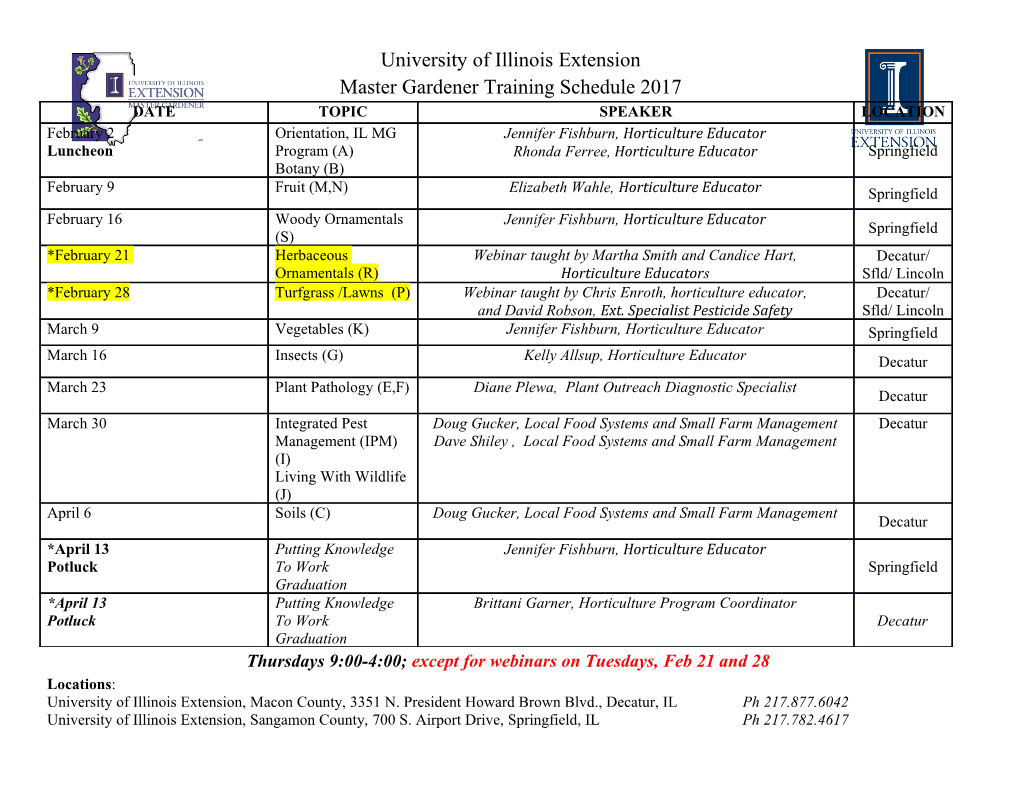
High-Speed Rail IDEA Program Magnetorheological Damping for Spring Frogs Final Report for High-Speed Rail IDEA Project 46 Prepared by: Leslie E. Olson Texas Transportation Institute Texas A&M University System College Station, TX July 2007 INNOVATIONS DESERVING EXPLORATORY ANALYSIS (IDEA) PROGRAMS MANAGED BY THE TRANSPORTATION RESEARCH BOARD This investigation was performed as part of the High-Speed Rail IDEA program supports innovative methods and technology in support of the Federal Railroad Administration’s (FRA) next-generation high-speed rail technology development program. The High-Speed Rail IDEA program is one of four IDEA programs managed by TRB. The other IDEA programs are listed below. • NCHRP Highway IDEA focuses on advances in the design, construction, safety, and maintenance of highway systems, is part of the National Cooperative Highway Research Program. • Transit IDEA focuses on development and testing of innovative concepts and methods for improving transit practice. The Transit IDEA Program is part of the Transit Cooperative Research Program, a cooperative effort of the Federal Transit Administration (FTA), the Transportation Research Board (TRB) and the Transit Development Corporation, a nonprofit educational and research organization of the American Public Transportation Association. The program is funded by the FTA and is managed by TRB. • Safety IDEA focuses on innovative approaches to improving motor carrier, railroad, and highway safety. The program is supported by the Federal Motor Carrier Safety Administration and the FRA. Management of the four IDEA programs is integrated to promote the development and testing of nontraditional and innovative concepts, methods, and technologies for surface transportation. For information on the IDEA programs, contact the IDEA programs office by telephone (202-334-3310); by fax (202-334-3471); or on the Internet at http://www.trb.org/idea IDEA Programs Transportation Research Board 500 Fifth Street, NW Washington, DC 20001 The project that is the subject of this contractor-authored report was a part of the Innovations Deserving Exploratory Analysis (IDEA) Programs, which are managed by the Transportation Research Board (TRB) with the approval of the Governing Board of the National Research Council. The members of the oversight committee that monitored the project and reviewed the report were chosen for their special competencies and with regard for appropriate balance. The views expressed in this report are those of the contractor who conducted the investigation documented in this report and do not necessarily reflect those of the Transportation Research Board, the National Research Council, or the sponsors of the IDEA Programs. This document has not been edited by TRB. The Transportation Research Board of the National Academies, the National Research Council, and the organizations that sponsor the IDEA Programs do not endorse products or manufacturers. Trade or manufacturers' names appear herein solely because they are considered essential to the object of the investigation. ii MAGNETORHEOLOGICAL DAMPING FOR SPRING FROGS IDEA PROGRAM FINAL REPORT FOR THE PERIOD JULY 2005 THROUGH DECEMBER 2006 HSR-46 PREPARED FOR THE IDEA PROGRAM TRANSPORTATION RESEARCH BOARD NATIONAL RESEARCH COUNCIL LESLIE E. OLSON TEXAS TRANSPORTATION INSTITUTE TEXAS A&M UNIVERSITY SYSTEM COLLEGE STATION, TEXAS 77843-3135 JULY 2007 iii ACKNOWLEDGEMENTS The research reported herein was performed under the Transportation Research Board’s High- Speed Rail IDEA Program, contract HSR-46, by the Rail Research Center of the Texas Transportation Institute at Texas A&M University. Texas Transportation Institute was the contractor for this research. Leslie Olson, Associate Research Scientist, and Paul Roschke, Associate Research Engineer, Texas Transportation Institute were joint investigators. The authors express their sincere thanks to Mr. Charles Taylor, IDEA Project Manager, for his support and guidance throughout the project; to Mr. Ed Kohake of Union Pacific Railroad without whose support the field tests could not have taken place; and to Mr. Trea Miller of the Union Pacific Railroad whose local scheduling allowed the field work to take place. The work was done under the general supervision of Dr. Paul N. Roschke. The laboratory investigation work was done at Texas A&M University under the supervision of Professor Roschke and Leslie Olson. iv ABSTRACT The goal of this study was to determine if a magnetorheological (MR) damper can replace the hydraulic retarder in spring frogs used on railways in the United States. Hydraulic retarders slow the return of the spring rail to reduce the slamming back of the spring rail that would otherwise occur. An MR damper is similar to a hydraulic damper except it uses a special MR fluid whose viscosity can be controlled by controlling electric current through electromagnetic coils wrapped around the piston head. This report discusses findings from a literature review; data acquisition of field data from a spring frog (SF); design, manufacture, and operation of a two-stage MR damper; a nonparametric model for operation of a spring frog; and a SF motion control algorithm. Field data from operation of a spring frog were collected during passage of three trains in Navasota, Texas. Several transducers, including an LVDT (Linear Variable Displacement Transducer), an accelerometer, and a load pin were used to collect real-time dynamic performance data in the field from a SF that has (1) no passive retarder and (2) a conventional passive retarder. Data were analyzed both in the frequency and time domains. An MR damper was designed to replace a passive hydraulic retarder that is currently in use. The process of design, fabrication, and assembly of a new MR damper is described. Performance tests were conducted on the prototype MR damper in a uniaxial MTS testing machine. Force levels that result from applied displacement, velocity, and voltage signals to the damper are presented. A MR damper fuzzy model was developed to represent characteristics of the behavior of the MR damper using an Adaptive Neuro-Fuzzy Inference System (ANFIS). Finally, a control algorithm for the SF motion control in real time was also developed and experimental results are reported. Union Pacific Railroad management worked with the research team to conduct field tests on the prototype MR damper in a spring frog. The MR damper was installed and allowed to operate in a completely passive condition for a period of six weeks. The MR damper was capable of holding the spring rail in the open position against the spring loading for periods of 200 seconds or more. The research team then instrumented the MR damper and applied power to the cylinder coil as a train transitioned through the switch. The MR cylinder shaft failed immediately. Subsequent analysis determined that the cylinder shaft failed due to bending fatigue caused by off-center loading that was due to the method used to adapt the MR cylinder to the retarder mounting brackets as designed by the manufacturer of the switch. Results of this project led to the conclusions that MR dampers hold the potential for a viable alternative to conventional hydraulic retarders that would be more durable and more effective. Further development of this concept should include the redesign of the mounting brackets to avoid off-center loading of the MR cylinder, followed by comprehensive laboratory and field testing. KEYWORDS Magnetorheological Damper MR damper Magnetorheologic Magnetorheological Retarder Spring Frog Spring Fail Frog Switch Point CONVERSION FACTORS KiloNewton = 224.80894 pound force KiloNewton-meters = 737.56215 foot-pounds force v TABLE OF CONTENTS Page ACKNOWLEDGEMENTS ................................................................................. ii ABSTRACT and KEYWORDS .........................................................................iii TABLE OF CONTENTS .................................................................................... iv EXECUTIVE SUMMARY ................................................................................ vii CHAPTER 1-INTRODUCTION......................................................................... 1 CHAPTER 2-DATA ACQUISITION AND ANALYSIS .................................. 5 DATA ACQUISITION WITH RETARDER IN PLACE ...................................... 7 TIME DOMAIN ANALYSIS................................................................................. 8 FREQUENCY DOMAIN ANALYSIS ................................................................ 10 CHAPTER 3-MAGNETORHEOLOGICAL DAMPER ................................ 12 DESIGN................................................................................................................ 12 FABRICATION.................................................................................................... 13 PERFORMANCE TESTS .................................................................................... 16 TESTING INPUT SIGNAL GENERATION....................................................... 16 DATA ACQUISITION......................................................................................... 16 TEST RESULTS................................................................................................... 18 CHAPTER 4-CONTROLLER DESIGN.......................................................... 19 CONTROL ALGORITHM................................................................................... 19 CONTROLLER LABORATORY TESTING .....................................................
Details
-
File Typepdf
-
Upload Time-
-
Content LanguagesEnglish
-
Upload UserAnonymous/Not logged-in
-
File Pages45 Page
-
File Size-