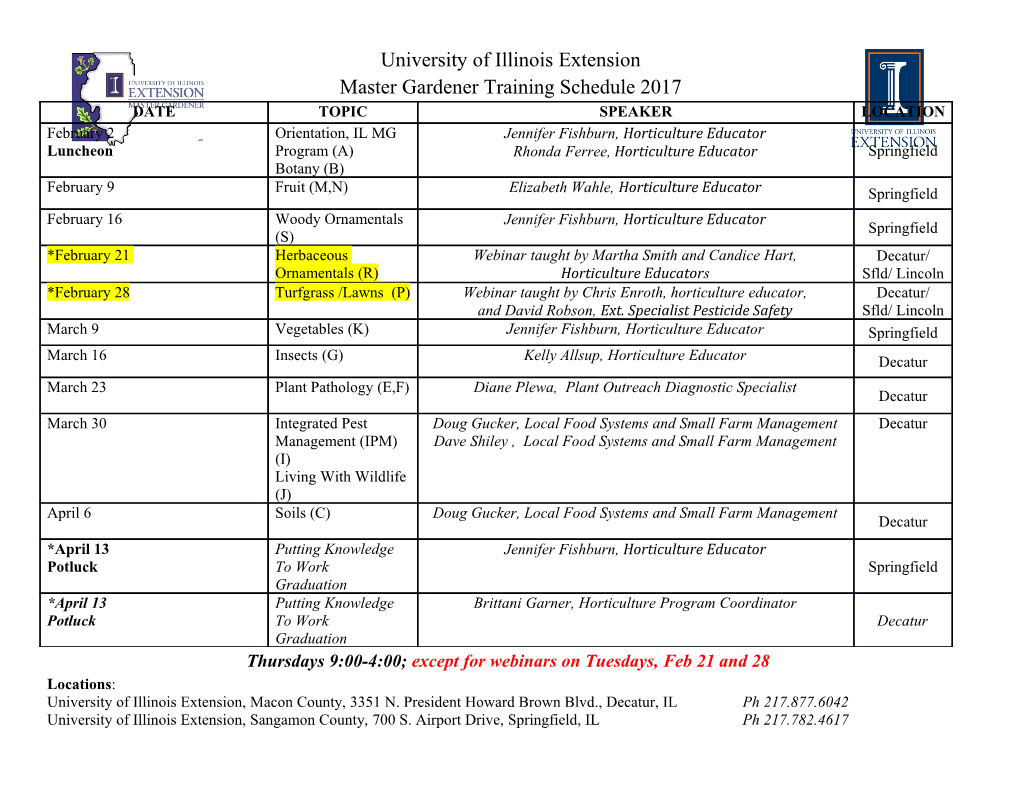
Casting & Welding Engineering (IE 203) Second Year, Industrial Engineering Dept., Faculty of Engineering, Fayoum University Dr. Ahmed Salah Abou Taleb 1 Furnaces 2 Introduction What is a Furnace? • Equipment to melt metals – Casting – Change shape – Change properties • Type of fuel important – Mostly liquid/gaseous fuel or electricity • Low efficiencies due to – High operating temperature – Emission of hot exhaust gases 3 Introduction What are Refractories: Materials that – Withstand high temperatures and sudden changes. – Withstand action of molten slag, glass, hot gases, etc. – Withstand load at service conditions – Withstand abrasive forces – Conserve heat – Have low coefficient of thermal expansion – Will not contaminate the load 4 Introduction Refractories Refractory lining of a furnace arc Refractory walls of a furnace interior with burner blocks 5 Introduction Properties of Refractories • Melting point – Temperature at which a ‘test pyramid’ (cone) fails to support its own weight • Size – Affects stability of furnace structure • Bulk density – Amount of refractory material within a volume (kg/m3) – High bulk density = high volume stability, heat capacity and resistance • Porosity – Volume of open pores as % of total refractory volume – Low porosity = less penetration of molten material 6 Introduction Properties of Refractories • Cold crushing strength – Resistance of refractory to crushing • Creep at high temperature – Deformation of refractory material under stress at given time and temperature • Volume stability, expansion & shrinkage – Permanent changes during refractory service life – Occurs at high temperatures • Reversible thermal expansion – Phase transformations during heating and cooling 7 Introduction Properties of Refractories • Thermal conductivity – Depends on composition and silica content – Increases with rising temperature • High thermal conductivity: – Heat transfer through brickwork required • Low thermal conductivity: – Heat conservation required (insulating refractories) 8 Furnaces for Casting Processes 9 Melting Furnaces Furnace selection? • Operating cost. • Furnace capacity. • Power availability (Heat source). • Type of charge materials. • Composition and Melting point of alloy. • Ease of super heating the metal. • Pollution and noise. • Furnace atmosphere control. 10 Cupola furnace Vertical cylindrical furnace equipped with tapping spout near base 11 Cupolas • Used only for cast irons, and although other furnaces are also used. • Largest tonnage of cast iron is melted in cupolas. • The "charge," consisting of iron, coke, flux, and possible alloying elements, is loaded through a charging door located less than halfway up height of cupola. 12 Charging of Cupolas • Before the blower is started, the furnace is uniformly pre-heated and the metal and coke charges, lying in alternate layers, are sufficiently heated up. • The cover plates are positioned suitably and the blower is started. • The height of coke charge in the cupola in each layer varies generally from 10 to 15 cm. • The requirement of flux to the metal charge depends upon the quality of the charged metal and scarp, the composition of the coke and the amount of ash content present in the coke. 13 Working of Cupolas • The charge, consisting of metal, alloying ingredients, limestone, and coal coke. • Air enters the bottom through tuyeres. The air inflow often contains enhanced oxygen levels. • Coke is consumed. • The charge drops and is melted. • Air is fed into the furnace, • As the material is consumed, additional charges can be added to the furnace • A continuous flow of iron emerges from the bottom of the furnace. • A hole higher than the tap allows slag to be drawn off. 14 Advantages of Cupolas • It is simple and economical to operate. • Capable of accepting a wide range of materials without reducing melt quality. Dirty, oily scrap steel and iron. • Play an important role in the metal recycling industry • Cupolas can refine the metal charge, removing impurities out of the slag. • The continuous rather than batch process suits the demands of a repetition foundry. • High melt rates • Ease of operation • Adequate temperature control • Chemical composition control • Less floor space requirements comparing with those furnaces with same capacity. 15 Limitations of Cupolas • Since molten iron and coke are in contact with each other, certain elements like Si, Mn are lost and others like S are picked up. This changes the final analysis of molten metal. • Close temperature control is difficult to maintain 16 Direct Fuel-Fired Furnaces Small open-hearth in which charge is heated by natural gas fuel burners located on side of furnace 17 Direct Fuel-Fired Furnaces • Furnace roof assists heating action by reflecting flame down against charge • At bottom of hearth is a tap hole to release molten metal • Generally used for nonferrous metals such as copper- base alloys and aluminum 18 Crucible furnace Metal is melted without direct contact with burning fuel mixture. 19 Crucible furnace • Sometimes called indirect fuel-fired furnaces. • Container (crucible) is made of high-temperature steel alloy. • Used for nonferrous metals such as bronze, brass, and alloys of zinc and aluminum 20 Induction Furnaces Uses alternating current passing through a coil to develop magnetic field in metal. 21 Induction Furnaces • Induced current causes rapid heating and melting. • Electromagnetic force field also causes mixing action in liquid metal. • Since metal does not contact heating elements, the environment can be closely controlled, which results in molten metals of high quality and purity. • Melting steel, cast iron, and aluminum alloys. 22 Electric Arc Furnace Charge is melted by heat generated from an electric arc 23 Electric Arc Furnace • High power consumption, but electric-arc furnaces can be designed for high melting capacity. • Used primarily for melting steel. 24 Melting Furnaces Furnaces Electric arc Induction Crucible Cupola Electric Arc Induction Crucible Cupola Materials Steel Steel, C I, Al Non ferrous C I Size Medium Small Small Large Heat source Electricity Electricity Fuel / electricity Coke contact Direct Indirect Indirect Direct Melting rate High Medium Medium Low 25 Furnaces Performance Q • Thermal efficiency of furnace Q • Heat in the stock (Q): QmCP t1 t2 • Heat in fuel consumed for heating the stock (Q’) Q K m Q = Quantity of heat of stock in kCal, Q’ = Heat in fuel consumed for heating the stock in kCal, m = Weight of the stock in kg, Cp= Mean specific heat of stock in kCal/kg oC, o t1 = Final temperature of stock in C, o t2 = Initial temperature of the stock before it enters the furnace in C K = Calorific value of oil kCal/kg m‘ = Fuel consumption kg/hr 26 Charge Calculation 27.
Details
-
File Typepdf
-
Upload Time-
-
Content LanguagesEnglish
-
Upload UserAnonymous/Not logged-in
-
File Pages27 Page
-
File Size-