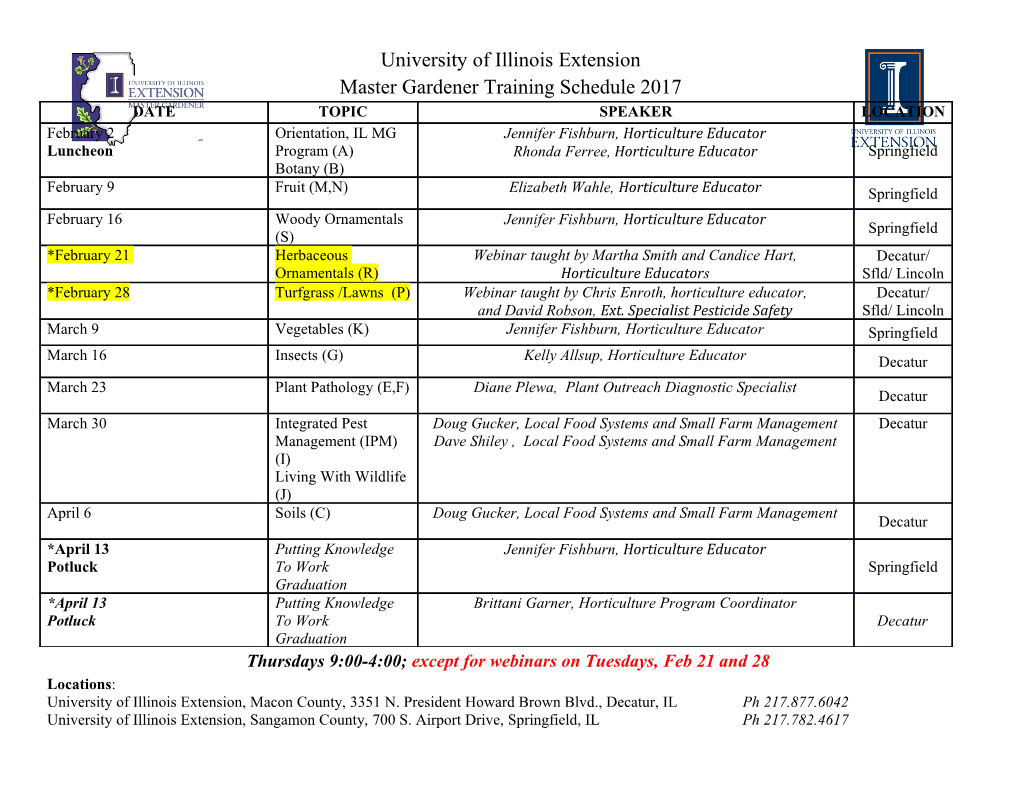
Specialized Tools & Filtration version 5 Specialized Tools & Filtration Table of contents Specialized Tools 2 Riser Cleaning Tools Liner Top Test Tools PUP RISER BRUSH (PRB) 35 WELL COMMISSIONER (WC) 2 RISER CLEANING TOOL (RCT) 36 Casing Cleaning Tools RISER DISPLACEMENT CLEANING TOOL (RDCT) 37 BRISTLE BACK REDRESSABLE 4 BOP Cleaning Tools MultiBACK (MBACK) 5 DUAL-ACTION BYpass SUB JETTING TOOL (DABS-JT) 38 Heavy-Duty RAZOR BACK (HDRB) 6 SINGLE-ACTION BYpass RAZOR BACK (RB) 8 SUB JETTING TOOL (SABS-JT) 39 RAZOR BACK with SHORT TRIP JETTING SUB (STJS) 40 Integral Top Dress Mill (RBTDM) 10 Wellhead Cleaning Tools RIDGE BACK Burr Mill (RBBM) 11 WELLHEAD BRUSHING/JETTING TOOL 41 SWITCHBACK (SWB) 13 Ancillary Tools Circulating Tools BYpass BALL Catcher (BBC) 42 Clutch-Type, Heavy-Duty multi-FUNCTION circulatinG TOOL (MFCT-HD) 14 LANDING SUB (LS) 43 DUAL-ACTION BYpass SUB (DABS) 16 POSI-DRIFT SUB (PDS) 44 Clutch Type, Multi-FUNCTION Customized Tools CirculatinG TOOL (MFCT) 17 BEARING SUB (BS) 45 PORTED BYpass SUB (PBS) 18 DISENGAGEABLE MILL ASSEMBLY (DMA) 46 SINGLE-ACTION BYpass SUB (SABS) 19 Disposable BRISTLE BACK (DBB) 47 WELL COMMANDER 20 PRESSURE SHEAR SUB (PSS) 48 WELL Isolation TOOL (WIT) 23 Debris Recovery Tools Filtration 50 JUNK MUNCHER (JM) 24 Completion Fluids Filtration 50 MAGNOSHOE (MSHOE) 25 DE Filtration Units plate and frame skid 54 MAGnostar (MSTAR) 26 Equipment 58 MAGnostar Heavy Duty (MSTAR HD) 27 Filter Press Package (Unit) 59 MAGNOSWEEP II (MSWEEP II) 28 Filter FLOC 59 SWITCHBACK MAGNET (SWBM) 29 SAFE-FLOC I 60 WELL Patroller (WP) 30 SAFE-FLOC II 61 WELL Patroller 500 Series 32 WELL PROTECTOR (WPR) 33 WELL SCAVENGER (WS) 34 1 Specialized Tools & Filtration WELL COMMISSIONER (WC) Specialized Tools: Liner Top Test Tools The WELL COMMISSIONER* tool How it works from M-I SWACO is unique in that it is The WELL COMMISSIONER tool is run designed to allow inflow and negative on the drillstring, spaced out to land on tests to be carried out on a liner overlap the liner-top Polished-Bore Receptacle and the liner shoe track on the same (PBR) when the cleanout string is at trip as the wellbore cleanup. It can final depth. The integral RAZOR BACK* also be used to perform an inflow or lantern cleans ahead of the packoff negative test on the liner top and liner element and prepares the area in which shoe track at any time during the life of the tool itself is to be set. The bypass the well. Regardless of when the tool under the element is open while running is run, it results in significant savings in in hole and allows high-rate circulation rig time compared to other methods of without the need for fluids to go around performing an inflow test. Significant the outside of the element (Figure 1). reduction in oil-contaminated seawater or brine volumes generated is also possible where OBM is in use. Advantages Weight The WELL COMMISSIONER tool gauge eliminates the need for a controlled displacement of the entire well to Safety trip lower density fluid through the choke button with the blowout preventers closed. It also eliminates a dedicated run with a Figure 1. Pick up off the liner and begin retrievable packer to perform the test, circulating and conditioning the mud. saving significant rig time. Positive tests on the casing or liner can also Specialized Tools: Liner Top Test Tools: WELL COMMISSIONER (WC) Tools: Test Liner Top Specialized Tools: be carried out. Significant reduction in waste volumes of contaminated fluids is also made. Features Advantages ■■ One-piece mandrel ■■ Saves rig time and improves ■■ Integral RAZOR BACK effectiveness of cleanup (scraper) lantern ■■ Simple to operate ■■ Integral liner-top dress mill ■■ Allows inflow/negative test on same ■■ Internal bypass under packoff element trip as cleanup ■■ Standard tool rated to 5,000 psi ■■ Allows drilling and milling with tool (345 bar) differential up to in string 302°F (150°C) ■■ Reduces waste volumes ■■ High-pressure tool rated to 7,000 psi (483 bar) differential up to 302°F (150°C) 2 Specialized Tools & Filtration Operation When a WELL COMMISSIONER tool is run in conjunction with an MFCT unit, When the integral liner-top dress mill at least 10,000 lb (4,536 kg) effective lands on the PBR, it can be used to dress string weight (tension) should be off the PBR top if required. A tieback mill available below the tool when it is can be run below the tool to clean inside at operating depth. If this is not the the PBR. case, consideration should be given to A low-density water- or oil-base fluid is increasing the shear rating on the then pumped into the upper portion of MFCT unit or running a Clutch-Type, the drill pipe to reduce the hydrostatic Figure 2. Slowly bleed down the work-string Heavy-Duty MFCT unit or adding pressure on the liner overlap and liner pressure to begin the inflow test. drill-collar weight to the string below. shoe track. While back pressure on the It is recommended that a tie back mill is drill pipe is held, the tool is set down on The Multi-FUNCTION CirculatinG run below the WELL COMMISSIONER the liner top, the packoff element is set TOOL* (MFCT) can be run above the tool to polish the inside of the tieback and the bypass closed. Back pressure liner top to boost circulation rates. receptacle of the PBR. This reduces the bleed-off is the inflow test performed by risk of a cement sheath, or other debris monitoring for an increased pressure in Operating Parameters buildup, preventing the tool from seating the drill pipe, indicating inflow (Figure 2). If an MFCT unit is proposed in the same on top of the tieback recep tacle or PBR. When the test is complete, repressurize string as the WELL COMMISSIONER Maximum running-in-hole/pulling-out- to the previous back pressure, pick up tool, M-I SWACO will perform a torque of-hole speed is 150 ft/min (46 m/min). to release the packoff element and open and drag analysis to verify the effective The required inflow test pressure can the bypass. The normal cleanup and tension in the string at the liner top only be achieved, if the resulting loading displacement to completion fluid can while tripping in hole at 150 ft/min on the liner hanger system is within now be conducted. (46 m/min) without rotation. operating guidelines. Operating parameters Maximum Maximum Tool (casing) Maximum rotating rotating speed in compression at tool size, in. speed in tension, rpm compression, rpm when rotating, lb (kg) 7 – 85⁄8 100 60 5,000 (2,268) 95⁄8 – 10¾ 120 90 10,000 (4,536) These are general guidelines only and are subject to review, if required, for individual circumstances. 3 Specialized Tools & Filtration BRISTLE BACK REDRESSABLE Specialized Tools: Casing Cleaning Tools The BRISTLE BACK REDRESSABLE* Applications brush tool utilizes a unique lantern The BRISTLE BACK REDRESSABLE design that provides greater bristle brush is run as an integral part of the life. This lantern design also allows drillstring to brush the casing ID clean easy, remote location redressing when as the pipe is run in hole. It can be run required, saving time and delivering as part of most drilling/milling/ polishing a higher level of service. The tool’s assemblies and can be rotated and effective, robust, and flexible design reciprocated without damage to either allows for complex, precompletion/ the casing or the tool. Drill-Stem Test (DST) and workover cleanup operations. Features Advantages ■■ Brush cleaning life prolonged during ■■ Scouring action ensures a clean rotation pipe wall ■■ Self-centralizing, flexible-brush ■■ Non-rotating stabilizer sleeves and lantern lantern avoid wear or damage to the ■■ Available in all common casing/ casing and the tool bristles during liner sizes pipe rotation ■■ Supplied with drill-pipe box-up/ ■■ Self-centralizing lantern distributes pin-down connections cleaning force equally for all hole inclinations ■■ Brush pads can easily be replaced on location ■■ Removes mud solids, cement sheath and pipe scale ■■ Saves time and inventory requirements Specialized Tools: Casing Cleaning Tools: BRISTLE BACK REDRESSABLE Casing Cleaning Tools: Specialized Tools: 4 Specialized Tools & Filtration MultiBACK (MBACK) Specialized Tools: Casing Cleaning Tools The MultiBACK* (MBACK) combination How it works casing cleaning tool merges the The MultiBACK tool is run in the well latest proven magnet, scraper, and as a conventional wellbore preparation brush technologies into a simplified tool on the workstring. The lanterns for and rugged tool that can be used on the scraper and brush unit are flexible, wellbore preparation trips. The flexibility non-rotating, and provide the force to of the component arrangement provides Casing Cleaning Tools: Specialized Tools: contact and clean 360° of the casing’s numerous options to customize the tool internal diameter. Its self-centralizing for a specific application. design ensures equal cleaning force Applications at all angles of inclination. The magnet section comprises a mandrel with The modular design of the MultiBACK fins that allow for large flow channels tool allows it to be configured for between them. The magnets are specific applications or requirements. installed on the inside faces of the The MultiBACK tool has an integral fins using a method for retaining the magnet section to capture ferrous individual magnets so that the debris is debris, scrapers to dislodge difficult- collected in the high volume channels. to-remove debris, and brushes to The magnet section is integral in the tool disturb the sheath and any other fluid while the scraper and brush sections build-up on the inner wall of the casing MU are interchangeable.
Details
-
File Typepdf
-
Upload Time-
-
Content LanguagesEnglish
-
Upload UserAnonymous/Not logged-in
-
File Pages64 Page
-
File Size-