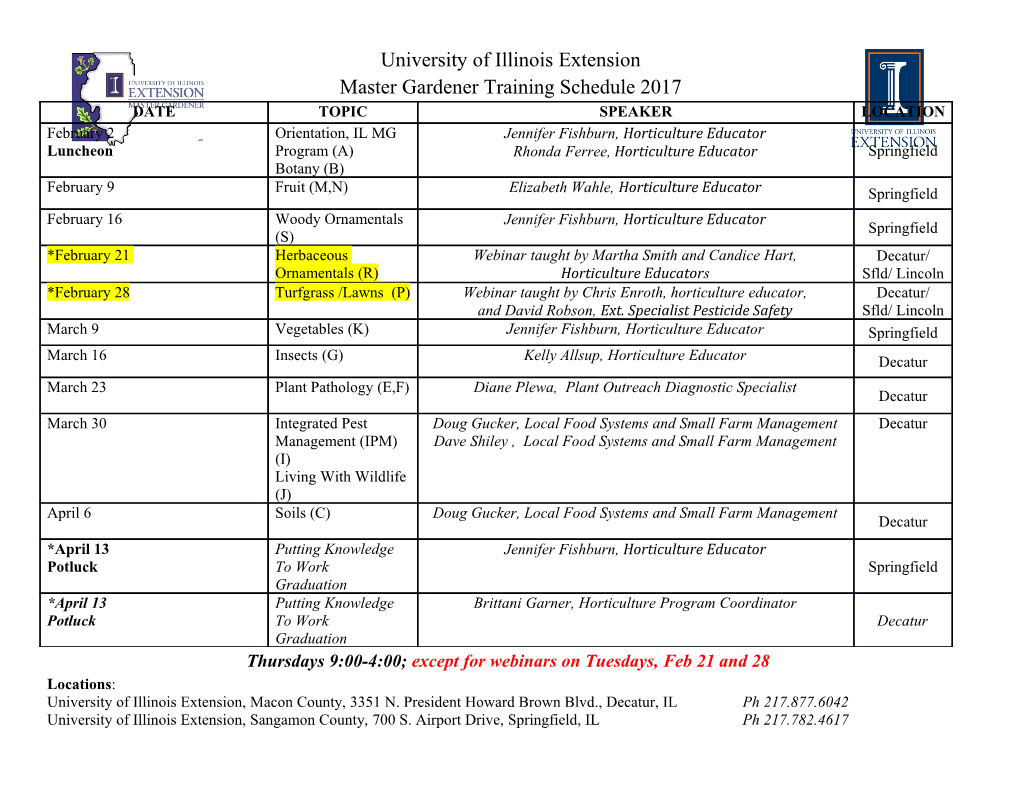
SWITCHED RELUCTANCE MOTOR WITH 16 STATOR POLES AND 12 ROTOR TEETH J. Wolff H. Späth Elektrotechnisches Institut, Universität Karlsruhe, Germany Abstract: The Elektrotechnisches Institut of the University Karlsruhe has developed, optimized and manufactured a Switched Reluctance Drive with power converter and control engineering according to the latest scientific findings. The motor was constructed for the rated output of about 25 kW and for industrial applications. Trondheim The nominal speed of the test Switched Reluctance Motors is 1500 revolutions per minute. The drive works in all for quadrants and was designed for applications with highest demands for dynamics, constant torque, low noise and highest power output. Keywords: Switched Reluctance Drive, Switched Reluctance Motor INTRODUCTION The Switched Reluctance Motor has already been phase winding propagated in many publications of English literature. However, these general publications do not A1 scientifically solve the use of this motor type as B1 D4 variable-speed drive. Most publications treat parts of C1 C4 the problems only. Less attention was paid to the stator pole examination and optimization of the overall system - D1 B4 composed of motor, converter and control. rotor tooth Uncertainties regarding utilization, torque undulation, A2 A4 noise generation and selection of converter circuits shaft bore lead to today's shadowy exixtence of this motor. Since the simple construction of the Switched Reluctance B2 D3 Motor promises production at low cost, the industry launched occasional enquiries and examinations C2 C3 regarding the Switched Reluctance Drive. D2 B3 A3 Nevertheless the drive could not yet find its wide acceptance, probably due to single, technically cooling-air duct unsolved problems. The motivation to realize this project at the Elektrotechnisches Institut of the University of Figure 1: Schematic cross-section of the Switched Karlsruhe is based on the unsolved technical problems, Reluctance Motor the robust construction and the favourably-priced motor. The paper will describe important findings regarding This design was proposed by author. Compared with the Switched Reluctance Drive as a whole. As an the 3-phase Reluctance Motor, the 4-phase machine example we selected a motor with an output of 25 kW requires the same or even lower number of power at 1500 revolutions per minute. semiconductors. Different types of variable-speed electromotors, such The four phase-winding poles split the forces up more as a.c. and d.c. motors, are widely spread with the evenly around the motor perimeter which reduces the selected technical major parameters. The Switched noise. If only two opposite poles belong to one phase- Reluctance Drive can therefore quickly and easily be winding as for example in the 4-phase-winding 8/6 compared with these drive types. reluctance motor, the forces do apply on two positions only. The 4-phase-winding 16/12 reluctance motor splits the forces up to four poles. Therefore, these are MOTOR DESIGN approximately only half as big as the forces of the 8/6 motor. Also, the 16/12 motor generates less noise than The Elektrotechnisches Institut selected the new the 8/6 motor. These findings are proved true by Switched Reluctance Motor with 16 stator poles and comparative measurements done with a 15 kW 8/6 12 rotor teeth. It is a 4-pase-winding machine, the 4 motor of the Oulton company. stator poles that are shifted by 90° to each other form one phase-winding (Figure 1). Vol.3; 558 The authors of the paper [1] compared a 6/4 motor additionally be employed for compensating the with a 12/8 motor and showed that the utilization of reactive power of the auxillary drives. Figure 3 shows the high-pole machine is better for higher torques the current and voltage values for motor operation which is due to the flux linkage and the narrow with 20 kW and reactive power compensation at the winding coils. The first causes a higher torque, the same time. latter a lower thermal resistance from the winding to For reluctance drives less demanding in terms of the iron. However, with a bigger number of pole/teeth dynamics and mains compatibility, diode bridges with the magnetic reversal frequency and iron losses smoothing and commutating reactors are used as increase. According to [1], a lower flux density should mains current converters. The reluctance drive can compensate this effect, so that iron losses of both also be operated with it, in most cases however, as motors range in the same size. However, the latter motor only. context does not seem to be proved true by our Switched Reluctance Motor. The iron losses increase phase-to-neutral voltage [V] 400 noticeably with higher torque. 200 0 TEST DRIVE -200 -400 0 10 20 time [ms] 40 The main components of the test drive are the mains current [A] Switched Reluctance Motor and the power converter. 100 The voltage-source converter consists of mains and 50 motor converter. The common supply for the three- 0 phase-self-commutated mains converter is 400V/50Hz. -50 The control electronic - including the measurement -100 0 10 20 time [ms] 40 and control techniques - is superior to the power electronic. Motor and converter can be used for the four-quadrant-drive. The basic structure is shown in Figure 3: Pmains = 24,4 kW, Qmains = -10 kVAr, Figure 2. cosj = 0,925cap, Pmotor = 20 kW, (measurement) three- control electronics phase LOAD-SIDE CONVERTER mains L1 mains + load-side For the Switched Reluctance machine the output L2 converter converter L3 current of the converter can be limited to one direction 400 V per phase due to the unipole excitation. The rotor 50 Hz moves into the magnetic field when the motor is in operation. This does not depend on the direction of the 33 kW magnetic flux density. 1500 r.p.m. SR-Machine With the generator in operation, the rotor moves out of MFR 132.5/3 the field. Three criteria must be complied with when selecting Figure 2: Basic structure of the the converter circuit: Switched Reluctance Drive 1. low number and low cost of power semiconductors 2. less current measurements MAINS FRIENDLINESS OF THE SWITCHED 3. many options for influencing the phase-winding RELUCTANCE DRIVE current The mains converter is a three-phase-self-commutated Criteria 3 contradicts 1 and 2. Less requirements for IGBT-Converter. The control of the mains current has power electronic and measurements restrict the options been optimized in a way that the drive, in stationary for current control. When defining the converter running with a power factor of about one, receives topology, you must compromise to fulfill these energy from or feeds energy into the 3-phase current demands. mains. This results in a sinusoidal mains current and in conformity of the phase position between current If a two-quadrant chopper circuit is used for each and voltage - at long last the mains friendliness of the phase and if each phase current is measured drive. separately, many options can be used. The complete The mains current converter operates in all four d.c link voltage Ud can be used for switching the quadrants and allows to implement highly dynamic phase-winding current on/off. The current can - for all drive solutions. For example, if the converter is used phase-windings and at any time - be adjusted to a pre- for the main drive of a group of drives, it may Vol.3; 559 defined desired value. A free-wheeling of the phase- same time, since for example A generates a motoric winding current is possible. and C a generator torque. Both torques are subtracted from each other, a not desirable status. Like this, the + Figure 4: H-Circuit phases A and C respectively B and D can be supplyed with one common transistor each without further Ud 2 The so-called H- restrictions regarding the current control. The currents A C Circuit [2] with can be determined by one common measurement. 0 connected neutral Only with very high output powers, the inactive phase B D point (Figure 4) conducts a small amount of residual current. The Ud 2 allows to control the measurement errors resulting for the active phase are single currents corrected in the control. - separately. This In comparison with the three-phase induction motor, circuit only requires one power switch and one diode the amplitudes of the phase currents are approximately per phase thus operating with the lowest number of 15% higher. Therefore, the power semiconductors can semiconductors. To profit from these benefits you must be selected with the size of the modules usually used in accept that there is no free-wheeling current and that power converters of asynchronous motors. only half the d.c. voltage is used. The current can only Compared with the H-Circuit, the cost for power be in- or decreased with Ud/2. Like this, motor semiconductors from average to higher output powers winding and current carrying capacity of the power are lower. The free-wheeling current can be used to semiconductors must be dimensioned for Ud/2. With lower the pulse frequency rate respectively the current regard to the two-quadrant chopper circuit per phase - ripple. Since there is no voltage neutral point this provided that the nominal speed of the motor is the circuit can also be used for very small speeds and for same - the number of turns per phase must be halved standstill torques. and the cross-section of the wire must be doubled. Additionally, power modules with doubled current carrying capacity must be selected. Two or four CURRENT AND TORQUE CONTROL measurements are required to measure the phase currents. Usually, the neutral point is generated by For the test drive, the torque control was optimized in means of a serial circuit of capacitors at the d.c.
Details
-
File Typepdf
-
Upload Time-
-
Content LanguagesEnglish
-
Upload UserAnonymous/Not logged-in
-
File Pages6 Page
-
File Size-