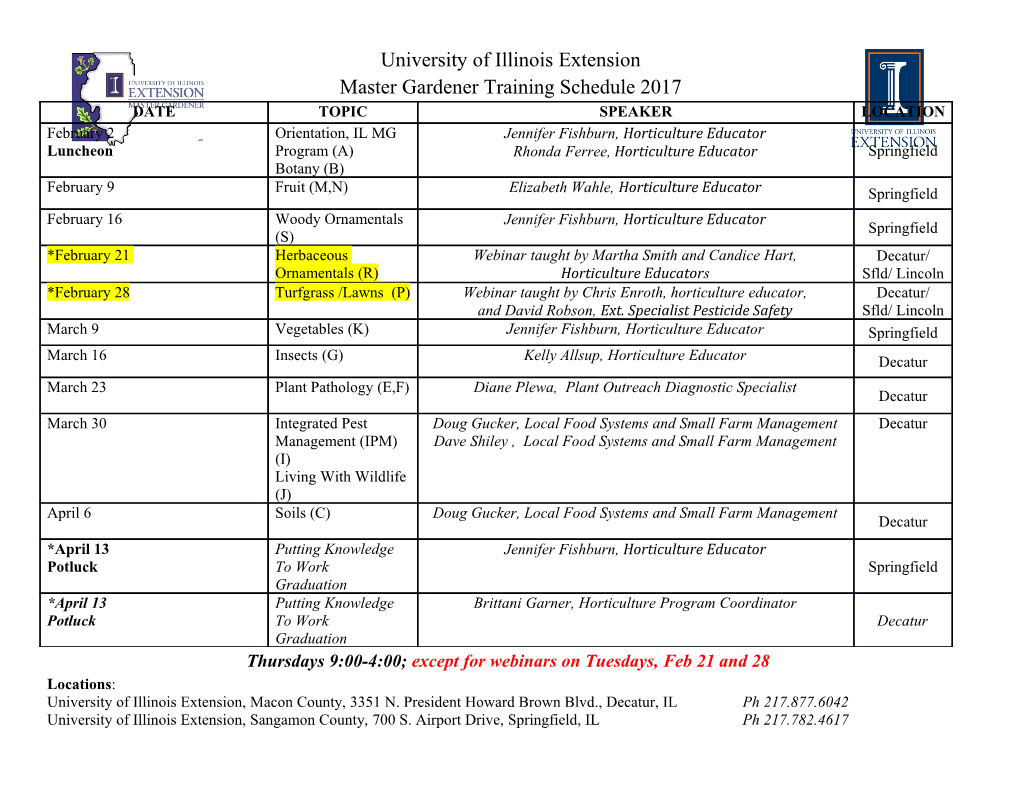
Studies on Properties and Reduction of Manganese Ores* By Tetsllo Yagihashi**, KaZlio Asada***, Kjjji Atarashiya***, Shlln-ichi Ichinohe* * * and Hiromichi H anada* * * Synopsis ready, preliminary reduction methods such as the To stuqy th e reducibility oj some manganese ores which are used Jor Elkem processl) and the Strategic-Udy process2) a re in Jerromanganese jJroducl'ion, the allthors investigated the jlrojJerties oj th ese use. Of course, the results of this investigation are ores by X-ray diffraction, differential thermal anarysis and thermal balance useful for these preliminary reduction processes. The anarysis, and the determination oj their mineral cOIll/Josition was disCIIssed. fundamental da ta on the prelimina ry reduction with Then, they studied manganese ore reduction with either CO gas or waste gas from the closed furnace were obtained. CO-C02 gas mixtures by the thermal balance anarysis method, and dis­ cllssed its reducibility in terms oj its mineral com/Josition. II. Tested Ores A great number of manganese minerals are known, I. Introduction and there are great differences in the properties of In the production of high carbon f, rromanganese, manganese ore deposits.3)-5) The properties of ore the properties of manganese ore have a n effect upon the deposits exert an inAuence on the mineral crystalliza ­ operative results. But, very little study has been made tion a nd the admixture of ores. R eally, manganese in connection with reduction reaction, because m an­ ores used for industry are generally complicated mix­ ganese ores have very complicated mineralogical com­ tures of various minerals. Importa nt minerals in pOSitIOns. Previous investigations of manganese ores ferromanganese production are m a nganese oxid e, have dealt almost exclusively with mineralogy. In h ydrated manganese oxide, manganese carbonate and order to determine how properties of manganese ores manganese silicate. Generaily, m anganese carbona te affect their reducibility, this investigation was carried ore is burnt and the burnt ore is supplied. out. Chemical compositions of tested m a nganese ores are Accompanying enlargement and closed opera tion shown in Table 1. Among these ores, Yakumo (A), of high carbon ferromanganese furnaces, the pre­ specia l Oe, common Oe, Jokoku (B) and J okoku (C) liminary treatment of ores has become serious. AI- are burnt ores and others are unburnt. All ores were Table 1. Chemical analyses of manganese ores (Unit : wt%) Mn MnO, SiO, F e AI,O, eao p India n (H .G.) 47.87 59.68 8.36 1. 63 0.10 0.236 - ~---I- -- -- Indian (L.G.) 39.12 51.20 7.95 11.02 4.26 1. 02 0.1 31 South African (H .G.) 45.36 65.97 4.67 8.85 0.43 0.72 0.017 -1--- South African (L.G .) 41.47 59.94 6.28 10.41 3.98 0. 10 0. 135 ---- -I Brazilian 52.95 78.55 1.02 4.24 2.67 0.10 0. 105 ---- Ghanaian 49 .48 71. 56 8.88 3.00 3.05 0.10 0. 119 lndonesian 48.11 70.60 7.24 3.84 1. 88 1.34 0.093 ----- Australian 53.54 2 .75 I. 78 0.49 0.1 0 0.028 - - -------- Yakumo (A) 14.84 3.61 1. 00 3.06 0.012 Oe (s pecial) 48.45 8.53 11 .98 0.61 1.85 0.029 --- -- O e (common) 21.98 10 12 0.66 0.94 0.015 1_ . _ 1 J okoku (0 ) 7.65 10 .98 I 0.43 - - - Jokoku (C) 14.81 1.59 -I I__ l~ 19 .80 5.93 2.79 I 63.00 7.48 I 5.48 4.87 Oshima 28.53 25.95 9.90 I 10.12 1. 24 7.58 Shibetsu 45.05 27.61 12.67 1.72 2. 19 2.85 I 0.065 ------ _I * Lecture delivered before the 64th Grand Lecture Meeting of The Iron & Steel Institute of Japan in October 1962 in Hiro­ shima. J apanese text was printed in T etsu-to-Hagane (Journal, Iron & Steel Institute, J apan), 49 (1963), 7, 971 - 975; 8, 1059- 1065. ** Dr. Sci., ational R esearch Institute for M etals. *** N ippon Denko Co., Ltd. Research Articles ( 12) Tetsu-to-Hagane O verseas Vol. 4 No.1 Mar. 1964 crushed finely under 200 mesh, and mixing of impuri­ H, SO. P, O, F low- meter Flow- meter ties was rigorously prevented. Guaranteed reagents, Mn02 and IVlnC0 were used for standard samples. nSample 3 holder III. Exp erimental Apparatus and Procedure 1. Determination of Mineral Compositions furnace For the purpose of determining the mineral com­ positions, X-ray diffraction, differential thermal analy­ sis and thermal balance analysis were carried out. o ~tl ~ t L- X -ray diffraction apparatus is the oreleo X-ray diffractometer. The FeKap lines excited at 35 kV and Or sat 6 rnA were used without filters. The appa ratus for gas anal yser differential thermal analysis is the Shimadzu type CO, -bombe Thermal balance DT-I A. The tested ore was inserted in aPt-capsule. Fig. 1. Apparatus used for manganese ore reduction The a-A1 20 3 powder was used as a standard sample. The thermal balance is the Oyorika type ORK. with CO gas or CO-C02 gas mixtures Differential thermal analysis and thermal balance ed to a solenoid circuit to produce a variation of con­ analysis are very useful methods for the amorphous trary direction equal to the weight change. phase where X-ray diffraction is not used. CO2 gas in the bombe was obtained commercially. Transformations of manganese ore observed in the It was generated through granular graphite heated at air are as follows. Under 400°C departure of adsorbed 1,000°C. CO2 gas was dehydrated and dried through gas, adsorbed water and water of crystallization is H 2S04 and P 20 5, and one part was introduced into observed and the decomposition of manganite (MnO· the gas holder in that condition. The other part was OH) occurs. Next from 500°C to 700°C deoxidation is introduced into the gas holder through the CO gen­ observed. erator and gas washers in which residual CO2 gas 4Mn02 =21n20 a+ 0 2-39.4kcal .. .... ... (1) was removed by soda lime, and CO gas was dried by L1Go= 38,880-50.40 T silica gel and P20 5 • As only CO gas was required, At about 1,000°C, gas flowed through the bypass of the CO-generator side. Mixing ratio of CO and CO gas was deter­ 6Mn203= 4Mn304+ 02- 49.9 kcal ......... (2) 2 mined by the flow volume of each side. While com­ L1Go= 49,440 - 31.60 T position of the gas was analysed by an Orsat gas such a reaction is observed. By the characteristic analyser, gas was introduced into the thermal balance changes of these reactions, mineral compositions are reaction tube. Experimental procedure was as fol­ determined. In air, deoxidation is stopped till haus­ lows. In the quartz sample holder, 500 mg of tested mannite (Mn30 4), and reaction (3) is no longer ore was weighed and inserted into the thermal balance observed under 1,000°C. reaction tube. 'While CO gas or CO-C02 gas mix­ 8 2Mn30 4 = 6MnO + 0 2- 11O.5 kcal.. .. .... .... (3) tures flowed at the rate of 50 cm per min., the air was L1Go= 109,920- 62.56 T expelled and the furnace temperature was raised at a Thermodynamical data of these deoxidations were rate of 5°C per min. The mechanism of reaction was quoted from J. P. Coughlin's table6}. The heat of discussed from the weight change of the samples. The reaction at 25°C is shown because its temperature samples obtained from intermediate states of reaction dependence is slight. It is shown that all reactions are were subjected to X-ray diffraction. X-ray di ffrac­ endothermic. In these reactions, the thermal change tion a pparatus is the Rigakudenki Geigerflex X-ray was detected by differential thermal analysis, and the diffractometer and FeKap and CuKa lines were weight change was detected by thermal balance used. analysis. Concerning manganese oxide reduction with CO gas, the discussion of the thermodynamics is as follows, 6 2. Manganese Ore Reduction with CO Gas or CO- C02 the data quoted from J. P. Coughlin's table ) being Gas Mixtures used. I. It The reduction apparatus is shown in Fig. is 2Mn02+ CO = Mn20 a+C02+ 47.9 kcal ... (4) a combination of thermal balance with a gas generator. L1Go= -48,060- 4.49T The principle of thermal balance is the zero method in 3Mn20a+ CO = 2Mna04+ C02+ 42.8 kcal which weight change is transformed into electric dis­ ... ............................... ... ... .............. ... (5) placement and is amplified selectively and then return- L1Go= -42,780+4.91 T Research Articles Te tsu-to-Hagane O verseas Vol. 4 No. 1 Mar. 1964 ( 13 J Mn30 4 +CO= 3MnO+C02 + 12 .4 kcal ... (6) It seems that the reduction to manganosite is very easy, LlGo= - 12,540-10.57T because the composition of the gas is very rich in CO2 MnO+ CO = Mn+C0 2 - 24.4kcal ......... (7) at equilibrium. Therefore reactions (4) and (5) are LlGo= 24,480+ 3.23 T more feasible than reaction (6), because CO2 gas at Namely, reactions (4), (5) and (6) occur under 1,000°C, equilibrium increases more and more. Many other but reaction (7) does not occur. Regarding reaction reactions will be described later. (6) which produces final reduced manganosite (M nO ), the chemical equilibrium was discussed. Concerning IV. Exp erimental Results and Discussions this, studies by H.
Details
-
File Typepdf
-
Upload Time-
-
Content LanguagesEnglish
-
Upload UserAnonymous/Not logged-in
-
File Pages9 Page
-
File Size-