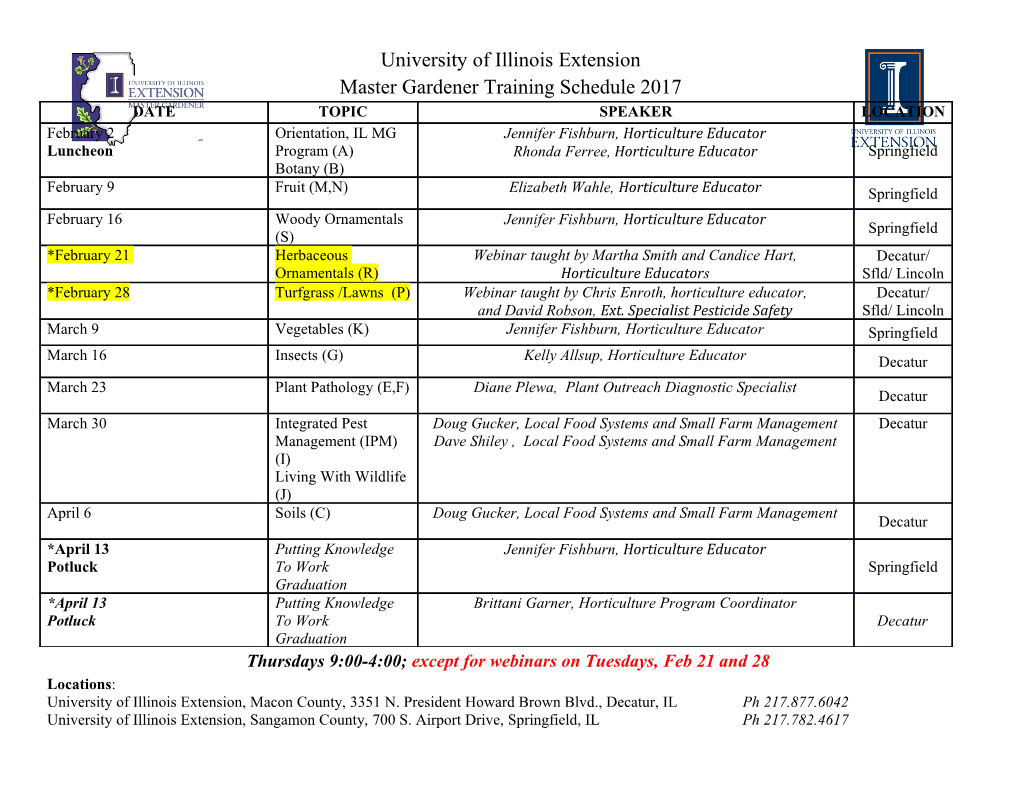
Continuous Casting Technology for Ferrous and Non-Ferrous Foundries FET Faculty (Engineering and Technology) MMU Multimedia University, Malaysia n continuous casting process, metal is achieved and dense bars, semi-finished products with a fine structure Imelted in a furnace and poured into a of crystals and even chemical composition is produced. Continuous tundish. The pour is accomplished through casting allows producing a wide range of different profiles: cylindrical ceramic piping, and the tundish is covered bares, tubes, square bares and tubes, hexagonal profiles, slabs of to prevent oxidation of the metal. From the various thickness and width. This method allows achieving any profile tundish, it is released into a mould. As the form, which is possible to flare through the crystallizer. metal cools and solidifies, usually aided Continuous Casting Technology in Foundries with water cooling systems, which surround An industrial horizontal continuous casting plant is shown below in the mould, finished cast metal protrudes Figure-2. It explains the processing of rod casting and strip casting, from the far end of the mould. Torches can which is self-explanatory. be used to cut the metal off at set lengths FIGURE-1 : INDUSTRIAL CONTINUOUS CASTING PLANT as desired. This method of metal casting is most effective, if it is necessary to manufacture semi-finished products of standardized form in large series. This method also provides increased control over the process through automation. Equal and continuous supply of metal, its crystallization and removal of the product allows obtaining a homogeneous semi- finished metal product during the casting process. With intensified cooling with water, it is possible to increase the speed of crystallization. Choosing the right speed, there can be a focused crystallization in the material, i.e., lengthwise to the cast axis is y g o Continuous casting transforms that enough heat is extracted to solidify at the casting speed. Liquid metal l o molten metal into solid on a continuous a shell of sufficient thickness. The shell continues to pour into the mould to n basis and includes a variety of is withdrawn from the bottom of the replenish the withdrawn metal at an h c important commercial processes. mould at a "casting speed" that matches equal rate. Upon exiting the mould, the e These processes are the most efficient the inflow of metal, so that the process strand enters a roller containment T way to solidify large volumes of metal ideally operates at steady state. Below section and secondary cooling into simple shapes for subsequent the mould, water is sprayed to further chamber in which the solidifying strand processing. Most basic metals are extract heat from the strand surface, is sprayed with water, or a combination mass-produced using a continuous and the strand eventually becomes of water and air referred as "air-mist" casting process, including over 500 fully solid when it reaches the to promote solidification. Once the million tons of steel, 20 million tons of ''metallurgical length''. Solidification strand is fully solidified and has passed aluminium, and 1 million tons of copper, begins in the mould, and continues through the straightener, the dummy nickel, and other metals in the world through the different zones of cooling bar is disconnected, removed and each year. Continuous casting is while the strand is continuously stored. distinguished from other solidification withdrawn at the casting speed. FIGURE-2 (B) SCHEMATIC SKETCH OF processes by its steady state nature, Finally, the solidified strand is CONTINUOUS CASTING PROCESS WITH relative to an outside observer in a straightened, cut, and then discharged STRAIGHTENING ROLLS & CUTTING TORCH laboratory frame of reference. The for intermediate storage or hot charged molten metal solidifies against the for finished rolling. Continuous casting mould walls while it is simultaneously process details are shown below in withdrawn from the bottom of the Figure-2 (a) and Figure-2 (b). mould at a rate, which maintains the FIGURE-2 (A) SCHEMATIC SKETCH OF solid-liquid interface at a constant CONTINUOUS CASTING PROCESS position with time. The process works best when all of its aspects operate in this steady-state manner. Relative to other casting processes, continuous casting generally has a higher capital cost, but lower operating cost. It is the most cost- and energy- efficient method to mass-produce semi finished metal products with consistent quality in a variety of sizes and shapes. Cross- sections can be rectangular, for subsequent rolling into plate or sheet, square or circular for long products, and even “dog-bone” shapes, for rolling into I or H beams. Many different types of continuous casting processes exist. Vertical machines are The shape of the tundish is typically used to cast aluminium and a few other rectangular. Nozzles are located along metals for special applications. Curved its bottom to distribute liquid steel to machines are used for the majority of the mould. The tundish also serves steel casting and require bending and several other key functions such as to or unbending of the solidifying strand. enhance oxide inclusion separation, to Horizontal casting features a shorter provide a continuous flow of liquid building and is used occasionally for To start a cast, the bottom of the steel to the mould during ladle both nonferrous alloys and steel. mould is sealed by a steel dummy bar. exchanges, to maintain a steady metal Finally, thin strip casting is being This bar prevents liquid metal from height above the nozzles to the mould, pioneered for steel and other metals in flowing out of the mould and the thereby keeping steel flow uniform and low-production markets in order to solidifying shell until a fully solidified also to provide more stable stream minimize the amount of rolling strand section is obtained. The liquid patterns to the mould. The main required. poured into the mould is partially' function of the mould is to establish a Co n t i n u o u s C a s t i n g P ro ce s s solidified in the mould, producing a solid shell sufficient in strength to Description strand with a solid outer shell and a support its liquid core upon entry into In the continuous casting process, liquid core. In this primary cooling the secondary spray-cooling zone. molten metal is poured from the ladle area, once the steel shell has a The mould is an open-ended box into the tundish and then through a sufficient thickness, the partially structure, containing a water-cooled submerged entry nozzle into a mould solidified strand will be withdrawn out inner lining fabricated from a high cavity. The mould is water cooled so of the mould along with the dummy bar purity copper alloy. The inner face of 30 June 2013 the copper mould is often plated with are now fully computer-controlled. While the large amount of chromium or nickel to provide a harder Several electromagnetic and thermal automation helps produce castings working surface, and to avoid copper sensors in the ladle shroud, tundish and with no shrinkage and little pickup on the surface of the cast mould sense the metal level or weight, segregation, continuous casting is of strand, which can otherwise facilitate flow rate and temperature of the hot no use if the metal is not clean surface cracks on the product. Mould metal, and the programmable logic beforehand, or becomes 'dirty' during oscillation is necessary to minimize controller, PLC can set the rate of the casting process. One of the main friction and sticking of the solidifying strand withdrawal via speed control of methods through which hot metal may shell, and avoid shell tearing, and liquid the withdrawal rolls. The flow of metal become dirty is by oxidation, which steel breakouts, which can wreak into the moulds can be controlled by occurs rapidly at molten metal havoc on equipment and machine two methods: temperatures (up to 1700 °C); downtime due to clean up and repairs. l By slide gates or stopper rods at inclusions of gas, slag or undissolved Friction between the shell and mould is the top of the mould shrouds alloys may also be present. To prevent reduced with mould lubricants such as l If the metal is open-poured, then oxidation, the metal is isolated from the oils or powdered fluxes. Oscillation is the metal flow into the moulds is atmosphere as much as possible. To achieved either hydraulically or via controlled solely by the internal achieve this, exposed metal surfaces motor-driven cams or levers which diameter of the metering nozzles. are covered by the shrouds, or in the support and reciprocate or oscillate the T h e s e n o z z l e s a r e u s u a l l y case of the ladle, tundish and mould, by mould. interchangeable. synthetic slag. In the tundish, any inclusions in the form of gas bubbles, Continuous Casting Start-up, Overall casting speed can be other slag or oxides, or undissolved Process Control and Problems adjusted by altering the amount of alloys may also be trapped in the slag The mechanism of continuous metal in the tundish, through the ladle layer. casting process is shown below in slide gate. The PLC can also set the Figure-4. Starting a continuous casting mould oscillation rate and the rate of A major problem that may occur in machine involves placing a dummy bar, mould powder feed, as well as the continuous casting is breakout. This is essentially a curved metal beam, up spray water flow. Computer control when the thin shell of the strand through the spray chamber to close off also allows vital casting data to be breaks, allowing the still-molten metal the base of the mould.
Details
-
File Typepdf
-
Upload Time-
-
Content LanguagesEnglish
-
Upload UserAnonymous/Not logged-in
-
File Pages5 Page
-
File Size-