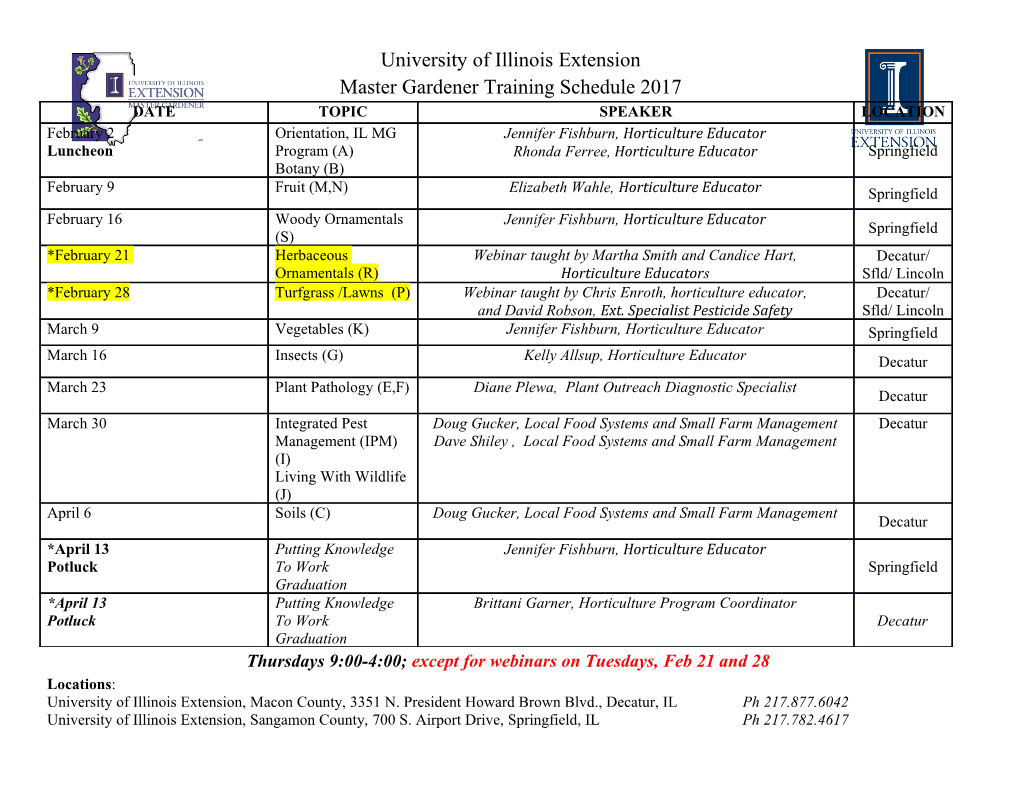
WELDERS’ FAVOURITE SINCE 1938 STAINLESS STEEL TECHNICAL HANDBOOK ELGA STAINLESS STEEL TECHNICAL HANDBOOK www.elga.se01. 02. ELGA STAINLESS STEEL TECHNICAL HANDBOOK CONTENTS Welding of stainless steel requires knowledge about the material as well as welding methods and products to maintain the material’s stainless properties. This techni- cal handbook provides both. If you have any further questions regarding welding methods and products, ask our technical support. You will find your nearest Elga contact at www.elga.se. BRIEF HISTORY OF STAINLESS STEELS 06 STRUCTURE OF STAINLESS STEELS 08 GENERAL PROPERTIES AND METALLURGY 13 CONSUMABLES SELECTION GUIDE 16 TYPICAL DUPLEX MICROSTRUCTURE 18 CRYOGENIC APPLICATIONS 19 DISSIMILAR STEELS AND JOINTS 22 PRACTICAL ADVICE FOR WELDING DISSIMILAR MATERIALS 24 CHOOSING A WELDING PROCESS 25 CHOOSING ELECTRODE COATINGS 27 STORAGE, HANDLING AND POST WELD CLEANING 28 CONSUMABLES GUIDE 31 ELGA STAINLESS STEEL TECHNICAL HANDBOOK 03. CROMAROD CROMACORE CROMAMIG CROMATIG HIGH PRODUCTIVITY AND RELIABLE END-RESULTS QUALITY & KNOW-HOW IN WELDING 04. ELGA STAINLESS STEEL TECHNICAL HANDBOOK WELDERS’ FAVOURITE SINCE 1938 Elga has been renowned for being the most demanding welders’ choice ever since the very beginning. Starting as a family company in Gothen- burg, Sweden, we have grown into a major supplier of consumables for the toughest and most challenging welding. Today, we support welders across the globe with reliable consumables and know-how. As part of the global ITW group, we have the expertise and resources to continually improve welding quality as well as productivity. Welcome to our world! ELGA STAINLESS STEEL TECHNICAL HANDBOOK 05. BRIEF HISTORY OF STAINLESS STEELS 221-206 BC The Chinese Qin dynasty 1778 Molybdenum uses chromium to is discovered by strengthen weapons another Swede; Carl and protect them Vilhelm von Scheele. from corrosion. 1911 Philip 1871 First patent on Monnartz reports “weather resistant on the relationship steel” by John T between chromium Wood and John content and Clark. corrosion resistance. 221 BC 1751 1778 1797 1871 1910 1911 1912 1751 Nickel is 1797 Nicolas 1910 First patent 1912, Krupp discovered by Louis Vauquelin on stainless steel engineers Benno Swedish scientist discovers Chrome. in Germany by Strauss and Axel Fredrik Cronstedt. Philip Monnartz and Eduard Maurer William Borchers. patent austenitic stainless steel as ThyssenKrupp Nirosta. 06. ELGA STAINLESS STEEL TECHNICAL HANDBOOK Mid 80’ The oil industry drives the develop- ment of much more highly alloyed 1919 Elwood materials such as Haynes patents a super duplex steels martensitic stainless (e.g. SAF 2507/UNS steel. S32750) with PREN values above 40, and 1960- Modern super austenitic Duplex SS (Nitrogen steels such as 1911-14 Several alloying is possible) 254SMO (UNS ferritic stainless Sandvik 3R60 S31254) and steels are (18.5Cr, 5Ni, 2.7Mo). 654SMO (UNS discovered. S32654). 1911 1913 1919 1920 1960 Mid Mid From -14 70’ 80’ 90’ 1913 Harry Brearley 1920 First duplex Mid 70’ From 90’ of the Brown-Firth stainless steel was 2205 (22Cr,5.5Ni, – present day research laboratory produced 3Mo,0,17N). This 2205 continues to in Sheffield, England, Avesta 453S (26Cr, DSS still has highest gain momentum in while seeking a 5Ni, 1.5Mo) annual tonnage. various industries. In corrosion-resistant Avesta 453E (26Cr, some cases the ex- alloy for gun 4Ni). traordinary corrosion barrels, discovers resistance is higher and subsequently than necessary. This industrialized a had led to the devel- martensitic stainless opment of numerous steel alloy. lean duplex grades, such as LDX 2101® and Duplex 2304. These new stainless steels contain fewer alloying elements than 2205 and are designed for appli- cations where they can replace grades like 304 and even 316. Source: ISSF. ELGA STAINLESS STEEL TECHNICAL HANDBOOK 07. STRUCTURE OF STAINLESS STEELS Stainless steel is not a specific mate- AtmoAtmosphericspheric corr corrosionosion re sresistanceistance a ass a a ffunctionunction ofof rial, but a common term for a group chrchromiumomium co contentntent of corrosion-resistant steel types. 175 Stainless steels are steels which normally have a chromium content 150 m u of at least 10.5%. , n 125 o i t a r They can also contain nickel, mo- t 100 e lybdenum, nitrogen, copper, man- n pe ganese, tungsten, titanium, niobium, 75 age cerium and other substances in var- r 50 e ying degrees. Interest in nitrogen as v A an alloying element is increasing and 25 many stainless steels, both austenit- 0 ic and duplex with significant nitro- 0 5 10 15 20 25 30 gen levels have been in commercial Chromium content, % use for the last ten years. It is well demonstrated that nitrogen in com- Figure 1. Chromium steels exposed in moderate marine atmosphere for 8 years. bination with molybdenum signifi- cantly increases resistance to pitting corrosion. The nitrogen also increas- es yield strength by solid solution Austenite stabilizers Ni, Mn, C, N, Co, Cu strengthening of austenite. Ferrite stabilizers Cr, Mo, Si, Ti, Nb, V, Al Since the mechanical properties and Table 1. the usefulness of each type of steel is dependent on its composition, it is important to take into account the Increasing the amount of austenite gamma phase. Gamma is an auste- different qualities of each type be- stabilizing elements or decreasing nitic phase which, compared to del- fore choosing the steel and welding the amount of ferrite stabilizing ele- ta-ferrite, is non-magnetic. consumable for the application con- ments will therefore promote a ful- cerned. ly austenitic structure. In the same If the composition of the melt had way, an increase in ferrite stabilizing been 17% Cr-15% Ni (B) instead, Metallurgy elements or a decrease in austenite the gamma phase would have Alloying elements are usually divided stabilizing elements would promote formed initially. Below 1400 °C, the into two groups – austenite stabiliz- the ferritic phase. only existing phase is gamma and ers and ferrite stabilizers – as shown the steel is fully austenitic. By add- in table 1. Some alloying elements Consider the phase diagram for ing elements shown in table 2, it is used in stainless steels are described Iron-Chromium-Nickel as shown in possible to control which phase is in table 2. figure 2. Note that if we follow the formed and in which amount it is composition 22% Cr-10% Ni (A) present. Stainless steels are divided into four during cooling from liquid to room subgroups: temperature, the first phase formed For welding applications, it is often is delta. This is a ferritic phase also desirable to have a small amount • Ferritic stainless steel called delta-ferrite. At about 1400 of delta-ferrite in the weld metal. • Martensitic stainless steel °C, the melt is fully solidified and the The reason for this is that ferrite has • Austenitic stainless steel phase present is delta-ferrite. Below a higher solubility for sulphur and • Duplex stainless steel this temperature, some of the del- phosphorous than austenite. Pri- ta-ferrite will be transformed to the mary austenite solidification causes 08. ELGA STAINLESS STEEL TECHNICAL HANDBOOK rejection of sulphur and phosphorus o C to the remaining liquid. A low melt- ing point segregates results, which A, 22Cr-10Ni B, 17Cr-15Ni become trapped between growing dendrites (austenite grains) causing 1500 Liquid, L cracks along grain boundaries. Pri- δ + L mary ferrite solidification does not cause sulphur and phosphorus re- γ + L jection, thus preventing solidification 1400 cracking. δ δ + γ + L Sometimes, however, it is not desir- γ able to have any delta ferrite at all. δ + γ This is the case in high temperature 1300 applications, where delta ferrite dur- ing service will transform to the very brittle sigma-phase causing weld Fe=68% const metal embrittlement. Type 310 fully austenitic steel is often used in such 0 5 10 15 20% Ni applications. 32 27 22 17 12% Cr Figure 2. Cr-Ni-Fe diagram. ϒ = austenite, δ = ferrite Alloying elements Role Effects Duplex S.S Metallurgy Nickel (Ni) Austenite stabilizer • DSS/SDSS* contains an intermediate amount of Ni such as 4-7% • Prevents formation of detrimental intermetallic phases in austenitic SS • Increases Charpy-V toughness I of austenitic SS • Balances the austenite/ferritic ratio Nitrogen (N) Austenite stabilizer • N is added to offset the effects of Cr and Mo contents to form sigma phase • Increases resistance to pitting and crevice corrosion • Substantially increases strength (mech. prop.) and toughness • Most effective strengthening element (solid solution) • Delays formation of intermetallic phases during welding and fabrication Manganese (Mn) Austenite stabilizer • Increases N solubility and to some extent stabilizes austenitic phase (directly or indirectly). Negative effect decreases resistance to pitting corrosion. Copper (Cu) Austenite stabilizer • Max 2% • Cavitation erosion • In standard SS it is a harmful alloy Chromium (Cr) Ferrite stabilizer • Increases corrosion resistance • Duplex more corrosion resistant than ferritic and 304/316 steels Molybdenum (Mo) Ferrite stabilizer • Improves chloride resistance together with Cr • Typically restricted to 4% in duplex stainless steels • Approx. three times as effective as Cr against pitting and crevice corrosion (Cr 18%) in environments containing chloride. Silicon (Si) Ferrite stabilizer • Added to stainless steels to improve resistance to oxidation at high temperature Tungsten (W) • Increases PREW** Titanium& Niobium (Ti&Nb) Ferrite stabilizer • Binds C and forms carbide, stops chrome from forming harmful chrome carbide Sulphur (S) Impurity • Used to improve machining properties (US = Sulfur) • Among the detrimental alloying elements, sulphur is likely to have the worst effect. S is generally combined with Mn or several oxides to form precipi- tates. The worst case is a large oxide inclusion surrounded by sulphur spe- cies. Locally, the passive film is unable to resist and severe local corrosion may start. Table 2. * DSS = Duplex Stainless Steel, SDSS = Super Duplex Stainless Steel ** (PREN = Pitting Resistance Equivalent (%Cr+3.3x%Mo+16x%N) (PREW = Cr%+3,3x(Mo%+0,5W)+16%N) ELGA STAINLESS STEEL TECHNICAL HANDBOOK 09.
Details
-
File Typepdf
-
Upload Time-
-
Content LanguagesEnglish
-
Upload UserAnonymous/Not logged-in
-
File Pages34 Page
-
File Size-