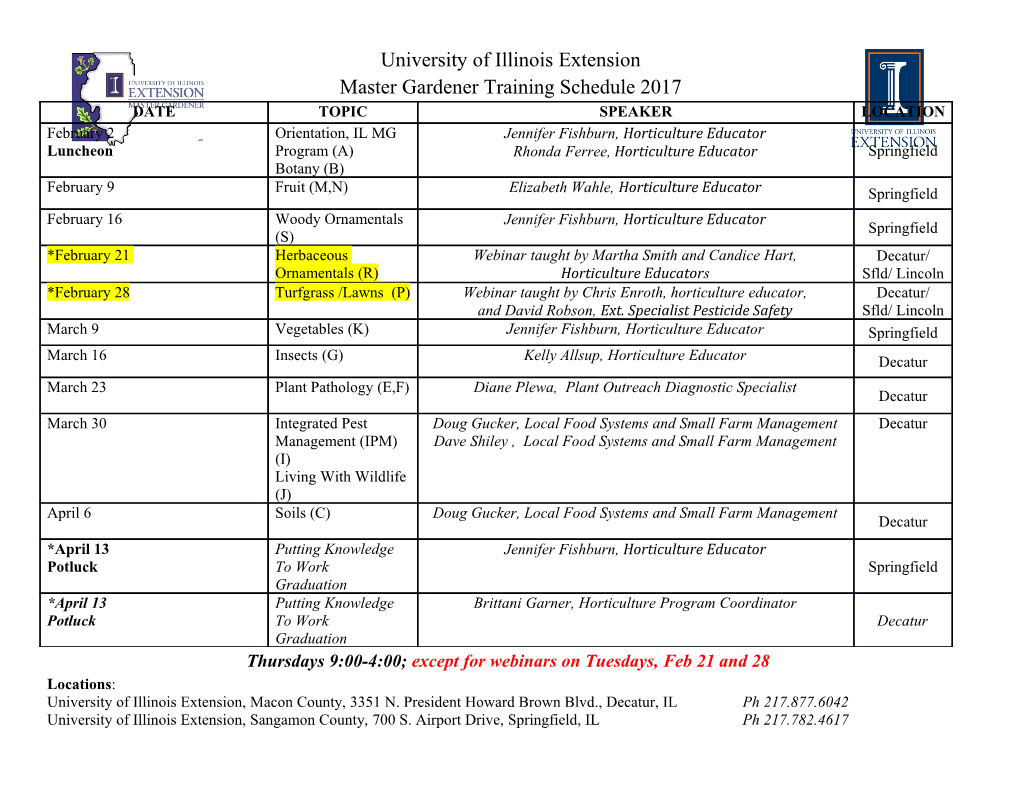
Determination of Metal Quality of Aluminium and Its Alloys by DERYA DISPINAR A thesis submitted to The University of Birmingham For the degree of DOCTOR OF PHILOSOPHY School of Metallurgy and Materials The University of Birmingham January 2005 University of Birmingham Research Archive e-theses repository This unpublished thesis/dissertation is copyright of the author and/or third parties. The intellectual property rights of the author or third parties in respect of this work are as defined by The Copyright Designs and Patents Act 1988 or as modified by any successor legislation. Any use made of information contained in this thesis/dissertation must be in accordance with that legislation and must be properly acknowledged. Further distribution or reproduction in any format is prohibited without the permission of the copyright holder. Abstract Aluminium alloy castings are being used increasingly in safety-critical applications in the automotive and aerospace industries. To produce castings of sufficient quality, it is, therefore, important to understand the mechanisms of the formation of defects in aluminium melts, and important to have a reliable and simple means of detection. During the production of aluminium ingots and castings, the surface oxide on the liquid is folded in to produce crack-like defects (bifilms) that are extremely thin, but can be extremely extensive, and so constitute seriously detrimental defects. However, the presence of bifilms has not been widely accepted, because there has been no single metal quality test that has been able to resolve features that are only nanometres, or sometimes micrometres, in thickness. In the past, porosity has usually been held solely responsible for most failures in aluminium alloys, and hydrogen has been blamed as the actual cause. In this work it has been found that bifilms are the initiator and hydrogen is only a contributor in the porosity formation process. For the first time, evidence is presented for the contribution of air (or perhaps more strictly, residual nitrogen from air) as an additional gas, adding to hydrogen in pores in cast Al alloys. The Reduced Pressure Test (RPT) is used which is a simple and widely known test, is cost effective and involves no complicated equipment or consumables, thus recommending it for implementation on the foundry floor. Nevertheless, the discriminating use of the RPT clearly reveals the existence of bifilms, and the effect of hydrogen on porosity formation. On this basis, several Al-Si based alloys were studied: LM0 (99.5% Al), LM2 (Al-11Si), LM4 (Al-5Si-3Cu), LM25 (Al-7Si-0.4Mg), LM24 (Al-8Si-3CuFe), LM27 (Al-6Si-2Cu). A quality index -Bifilm Index - is introduced to quantify the results of the reduced pressure test which helps to asses the aluminium melt quality in best means. In addition, mechanical tests were carried out to correlate bifilm index with mechanical properties. The oxide content of recycled aluminium alloys has been a long-standing and serious problem. This thesis reports the use of the RPT test developed in this study to an industrial remelting facility that has resulted in significant benefit. Acknowledgement It is the greatest honour to be able to work under supervision of Professor John Campbell. I am grateful to be one of the luckiest persons who had a chance to work with him. I am thankful and gratified for all of his help, assistance, inspiration and guidance on the all aspects. I would like to thank Professor Nick R. Green for his support and supervision. I thank the University of Istanbul, Metallurgy and Materials Engineering, Head of Department, Prof. Dr. Ibrahim Yusufoglu, for his encouragement to help me begin my postgraduate study in University of Birmingham. Thanks to all of my colleagues, the research assistants in the department, particularly Dr. Cem Kahruman in Istanbul. I would have to acknowledge Higher Education Council of Turkey, for supporting my research. I would like to acknowledge the financial support of Norton Aluminium and particularly their assistance in the use of facilities in the foundry. The research was also partially supported by University of Birmingham. I would like to thank Adrian Caden for his assistance during the experiments and rest of the IRC group for their warm and kind friendship. Although we could not finalise this project together, I would like to thank to Dr. Simon Fox for his effort and support on the start of my thesis. I would like to express my gratitude to Nazım Karadağ for his commitment and continued support as my best friend. My mom and dad, and my whole family; there are no words to express my feelings for your never-ending support and belief in me. Above all, I would like to express my deepest gratitude to my wife and best friend Muzi, for her love and support and everything during this work and ever. TABLE of CONTENTS CHAPTER 1 INTRODUCTION ............................................................................................... 1 CHAPTER 2 LITERATURE REVIEW...................................................................................... 4 2.1 History of Casting and Aluminium ....................................................................................................5 2.1.1 Casting Processes.................................................................................................................................6 2.2 Metal Quality ...........................................................................................................................................8 2.2.1 The Dissolution of Hydrogen.............................................................................................................9 2.2.2 Formation of Oxide Film ..................................................................................................................10 2.3 The Concept of Surface Entrainment: Bifilms ................................................................................14 2.3.1 Incorporation of Surface Films into Melts .....................................................................................15 2.4 Compacting and Unfurling (Ravelling and Unravelling) of Bifilms...........................................15 2.5 Porosity Phenomena .............................................................................................................................16 2.5.1 Nucleation ..........................................................................................................................................16 2.5.2 Growth ...............................................................................................................................................18 2.5.3 The New Approach to Pore Formation .........................................................................................18 2.6 Porosity Types .......................................................................................................................................20 2.6.1 Shrinkage Porosity ............................................................................................................................21 2.6.2 Gas Porosity ......................................................................................................................................22 2.7 Factors Affecting Porosity....................................................................................................................22 2.7.1 An Inrease in the Hydrogen Content of the Melt .........................................................................23 2.7.2 An Increase in the Entrained (exogenous) Inclusion Content ....................................................23 2.7.3 Oxide Structure .................................................................................................................................23 2.7.4 Alloying ..............................................................................................................................................24 2.7.5 Cooling Rate ......................................................................................................................................24 2.7.6 Intermetallics .....................................................................................................................................24 2.8 Measurement of Metal Quality...........................................................................................................25 2.8.1 Inclusion Detection Tecniques ........................................................................................................26 2.8.1.1 LIMCA (Liquid Metal Cleanliness Analyser) ......................................................................26 2.8.1.2 PoDFA – PREFIL (Porous Disk Filtration Analysis) ..........................................................26 2.8.1.3 Ultrasonic .................................................................................................................................27 2.8.1.4 Summary of Quality Assessment Tecniques .......................................................................27 2.8.2 Reduced Pressure Test (RPT) ..........................................................................................................28 2.9 Secondary Remelting - Recycling ......................................................................................................29 2.9.1 Melting ...............................................................................................................................................30 2.9.1.1 Rotary Furnace ........................................................................................................................30
Details
-
File Typepdf
-
Upload Time-
-
Content LanguagesEnglish
-
Upload UserAnonymous/Not logged-in
-
File Pages130 Page
-
File Size-