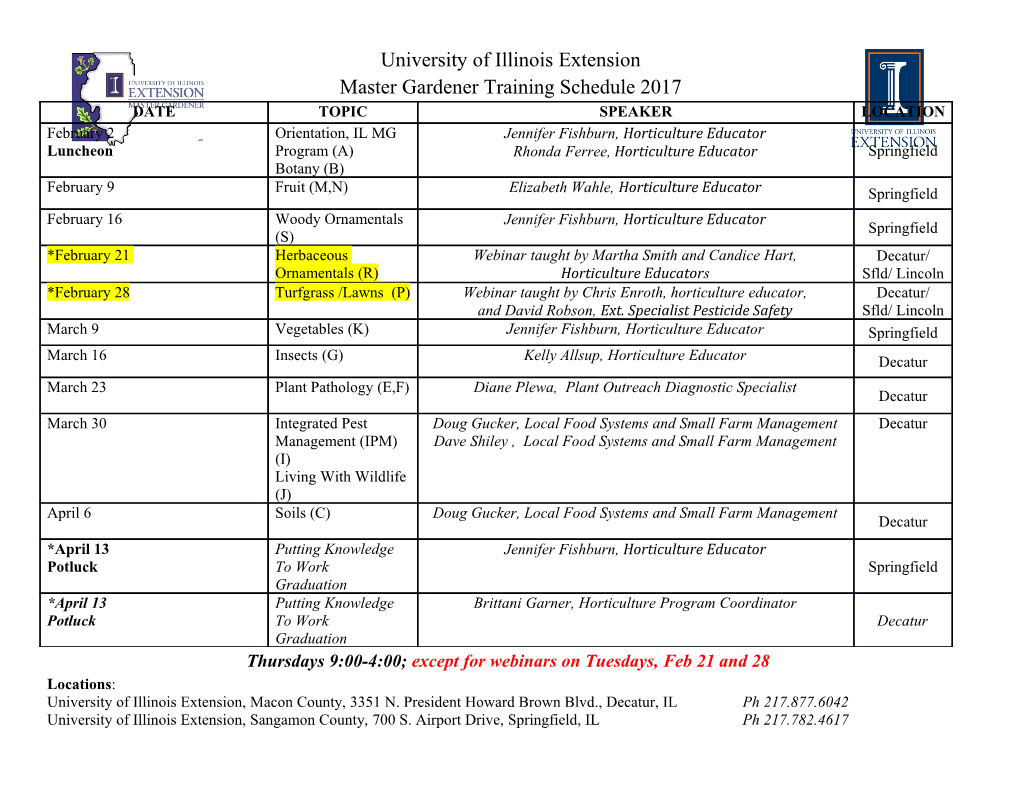
Purdue University Purdue e-Pubs International Compressor Engineering Conference School of Mechanical Engineering 1974 Application of Basic Thermodynamics to Compressor Cycle Analysis R. G. Kent Allis Chalmers Corporation Follow this and additional works at: https://docs.lib.purdue.edu/icec Kent, R. G., "Application of Basic Thermodynamics to Compressor Cycle Analysis" (1974). International Compressor Engineering Conference. Paper 135. https://docs.lib.purdue.edu/icec/135 This document has been made available through Purdue e-Pubs, a service of the Purdue University Libraries. Please contact [email protected] for additional information. Complete proceedings may be acquired in print and on CD-ROM directly from the Ray W. Herrick Laboratories at https://engineering.purdue.edu/ Herrick/Events/orderlit.html APPLICATION GF BASIC THERMODYNAMICS TO COMPRESSOR CYCLE ANALYSIS Richard G. Kent P.E. (Reg. N, J., PA) Allis Chalmers Corporation, Milwaukee, Wisconsin INTRODUCTION Discharge Volume: This paper looks at the basic steps in compressor V2 "' w X R X T "' 1 X 53,3 X 610 operation with examples showing their relation to pl 144 X 29,4 the language of thermodynamics textbooks. 7.68 ft. 3 The various types of compressors: centrifugal, One Complete Cycle Using the Mechanical Approach axial, rotary, reciprocating, helical screw, and others, differ considerably in construction and Here the events during one compressor cycle would means of compression, nevertheless, they all have be in terms of how many foot pounds of work the the same common threefold task to perform upon the crankshaft must provide for each one of these steps gas between suction and discharge flanges. in a complete cycle, This approach will differ from the textbook, heat balance approach for cal­ 1. Suction - Containing the gas witHin the com­ culating work, but the net result must be the same pressor. in each case, 2. Compression - Raising the gas pressure to dis­ a. Crankshaft work during suction stroke. charge pressure. Because there is no difference in pressure between the top and bottom sides of the piston, there is no 3. Discharge - Moving the compressed gas into the crankshaft work during the suction stroke. discharge line, b. Compression work. To understand these three steps in detail, let's At the beginning of compression the pressure on consider a single acting frictionless piston and both the top and bottom of the piston is the same. cylinder operating with the following conditions: In our calculations, absolute air pressure values are used to measure the force resisting upward pis­ Cylinder capacity at inlet conditions: 1 pound of ton movement, therefore, we must also take into dry air. account the opposite force provided by atmospheric pressure in the crankcase. Thus, the total work 2 to compress the air is equal to the sum of crank­ Inletpressure: p1 14.7lbs./in. shaft work plus the work resulting from atmospheric 2 Discharge pressure: p 29.4 lbs./in. pressure on the bottom area of the piston. Since 2 we assumed the piston is frictionless and no heat Inlet temperature: is added to, or removed from, the confined air be­ ing compressed, between work and internal energy is: From th5.s data we can calculate: Work Expressed In BTU Inlet Volume: lb. of air Where: v1 "' wt. x R x T 1 X 53.3 X 500 pl 144 X 14,7 L1u "'~hange in internal energy, BTU per lb. "'12.6 ft. 3 Ll T Change in air temperature, 0 Further, we'll initially assume no heat is added to, °F or R or removed from the cylinder during these three steps - this is called adiabatic compression, and Cv Specific heat at constant volume would result in the following temperature and volume. (.172 BTU for each lb. of dry air) ~ Discharge Temperature (Adiabatic): We'll emphasize here that internal energy is strict­ T k-1 ly a function of temperature and it is unrelated to k other gas properties. Thus: 291 1. Total work of compression = .172 (610 - 500) rather than on the air. Starting with air in the inlet line, we'll review the same fundamental steps = 18.9 BTU of compressor operation. 2. Work supplied by atmospheric air in the crank­ a. Total energy or enthalpy (h) in the intake line case. h "'_internal energy and potential energy Work (BTU) = PSIA x Piston Area x Piston Travel x Sq. In. h (BTU) "' CvT + pv x 144 144 Sq. Ft. TIE Ft. Lb, 778 BTU = .172 X 500 + 14.7 X 144 X 12.6 = PSIA x (Initial ft. 3 - Final rt.3) 778 "' 120.3 BTU "'14.7 X (12.6 7.68) X 144 TIE b. Work done by the air during suction stroke. 13.4 BTU The minus sign-will show that work was done by, rather than on, the air. 3. Thus, work supplied by crankshaft, to compress the air: Total Compression Work - Work Provided bv Atmos. Air ~ PSIA (Initial volume - Final volume x Crankshaft Work 144 778 c. Work to push the air out of the cylinder. 14.7 X (0-12.6) X 144 778 1. Total work = PSIA x (Initial - Final volume) x -34.3 BTU X 144 m c. Work done on the air during compression 29.4 X (7.68 - 0) X 144 Work (BTU) = .172 (610 - 500) 778 = 18.9 BTU "' 41.8 BTU d. Work done ~ the air during discharge 2. Work supplied by atmospheric air in the crank case. Work (BTU) 14.7 X (7.68 - 0) X 144 778 = 29.4 X 7.68 X m144 "' 20.9 BTU = 41.8 BTU 3. Work supplied by crankshaft to push the air out of the cylinder. e. Total energy or enthalpy in the discharge line 41.8 - 20.9 "' 20.9 h at inlet + the net work on the air = h at discharge d. Summing up the work supplied by the crankshaft 120.3 - 34.3 + 18.9 + 41.8 = 146.7 BTU for one complete revolution. Check: Work during: Suction (o) Compression (5.5) h = .172 X 610 + 144 (29.4 X 7.68) 146.7 BTU + Discharge ~20.9) 778 Net crankshaft work 26.4 BTU) And : Change in EnthalFY : Now the Textbook Way! 146.7- 120.3 = 26.4 BTU Consider the same problem with the thermodynamic Therefore, the compressor has increased the air's textbook heat balance approach where changes in total energy by 26.4 BTU which is equal to the enthalpy (i.e., the sum of internal and potential net work done by the crankshaft in our first ap­ energy) are calculated, Calculations can be con­ proach. This is obvious, for when there is no siderably simpler than the previous example by friction or heat flow into, or out of the air, all omitting the effect of crankcase pressure, provid­ the work done by the crankshaft must be absorbed ing we treat the suction stroke as work done by, by the air. Accordingly when we summarize and 292 simplify the work of suction, compression, and from the gas being compressed. This is commonly discharge the following equation for compressor done with fins, cooling water jackets, or spray v1ork results: injection. Using the conditions of our original example, we'll cool the air. When the air just reach~s discharge line pressure, we'll stop the l X 144 piston and cool the cylinder unitl the air tem­ rn perature reaches inlet air temperature. Again, -j Charles' Law enters the picture with a resulting drop in pressure to; The math involved in transforming the three steps of the compressor process into this equation, for 29.4 x 500 or 24.1 PSIA adiabatic compression is readily available in most hlo thermodynamic texts. Our object here is primarily to show the meaning of the three factors which Now we'll restart the compressor for the two steps form the equation. required to complete the cycle: a. Compress the air from 24.1 back up to 29.4 PSIA Side Issues, Friction and Cooling k 236 Most shop men take a dim view of explanations Resulting NewT T (p2) K=I ~ 500 ~2t.4~ · limited to frictionless devices such as we have (pl) 2 .l assumed. Thus, we'll show how the basic process changes with the inevitably present heat of fric- "tion. Friction simply results in the addition of "' 530° heat to the air being compressed, thus, we'll visualize its effects by stopping the piston at Additional work of compression the completion of its intake stroke and add heat through the cylinder walls. In accordance with Cv (T2 - T 1) BTU Charles' Law, the absolute pressure of the con­ fined air will rise in direct proportion to the Or .172 (530 - 500) 5.16 BTU rise in absolute temperature. Hence, if we add enough heat the air pressure within the cylinder Then v 12.6 X 530 X 14.7 will reach discharge line pressure even though no 500 ~ work of compression has been done by the piston. We can then restart the compressor and complete the "' 6.67 ft.3 cycle by discharging the air which is already at discharge line pressure. At first glance, it ap­ This is the volume of compressed air which must be pears that the addition of heat would result in pushed into the discharge line. less total compressor work since no piston work was required to compress the air. However, recall­ b. Work of discharging the compressed air ing that total horsepower is the sum of suction, compression and discharge work, we find: P (Initial Vol. -Final Vol.) x 144 2 m Total Compressor Work ~ Suction Work + Compression Work* + Discharge Work ~'l (Initial Vol.
Details
-
File Typepdf
-
Upload Time-
-
Content LanguagesEnglish
-
Upload UserAnonymous/Not logged-in
-
File Pages7 Page
-
File Size-