow quality research in the test section “C“. The goal is to check the functionality of the model support system (MSS), which is a part of the test section “C“, and determine the aerodynamic characteristics of the model. Experiment included testing of the calibration model ONERA M4 in subsonic velocity range, in the wind tunnel T-35 test section “C”, for the range of the angle of attack -6˚ < α < +6˚, with increment 1˚, and the rolling angles of φ = 0˚ and φ = 180˚. Testing with these rolling angles was intended to check the repeatability of results. Another goal was the preliminary estimation of flow quality in the test section, taking into account the difference between the obtained values of aerodynamic coefficients. Figure 1. ONERA M4 calibration model Model ° 0 ° 0 0 ONERA has designed the family of models for the 0 , 0 3 0 13,49 , purpose of testing them in its own wind tunnels. Nowadays, 3 these models are used as standard for checking and controlling the new wind tunnel installations. To test the functionality and reliability of the model support system 102 25,3 (MSS) in the wind tunnel T-35, and for preliminary 15,24 estimation of the flow quality, a model from ONERA family 800 is used. 168,65 286,32 The wing span of the series of ONERA models ranges from 0.3m to 1.0m. These models have extremely high Ø64,43 accuracy of manufacture; maximum error does not exceed 0.03mm. Labels of the models are M1, M2, M3, M4 and 67,46 5 2 47,56 101,2 , M5, depending on their scale [6]. 5 0 ° 0 ONERA М4 model (Fig.1) has internal space of adequate 0 ° 0 5 , size for setting up six-component wind tunnel balance 7 172,87 4 ABLE 2” МК XVIII, with diameter of 50.8 mm (Fig.3). Geometric characteristics of the model are shown in the Fig.2, with the fuselage diameter of 102mm. Airfoils of the wing, and airfoils of the horizontal and vertical tails are 50,59 symmetrical, of “peaky” type, with maximum thickness of 112 10.5% at the 37.5% of the chord. The angle between the 861.8 6 168,64 leading edge of the swept wing and the fuselage axis is 30º, 738,69 0 , 0 0 0 aspect ratio of the wing is 7.31, and its installation angle is 615,66 ° 4º with relation to the fuselage axis. The angles between the 192 leading edge of the horizontal and vertical tails and the 425,56 fuselage axis are 37.5º and 47.5º, respectively. The cylindrical fuselage has three sections. The wing and the 286,7 horizontal tail have dihedral angle of 3º and they are not warped. The model is designed for the installation on the sting (Fig.4) with strictly defined geometry. The sting diameter is Figure 2. The basic geometric characteristics of ONERA M4 model G.OCOKOLJIĆ: TESTING OF CALIBRATION MODEL ONERA M4 IN THE SUBSONIC WIND TUNNEL T - 35 47 combination of fan and injector. The value of the total pressure in the test section is 1 bar using fan only, and up to 1.52 bar with the fan and injector combination. Theoretically speaking, the duration of the test with fan only is unlimited, and with the combination of fan and injector is up to 120 s. Instrumentation and data acquisition Absolute pressure transducer, manufactured by Mensor, with Bourdon quartz pipe, is used for measuring the total pressure P0 in the test section. The transducer is pneumatically connected with the Pitot probe, located in the upper part of the collector. The range of the transducer is 1.65 bars. Non-linearity and hysteresis of these transducers are 0.02% F.S. The transducer is calibrated along with the system for data acquisition. Static and total pressure difference Pst-P0 is measured by differential pressure transducer, manufactured by Druck, with the range of 0.07 bars. Measurement points are openings on the wind tunnel wall, at the exit of the collector. Non-linearity and hysteresis of these transducers are 0.02% F.S. The calibration procedure for this transducer Figure 3. Internal six-component wind tunnel balance ABLE 2” МК XVIII is the same as the procedure for the total pressure transducer. Total temperature T0 is measured by RTD probe, which is placed on the same support as the probe for total pressure. The transducer accuracy is ± 0.5 K. Resolvers, located in the mechanism for model movement, measure the angle of attack, sideslip angle and rolling angle of the model. Output of the accurate digital watch is used as time base for data segmentation, and it is sampled along with other transducer signals.
Details
-
File Typepdf
-
Upload Time-
-
Content LanguagesEnglish
-
Upload UserAnonymous/Not logged-in
-
File Pages7 Page
-
File Size-