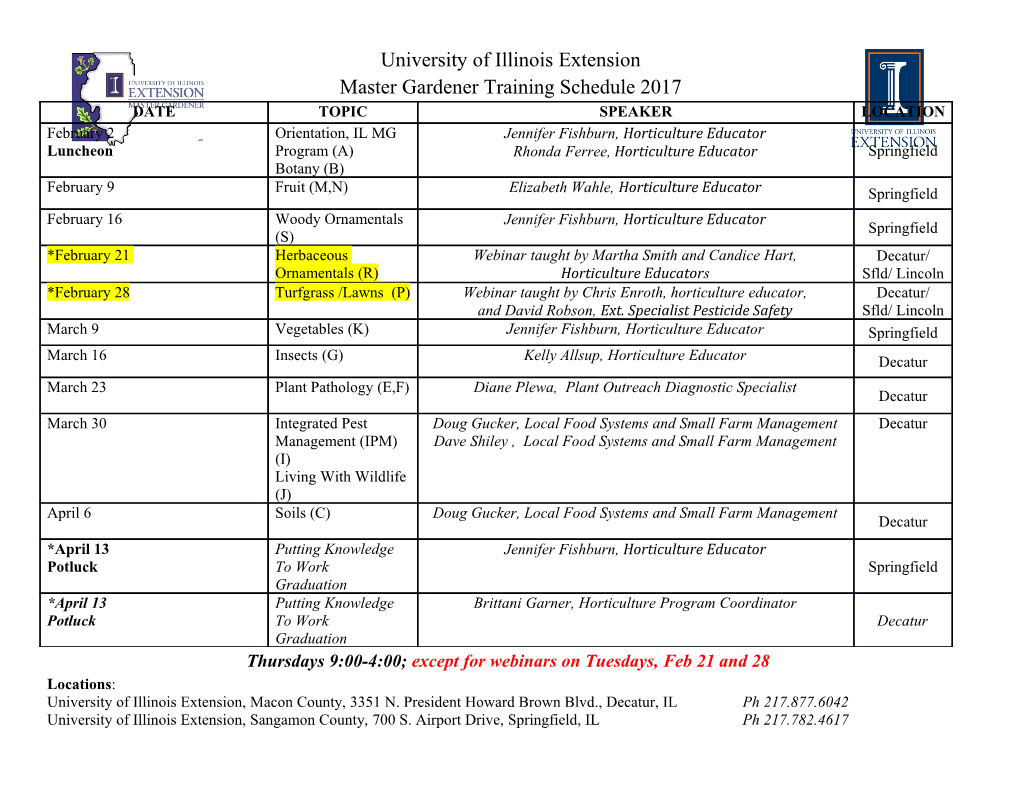
BOILER A boiler is a device for heating water and generating steam above atmospheric pressure. The boiler consists of a compartment where the fuel is burned and a compartment where water can be evaporated into steam. The hot water or steam is used to transfer heat to a process STEAM TO PROCESS EXHAUST GAS VENT STACK DE AERATOR r r PUMPS e e z z i i m m o o n n o o c c E E VENT BOILER BURNE WATER R WATER SOURCE BLOW DOWN SEPARATOR FUEL BRINE CHEMICAL FEED SOFTENERS Schematic overview of a boiler room Boiler Mountings and Accessories Fitting and devices which are necessary for the safety and control are knows as boiler mountings Fitting or devices which are provided to increase the efficiency of the boiler and help in the smooth working of the plant are knows as boiler accessories • Safety valve: It is used to relieve pressure and prevent possible explosion of a boiler. • Water level indicators: They show the operator the level of fluid in the boiler, also known as a sight glass, water gauge or water column is provided. • Bottom blow down valves: They provide a means for removing solid particulates that condense and lay on the bottom of a boiler. As the name implies, this valve is usually located directly on the bottom of the boiler, and is occasionally opened to use the pressure in the boiler to push these particulates out. • Continuous lowdown valve: This allows a small quantity of water to escape continuously. Its purpose is to prevent the water in the boiler becoming saturated with dissolved salts. Saturation would lead to foaming and cause water droplets to be carried over with the steam - a condition known as priming. • Hand holes: They are steel plates installed in openings in "header" to allow for inspections & installation of tubes and inspection of internal surfaces. • Steam drum internals, A series of screen, scrubber & cans (cyclone separators). • Low- water cutoff: It is a mechanical means (usually a float switch) that is used to turn off the burner or shut off fuel to the boiler to prevent it from running once the water goes below a certain point. If a boiler is "dry-fired" (burned without water in it) it can cause rupture or catastrophic failure. • Surface blowdown line: It provides a means for removing foam or other lightweight non-condensable substances that tend to float on top of the water inside the boiler. • Circulating pump: It is designed to circulate water back to the boiler after it has expelled some of its heat. • Feedwater check valve or clack valve : A no return stop valve in the feed water line. This may be fitted to the side of the boiler, just below the water level, or to the top of the boiler. A top-mounted check valve is called a top feed and is intended to reduce the nuisance of lime scale. It does not prevent lime scale formation but causes the limescale to be precipitated in a powdery form which is easily washed out of the boiler. • Desuperheater tubes or bundles : A series of tubes or bundle of tubes, in the water drum but sometime in the steam drum that De-superheated steam. This is for equipment that doesn't need dry steam. • Chemical injection line : A connection to add chemicals for controlling feedwater pH. Steam accessories • Main steam stop valve : • Steam traps: • Main steam stop/Check valve : It is used on multiple boiler installations. Combustion accessories • Fuel oil system : • Gas system : • Coal system : Other essential items • Pressure gauges : • Feed pumps : • Fusible plug : • Inspectors test pressure gauge attachment : • Name plate : • Registration plate WATER TUBE BOILER A water-tube boiler is a type of boiler in which water circulates in tubes heated externally by the fire. Water-tube boilers are used for high-pressure boilers. Fuel is burned inside the furnace, creating hot gas which heats up water in the steam-generating tubes. In smaller boilers, additional generating tubes are separate in the furnace, while larger utility boilers rely on the water-filled tubes that make up the walls of the furnace to generate steam. Interior to the boiler tubes is the fluid medium to be heated or physically altered; thus the name "water tube" . WORKING Many water-tube boilers operate on the principle of natural water circulation (also known as 'thermo-siphoning'). This is a subject that is worth covering before looking at the different types of water-tube boilers that are available. Figure A helps to explain this principle: Fig. A Natural water circulation in a water-tube boiler • Cooler feed water is introduced into the team drum behind a baffle where, because the density of the cold water is greater, it descends in the 'downcomer' towards the lower or 'mud' drum, displacing the warmer water up into the front tubes. • Continued heating creates steam bubbles in the front tubes, which are naturally separated from the hot water in the steam drum, and are taken off. However, when the pressure in the water-tube boiler is increased, the difference between the densities of the water and saturated steam falls, consequently less circulation occurs. To keep the same level of steam output at higher design pressures, the distance between the lower drum and the steam drum must be increased, or some means of forced circulation must be introduced. Water-tube boiler sections The energy from the heat source may be extracted as either radiant or convection and conduction. The furnace or radiant section This is an open area accommodating the flame(s) from the burner(s). If the flames were allowed to come into contact with the boiler tubes, serious erosion and finally tube failure would occur. The walls of the furnace section are lined with finned tubes called membrane panels, which are designed to absorb the radiant heat from the flame. Fig B Heat transfer in the furnace or radiant section Convection section This part is designed to absorb the heat from the hot gases by conduction and convection. Large boilers may have several tube banks (also called pendants) in series, in order to gain maximum energy from the hot gases. Fig. C Heat transfer in the convection section TYPES OF WATER TUBE BOILER Water-tube boilers are usually classified according to certain characteristics, see Table Water-tube boiler classifications Longitudinal drum boiler The longitudinal drum boiler was the original type of water-tube boiler that operated on the thermo-siphon principle (see Figure 1). Cooler feed water is fed into a drum, which is placed longitudinally above the heat source. The cooler water falls down a rear circulation header into several inclined heated tubes. As the water temperature increases as it passes up through the inclined tubes, it boils and its density decreases, therefore circulating hot water and steam up the inclined tubes into the front circulation header which feeds back to the drum. In the drum, the steam bubbles separate from the water and the steam can be taken off. Typical capacities for longitudinal drum boilers range from 2 250 kg/to 36 000 kg/h. Cross drum boiler The cross drum boiler is a variant of the longitudinal drum boiler in that the drum is placed cross ways to the heat source as shown in Figure2. The cross drum operates on the same principle as the longitudinal drum except that it achieves a more uniform temperature across the drum. However it does risk damage due to faulty circulation at high steam loads; if the upper tubes become dry, they can overheat and eventually fail. The cross drum boiler also has the added advantage of being able to serve a larger number of inclined tubes due to its cross ways position. Typical capacities for a cross drum boiler range from 700 kg / h to 240 000 kg/h. Fig.2 Cross drum boiler D-type boiler This is the most common type of small-medium sized boilers, similar to the one shown in the schematic diagram. It is used in both stationary and marine applications. It consists of a large steam drum vertically connected to a smaller water drum (a.k.a. mud drum) via multiple steam-generating tubes. These are surrounded by walls made up of larger water filled tubes, which make up the furnace. Babcock & Wilcox boiler This has a single drum, with feed water drawn from the bottom of the drum into a header that supplies inclined water-tubes. The water tubes supply steam back into the top of the drum. Furnaces are located below the tubes and drum. This type of boiler was used by the Royal Navy's Leander class frigates. The Y160 variant used on the Batch 3 Leander s (e.g. HMS Jupiter ) also incorporated steam atomisation equipment on the fuel supply so that the diesel fuel entering the boilers via the three main burners was atomised into a fine spray for better flame efficiency. The superheat temperature of the Y160 was controlled manually by the Boiler Room Petty Officer of the Watch between 750 0F and 850 0F and the steam supplied to the main turbines was at a pressure of 550 psi. Bent tube or Stirling boiler This type has three upper drums connected to two lower drums by water tubes. These are mainly used as stationary boilers. There are also Stirling's that are two drum, a steam drum and a mud drum. These are used mostly in industrial settings (Paper Mills, etc). These are also a type of boiler you will see that will burn multiple fuels, such as bark, bagasse, etc.
Details
-
File Typepdf
-
Upload Time-
-
Content LanguagesEnglish
-
Upload UserAnonymous/Not logged-in
-
File Pages14 Page
-
File Size-