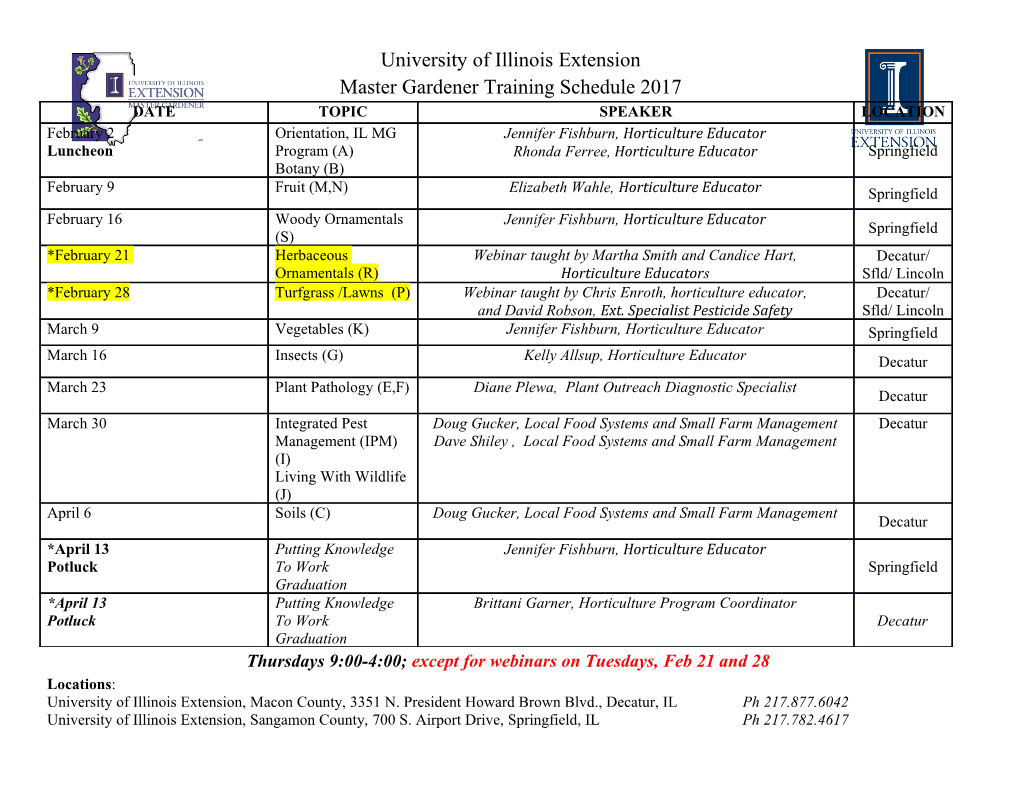
PhilberthDEEP SOUNDIN G : TECHNIQUES 65 Probe (1968) SESAME EPIC Combined (Vac + (2018) Hyperbaric Chamber): HEATED RESERVOIR M UPPER HOT POINT i ü COIL SECTION J-NEXT Ice Drilling CHROWE (2018) INSTRUMENTATION SECTION Philberth Probe/Cryobot & Hot Water Drilling and the LOWER MOT 108 Benson and others: IceCube Enhanced Hot Water Drill POINT EPIC THE PHILBERTH PROBE THE PENDULUM PROBE Atelier FIG. 1. The probes have a length to diameter ratio of about 25:1. Their power levels range from 5 to 15 kw for penetration rates from 2-5 to 5 m/hr. (2017) Hot Water Drill Science Payload 1978-1979) Knut I. Oxnevad, Bill J. Nesmith Conceptual Design (submersible) Comm Electronics (C&DH (5 pucks) and Nav) 7 KWth Main + 1 KWth Nose Power Sources CBE Mass CBE Power JPLFig. 3. TOS structure and tower,drill cable reel,return water reels,and drill supply hose reel. Ice Probe (Kg) (We) Total Probe 210.8 597.6 reintroduced into the system as a source of make-up water. film on all internal wetted surfaces and in the borehole Although this could provide up to 15% of the required water column. In retrospect,the project should have opted NaviGation 4.59 11.4 Power June 3,make-up 2019water,the additional work to maintain the for stainless coils for both heat exchangers to avoid the iron (New Microsphere C&DH 1.50 10.0 collection system and neutralize the condensate seemed to oxide accumulation. Drill and Jet Radioisotope Based Thermoelectric outweigh the benefit. Other means of disposal would be Downstream of the MHP buildings,the heated water was Power 33.26 4.0 (Shaving bit with Generator) water jets) considered in the future. routed back to the HPP to combine the flows into a simple Telecommunication 5.55 30.0 Redundant levels of safety were implemented on the manifold;measure the pressure,flow and temperature;and © 2019 California Institute of Technology.heaters. GovernmentHeater output temperature was sponsorshipinstrumented with finally direct acknowledgedthe water to the TOS via a long insulated. DrillinG / Water Jet 16.00 400.0 With newly developed pellet thermal source three levels of safety devices (thermocouple monitored by 64 mm inner diameter (i.d.) ethylene propylene diene Submarine payload 26.70 27.2 control system; local thermostat and thermocouple; over- monomer (EPDM) rubber surface hose. Structure 112.00 5.0 temperature switch),and flow with two levels (turbine flow meter monitored by control system;local differential pres- Tower operations site (TOS) surface equipment Thermal 11.20 110.0 (Figs 3 and 4) sure switch across heater). Note that the flow and tempera- Margin (%)* 41 29 ture devices work in conjunction with each other,since a The primary function of the TOS during deep drilling was to 4 m satisfied flow is required to transport heated water past the deliver hose and cable to the hole at an appropriate rate for SUSI (at DLR EnEx Ice*Mass margin calculated against 335 Mole Kg landed mass allocation for Europa Lander Class DDL COLDTech APL-UW Ice VALKYRIE temperature sensors. IeCubecreating the desired hole shape. With the hose and cable *Power margin based on 836 W EOL (9 years) The primary heater coils were schedule 80 steel pipe. deployed to 2500 m,there was 118 kN of equipment load, Stone and others: Towards an optically powered cryobot These corroded,resulting in build-up3 of a muddy iron oxide but only 29 kN of downward load exerted on the drill tower Dachwald and others: IceMole 17 Power (GPHS Testlab) Diver (2013) (2014) (2014) (2014) CHAMPbased) (2006) With existing GPHS thermal source(2016) 19 CHIRPS (2001) Fig. 6. Deployment of the IceMole 1 prototype on Morteratsch- gletscher in 2010. The penetration velocity in each of the tests was only 1 0.3 m hÀ because of the still suboptimal matching ⇠ between drive and melting power. IceMole 2 Between 2010 and 2012, a second IceMole prototype, IceMole 2, was developed at FH Aachen University of Applied Sciences (Fig. 10; Table 1). IceMole 2 had a more sophisticated heater control system, with 12 separately controllable heating cartridges in the parabolically shaped melting head and eight side-wall Fig. 5. IceMole 1 assembly view. heaters. Both updates were intended to improve the probe’s maneuverability and support its curve-melting capabilities. IceMole 2 weighed less than IceMole 1 and contained an attitude and position determination system. The melting 1 velocity was increased to 1mhÀ . ⇠ Fig. 2. VALKYRIE field test set-up. Table 1. Technical data for the different IceMole probes Fig. 4. TOS surface and downhole equipment. IceMole 1 IceMole 2 EnEx-IceMole 1 the following layer structure: 400 m core diameter, 440 m external optical waveguide? Will there be unacceptable m m Cross section 15 cm 15 cm 15 cm 15 cm 15 cm 15 cm ⇥ ⇥ ⇥ power losses over a 3–4 km penetration distance? Will the outer diameter (OD) cladding and 480 mm OD polyimide Shape of melting head complanate parabolic complanate Max. heating power for melting head 4 800 W 12 200 W (8 200 W) (8 160 W) ⇥ ⇥ ⇥ á ⇥ Max. heating power for side-wall heaters N/A 8 300 W 8 1000 W bending of the fiber to create an on-board spooler on the coating (for the prevention of water intrusion). The ⇥ ⇥ (partial coverage with const. heat distr.) (full coverage with linear heat distr.) vehicle exacerbate power losses? composite fiber had a numerical aperture (NA) of 0.22. Max. power for forward melting 3.2 kW 2.4 kW 2.9 kW Max. power for curve driving 1.6 kW 1.8 kW 5.0 kW 1 1 1 High-power fiber transmission tests were conducted by For these high-power tests we used an IPG 20kW Max. penetration velocity 0.3 m hÀ 1.0 m hÀ 1.1 m hÀ ⇠ ⇠ ⇠ Length (without ice screw) 0.9 m 1.2 m 2.0 m Stone Aerospace (SAS) engineers in July 2010. The optical multimode fiber laser (1070 nm, model No. YLS-20000). Length of ice screw 7 cm 8.5 cm 6 cm waveguide was a custom-made silica fiber 1050 m in length The laser was calibrated, using a collimator and a Primes Ice-screw driving power 25 W 25 W 25 W Mass 30 kg 25 kg 60 kg ⇠ ⇠ ⇠ with a core diameter of 400 mm, which was spooled onto a calorimeter, from 40 W to 20 kW prior to testing through the Max. pressure 1 bar 5 bar 5 bar Bus system SPI CAN CAN, Ethernet water-cooled polyethylene tray of 1 m diameter (Fig. 4). The optical waveguide. Figure 5 shows the experiment archi- Communications to surface power-line modem power-line modem Ethernet and power-line modem 1 1 1 Max. data rate to surface 19.2 kbit sÀ 19.2 kbit sÀ 1000 Mbit sÀ spool diameter was chosen because it exceeds the theoret- tecture. Connection of modular high-power laser elements Attitude and position determination system no simple advanced Decontamination and sampling system no no yes ical threshold for significant power loss due to fiber-bending requires the use of special connectors in which the fiber is Obstacle and target detection system no no yes effects. The power transmission fiber, specified by SAS and terminated into a fused quartz block within a water-cooled Field tests Morteratschgletscher Morteratschgletscher 2012, Morteratschgletscher 2013, 2010 Hofsjo¨kull 2012 Canada Glacier 2013 Longest channel made 5m 8m 25 m manufactured by Polymicro, consisted of a multimode step housing. Two connectors can be joined within a beam ⇠ ⇠ ⇠ Min. curve radius 10 m N/A 10 m index pure silica core with fluorine-doped cladding. It had coupler (Fig. 6), which contains internal optics that expand, ⇠ ⇠ Notes: N/A = not applicable. Max. power for curve driving = (0.5 max. heating power) for melting head + (0.25 max. heating power) for side-wall heaters. collimate and align the beam with the adjacent connector ⇥ ⇥ optics. The coupler housing is also water-cooled and contains several sensor interlocks that enable automated shutdown of the laser if the coupler overheats. These interlocks are required because the power levels are sufficient to initiate a fiber ‘fuse’ in the event of a thermal Fig. 3. Mission duration as a function of input power for a 0.25 m Fig. 4. Preparing 1050 m of fiber for the initial high-power diameter cryobot. transmission test. DEEP SOUNDING : TECHNIQUES 65 A. Ice Melting Systems: The Start HEATED RESERVOIR M The cryobot, initially called the “Philberth Probe, was invented by German physicist Karl Philberth. It was first UPPER HOT demonstratedPOINT iinü the 1968 International Glaciological Greenland Expedition (EGIG). Drilling depths in excess of 1,000 meters (3,300 ft) were achieved. During this time Philberth seemed to have worked closely with H. W. C. Aamot and B. Lyle Hansen, of the U.S. Army Cold Regions Research and Engineering Laboratory (CRREL). As part of this collaboration, Aamot developed the heat transfer and performance analysis approaches for the thermal probe. COIL SECTION Probe Concept Probe Name Dimensions: Mass (kg) Thermal Tether Passive Active (Water Jet: Max Depth Velocity (m/h) Environment Ice References d x l (m) Power (kW) (Y/N) (Melt only): WJ or Drill: D) (m) (Vacuum: V or Temperature Y/N Atmosphere: (K) A) Probe I and II I: 0.108x2.5; NA 3.6 Y Y N I: 218; II: 1005 2 A 243 (after Philberth, INSTRUMENTATION “PhilberthSECTION Probe” II: 0.108x3 cooling) K., 1968 LOWER MOT AAMOT,POINT H. W. C., Heat transfer and performance analysis of a thermal probe for glaciers. U.S.A.
Details
-
File Typepdf
-
Upload Time-
-
Content LanguagesEnglish
-
Upload UserAnonymous/Not logged-in
-
File Pages15 Page
-
File Size-