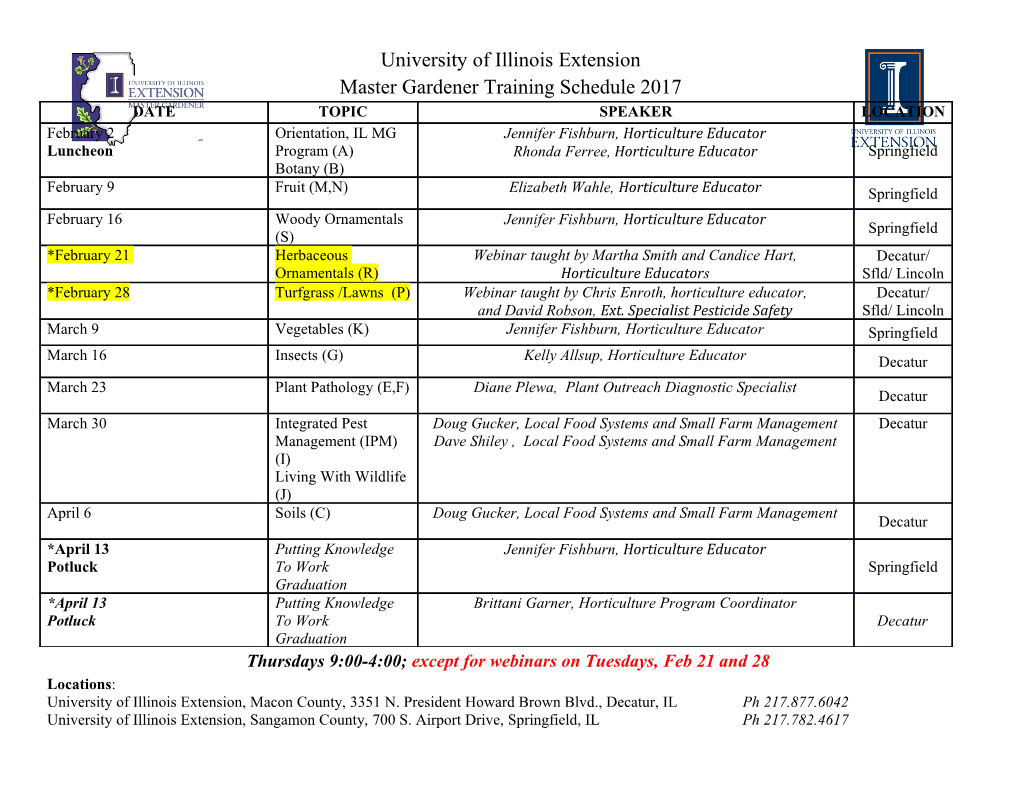
PSFC/JA-16-60 Linear servomotor probe drive system with real-time self-adaptive position control for the Alcator C-Mod tokamak D. Brunner, A.Q. Kuang, B. LaBombard, and W. Burke October 2016 Plasma Science and Fusion Center Massachusetts Institute of Technology Cambridge MA 02139 USA This work was supported by DoE Contract DE-FC02-99ER54512 on Alcator C-Mod, a DoE Office of Science user facility. Reproduction, translation, publication, use and disposal, in whole or in part, by or for the United States government is permitted. Linear servomotor probe drive system with real-time self-adaptive position control for the Alcator C-Mod tokamak D. Brunner, A.Q. Kuang, B. LaBombard, and W. Burke [email protected] Plasma Science and Fusion Center, Massachusetts Institute of Technology, Cambridge, Massachusetts, 02139, USA A new servomotor drive system has been developed for the horizontal reciprocating probe on the Alcator C-Mod tokamak. Real-time measurements of plasma temperature and density—through use of a mirror Langmuir probe bias system—combined with a commercial linear servomotor and controller enables self-adaptive position control. Probe surface temperature and its rate of change are computed in real time and used to control probe insertion depth. It is found that a universal trigger threshold can be defined in terms of these two parameters; if the probe is triggered to retract when crossing the trigger threshold, it will reach the same ultimate surface temperature, independent of velocity, acceleration, or scrape-off layer heat flux scale length. In addition to controlling the probe motion, the controller is used to monitor and control all aspects of the integrated probe drive system. 1 Introduction Plasma probes, i.e., measurement instruments that make direct contact with the plasma, have been one of the primary tools to study boundary plasma physics in experimental fusion reactors. Probes enable excellent temporal resolution (up to ~1 MHz with present technology1) and spatial location (sub- millimeter) of many quantities of interest: ion and electron temperatures, plasma density, plasma potential, flow velocities, and magnetic field. Reciprocating systems allow probes to measure and survive plasma in conditions too intense for stationary probes. Fast reciprocation of the probe into and out of the plasma limits the probe exposure to high heat flux. The reciprocations are typically fast enough to take advantage of ‘inertial cooling’, i.e., a situation in which only a thin surface layer is heated. In this case, active cooling of the probe will not enable deeper scanning. It is desirable to scan the probe as deep as possible. However, the exponentially increasing heat flux profile a tokamak scrape-off layer presents a considerable challenge, requiring accurate control of the probe trajectory – in particular the insertion depth. There are two effects that limit scan depth: (1) Melting the probe should be avoided. Melting can cause the probe tip to deform (making the collection area and thus the inferred density uncertain), shorting of the electrode (rendering it useless), and termination of the tokamak plasma (through a large impurity injection). (2) Even before melting, as the surface temperature is raised the probe can undergo thermionic electron emission. The electrons emitted from the probe reduce the sheath potential (rendering plasma potential measurements uncertain) and increase the net current collected during ion saturation measurement (making plasma density measurements uncertain). Fortunately, enhanced electron emission occurs at a surface temperature that is significantly below melting temperature. Thus, the onset of electron emission can often be used as a marker to identify the maximum useful scan depth without irreversible damage to the probe. Reciprocating probe systems have been implemented and used on many plasma physics experiments. A comprehensive list would include nearly every magnetic fusion experiment. For a partial list see Ref. 2. Most systems have relied on a pneumatic or hydraulic drive to reciprocate the probe into and out of the plasma. Pneumatic/hydraulic drives have the advantage of being a simple system with few components. 1 They are relatively easy to implement and can readily achieve velocities (~1 m/s) as well as accelerations (>100 m/s2) that enable effective operation. The major disadvantage of pneumatic/hydraulic systems is the control of their ultimate plunge depth. This is typically done by trial and error. The plasma boundary shape from a previous plasma pulse is taken into account and the position of the pneumatic cylinder that drives the probe is adjusted (typically with a slow stepper motor) such that it scans deep enough to measure interesting plasma physics but not so deep as to destroy the probe. In order to minimizing the dwell time at the probe’s end-of-stroke (during maximum heat flux), the C-Mod pneumatic systems additionally engage a mechanical return spring that provides a large turn-around acceleration (~600 m/s2). Some other systems rely solely on toggling air or hydraulic pressure to the opposite side of the cylinder to change probe direction, resulting in a much lower turn-around acceleration and shallower scan depth into the plasma. Neither of these pneumatic systems have sufficient time response for precise, real-time control of probe position in narrow scrape-off layers. Electromagnetic systems, however, can have sufficient performance for real-time control. Electronic circuits can respond fast enough (<1 ms) to turn the probe around in time. Electromagnetic control of probe movement can been implemented in three ways: (1) Using standard servomotors (either linear3 or rotary4) with a series of permanent magnets to provide a background field; (2) Using the magnetic field of the experiment to provide the background field5–10; (3) Using pulsed electromagnets to induce currents in a ‘drive hoop’11. In first two cases a current is passed through a coil or series of coils and the Lorentz force between the current in the coil(s) and the background magnetic field provides the acceleration. In the third case the image currents in the ‘drive hoop’ act against the pulsed electromagnets. Both an electromagnetic, the so-called ‘pecker-probe’, and a hydraulic reciprocating probe with real- time control were operated on Tore Supra10,12. The output of a real-time calculation of the magnetic equilibrium was used to control the ultimate depth of each probe scan. This is not a viable technique for use on Alcator C-Mod; the magnetic equilibrium reconstruction of the plasma boundary and the probe- measured boundary plasma can drift over the course of a plasma shot (it is presumed that this is due to currents redistributing in the copper toroidal field coils as they heat up). That is, for an equilibrium with a constant boundary plasma position at the outer plasma-wall gap, the probe-measured plasma temperature and density profile can drift away from the probe. The profiles can drift a few millimeters— a few heat flux decay lengths. That size of variation in the actual plasma position relative the calculated equilibrium does not provide for a useful feedback technique. Since probe insertion depth is practically limited by surface temperature, a better approach is to control the probe depth based on real-time measurements of probe surface temperature. Experiments indicate that this should be feasible: an IR camera was used to measure the heat flux on a reciprocating probe on ASDEX-U13 and surface thermocouples14 could be integrated into a probe. A less direct, but perhaps simpler solution, would be to use real-time measurements of the plasma quantities at the probe tip combined with a thermal model of the probe to calculate surface temperature. The Mirror Langmuir Probe1 (MLP) bias system provides real-time measurements of plasma temperature and flux. An MLP is an analog computer that quickly switches (~3 MHz) through three bias states of a Langmuir probe I-V (current-voltage) trace. The system optimizes each bias voltage through use of circuitry that mirrors the Langmuir probe response in the plasma. A by-product of this is real-time 2 outputs proportional to the three fit parameters to the I-V: ion saturation current (Isat, proportional to the plasma flux), electron temperature (Te), and floating potential (Vf, related to the plasma potential through sheath theory). To complement the MLP analog computer we have developed an analog computer that ‘solves’ a thermal model of the Langmuir probe body, outputting the surface temperature evolution of the probe head in real time. It uses real-time MLP Te and Isat measurements to compute the incident plasma heat flux, based on a simple sheath heat flux model. The scanning probe system must be capable of diagnosing a wide variety of scrape-off layer plasma profiles. As discussed below, this makes it impractical to use surface temperature alone as a parameter to trigger a turn-around response. Fortunately, the scrape-off layer profiles are close to exponential. In this case, a fairly reliable estimate of the surface temperature at a future time can be made based on the current temperature and its time derivative. Using these two parameters, we’ve found a robust, universal control algorithm that is able to trigger the probe’s turn-around such that its surface temperature stays below a specified peak temperature. This paper is organized as follows. Section 2 explores the optimization of probe acceleration and velocity for maximizing the depth of probe scan into the plasma while ensuring controllability. A universal control algorithm is developed in Section 2. Section 3 describes the mechanical design and implementation of the linear servomotor system. Section 4 covers the control (software and electrical) interface, including the surface temperature analog computer. Section 5 describes operational results of the linear servomotor drive system on Alcator C-Mod. 2 Thermal performance The thermal performance is the crucial concern when considering designing a reciprocating probe system with feedback control.
Details
-
File Typepdf
-
Upload Time-
-
Content LanguagesEnglish
-
Upload UserAnonymous/Not logged-in
-
File Pages26 Page
-
File Size-