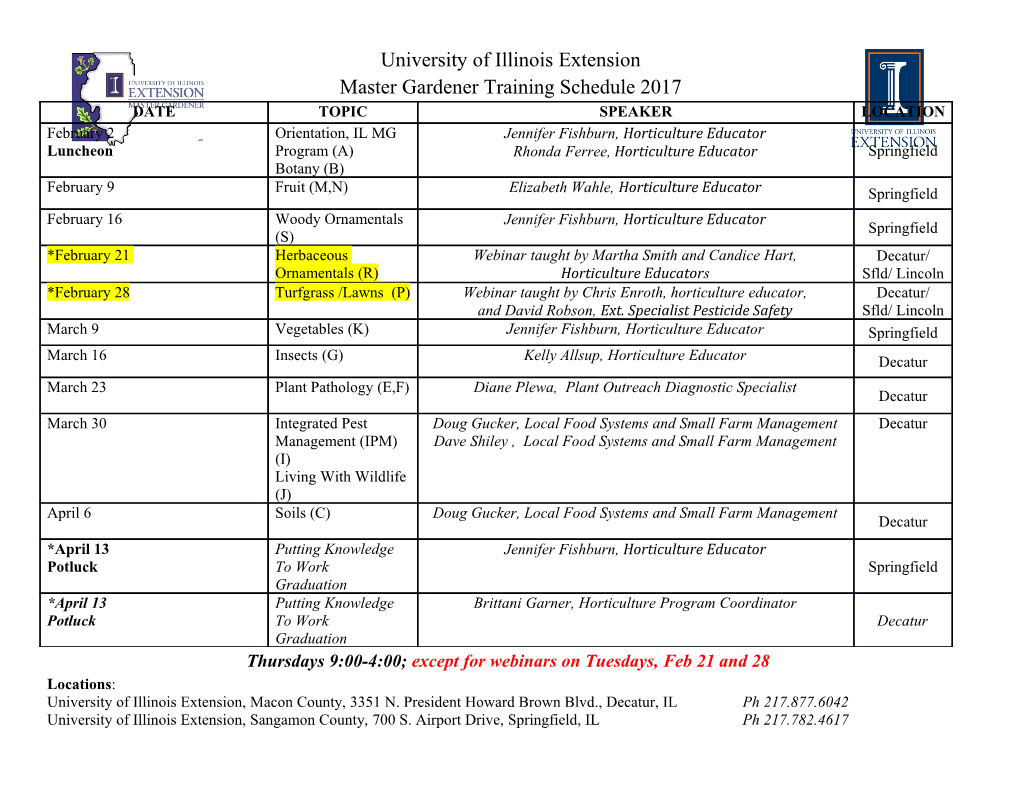
Review The status of membrane bioreactor technology Simon Judd Centre for Water Science, Cranfield University, Cranfield, Bedfordshire, MK43 0AL, UK In this article, the current status of membrane bioreactor types of membrane system*. Although originally commer- (MBR) technology for wastewater treatment is cialized in the early 1970s as a sidestream process reviewed. Fundamental facets of the MBR process and (Figure 2a), it was the introduction of the immersed membrane and process configurations are outlined and process (Figure 2b) twenty years later that precipitated the advantages and disadvantages over conventional exponential growth in both the number of installations and suspended growth-based biotreatment are briefly ident- the total installed flow capacity of MBRs throughout the ified. Key process design and operating parameters are 1990s. The technology is becoming more cost-effective as defined and their significance explained. The inter- membrane and membrane process costs continue to fall relationships between these parameters are identified and environmental regulations become increasingly more and their implications discussed, with particular refer- stringent [1]. It is estimated that the market is currently ence to impacts on membrane surface fouling and chan- doubling every seven years, and will be worth a projected nel clogging. In addition, current understanding of US$360 million by 2010. membrane surface fouling and identification of candi- date foulants is appraised. Although much interest in Process description this technology exists and its penetration of the market Process configurations will probably increase significantly, there remains a lack Several different process configurations exist for MBRs, of understanding of key process constraints such as including extractive and diffusive systems. In extractive membrane channel clogging, and of the science of mem- systems the membrane is used to extract specific com- brane cleaning. ponents across the membrane either for their discrete Introduction Membrane bioreactor (MBR, see Glossary) technologies Glossary are, as the name suggests, those technologies that provide (e)EPS (extracted): extracellular polymeric substances. biological treatment with membrane separation. The term Aerobic oxygen: dependent, as relating to degradation of organic matter. is more appropriately applied to processes in which there is Capex: capital expenditure. a coupling of these two elements, rather than the sequen- CST: capillary suction time: an empirical measure of the filterability of sludge. Dewaterable: ease with which water can be removed (from a sludge). tial application of membrane separation downstream of dMBR: diffusion MBR. classical biotreatment. Conventional treatment of munici- DOC: dissolved organic carbon. pal wastewater (sewage) usually proceeds through a three- eMBR: extraction MBR. Floc: suspended solid particle of the mixed liquor. stage process: sedimentation of gross solids in the feed Flux: volumetric flow rate per unit membrane area (e.g. L m2 hÀ1). water followed by aerobic degradation of the organic mat- FS: flat sheet. HF: hollow fibre. ter and then a second sedimentation process to remove the HRT: hydraulic retention time: the time taken for the liquid phase to pass biomass (Figure 1). An MBR can displace the two physical through a tank. separation processes by filtering the biomass through a iMBR: immersed MBR. MBR: membrane bioreactor. membrane. As a result the product water quality is sig- Mixed liquor: the material formed in the bioreactor, containing biomass and nificantly higher than that generated by conventional other solids. treatment, obviating the need for a further tertiary disin- MLSS: mixed liquor suspended solids. MT: multitube. fection process. Opex: operating expenditure. The commercial significance of this technology is con- Permeability: flux per unit TMP. siderable, with applications in municipal and industrial rMBR: rejection MBR. sMBR: sidestream MBR. wastewater treatment becoming increasingly widespread. SMP: soluble microbial product. A recent review indicated the market value of MBR tech- SRF: specific resistance to filtration: a generic measure of filterability of a nology to be approximately US$217 million in 2005, rising suspension. SRT: solids retention time: the time taken for the solid (particulate) phase to at an average annual growth rate of 10.9% – significantly pass through a tank. faster than other advanced wastewater treatment technol- SVI: sludge volume index: an empirical measure of the settlability of sludge. ogies (e.g. biological aerated filters and sequencing batch TMP: transmembrane pressure (Pa). reactors), and also more rapidly than the markets for other * Hanft, S. (2006) Membrane Bioreactors in the Changing World Water Market, Corresponding author: Judd, S. ([email protected]). Business Communications Company Inc. report C-240. 0167-7799/$ – see front matter ß 2007 Elsevier Ltd. All rights reserved. doi:10.1016/j.tibtech.2007.11.005 Available online 11 January 2008 109 Review TRENDS in Biotechnology Vol.26 No.2 Figure 1. Schematic of conventional sewage treatment and unit operations displaced by MBR technology. biotreatment or for biological treatment of the remaining (i) Production of high quality, clarified and largely effluent [2,3]. In diffusive MBRs the membrane is used to disinfected permeate product in a single stage; the introduce gas into the bioreactor in the molecular form to membrane has an effective pore size <0.1 mm– enhance its use for biotreatment. This means that the gas significantly smaller than the pathogenic bacteria is passed directly into the biofilm, formed directly on the and viruses in the sludge. membrane surface, without having to undergo dissolution. (ii) Independent control of solids and hydraulic retention Therefore nearly100% utilization of the gas takes place, time (SRT and HRT, respectively). In a conventional compared with 30% for conventional air sparging. ASP separation of solids is achieved by sedimen- The principal applications of MBR in biotreatment seem tation, which then relies on growth of the mixed liquor to be aerobic treatment at high loadings [4] and the more solid particles (of flocs) to a sufficient size (>50 mm) to recent hydrogenation of oxyanions such as nitrate [5,6], allow their removal by settlement. This then which is conducive to treatment by all three configurations demands an appropriately long HRT for growth. In (Figure 3). However, notwithstanding the significant pro- an MBR the particles need only be larger than the gress made in the development of diffusive systems in membrane pore size. particular, extractive and diffusive systems have yet to (iii) Operation at higher mixed liquor suspended solids be commercialized. (MLSS) concentrations, which reduces the required reactor size and promotes the development of specific Rejection MBRs nitrifying bacteria, thereby enhancing ammonia Conventionally configured rejection MBRs (rMBRs, removal. Figure 3b) combine biotreatment with membrane separ- (iv) Reduced sludge production, which results from ation by microfiltration (MF) or ultrafiltration (UF), with operation at long SRTs because the longer the solids the membrane being placed either external to or inside the are retained in the biotank the lower the waste solids bioreactor. The membranes are usually of flat sheet (FS) or (sludge) production. hollow fibre (HF) configuration if placed inside the bio- reactor, or multi-tube (MT) if placed outside it (Figure 4). Of these advantages, it is the intensity of the process The advantages offered by this process over conventional (i.e. the smaller size of the plant compared to conventional activated sludge processes (ASPs, Figure 1) are widely treatment) and the superior quality of the treated product recognized [1], and of these the ones most often cited are: water that are generally most important in practical wastewater treatment applications. An MBR displaces three or four individual process, demanding only that the initial screening stage (which provides screened sew- age from the raw sewage, Figure 1) be upgraded to limit the impact of large gross solids (>1–3 mm in size) on clogging of the membrane flow channels. Having said this, com- pared with conventional biotreatment processes MBRs are to some extent constrained, primarily by: (i) Greater process complexity; membrane separation demands additional operational protocols relating to the maintenance of membrane cleanliness. (ii) Higher capital equipment and operating costs; the membrane component of the MBR incurs a significant capital cost over and above that of an ASP and Figure 2. MBR process configurations: (a) sidestream and (b) immersed. maintaining membrane cleanliness demands further 110 Review TRENDS in Biotechnology Vol.26 No.2 Figure 3. System configurations, denitrifying MBR: (a) nitrate extraction (eMBR), (b) membrane diffusion of hydrogen (dMBR) and (c) biomass rejection (rMBR). capital equipment (capex) and operating costs (opex). System parameter inter-relationships This is only partly offset by the small size of the plant. As already stated, MBRs offer greater process control than conventional ASPs because of the uncoupling of SRT and In addition, there are further operational issues, in- HRT. These two parameters are usually defined by the cluding greater foaming propensity (partly associated with system biokinetics (i.e. the speed at which the active the larger aeration demand of the MBR process compared microorganisms break down the components of
Details
-
File Typepdf
-
Upload Time-
-
Content LanguagesEnglish
-
Upload UserAnonymous/Not logged-in
-
File Pages8 Page
-
File Size-