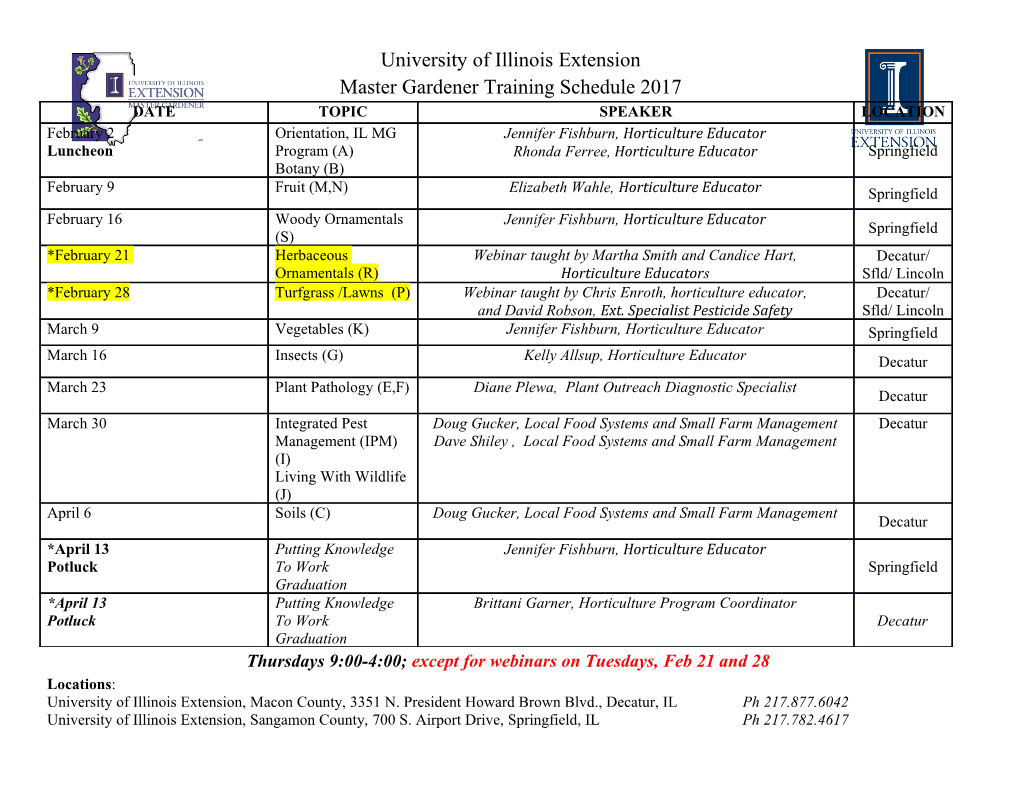
International Journal of Scientific Research and Innovative Technology ISSN: 2313-3759 Vol. 4 No. 8; August 2017 Review Article (2017) Development and Characterization of Nanoparticle Metal Matrix Composites: A Review Muhammad Arshad Chaudhry1, Liaqat Ali2, Khalid Mahmood Ghauri2 1Ph.D Research Scholar, Department of Metallurgical and Materials Engineering, University of Engineering & Technology, Lahore, Pakistan 2Professor Dr. Department of Metallurgical and Materials Engineering, University of Engineering & Technology, Lahore, Pakistan Corresponding Author: [email protected] Abstract: A composite material consists of at least two or more physically and chemically separate phases, one being a metal and other may be a ceramic. In recent years, Al and its alloys based cast MMCs have gained a great importance in the fields of engineering and technology due to improved properties such as high strength, low CTE, good fatigue resistance and lower creep rate than unreinforced materials. The present research is aimed for Development of nano particle Metal Matrix Composites by using stir casting process and subsequent characterization for analyzing the microstructure and mechanical properties. MMCs play a vital role in the present day industrial and engineering sectors like Automotive, Aerospace, Defense and Industrial Infrastructure. Al alloy / SiC nano particle composites using stir casting method are light weight along with high strength and toughness. It has various advantages such as simple, flexible and could be made economical if applicable to large quantity production with enhanced efficiency of the engineering systems. Nano Composite has nano particles with average particle size of 45-55nm. Its properties include mechanical, electrical and thermal which depends upon the materials composition used. The properties and microstructures are governed by type and size of reinforcement, nature of bonding and process of production. Recent focus is on reinforcing aluminum matrix with much smaller particles, submicron or nano sized range, is one of the key factor in producing high performance composites with enhanced mechanical properties. Keywords: Al-Cu alloy, SiCnp, Stir Casting, Characterization. 90 International Journal of Scientific Research and Innovative Technology ISSN: 2313-3759 Vol. 4 No. 8; August 2017 1. Introduction in Sequence of Events having 50% improvement with 2.0 wt% nano particle [10]. MMC is produced using Stir Casting by selecting metal Al is widely used because of its easy availability, high matrix of required grade and the dispersion of the strength to weight ratio, easy machinablity, durability, reinforcement material. In order to form a vortex, stirring ductility and malleability [11]. Stir casting is the type of is carried out vigorously in which reinforcing materials are vortex heating with stirring method in which the raw inserted from the vortex side. The reinforcement particles material gets homogeneously mixed with each other at along with all impurities drag to form the vortex. The air is controlled temperature rate [12]. It is well known that entrapped by the vortex into the melt. Due to increased MMCs being light weight, hard and abrasion resistant are viscosity of the slurry, it is difficult to remove the air from widely used for high temperature and speed parts such the melt [1]. The Particle distribution in the melt depends as pistons, axles, high speed wheels and so on [13]. upon the viscosity of the slurry, particle wetting, particle settling rate, effective mixing, agglomeration breakup and Decrease in the reinforcement particle size from micron minimum gas entrapment [2]. The Metal matrices have a to nano sized increases the tendency of particles useful combination of properties such as high strength, clustering and agglomeration but having good strength. ductility and high temperature resistance but sometimes Homogenous particle distribution improves mechanical have low stiffness, whereas ceramics are stiff and properties [14]. Al Metal Matrix Nano Composites strong though brittle [3]. (AMMNCs) have gained considered importance because It is well known fact that Liquid phase process has of dispersion of nano particles in the host matrix to achieve superior mechanical properties [15]. capability to develop producing of intricate profiles having light weight [4]. Al and its alloys have preferable dispersing Al alloys having light weight, good stiffness, corrosion of SiC due to its high melting point (23000C), high stiffness resistance and improved mechanical properties etc [16]. (480 GPa), good thermal stability, high hardness (9.7 Mohs), Al alloys are mostly attractive due to their low density, great resistance to chemical attack at room temperature, good thermal & electrical properties and having good low density (3.21 gm/cm3) and low thermal coefficient of damping capacity [17]. Stir casting method is used to expansion (4.7 x 10-6 K-1). That’s why, SiC has proved achieve a suitable dispersion. It has some advantages competitive reinforcing material with wider applications in such as simple, flexible, economical and applicable to industries [5]. large quantity production [18]. Al alloy reinforced with particulates composites are achieving great importance Al Metal Matrix Composites (AMMCs) are produced by dispersing SiC, Al 203 and B4C having micron or nano sized due to their low cost, isotropic in nature and useful into Al alloy matrix. [6]. Al Metal Matrix Nano Composites for secondary processing [19]. (AMMNCs) reinforced by nano scale particulates are widely The development of Al alloy / Al2O3 reinforced used in industry such as automotive and aerospace [7]. Stir (MMNCs) is important for such applications in casting method has some limitations of poor wettability aerospace, jet engine exit vanes, blade sleeves of which enhances the tendency of agglomeration of helicopters, parts of space shuttle, piston and cylinder reinforcement material. The wettability of SiC and Al2O3 liners, brake drums and discs [20]. Cast Al alloy matrices may be improved by adding Si or Mg [8]. have higher specific strength, specific modulus and The objective of the present study was to investigate the good wear resistance [21]. Al alloys are preferred influence of the stir casting process parameters like heating engineering materials in automobile and aviation temperature with holding time for uniform distribution of industries for various high performance components [22]. SiC particles and obtain mechanical properties such as TS, Al alloys reinforced with Al2O3 have been used in ductility, impact and hardness behavior [9]. automobile, aerospace, aircraft etc. due to their high Current researches reveal that the dispersing of strength- to-weight ratio, good cast ability and better nanoparitcles into the Al matrix improve the hardness, tribological properties [23]. The dispersion of SiC into yield and UTS substantially whereas the ductility is retained. It was observed that yield strength of A356 alloy 91 International Journal of Scientific Research and Innovative Technology ISSN: 2313-3759 Vol. 4 No. 8; August 2017 Al matrix is constrained due to more %age of Si. It is casting method is most suitable for large quantity noted that viscosity of the molten metal increases because production of composite [40]. The development of of the addition of nano SiC particles [24]. Stir Casting is one Aluminum Metal Matrix Nano Composites (AMMNCs) is of the most economical, simple casting route for the most considered material for high temperature production of AMMCs [25]. Composite materials have more applications, due to their excellent mechanical properties, potential for replacing of widely used steel and Al. They increased performance and weight saving for more have many times better performance [26]. reduction of fuel consumption [41]. Al matrix composites reinforced with SiC have structural Stir casting process has certain characterized features and non-structural applications both at room and high such as simple and low cost technology, dispersion phase temperatures. [27]. A MMC is an engineered material by may not more than 30 vol %, inhomogenous distribution combining the metal (matrix) and ceramic hard particles of reinforced particles, might be clusters of dispersed (reinforcement) in order to obtain required properties [28]. particles and possibility of gravity segregation of Al metal matrix composites have specific use due to low dispersed phase because of difference in the densities of cost, ease in fabrication, recyclability and isotropic matrix and dispersed phases. Rheocasting / characteristics [29]. Al alloys are used for engineering compocasting is the method in which matrix in semi applications at moderate temperature [30]. solid state is used to improve the distribution of dispersed phase [42]. There are various factors such as In the production of composite with desired properties, the nature and type of reinforcement material, its important factors like nature of metal matrix and choice, particle size and weight or volume fraction, the the kind of reinforced particulates and the process involve, processing conditions, secondary forming and heat must be standardized [31]. By using casting method, the treatment processes, which affect the properties of cost of composite production is about 1/3 to 1/2 and for MMCs. [43]. high volume production, it falls to 1/10 [32]. Normally, Al and its alloys solidify in columnar structure having In order to obtain optimum mechanical properties of large
Details
-
File Typepdf
-
Upload Time-
-
Content LanguagesEnglish
-
Upload UserAnonymous/Not logged-in
-
File Pages41 Page
-
File Size-