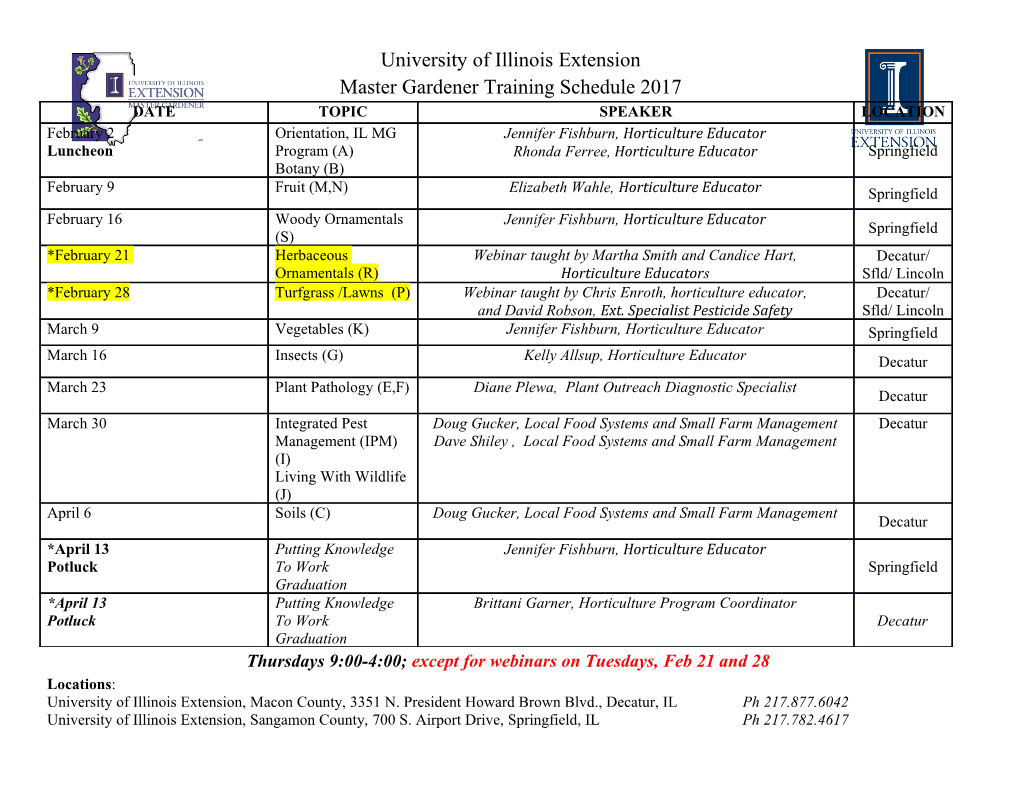
Originally appeared in: April 2014, pgs 63-66. Used with permission. Petrochemical Developments Special Report J. M. LLANES, B. ARAMBURU, M. ARJONA and E. SERRANO, CEPSA, Huelva, Spain; and M. MIRANDA, C. KEELEY, V. KOMVOKIS and S. RIVA, BASF, Iselin, New Jersey New catalyst increases FCC olefin yields Spanish Petroleum Co. (CEPSA) has three refineries in Spain mance was possible. The base case catalyst was a high propylene (Tenerife, La Rábida in Huelva and Gibraltar–San Roque) that yield catalyst.3 To see if the new catalyst would outperform this, produce transport fuels and petrochemical feedstock. The La Rá- laboratory testing and a commercial trial were undertaken. bida refinery started operations in 1967, and the refinery configu- ration and port facilities allow the refinery to produce, store and Trial objectives. The refinery defined four objectives for the distribute a wide range of products for industry and consumers. new catalyst. They were: The fluid catalytic cracking unit (FCCU) was designed with the 1. Increase propylene and isobutylene yields goal to enable processing flexibility for a wide variety of feeds.a 2. Maintain similar light cracked naphtha at higher In recent years, the profitability of European refineries has been propylene yield negatively affected by a number of large-scale trends. Two particular 3. Increase bottoms upgrading and conversion trends are the reduced appetite for gasoline imports from Europe to 4. Improve the capability and flexibility to process the East Coast of the US and the movement toward dieselization. 100 However, adaptable refineries are able to improve product mix to 90 Furfural extracts meet changing societal needs and maintain profitable margins. In VGO New catalyst trial particular, refineries able to produce high-quality petrochemicals 80 feedstock (like propylene), make the right amount of gasoline and 70 increase conversion of low-value feeds, have improved margins. 60 Around 80% of propylene is generated as a byproduct of ethyl- ene via steam cracking and gasoline by the FCCU. However, recent 50 shifts to using lighter feedstocks in steam crackers have resulted in 40 1 a decrease in propylene production. There is potential to fill this 30 gap with FCCU propylene. Analysis of FCCU equilibrium catalyst 20 (ECat) data shows increased propylene make from all regions be- Furfural extracts and VGO, vol% of total feed tween 2002 and 2012. This trend is expected to continue.2 At the 10 La Rábida refinery, making propylene is an attractive proposition, 0 since the refinery and petrochemical sites are closely integrated. 18/10/2012 17/03/2013 07/12/2012 21/05/2012 26/01/2013 03/10/2013 10/07/2012 CEPSA’s La Rábida refinery has been producing high propyl- 14/08/2013 01/04/2012 25/06/2013 29/08/2012 06/05/2013 ene yields for almost 25 years. Nonetheless, the refinery wished to challenge the status quo and investigate if even better perfor- FIG. 1. FCCU feed composition. 12.0 22 11.5 21 11.0 20 10.5 10.0 19 Propylene, %wt 9.5 Isobutylene, wt% 18 9.0 17 8.5 Base catalyst Base catalyst New catalyst New catalyst 8.0 16 0 5 10 15 20 25 0 5 10 15 20 25 Furfural extracts on feed, vol% Furfural extracts on feed, vol% FIG. 2. Propylene (left) and isobutylene (right) yields vs. proportion of FE in feed. HYDROCARBON PROCESSING APRIL 2014 Petrochemical Developments unconverted oil (UCO) from the hydrocracker mized liquefied petroleum gas (LPG) olefins.5, 6 This particular and other nonconventional feeds in the FCC. catalyst allows for the production of highly olefinic naphtha by pro- viding enhanced diffusion of feed molecules to pre-cracking sites Laboratory testing. Prior to the commercial trial, CEPSA located on the external, exposed surface of highly dispersed zeolite R&D performed a catalyst evaluation in its laboratory, compar- crystals. This results in higher bottoms conversion with high yields ing catalysts from the incumbent and new catalyst suppliers.b of olefinic naphtha. The gasoline range olefins are then selectively Fresh catalyst samples from each supplier were steam deacti- converted to LPG olefins by the ZSM-5 functionality.8 vated to simulate commercial ECat and then tested in a Davison circulating riser pilot plant unit. Based on the results of this eval- Technical support service. While the catalyst was being uation, the new catalyst was selected for a commercial unit trial.b tested, technical support services were provided to the refin- In general, FCCUs typically produce around 4 wt% to 6 wt% ery. The package included site visits and logistical support, propylene, depending on feed type, operating conditions and process and laboratory sample analysis and FCCU optimiza- the FCC catalyst. By optimizing all these factors, propylene pro- tion using a number of proprietary tools. duction can be increased up to 12 wt%.2, 4 To generate higher propylene yield, ZSM-5 additive is typi- Trial results. The La Rábida FCCU feed is a mixture of vacuum cally added on top of the base catalyst, which can result in dilu- gasoil (VGO) and nonconventional feed components, such as tion of the base catalyst activity. As a rule of thumb, every 5% UCO from the hydrocracker, Furfural extract (FE) from lubes of non-FCC cracking material in the unit inventory reduces the processing and other low-value components. It is desirable to FCC conversion by 1%. This is not a concern at low ZSM-5 ad- process all the UCO in the FCCU because recycling this in the ditive levels, but at the high levels required to truly maximize hydrocracker tends to shorten catalyst cycle length. propylene, it can become an issue. This can require higher fresh As the proportion of UCO in FCCU feed is increased, the pro- catalyst addition rates to compensate for this activity dilution. portion of FE must also be increased to improve slurry viscosity The catalyst under evaluation does not suffer activity dilution and heat balance in the FCCU. However, FE contains about 80% because the ZSM-5 functionality is present in the base catalyst for- hydrocarbons with aromatic rings, and with the previously sup- mulation. The presence of the ZSM-5 zeolite also allows for maxi- plied catalyst in the base case operation, it was difficult to convert this material in the FCCU. In addition, the refractory FE con- 35 tributed to increased slurry yields. Historically at La Rábida, the 34 Base catalyst maximum amount of FE that could be processed in the FCCU New catalyst 33 was constrained by the maximum slurry disposal to fuel oil. 32 The new catalyst delivered improved bottoms cracking perfor- 31 mance, allowing more of the FE aromatic side chains to be convert- ed. As a result, it was possible to significantly increase the proportion 30 of FE in feed. The FE limit with the base catalyst was around 10%, LPG yield, wt% 29 while, with the new catalyst, the FCCU is now able to operate with 28 up to 20% FE in feed. The flexibility to increase the proportion of 27 FE in the FCCU feed enabled all the UCO production from the 26 hydrocracker to be sent to the FCCU for the first time. Increasing 25 the FE and UCO in FCCU feed has enabled the refinery to signifi- 510 515 520 525 530 535 540 545 550 555 cantly reduce the amount of VGO sent to the FCCU. VGO is a good Reactor outlet temperature, °C quality FCC feed, but it is also significantly more expensive than FE FIG. 3. Total LPG production vs. reactor outlet temperature. and UCO. Further, it is preferred to send VGO to the hydrocracker where it is more valuable to the refinery. The net results were: 36 6 35 5 34 33 4 32 LCN, wt% 3 31 LCN olefins, wt% 2 New catalyst trial 30 C6s Base catalyst C7s 29 New catalyst C8s 1 C9s 28 510 515 520 525 530 535 540 545 550 555 0 Reactor outlet temperature (ROT), °C FIG. 4. Light-cracked naphtha (LCN) yield vs. ROT (left) and CEPSA R&D LCN olefins wt% for the La Rábida feed (right). HYDROCARBON PROCESSING APRIL 2014 HYDROCARBON PROCESSING APRIL 2014 Petrochemical Developments 10.0 10.0 9.5 Base catalyst 9.5 Base catalyst New catalyst New catalyst 9.0 9.0 8.5 8.5 8.0 8.0 7.5 7.5 7.0 7.0 Slurry yield, wt% Slurry yield, wt% 6.5 6.5 6.0 6.0 5.5 5.5 5.0 5.0 510 515 520 525 530 535 540 545 550 555 0 5 10 15 20 25 ROT, °C Furfural extracts on feed, vol% FIG. 5. Slurry yield vs. ROT (left) and proportion of FE in feed (right). 10.0 TABLE 1. Yield improvements and feed changes provided 9.5 Base catalyst increased profitability New catalyst 9.0 Base catalyst New catalyst 8.5 FE in feed, wt% Up to around 10 Up to 20 8.0 UCO in feed Part of production All production 7.5 Propylene yield, wt% Base +0.81 7.0 Isobutylene yield, wt% Base +0.92 Slurry yield, wt% 6.5 Total LPG, wt% Base +2.14 6.0 Total naphtha yield, wt% Base –0.81 5.5 Light cycle oil yield, wt% Base –1.26 5.0 Coke yield, wt% Base +0.2 4.0 4.2 4.4 4.6 4.8 5.0 5.2 5.4 Coke yield, wt% Slurry yield, wt% Base –0.89 FIG. 6. Slurry yield vs. coke yield. Conversion, wt% Base +2.12 Raw FCCU profitability Base +2.5 $/B of feed 1.
Details
-
File Typepdf
-
Upload Time-
-
Content LanguagesEnglish
-
Upload UserAnonymous/Not logged-in
-
File Pages4 Page
-
File Size-